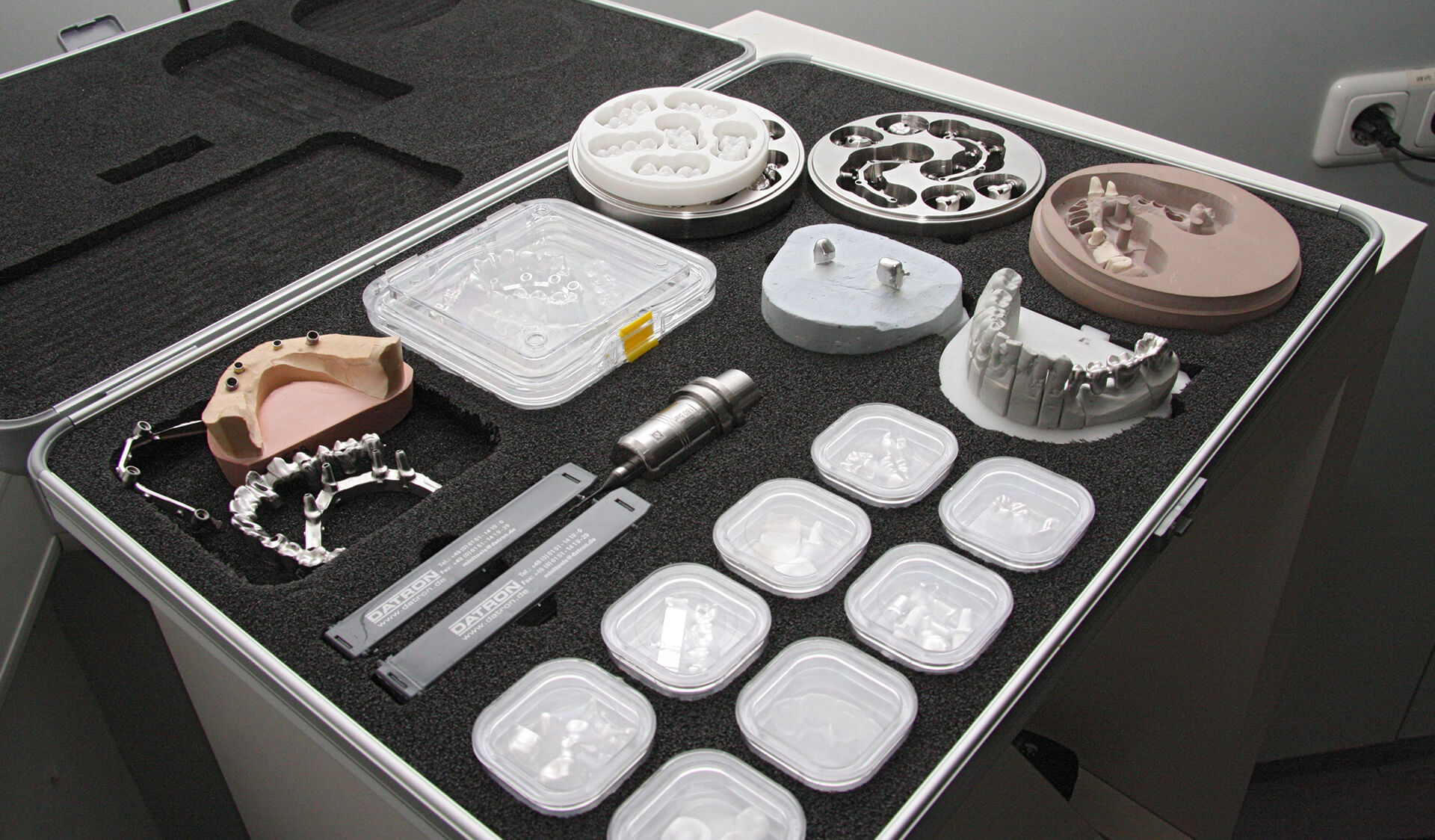
Medizintechnik
Passt perfekt
Die dritten Zähne müssen genau passen, sonst verliert der Patient an Lebensqualität. Fünf-Achs-Fräszentren vollbringen Höchstleistungen, aber der Anwender muss wissen, wo ihre Stärken und Schwächen liegen.
Um die geforderte Genauigkeit und Prozessfähigkeit in der Dentaltechnik zu gewährleisten, wird auch für die dentale Produktionskette zur Überprüfung der Qualität des Bearbeitungszentrums ein genormtes Abnahmebauteil benötigt. Ein Prüfwerkstück auf Rondenbasis ist entwickelt worden, das dem Anwender erstmals erlaubt, die Qualität der Produkte in Beziehung zu den qualitativen Maschinenkennwerten zu setzen.
Die dentale Prozesskette wird in vier Prozessschritte unterteilt. Beginnend mit der digitalen Datenerfassung wird mittels dentalen Scannern die Zahnsituation entweder direkt im Mund oder am Gipsmodell erfasst. Anhand des eingescannten digitalen Abdrucks erfolgt die Modellierung der Brücken und Kronen in der CAD-Software. Die Modelldaten werden in STL-Format konvertiert und an die CAM-Berechnung weitergegeben. Die CAM-Software nutzt Informationen über die unterschiedlichen Werkzeug-, Maschinen- und Materialienparameter mit den zugehörigen Bearbeitungs- und Fertigungsstrategien. Jeder Prozessschritt stellt eine Fehlerquelle und damit ein Risiko für die Erreichung der geforderten Qualität bei der Unikatproduktion dar.
Die Qualitätsprüfung der Endprodukte und das Qualitätsmanagement entlang der digitalen Prozesskette müssen aufgrund der Freiformbauteile grundsätzlich überarbeitet und für die Produkte sowie die eingesetzte Produktionstechnik weiterentwickelt werden. Die bislang zumeist qualitativen Prüfverfahren aus einer traditionellen Handarbeit sind mit zunehmender Automatisierung und gleichzeitig zunehmender Öffnung der Prozessschnittstellen (CAD/CAM-Produktion) nicht zielführend anwendbar. Weiterhin wird besonders bei der Fertigung von Grünlingen (Zirkondioxid) auf Sonder-(Low-Cost-)Komponenten ohne direktes Wegmesssystem gesetzt. Mit diesen material- und maschinenspezifischen Veränderungen ist eine neue Maschinenklasse entstanden.
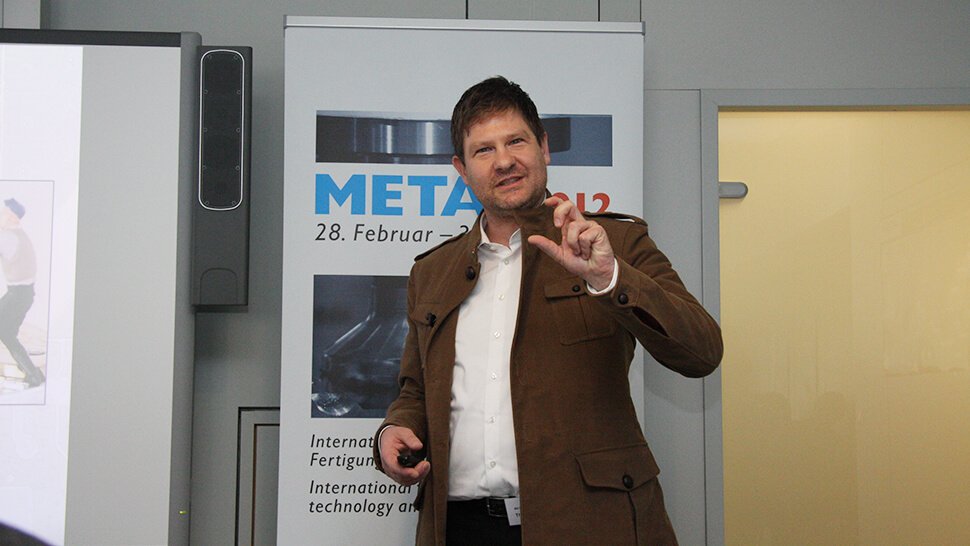
Fotos: Dlugosch
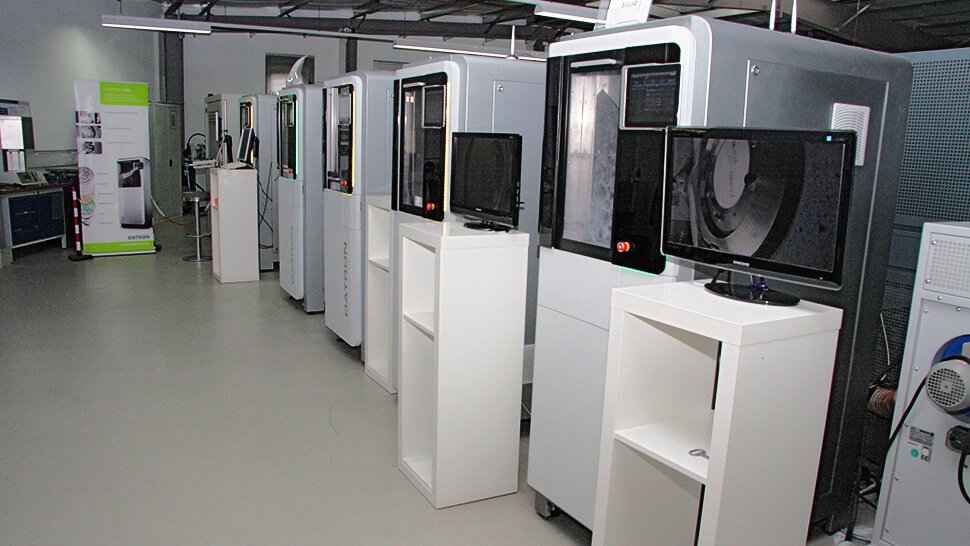
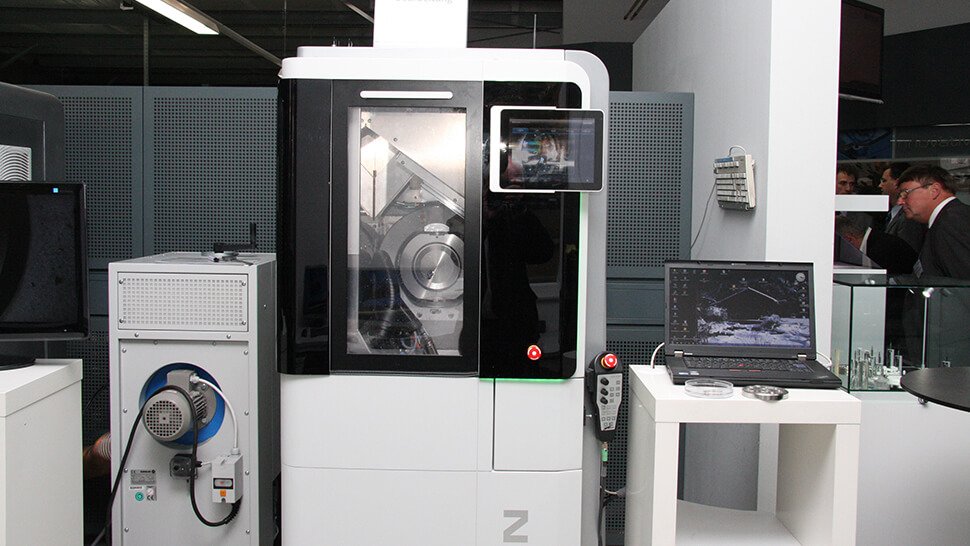
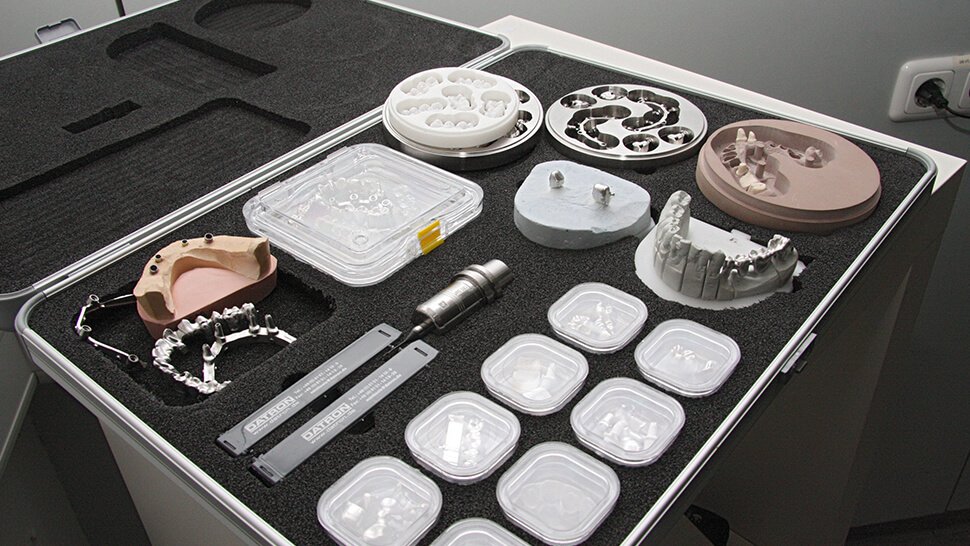
Mit direkten und indirekten Messmethoden können die geforderte Maschinengenauigkeit und die Prozessfähigkeit geprüft werden. Beim direkten Verfahren werden die Merkmale der Vorschubachsen wie Positioniergenauigkeit oder Wiederholgenauigkeit durch Einsatz von Messinstrumenten direkt ermittelt. Bei diesem Verfahren wird ein Fehler durch den Bearbeitungsprozess jedoch nicht beachtet. Beim indirekten Messverfahren werden standardisierte Bauteile gefertigt und anschließend vermessen. Auf Basis der gefertigten Prüfbauteile lassen sich Rückschlüsse auf die Genauigkeit der Werkzeugmaschine ziehen. Ein großer Vorteil des indirekten Verfahrens ist, dass bei diesem Verfahren die Maschinengenauigkeit unter Einfluss des Bearbeitungsprozesses bestimmt wird.
Um die Funktionalität eines Fünf-Achs-Bearbeitungszentrums zu qualifizieren, sind viele unterschiedliche Vorgänge notwendig. Ihre Prüfung im Einzelnen ist mit viel Aufwand verbunden. In solchen Situationen helfen Prüfwerkstücke, um sich einen schnellen Überblick über die wichtigsten Parameter zu verschaffen. So werden nicht nur die statischen Bedingungen betrachtet, sondern auch die dynamischen Prozesse während der Bearbeitung finden Eingang in die Prüfung.
Die spezifischen Randbedingungen (Komponentenstruktur, Achsverfahrwege, Umschlagbearbeitung) für die Herstellung von Dentalimplantaten machten zudem eine Weiterentwicklung der vorhandenen Prüfwerkstücke erforderlich. Das im Rahmen eines Forschungsprojekts entwickelte Prüfwerkstück leistet einen Beitrag zur Vermessung sowie Qualitätssicherung von dentalen automatisierten Prozessketten, indem ein objektiver Maschinenvergleich anhand von über 20 Formelementen ermöglicht wird.
Die Genauigkeiten werden in achsspezifische Positionsabweichungen, Geradheiten sowie Abweichungen aufgrund der Maschinendynamik (drei oder fünf Achsen) und der Genauigkeit einer Umschlagbearbeitung unterschieden und ausgewertet. Somit ist es erstmals möglich, die Toleranzklassen von einzelnen dentalen Produktgruppen auf qualitative Maschinenkennwerte zu beziehen.
Kontakt
Sören Dietz
Wissenschaftlicher Mitarbeiter
Institut für Produktionsmanagement, Technologie und Werkzeugmaschinen (PTW)
Technische Universität Darmstadt
Tel. +49 6151 16-6620
E-Mail senden
Vitali Dejkun
Wissenschaftlicher Mitarbeiter
PTW TU-Darmstadt
Prof. Dr.-Ing. Eberhard Abele
Institutsleiter
Institut für Produktionsmanagement, Technologie und Werkzeugmaschinen (PTW)
Technische Universität Darmstadt