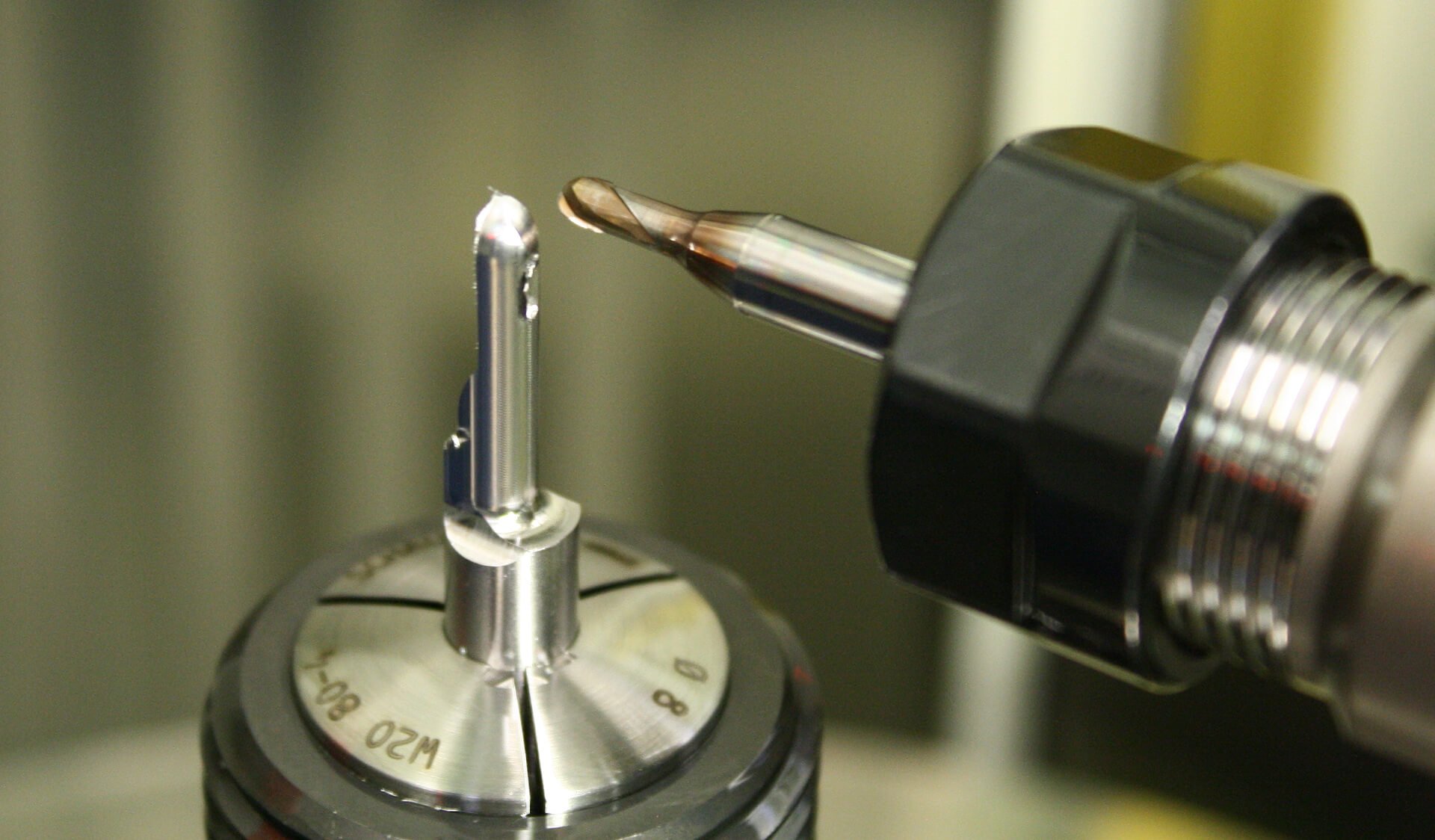
Titelthema
Feingefühl und härtester Stahl
Der Werkzeugbau der Aesculap AG, Tuttlingen, gehört zu den besten in Deutschlands Mittelstand. Vernetzung und der organisatorische Aufbau dieses Bereichs sind dafür ausschlaggebend. Die Abteilung ist hervorragend in die Produktentwicklung eingebunden und fungiert als technologischer Impulsgeber für das Unternehmen, das seit 145 Jahren Medizintechnik herstellt. Die Herausforderungen aus dieser Branche sind klar: Innovationsgeist, Perfektion und Präzision.
„Unser Portfolio umfasst 25 000 Fertigprodukte“, beziffert Hans Keller, Leiter Prototypen- und Werkzeugbau bei Aesculap, die Vielfalt und Innovationskraft des Unternehmens. Vom Implantat für die Orthopädie über Neuro- und Wirbelsäulenchirurgie bis zu Instrumenten für minimal-invasive Zugänge reicht die Palette der Produkte. „Aesculap hat in den 80er Jahren auf die rasante Entwicklung von Spezialdisziplinen der Chirurgie reagiert“, erinnert sich Keller. Diese Flexibilität führte in der Folge beispielsweise zur Entwicklung neuer Produkte für die Mikro-Neuro- und Gefäßchirurgie oder Arthroskopie.
CNC-Technik führt in neue Ära
Die zukunftsorientierte Innovationsbereitschaft zieht sich wie ein roter Faden durch die Unternehmensgeschichte. Ein Großteil des Umsatzes wird mit Produkten erzielt, die weniger als fünf Jahre alt sind. Aufgrund dieser Stärke im Bereich Forschung und Entwicklungen gelten die Spezialisten von der Schwäbischen Alb in der deutschen Medizintechnikbranche als vorbildlich. Die Innovationsbereitschaft geht weit über die Ebene der Produktentwicklung hinaus. Sie betrifft auch die kontinuierliche Optimierung sämtlicher Prozesse und Abläufe, wie die Fertigungstechnik eindrucksvoll unterstreicht.
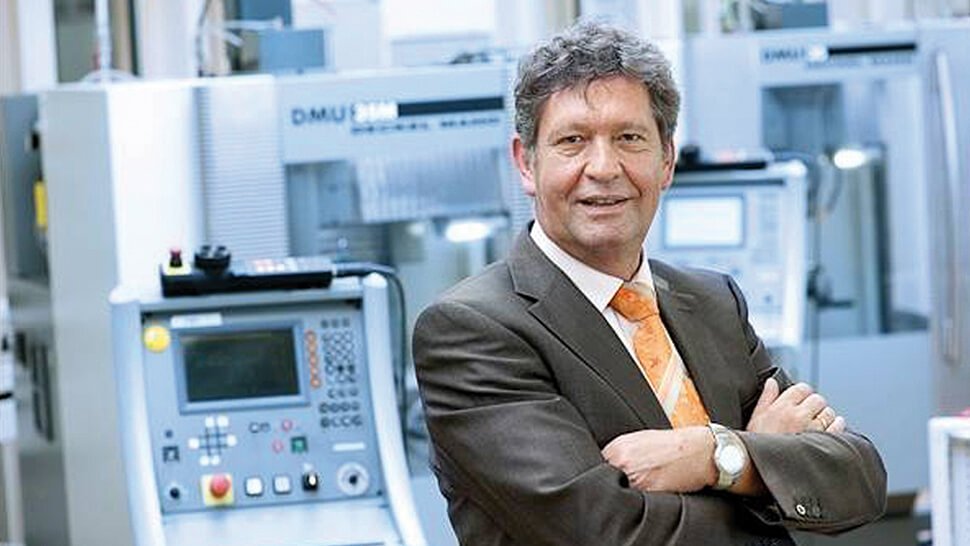
Hans Keller, Leiter Prototypen- und Werkzeugbau. Foto: Aesculap
Spanende Fertigungsprozesse spielen im Produktionsalltag eine bedeutende Rolle. „Der Einstieg in die CNC-Technologie war für uns ein Meilenstein“, erzählt Keller, „wir sind den Schritt sehr früh gegangen. 1988 haben wir unser erstes Bauteil steuerungsunterstützt gefräst.“ Damals wurde mit einer FP3 NC von Deckel gearbeitet, inzwischen sind auch Werkzeugmaschinen von DMG, Grob Hermle oder Willemin im Einsatz. Das zukunftsorientierte Denken gehört zum Firmenalltag. Das Fräsen in allen Facetten wird ständig perfektioniert. Heutzutage gehört es als Kerntechnologie in die Prozesskette der Herstellung von chirurgischen Produkten.
Erwartungen an die CNC-Technik
Auch die Werkzeugmaschinen müssen noch kleiner und genauer werden, fordert Keller. „Die Werkzeuge für die Fertigung der Implantate sind bereits immer genauer und immer komplexer geworden“, erläutert er die Herausforderung, immer präziser zu produzieren. Bei der Genauigkeit ist Aesculap bereits in den Mikrometerbereich vorgedrungen. „Und die Drehzahl muss sich stark steigern“, blickt Keller in die Zukunft. Derzeit wird mit 42 000 Umdrehungen gearbeitet, aber „wir brauchen 90 000 Umdrehungen pro Minute, weil die Fräser immer kleiner werden, denn der Chirurg will immer kleinere Instrumente.“ Während früher in einem Zwölf-Millimeter-Rohr die Instrumente zehn Millimeter groß waren, werden jetzt beispielsweise im Kopfbereich bereits drei Millimeter verlangt.
„Wir müssen das 3D-Fräsen und die 5-Achs-Bearbeitung beherrschen“, heißt es bei Aesculap. Die Umformwerkzeuge für das Warmschmieden in einer Spindelpresse werden immer besser und formstabiler. Gleichzeitig kommt es auch auf die Beschichtung der Werkzeuge sowie auf die Haltewerkzeuge an und auf die Integration von Elektropoliervorrichtungen oder Handhabungsanlagen.
Besonders wichtig ist dem Leiter des Prototypen- und Werkzeugbaus, dass „die Werkzeugmaschinen stabiler werden“, stöhnt er: „Die Reparaturanfälligkeit ist zu hoch!“ Und fast noch schwieriger ist der richtige Service: „Die Reaktionszeit mancher Firma ist nicht akzeptabel.“
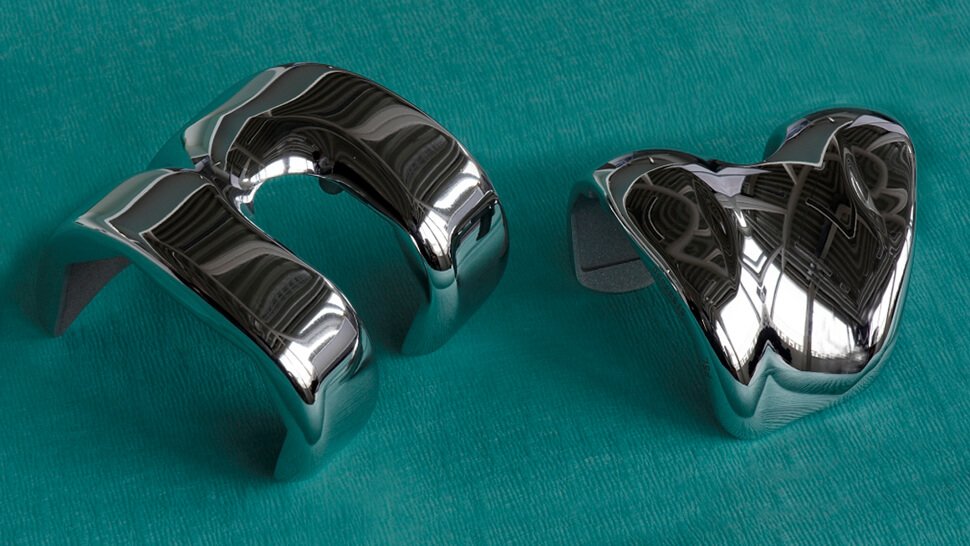
Fotos: Aesculap
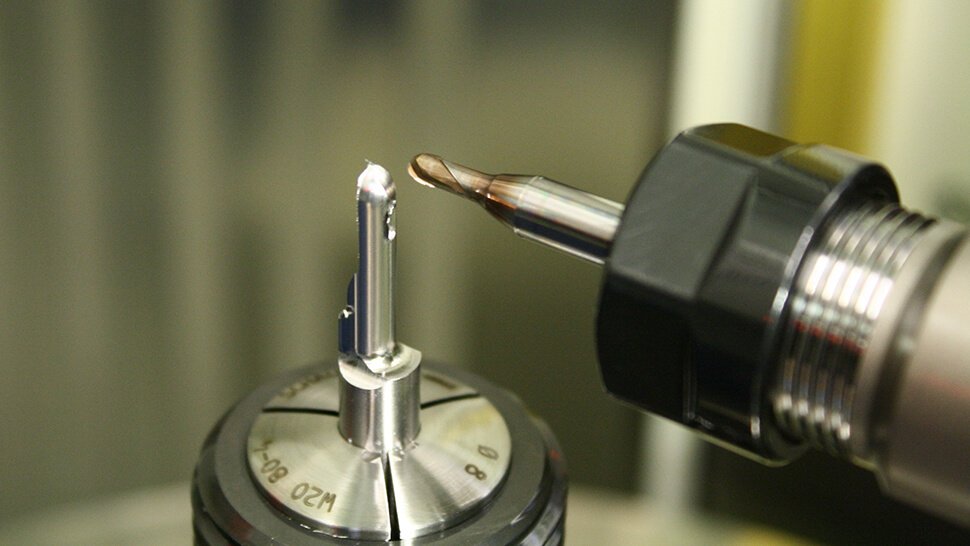
Weltweite Standards
Die Bedeutung der Frästechnologie spiegelt den Verantwortungsbereich Kellers anschaulich wider, denn allein im Prototypenbereich stehen die Werkzeugmaschinen wie Perlen an einer Schnur aufgereiht. Die jüngsten Anschaffungen der Abteilung sind eine DMU 50 und eine HSC55 von DMG, eine HSC Fräsmaschine von DIGMA, eine CNC Messmaschine Helicheck Pro von Walter, sowie eine Erodiermaschine Agie Cut 2000.
In den hohen Fertigungsanforderungen sieht Keller den Grund für den modernen Maschinenpark: „Wir bearbeiten ausschließlich schwer zerspanbare Materialien, benötigen mindestens fünf Achsen für die komplexen Geometrien und haben sehr kleine Toleranzen.“ Bearbeitungszentren, die sich im Prototypenbau bewährt haben, finden auch schnell Einzug in die Serienfertigung - die Zusammenarbeit der einzelnen Werke in Tuttlingen hat sich bewährt. Das gesammelte Know-how im Bereich der CNC-Bearbeitung und der einheitliche Maschinenpark sind der Grund dafür, dass der Standort Tuttlingen inzwischen weltweit für die Entwicklung und Fertigung verantwortlich zeichnet. Dem Leitmotiv „Sharing Expertise“ folgend wird das Wissen der B.-Braun-Mitarbeiter untereinander weltweit geteilt.
Produktiv bei höchster Härte
Die Entwicklung der CNC-Frästechnik, insbesondere bei den besonders harten Metallen, beobachtet Keller genau: „Seit einigen Jahren arbeiten wir verstärkt mit schwer zerspanbaren Materialien wie Kobalt-Chrom oder Titan.“ Die Tendenz ist steigend, und damit steigen auch die Ansprüche an die Fräsbearbeitung. Der Toleranzbereich beträgt maximal 50 Mikrometer in beide Richtungen. Diesen Ansprüchen werden nur robuste und vielseitige Bearbeitungszentren gerecht. „Die Herstellung hochwertiger medizintechnischer Bauteile rechnet sich nur, wenn die Produktivität stimmt“, betont der Leiter des Werkzeugbaus.
Das 5-achsige Simultanfräsen wird als Kerntechnologie betrachtet; es hat maßgeblich zur Produktivitätssteigerung beigetragen. Der kommende Innovationssprung ist bereits fest im Blick: „Im nächsten Schritt werden wir die Fertigungsprozesse weiter optimieren, indem wir sie verstärkt automatisieren – speziell am Standort Tuttlingen im Bereich Orthopädie und Chirurgie.“
Kontakt
Wolfgang Kunz
Werkzeugtechnologie
F & E Prototypenbau
Aesculap AG
Tel. +49 7461 95-2727
E-Mail senden
Anzeige
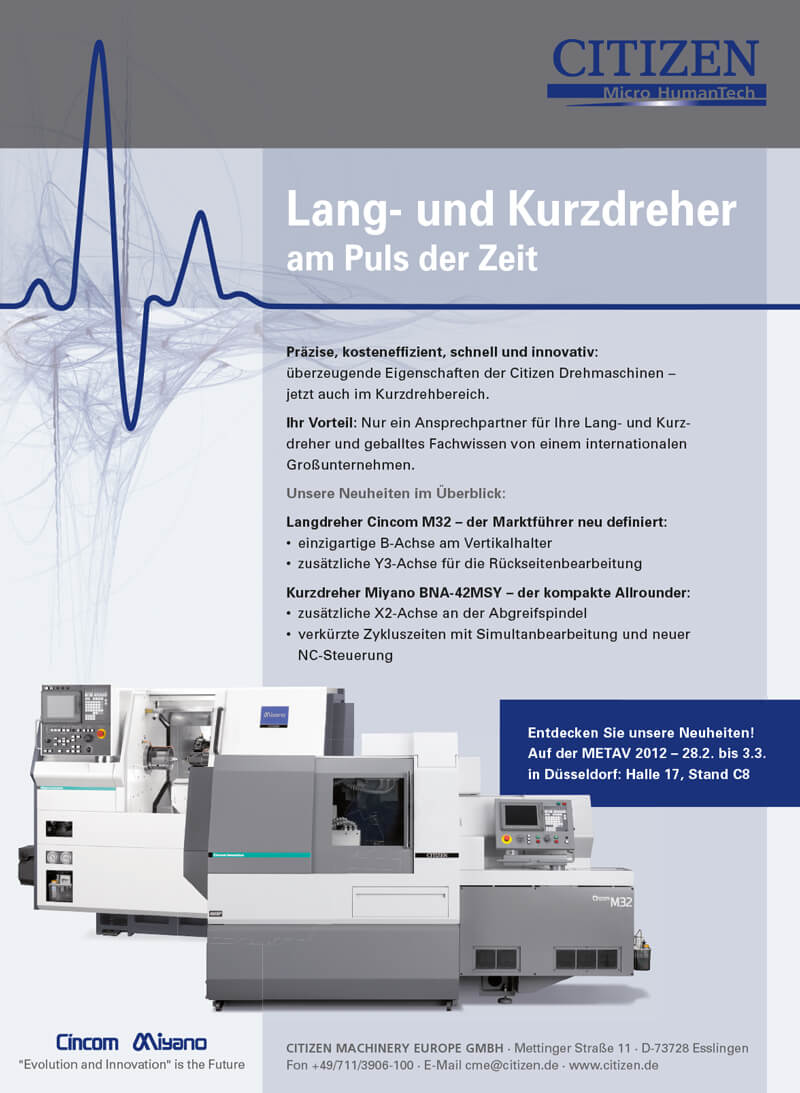