Global One - Integration. Innovation. Quality.
Intelligente Prozessketten für die additive Fertigung
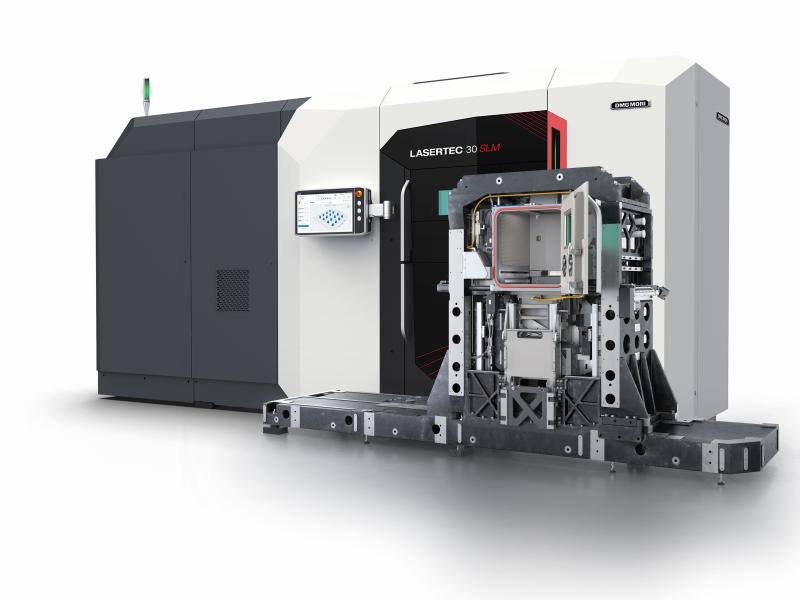
Auf der diesjährigen formnext in Frankfurt demonstriert DMG MORI vom 19. bis zum 22. November 2024 die jüngsten Entwicklungen im Bereich der additiven Fertigung. Das Highlight der Ausstellung in Halle 12-0 ist die kürzlich vorgestellte LASERTEC 30 SLM 3. Generation. Ihr Design basiert zu 100 Prozent auf den langjährigen Erfahrungen in der Konstruktion stabiler Werkzeugmaschinen. Die Prozesskette rund um die additive Fertigung komplettiert DMG MORI mit der DMU 60 eVo. Auf ihr werden – dank des Palettenhandlings PH Cell 300 – im Pulverbett gedruckte Bauteile hochpräzise fertig bearbeitet. Das Potenzial einer durchgängigen Prozesskette ist auch am Beispiel der LASERTEC 65 DED hybrid zu sehen. Die Hybridmaschine vereint additive Fertigung mittels Pulverauftragschweißen und hochpräzises 5-Achs-Simutanfräsen in einem Arbeitsraum. Sie verfügt über einen vollintegrierten, automatisierten DMG MORI scan3D Laserscanner für Reparaturanwendungen und repräsentiert auf eindrucksvolle Weise das Konzept der Machining Transformation (MX), mit dem der Werkzeugmaschinenhersteller die Zukunft der Fertigung gestaltet: Die Integration von additiver Fertigung und CNC-Bearbeitung in einem Arbeitsraum, das automatisierte Scannen reparaturbedürftiger Werkstücke und digitalisierte Abläufe ermöglichen eine ressourcenschonende und damit nachhaltigere Nutzung von Maschinen und Komponenten. Um die weitreichenden Möglichkeiten der additiven Fertigung zielführend einzusetzen, hat DMG MORI die ADDITIVE INTELLIGENCE gegründet. Die Beratungseinheit der DMG MORI Academy, hat es sich zur Aufgabe gemacht, Prozesse rund um die Herstellung komplexer Produkte nachhaltig zu optimieren – 3D-Druck, Digitalisierungsmaßnahmen, automatisiertes Handling und der Einsatz innovativer Bearbeitungstechnologien sind wesentliche Bestandteile der ganzheitlichen Fertigungslösungen.
LASERTEC 30 SLM 3. Generation: robust, zuverlässig und präzise
Ein perfektes Beispiel für Innovation ist die auf der vergangenen Hausausstellung in Bielefeld vorgestellte LASERTEC 30 SLM 3. Generation. Die Pulverbettmaschine baut auf den Stärken ihrer Vorgänger auf und erfüllt die wachsenden Anforderungen eines dynamischen Marktes. So bietet der neue Quad-Laser eine vollständige Überlappung der Scanfelder in einem Bauvolumen von 325 x 325 x 400 mm. DMG MORI hat die LASERTEC 30 SLM 3. Generation mit umfangreichem Knowhow aus dem Werkzeugmaschinenbau konstruiert. Analog zu Fräs- und Drehmaschinen werden in der LASERTEC 30 SLM 3. Generation Gussteile für den Rahmen verwendet. Diese Bauweise garantiert höchste Steifigkeit und optimale Fertigungsbedingungen, sodass die Neuentwicklung Robustheit und Wiederholgenauigkeit neu definiert.
Während bei herkömmlichen Werkzeugmaschinen dynamische Kräfte durch Achsbewegungen entstehen, sind thermische Veränderungen die größte Herausforderung in der additiven Fertigung im Pulverbett. Auch hier profitiert die LASERTEC 30 SLM 3. Generation von der Erfahrung im Werkzeugmaschinenbau. Die Prozesskammer ist innerhalb des thermosymmetrischen Gussrahmes schwimmend gelagert und kann sich bei Temperaturschwankungen frei ausdehnen. Gleichzeitig sind die Optikmodule fest auf dem Gussrahmen montiert. Eine präzise Kalibrierung des Beschichters mittels einer Referenzfläche gewährleistet einen konstanten Abstand zwischen Optik und Pulverbett, zusätzlich unterstützt durch eine aktive Temperaturkompensation der Positionierung in der Z-Achse. Diese effektive Lösung vermeidet Qualitätsprobleme, die aus Abstandsänderungen zwischen Optik und Pulverbett sowie Schwankungen in der Schichtdicke resultieren.
rePLUG: Schneller Materialwechsel über geschlossene Pulvermodule
Ein entscheidender Wettbewerbsvorteil der LASERTEC SLM Serie sind die rePLUG-Pulvermodule von DMG MORI, die die Zeit zwischen den Fertigungsaufträgen verkürzen und die Flexibilität erhöhen. Das rePLUG-Pulvermodul ist eine in sich geschlossene, automatisierte Einheit für das Metallpulvermanagament, die gegen andere rePLUG-Einheiten ausgetauscht werden kann. Bestehende Kunden mit zertifizierten Prozessen, wie sie häufig in der Luft- und Raumfahrt sowie in der Medizintechnik anzutreffen sind, schätzen und verlassen sich auf das rePLUG-System, um sicherzustellen, dass kontinuierlich Pulver von höchster Qualität im Einsatz ist. Das nicht aufgeschmolzene Pulver aus dem Arbeitsbereich wird gesiebt und für die Wiederverwendung vorbereitet – alles unter einer Inertgasatmosphäre in einem geschlossenen Kreislauf. Dadurch wird nicht nur die Oxidation oder Feuchtigkeitsbildung minimiert, sondern auch die mögliche Exposition des Bedieners gegenüber dem Pulver verringert – ein wichtiger Sicherheitsaspekt. Für andere Kunden erleichtert das rePLUG Pulvermodul den Wechsel zwischen verschiedenen Materialien erheblich. Das rePLUG Modul und die einfache Reinigung der zugehörigen Komponenten machen die LASERTEC 30 SLM 3. Generation zur Maschine mit dem schnellsten Materialwechsel auf dem Markt.
Neue Bauaufträge ohne Wartezeit
DMG MORI konnte die Effizienz der LASERTEC 30 SLM 3. Generation zusätzlich steigern, weil nun auch ein schneller Wechsel des Baucontainers möglich ist. Anwender müssen nicht mehr warten, bis der Bauauftrag abgekühlt ist. Abdeckungen für den Baucontainer und den Arbeitsraum werden während des Betriebs im Arbeitsraum gelagert. Sie dienen dazu, den Baucontainer bei der Entnahme zu verschließen und die Inertgasatmosphäre in der Maschine zu erhalten. Der nächste Bauauftrag kann so ohne erneute Inertgasflutung schnell gestartet werden.
Prozesssicherheit durch effizientes Monitoring und einfache Bedienung
Eine Kameraüberwachung des Pulverbetts stellt eine hohe Bauteilqualität sicher und minimiert Prozessunterbrechungen. Nach jeder Schicht wird die Oberfläche auf Anomalien gescannt, bevor sich der Beschichter bewegt. Für den Fall, dass ein Vorsprung nicht rechtzeitig erkannt wird, ist der bidirektionale Beschichter mit einem Kollisionsschutzmechanismus ausgestattet.
Der neu konzipierte Gasvolumenstrom über dem Pulverbett gewährleistet eine gleichmäßige laminare Strömung während des Prozesses. Der sekundäre Gasstrom unterhalb des Schutzglases verhindert die Bildung von Verschmutzungen auf dem Schutzglas. Ein innovatives Schutzglasmonitoringsystem überwacht das Schutzglas während des gesamten Prozesses und warnt vor Verschmutzungen. Eine zusätzliche Beleuchtung des Schutzglases unterstützt die einfache Überprüfung und Reinigung zwischen den Baujobs.
Die Benutzerfreundlichkeit und Ergonomie der Maschine stehen bei DMG MORI im Mittelpunkt. Die neue CELOS X Bedienumgebung führt durch alle Schritte des Druckjobs, von der Reinigung des Sicherheitsglases bis zur Nachfüllung von Pulver und täglichen Wartungsarbeiten. Diese Anleitung gewährleistet sichere sowie effiziente Arbeitsabläufe und senkt die Eintrittshürden insbesondere für Technologieeinsteiger erheblich.
DMG MORI auf der formnext 2024
19. - 22. November 2024
Halle 12-0, D 139
https://event.dmgmori.com/en/events/formnext-messe-frankfurt-2024
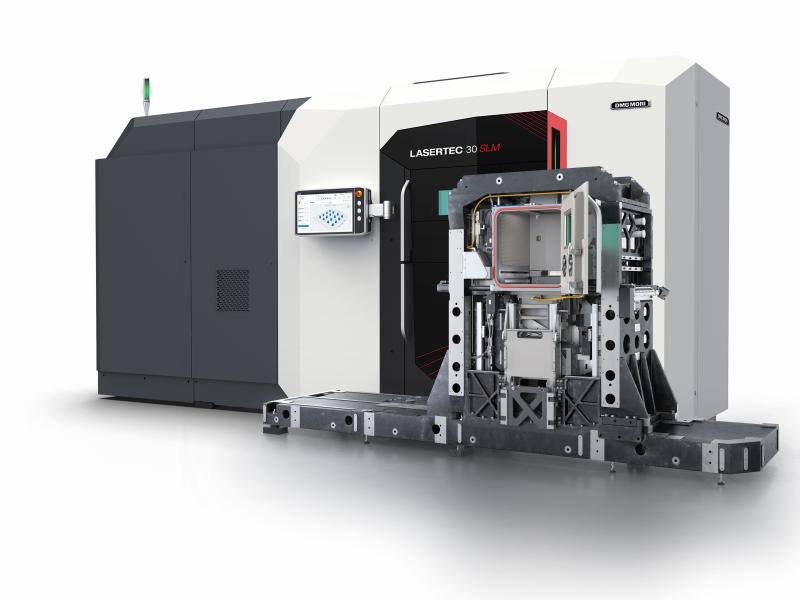
Auf der diesjährigen formnext in Frankfurt demonstriert DMG MORI vom 19. bis zum 22. November 2024 die jüngsten Entwicklungen im Bereich der additiven Fertigung. Das Highlight der Ausstellung in Halle 12-0 ist die kürzlich vorgestellte LASERTEC 30 SLM 3. Generation. Ihr Design basiert zu 100 Prozent auf den langjährigen Erfahrungen in der Konstruktion stabiler Werkzeugmaschinen. Die Prozesskette rund um die additive Fertigung komplettiert DMG MORI mit der DMU 60 eVo. Auf ihr werden – dank des Palettenhandlings PH Cell 300 – im Pulverbett gedruckte Bauteile hochpräzise fertig bearbeitet. Das Potenzial einer durchgängigen Prozesskette ist auch am Beispiel der LASERTEC 65 DED hybrid zu sehen. Die Hybridmaschine vereint additive Fertigung mittels Pulverauftragschweißen und hochpräzises 5-Achs-Simutanfräsen in einem Arbeitsraum. Sie verfügt über einen vollintegrierten, automatisierten DMG MORI scan3D Laserscanner für Reparaturanwendungen und repräsentiert auf eindrucksvolle Weise das Konzept der Machining Transformation (MX), mit dem der Werkzeugmaschinenhersteller die Zukunft der Fertigung gestaltet: Die Integration von additiver Fertigung und CNC-Bearbeitung in einem Arbeitsraum, das automatisierte Scannen reparaturbedürftiger Werkstücke und digitalisierte Abläufe ermöglichen eine ressourcenschonende und damit nachhaltigere Nutzung von Maschinen und Komponenten. Um die weitreichenden Möglichkeiten der additiven Fertigung zielführend einzusetzen, hat DMG MORI die ADDITIVE INTELLIGENCE gegründet. Die Beratungseinheit der DMG MORI Academy, hat es sich zur Aufgabe gemacht, Prozesse rund um die Herstellung komplexer Produkte nachhaltig zu optimieren – 3D-Druck, Digitalisierungsmaßnahmen, automatisiertes Handling und der Einsatz innovativer Bearbeitungstechnologien sind wesentliche Bestandteile der ganzheitlichen Fertigungslösungen.
LASERTEC 30 SLM 3. Generation: robust, zuverlässig und präzise
Ein perfektes Beispiel für Innovation ist die auf der vergangenen Hausausstellung in Bielefeld vorgestellte LASERTEC 30 SLM 3. Generation. Die Pulverbettmaschine baut auf den Stärken ihrer Vorgänger auf und erfüllt die wachsenden Anforderungen eines dynamischen Marktes. So bietet der neue Quad-Laser eine vollständige Überlappung der Scanfelder in einem Bauvolumen von 325 x 325 x 400 mm. DMG MORI hat die LASERTEC 30 SLM 3. Generation mit umfangreichem Knowhow aus dem Werkzeugmaschinenbau konstruiert. Analog zu Fräs- und Drehmaschinen werden in der LASERTEC 30 SLM 3. Generation Gussteile für den Rahmen verwendet. Diese Bauweise garantiert höchste Steifigkeit und optimale Fertigungsbedingungen, sodass die Neuentwicklung Robustheit und Wiederholgenauigkeit neu definiert.
Während bei herkömmlichen Werkzeugmaschinen dynamische Kräfte durch Achsbewegungen entstehen, sind thermische Veränderungen die größte Herausforderung in der additiven Fertigung im Pulverbett. Auch hier profitiert die LASERTEC 30 SLM 3. Generation von der Erfahrung im Werkzeugmaschinenbau. Die Prozesskammer ist innerhalb des thermosymmetrischen Gussrahmes schwimmend gelagert und kann sich bei Temperaturschwankungen frei ausdehnen. Gleichzeitig sind die Optikmodule fest auf dem Gussrahmen montiert. Eine präzise Kalibrierung des Beschichters mittels einer Referenzfläche gewährleistet einen konstanten Abstand zwischen Optik und Pulverbett, zusätzlich unterstützt durch eine aktive Temperaturkompensation der Positionierung in der Z-Achse. Diese effektive Lösung vermeidet Qualitätsprobleme, die aus Abstandsänderungen zwischen Optik und Pulverbett sowie Schwankungen in der Schichtdicke resultieren.
rePLUG: Schneller Materialwechsel über geschlossene Pulvermodule
Ein entscheidender Wettbewerbsvorteil der LASERTEC SLM Serie sind die rePLUG-Pulvermodule von DMG MORI, die die Zeit zwischen den Fertigungsaufträgen verkürzen und die Flexibilität erhöhen. Das rePLUG-Pulvermodul ist eine in sich geschlossene, automatisierte Einheit für das Metallpulvermanagament, die gegen andere rePLUG-Einheiten ausgetauscht werden kann. Bestehende Kunden mit zertifizierten Prozessen, wie sie häufig in der Luft- und Raumfahrt sowie in der Medizintechnik anzutreffen sind, schätzen und verlassen sich auf das rePLUG-System, um sicherzustellen, dass kontinuierlich Pulver von höchster Qualität im Einsatz ist. Das nicht aufgeschmolzene Pulver aus dem Arbeitsbereich wird gesiebt und für die Wiederverwendung vorbereitet – alles unter einer Inertgasatmosphäre in einem geschlossenen Kreislauf. Dadurch wird nicht nur die Oxidation oder Feuchtigkeitsbildung minimiert, sondern auch die mögliche Exposition des Bedieners gegenüber dem Pulver verringert – ein wichtiger Sicherheitsaspekt. Für andere Kunden erleichtert das rePLUG Pulvermodul den Wechsel zwischen verschiedenen Materialien erheblich. Das rePLUG Modul und die einfache Reinigung der zugehörigen Komponenten machen die LASERTEC 30 SLM 3. Generation zur Maschine mit dem schnellsten Materialwechsel auf dem Markt.
Neue Bauaufträge ohne Wartezeit
DMG MORI konnte die Effizienz der LASERTEC 30 SLM 3. Generation zusätzlich steigern, weil nun auch ein schneller Wechsel des Baucontainers möglich ist. Anwender müssen nicht mehr warten, bis der Bauauftrag abgekühlt ist. Abdeckungen für den Baucontainer und den Arbeitsraum werden während des Betriebs im Arbeitsraum gelagert. Sie dienen dazu, den Baucontainer bei der Entnahme zu verschließen und die Inertgasatmosphäre in der Maschine zu erhalten. Der nächste Bauauftrag kann so ohne erneute Inertgasflutung schnell gestartet werden.
Prozesssicherheit durch effizientes Monitoring und einfache Bedienung
Eine Kameraüberwachung des Pulverbetts stellt eine hohe Bauteilqualität sicher und minimiert Prozessunterbrechungen. Nach jeder Schicht wird die Oberfläche auf Anomalien gescannt, bevor sich der Beschichter bewegt. Für den Fall, dass ein Vorsprung nicht rechtzeitig erkannt wird, ist der bidirektionale Beschichter mit einem Kollisionsschutzmechanismus ausgestattet.
Der neu konzipierte Gasvolumenstrom über dem Pulverbett gewährleistet eine gleichmäßige laminare Strömung während des Prozesses. Der sekundäre Gasstrom unterhalb des Schutzglases verhindert die Bildung von Verschmutzungen auf dem Schutzglas. Ein innovatives Schutzglasmonitoringsystem überwacht das Schutzglas während des gesamten Prozesses und warnt vor Verschmutzungen. Eine zusätzliche Beleuchtung des Schutzglases unterstützt die einfache Überprüfung und Reinigung zwischen den Baujobs.
Die Benutzerfreundlichkeit und Ergonomie der Maschine stehen bei DMG MORI im Mittelpunkt. Die neue CELOS X Bedienumgebung führt durch alle Schritte des Druckjobs, von der Reinigung des Sicherheitsglases bis zur Nachfüllung von Pulver und täglichen Wartungsarbeiten. Diese Anleitung gewährleistet sichere sowie effiziente Arbeitsabläufe und senkt die Eintrittshürden insbesondere für Technologieeinsteiger erheblich.
DMG MORI auf der formnext 2024
19. - 22. November 2024
Halle 12-0, D 139
https://event.dmgmori.com/en/events/formnext-messe-frankfurt-2024