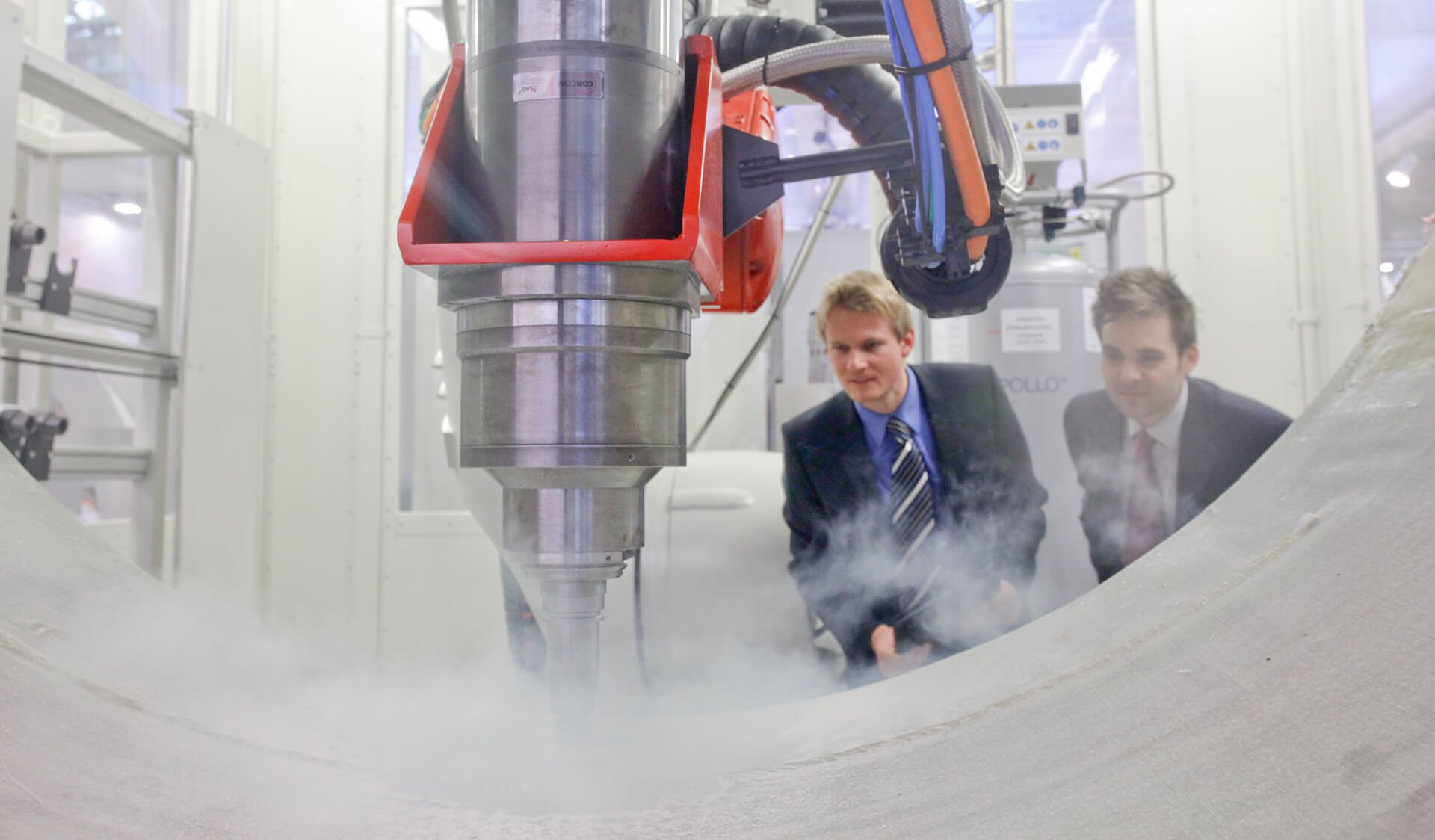
Titelthema
GFK-Bearbeitung mit Stickstoffkühlung
Die durch Reibung, Scherung und Abrieb an der Schneide erzeugte Wärme stellt bei der Bearbeitung von glasfaserverstärktem Kunststoff (GFK) ein echtes Problem dar. Dieser Verbund aus Kunststoff (Harz) und Glasfasern ist ein schlechter Wärmeleiter, zudem neigt er durch die in der Schnittzone entstehende Hitze zum Verfransen und zu Verformungen.
Materialbedingt muss die Bearbeitungstemperatur von GFK unterhalb der Aggregat-Übergangstemperatur des Harzsystems liegen (bei Epoxid etwa zwischen 70 und 160 Grad Celsius). Der Werkstoff ist dann spröde, bei höheren Temperaturen verschmiert jedoch das Harz. Ebenfalls spröde und zudem stark abrasiv wirkend verhält sich das Glasfasermaterial.
Auch erreicht bei der konventionellen Schneidenkühlung, die vor allem auf Span, Halter und Werkstück gerichtet ist, das Kühlmittel die Schneidkante nur bedingt. Mit zunehmender Schnittgeschwindigkeit erhöht sich zudem maßgeblich die Schneidentemperatur, so dass bei Überschreiten einer kritischen Geschwindigkeit der Werkzeugverschleiß stark ansteigt. Daraus ergibt sich zwangsläufig eine Einschränkung der Produktivität.
Minus 196 Grad
Speziell für solche Problemstellungen hat der Werkzeugmaschinenhersteller MAG deshalb eine Lösung entwickelt, die Schneide und Schneidkörper von innen mit Flüssigstickstoff kühlt. Diese sogenannte kryogene Zerspanung der MAG IAS LLC mit Spindel/Werkzeug-Innenkühlung bei minus 196 Grad direkt an der Schneide wirkt effektiver als alle bisherigen Methoden. Sie ermöglicht so erheblich höhere Schnittgeschwindigkeiten und damit eine höhere Zerspanungsproduktivität und längere Werkzeugstandzeiten.
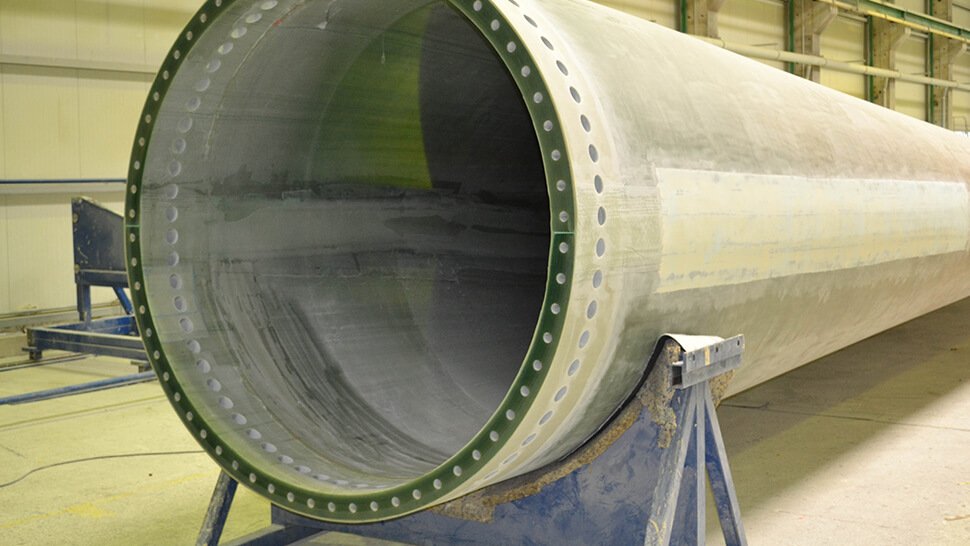
Der Schlüssel für die Effizienz des Flüssigstickstoff-Kühlsystems liegt in der Fähigkeit, den Kühleffekt im Körper des Schneideinsatzes zu konzentrieren. „Die kryogene Bearbeitung war nie zuvor so wirkungsvoll wie jetzt, da wir die Kühlung durch die Spindel direkt an das Zentrum des Schneidstoffs leiten können“, erläutert Dr. Wolfgang Horn, MAG Vice Chairman Technology Global. „Werkzeug-Innenkühlung ist das effektivste Wärmetransportmodell und verbraucht die geringste Menge Flüssigstickstoff. Beim Fräsen und Feinbohren liegt der Verbrauch bei etwa 0,04 Litern pro Minute und Schneide.“
Kein Schmiermittel
Der flüssige Stickstoff verflüchtigt sich durch die beim Zerspanprozess entstehende Hitze. Im Gegensatz zu herkömmlichen Kühlmitteln entfällt die Belastung für Mensch und Umwelt. Die Trockenbearbeitung senkt zudem Fertigungskosten, da sowohl die Ausgaben für flüssiges Kühlschmiermittel entfallen als auch geringere Werkstückreinigungskosten entstehen.
Ein zusätzlicher Kostenvorteil ergibt sich aus der Umweltfreundlichkeit des Kühlmittels. Es muss kein Sprühnebel aufgefangen werden, es gibt weder Filtration noch nasse Späne, kontaminierte Werkstücke oder Kühlmittel-Entsorgungskosten. Durch den Wegfall der Pumpen, Ventilatoren und Antriebe für den Umgang mit Kühlmitteln ist zudem der Energieverbrauch wesentlich geringer.
Hart am Wind
Glasfaserverstärkter Kunststoff ist beispielsweise bei Herstellern von Windkraftanlagen ein gängiger Werkstoff. Speziell für die Bearbeitung der Wurzel-Enden von Rotorblättern hat MAG nun sogar eine robotergestützte Maschine für die kryogene Bearbeitung entwickelt. Sie ist exakt auf Blattdesign, Lochkreisdurchmesser, Material, Durchsatz und Genauigkeit abgestimmt, und aufgrund der stabilen Prozesstemperatur durch das Flüssigstickstoff-Kühlsystem bringt sie erhebliche Verbesserungen mit sich.
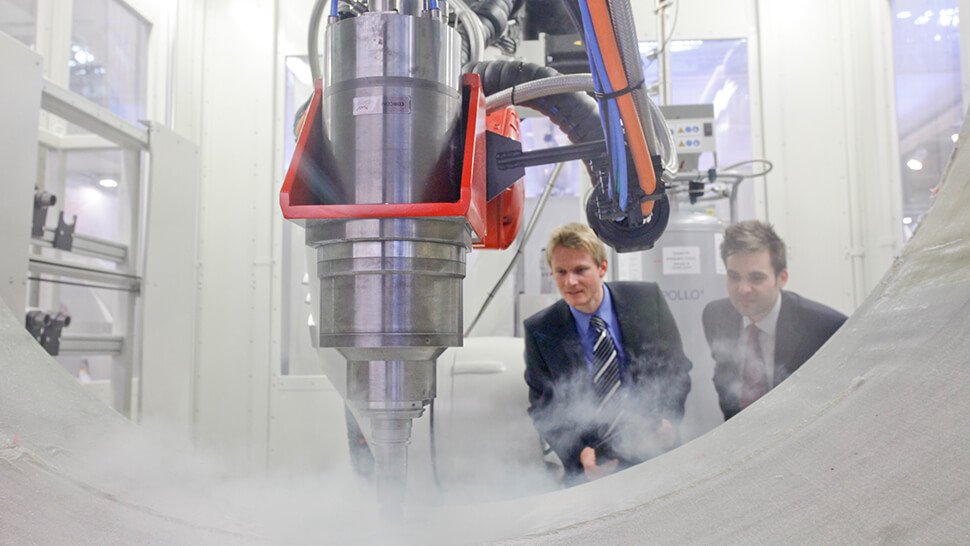
Trotz des schwierig zu bearbeitenden Materials sind die Prozesssicherheit und damit die Produktivität wesentlich erhöht. Verfahrensschritte und Arbeitsschritte wie Sägen, Fräsen, Längs- und Querbohren laufen in einem Arbeitsbereich von 2,80 Metern vollautomatisiert ab.
Somit steht ein absolut zuverlässiger und hochproduktiver Bearbeitungsprozess mit 6-Achs-Roboter und innengekühlten Spezialwerkzeugen zur Verfügung. Die Gesamtproduktivität bei dieser hochflexiblen Lösung steigt um 20 bis 30 Prozent, die Werkzeuglebensdauer verlängert sich um 30 Prozent, und die Harztemperatur bleibt immer unter 70 Grad.
„Wie kein anderes Werkzeugmaschinenbauunternehmen beherrscht MAG die zerspanende Bearbeitung unter diesen Bedingungen“, sagt Gunter Connert, Leiter des Geschäftsbereichs Erneuerbare Energien bei MAG in Schaffhausen, Schweiz. „Dieses Know-how haben wir nun gekoppelt an eine robotergestützte Fertigung. Durch die kryogene Bearbeitung von GFK erreichen Hersteller von Rotorblättern signifikante Produktivitätssteigerungen, damit werden sie wettbewerbsfähiger.“
Kontakt | Autor
Ralf M. Haaßengier
PRX Agentur für Public Relations GmbH
Kalkhofstraße 5
70567 Stuttgart
Tel. +49 711 7189903
E-Mail senden
www.pr-x.de
Kontakt | Unternehmen
Joachim Jäckl
Leiter PR
MAG Europe GmbH
Stuttgarter Straße 50
73033 Göppingen
Tel. +49 7161 2014083
E-Mail senden