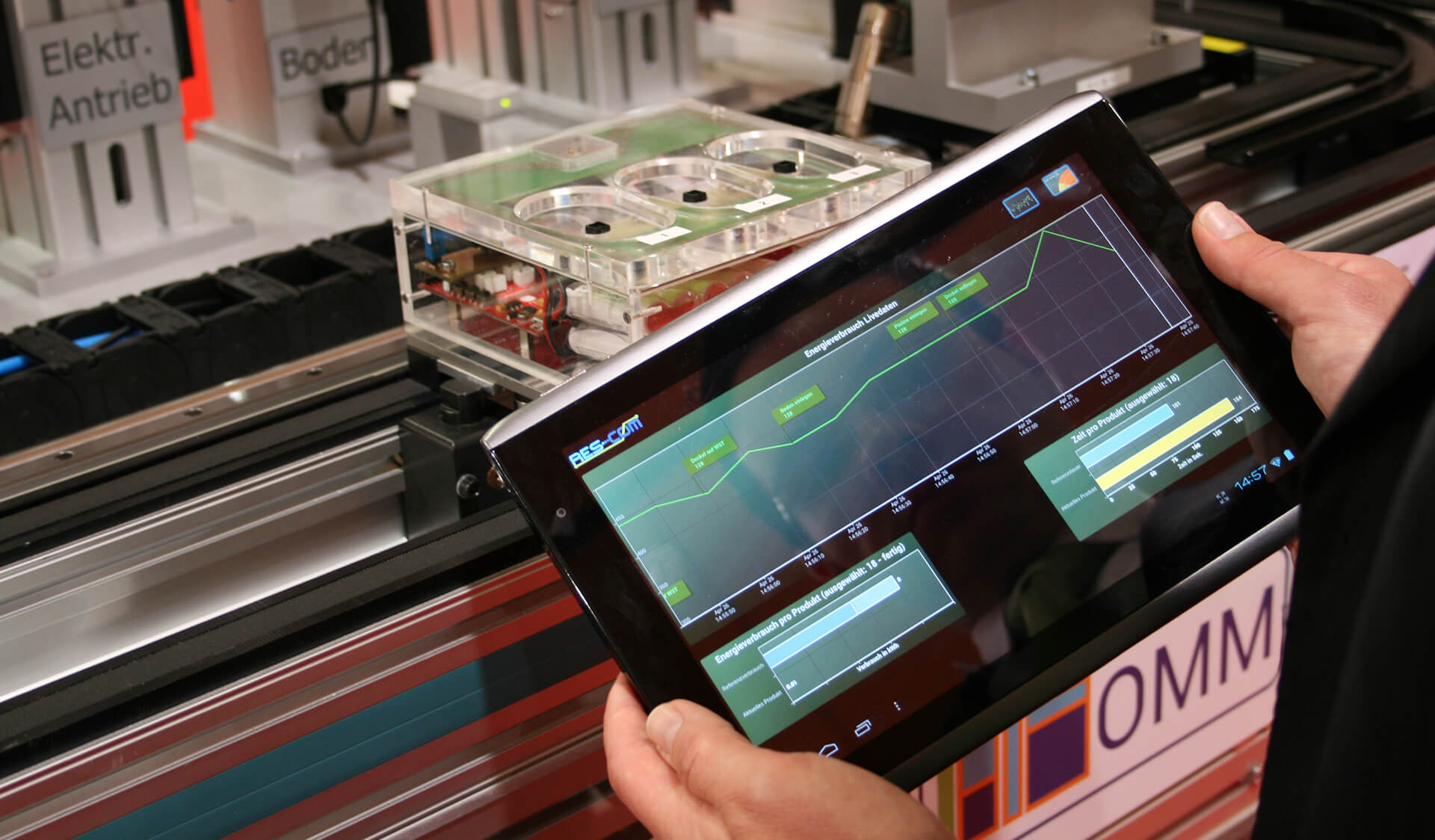
Titelthema
Gut gerüstet für die Zukunft
In der Produktion der Zukunft werden sich Technologien zur Realisierung einer offenen Kommunikationsplattform ausbreiten und zur Ablösung der streng hierarchisierten IT-Landschaft führen. Netzbasierende Dienste, die direkt aus der Produktion heraus angeboten werden können, erlauben die Erschließung neuer Geschäftsfelder im Bereich von Mehrwertdiensten zum Produkt.
Die sich daraus ableitenden Möglichkeiten zur Realisierung optimierter Prozesse und neuer Wertschöpfungsketten bergen genau jene Effizienzpotenziale, die durch die 4. Industrielle Revolution erschlossen werden.
Um in einer vernetzten Welt wettbewerbsfähig zu bleiben, werden Hersteller von Automatisierungstechnik gezwungen sein, sich von ihrem Selbstverständnis eines Produktanbieters zu lösen und sich hin zu einem Anbieter von maßgeschneiderten Lösungen zu entwickeln. Dies wird alleine schon deshalb notwendig sein, weil die Schaffung eines Mehrwerts für den Betreiber einer Anlage zukünftig nicht mehr aus der reinen Bereitstellung von automatisierungstechnischen Komponenten, sondern aus deren prozessbezogener Verbindung mit vorhandenen IT-Systemen resultieren wird.Daneben ist vor allem der Betreiber gefordert. Die Effizienzsteigerung wird wesentlich durch die Optimierung von Prozessen auf Basis von Informationen über Produkte, Anlagen und Prozesse resultieren. Da es Unternehmen in Deutschland in der Vergangenheit gelungen ist, neue technologische Entwicklungen in Produktionsprozesse und Produkte schnell zu integrieren, ist davon auszugehen, dass sich der bevorstehende Paradigmenwechsel bei allen Beteiligten schnell vollziehen wird und sich deutsche Unternehmen sowohl als Leitnutzer als auch als Leitanbieter von Komponenten und Produkten auf Basis so genannter Cyber-Physischer Systeme (CPS) an die Spitze der 4. Industriellen Revolution setzen und auf dem Weltmarkt positionieren werden.
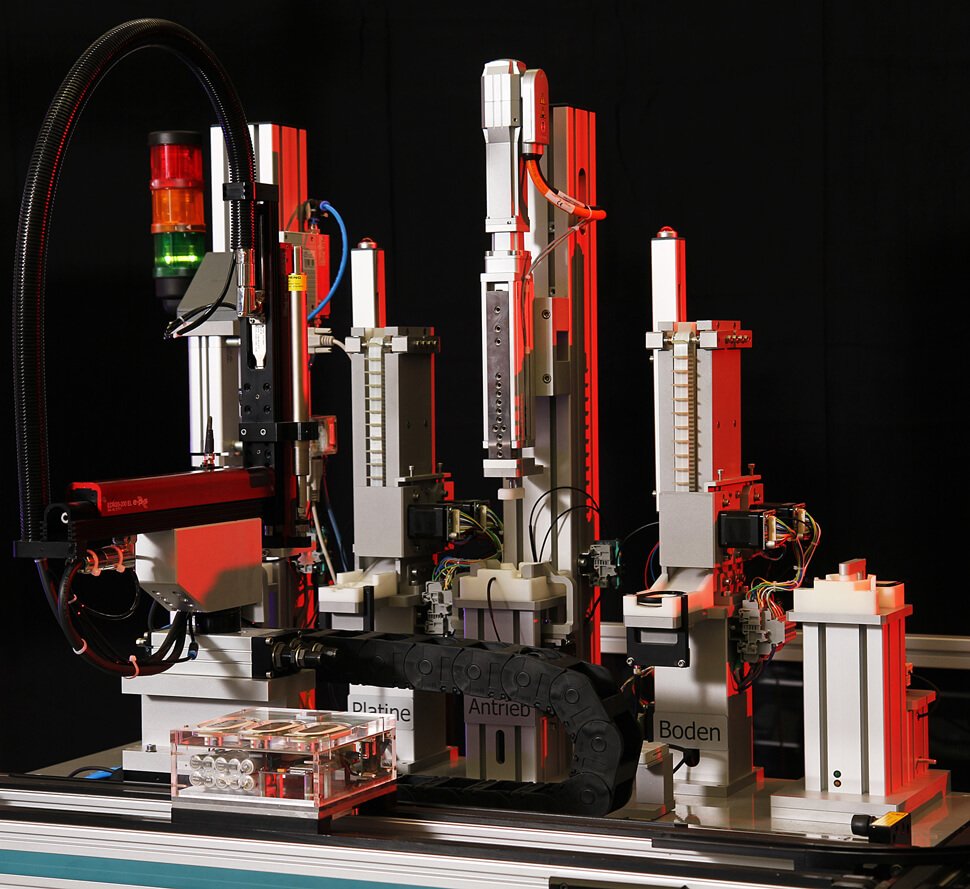
Foto: DFKI
Vernetzung der Steuerungsstrukturen
Nach einer Studie des Deutschen Forschungszentrums für Künstliche Intelligenz (DFKI) aus dem Jahr 2011 ist die Automatisierungspyramide als Strukturierungsmittel für Fabriksysteme immer noch probat. Danach lässt sich aus Sicht der Kommunikationssysteme eine Unterteilung in drei Ebenen vornehmen. Die oberste Ebene repräsentiert das Firmen-Intranet und dient beispielsweise der Vernetzung von ERP, MES und Büroanwendungen. Die mittlere und untere Ebene stellen das Produktionsnetzwerk dar. Auf der mittleren Ebene befinden sich die (speicherprogrammierbaren) Steuerungen und Leitsysteme. Falls eine Vernetzung mit der oberen Ebene eingerichtet ist, dann auf Basis von Standard-Ethernet. Die Verbindung zu den angeschlossenen Feldgeräten in der unteren Ebene geschieht über die unterschiedlichen Feldbusse und industriellen Ethernet-Varianten.
Auch wenn die Kommunikationscharakteristika und die Anwendungen sich auf den verschiedenen Ebenen der Automatisierungspyramide unterscheiden, so ist doch der Wunsch und die Konvergenz zu einem einheitlichen Kommunikationssystem – vorzugsweise auf Basis von Ethernet – deutlich erkennbar. Durch die zunehmende Durchdringung der Fabriken mit CPS-basierenden Komponenten und Produkten ist mit einem starken Zusammenwachsen der heutzutage meist getrennten Bereiche Firmen-Intranet und Produktionsnetzwerk zu rechnen. Basis für das Kollaborieren unterschiedlicher Systeme müssen dann standardisierte Informationsmodelle sein, die mit von Maschinen nutzbaren, offenen Datenformaten beschrieben sind, beispielsweise in XML, mittels Web-Services gekapselt und über ein offenes Netz aufgerufen werden können.
Die herstellerunabhängige Technologie-Initiative SmartFactory am Deutschen Forschungszentrum für Künstliche Intelligenz (DFKI) erprobt und entwickelt mit Partnern aus Industrie und Wissenschaft reale Lösungen und neue Technologien für die Fabrik der Zukunft und leistet Pionierarbeit zur praktischen Umsetzung der Kernaspekte der 4. Industriellen Revolution.
Der Nutzen dieses medienbruchfreien, konfigurationsarmen und durchgängigen Informationszugriffes entsteht durch die Optimierung von Produktions- und Geschäftsprozessen, die zur Erreichung der unternehmerischen Ziele dienen. Besonders in produktionsnahen Aufgabenbereichen großer Komplexität, hoher geforderter Flexibilität und großer Produktvarianten dienen dazu MES-Anwendungen. Der wachsende Einsatz des Internets wird diesen Trend verstärken. MES-Anwendungen sind auf das jeweilige Anwendungsgebiet spezialisiert und für das jeweilige Unternehmen maßgeschneidert. Ein kollaboratives Neben- und Miteinander wird gefordert. Das Anbieten von MES-Anwendungen als Cloud-Service und die Visualisierung mithilfe von Apps liefern Lösungsansätze für diese Forderungen.
Ausgewählte Anwendungsformen
Die zentralen Aspekte der 4. Industriellen Revolution können anhand von drei Paradigmen verdeutlicht werden: das intelligente Produkt („Smart Product“), die kooperierende Maschine („Smart Machine“) und der assistierende Bediener („Augmented Operator“). Das Paradigma des intelligenten Produkts beschreibt die neue Rolle der zu fertigenden Produkte als aktive Systemkomponenten, die durch die Ausstattung mit digitalen Produktgedächtnissen Wissen über den Produktionsauftrag mit sich tragen und ihren Produktionsprozess selbst steuern. Durch das Paradigma der kooperierenden Maschine werden Produktionsmittel zu Cyber-Physischen Systemen, also autonomen Elementen mit lokaler Steuerungsintelligenz, die über offene Netze und semantische Beschreibungen in einem Automatisierungsnetzwerk mit anderen Maschinen, Produkten und Anlagen kommunizieren. Sie sind verteilte, intelligente Objekte, die miteinander vernetzt sind. Im Bereich der Produktionstechnik werden sie auch als Cyber-Physische Produktionssysteme (CPPS) bezeichnet. Das Paradigma des assistierenden Bedieners stellt schließlich den Menschen im Zentrum der Fabrik dar, der durch kontextsensitive Informationsbereitstellung und Augmented Reality unterstützt wird, um die steigende technische Komplexität optimal zu beherrschen.
Diese Kernparadigmen werden in der einzigartigen Demonstrationsanlage der DFKI-SmartFactory in Form einer kompletten Produktionslinie praxisnah vorgestellt. Die modular aufgebaute Anlage zeigt die flexible kundenindividuelle Fertigung eines exemplarischen Produkts, dessen Bauteile (Gehäusedeckel, Gehäuseboden, Platine) in der Anlage gehandhabt, mechanisch bearbeitet und montiert werden.
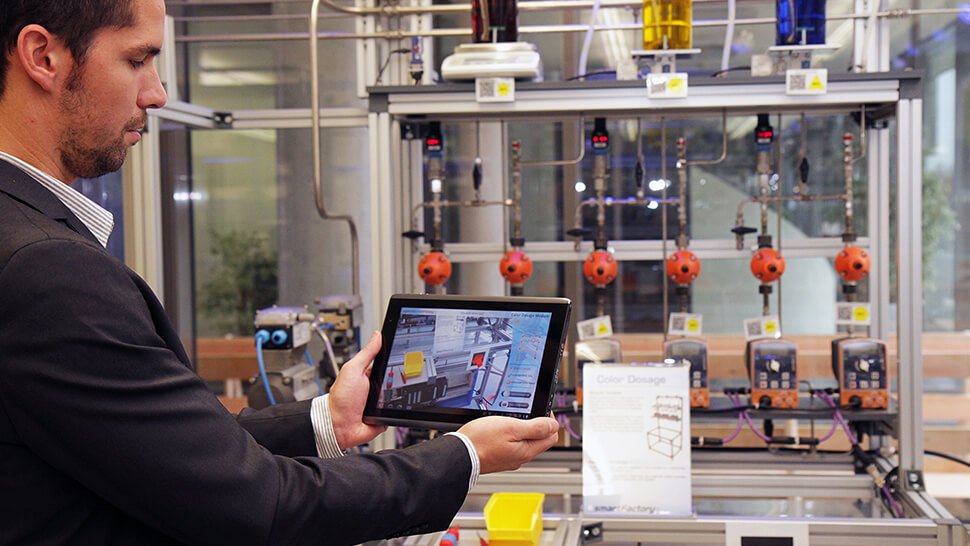
Fotos: DFKI
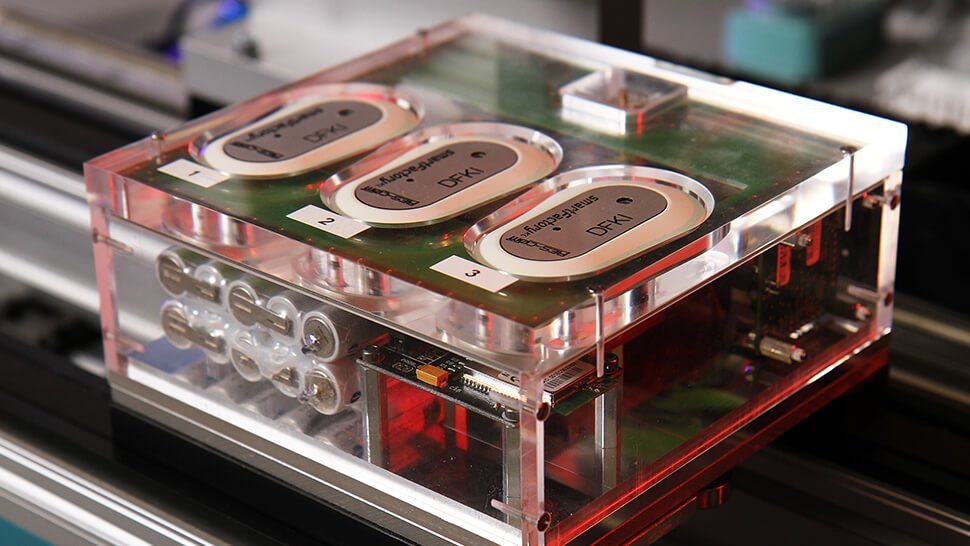
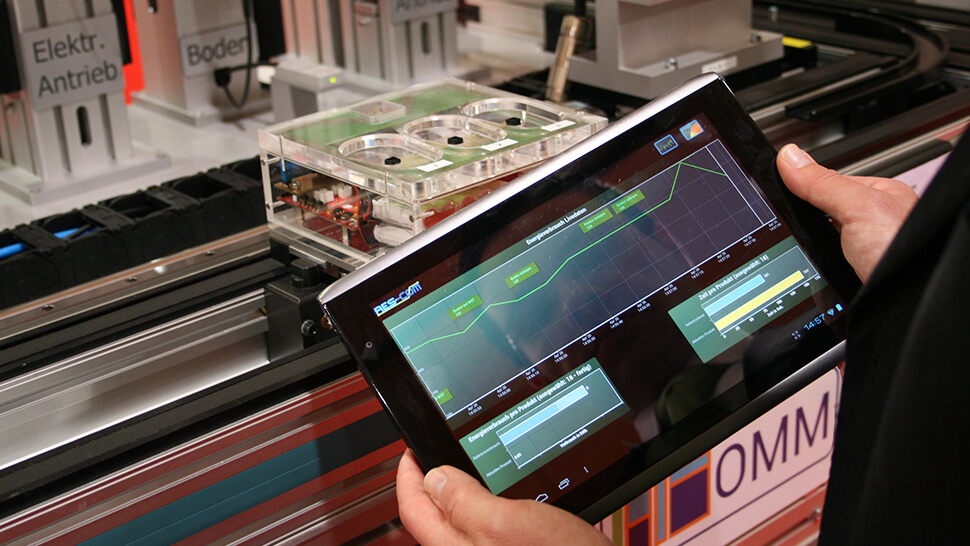
Das intelligente Produkt
Ein Ansatz zur zukünftigen informationstechnischen Verknüpfung der unterschiedlichen Ebenen der Produktion ist die Nutzung des Produkts selbst als Informationsträger. Das individuelle Produkt wird dazu mit einem automatisch auslesbaren Datenträger ausgerüstet. Bei Flüssigkeiten ist die individuelle Kennzeichnung vor der Abfüllung in einen Behälter schwieriger zu realisieren.
Als Denkmodell kann die Chargennummer in Verbindung mit der Prozessinformation aus dem Leitsystem jedoch zur virtuellen Kennzeichnung dienen. Derzeit werden diese Technologien allerdings oft nur unternehmensintern verwendet.
Digitale Produktgedächtnisse stellen demgegenüber ein ganzheitliches Konzept zum technologieunabhängigen Informationsaustausch über die Ebenen des Unternehmens und sogar Unternehmensgrenzen hinweg dar. Dies wird durch einheitliche Datenformate wie das im Rahmen des BMBF-Projekts „SemProM – Semantic Product Memory“ initial entwickelte und unter dem Dach der W3C weiterentwickelte Object Memory Model (OMM) ermöglicht.
Die technische Implementierung des digitalen Produktgedächtnisses kann von einfachen Data-Matrix-Codes oder RFID-basierenden Systemen bis hin zu komplexen und autonom agierenden aktiven digitalen Produktgedächtnissen auf Basis eingebetteter Systeme variieren.
Kontakt
Prof. Dr.-Ing. Detlef Zühlke
Vorstandsvorsitzender und Initiator der SmartFactory
Forschungsbereichsleiter für Innovative Fabriksysteme am Deutschen Forschungszentrum für Künstliche Intelligenz (DFKI) GmbH und
Inhaber des Lehrstuhls für Produktionsautomatisierung an der TU Kaiserslautern
Dr. Jochen Schlick
Stellvertretender Forschungsbereichsleiter für Innovative Fabriksysteme am Deutschen Forschungszentrum für Künstliche Intelligenz (DFKI) GmbH und
Forschungskoordinator der Technologie-Initiative SmartFactory e.V.
Iris Merget
Öffentlichkeitsarbeit & Kommunikation
Innovative Fabriksysteme – IFS & SmartFactory
Deutsches Forschungszentrum für Künstliche Intelligenz (DFKI)
Tel. +49 631 205753406
E-Mail senden
www.dfki.de/ifs