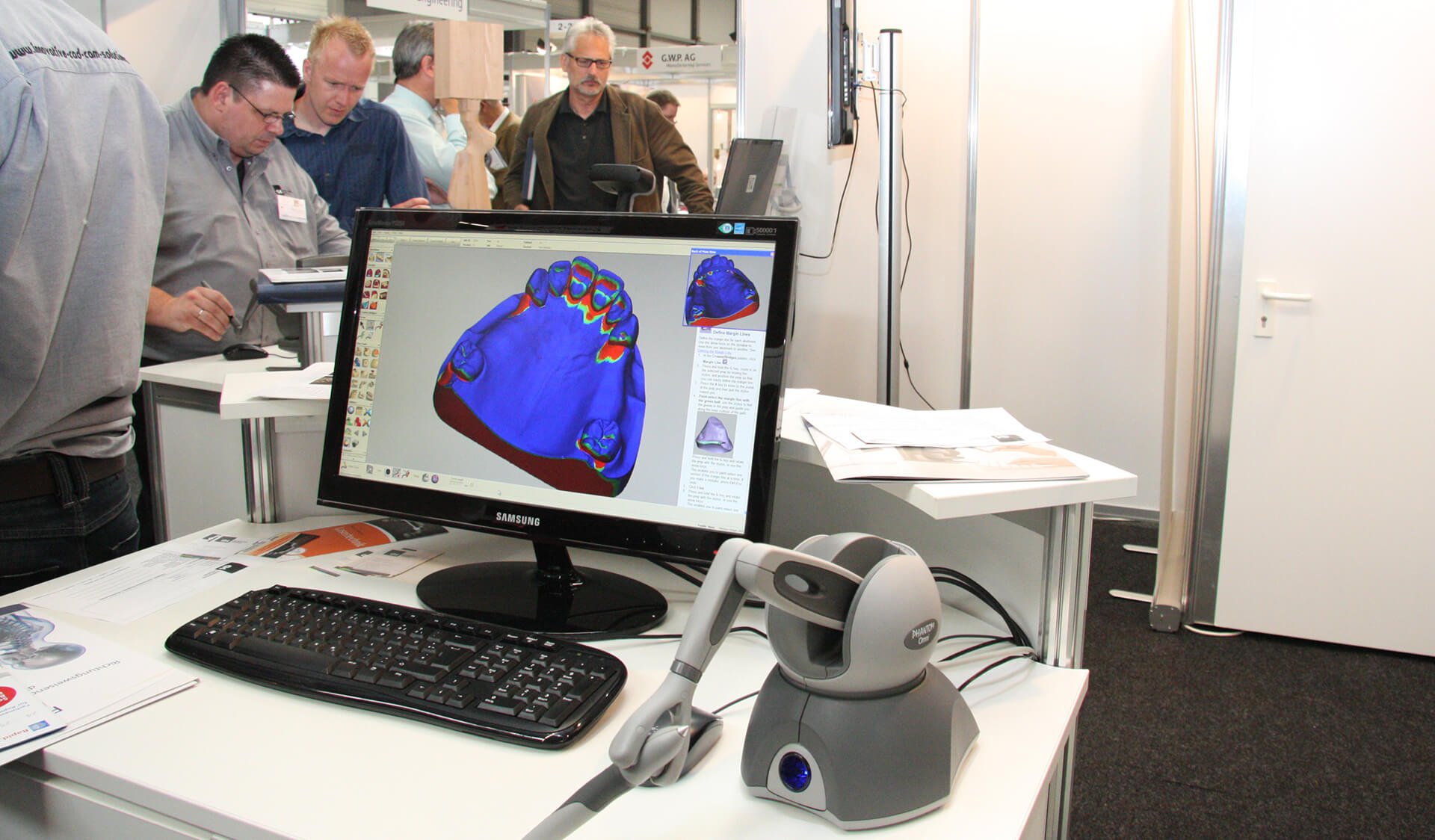
Medizintechnik
Schicht für Schicht
individuell und günstiger
In der Medizin sind passgenaue Produkte immer stärker gefragt. Mit additiver Fertigung lässt sich der Zielkonflikt zwischen Kleinstserien und Wirtschaftlichkeit lösen. Individuell angepasste Produkte für den Patienten sorgen zeitnah und kostengünstig für eine gute medizinische Versorgung.
Additive Fertigung, häufig noch Rapid Prototyping genannt, springt an genau der Stelle ein, wo konventionelle abtragende Verfahren passen müssen: bei Schnelligkeit und Wirtschaftlichkeit. Sie dringt nun auch in die Welt der Mikrobauteile vor.
Eine Form der additiven Technologie nutzt Stereolithographie, um Prototypen aus einem lichtaushärtenden Kunststoff durch Fotopolymerisation zu erzeugen. Im Bereich der Verarbeitung von metallischen Werkstoffen werden Materialien mit einem niedrigschmelzenden Binder benutzt und die vorgesinterten Bauteile in einem folgenden Verfahrensschritt nachverdichtet. Heutzutage kommen auch binderlose Metallpulver zum Einsatz.
Die erreichbare Bauteildichte bis zu 100 Prozent führte zu einer branchenübergreifenden Nutzung der additiven Fertigung, neben der Medizintechnik auch im Werkzeug- und Formenbau, der Luft- und Raumfahrt sowie der Konsumgüterproduktion. Das häufig eingesetzte Verfahren ist das Selektive Laser-Schmelzen (Selective Laser Melting, SLM). Mit Hilfe eines Laserstrahls wird Metallpulver entsprechend den CAD-Konturdaten des Bauteils aufgeschmolzen. Die repetitive Verkettung der Verfahrensschritte Materialauftrag, Belichtungsprozess und Absenken der Bauplattform ermöglicht die Realisierung hochkomplexer Unikate.
Beim Mikrolasersintern werden analog zum SLM die Mikrobauteile additiv generiert. Bedingt durch eine reduzierte Pulverschichtdicke im Bereich von eins bis fünf Mikrometern und einen Laserfokusdurchmesser von 30 Mikrometern können sehr kleine Strukturen und Details realisiert werden. Das Institut für Produktionsmanagement, Technologie und Werkzeugmaschinen der Universität Darmstadt (PTW) untersucht in Kooperation mit Industrieunternehmen den zweckmäßigen Technologieeinsatz intensiv für die Medizintechnik. Weiterentwickelt werden auch Verfahrenskombinationen.

Fotos: Dlugosch
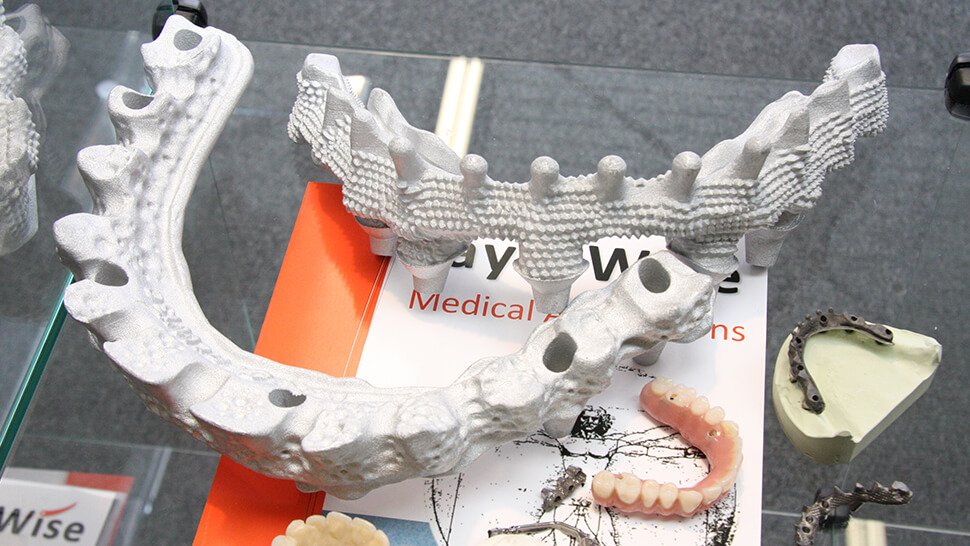
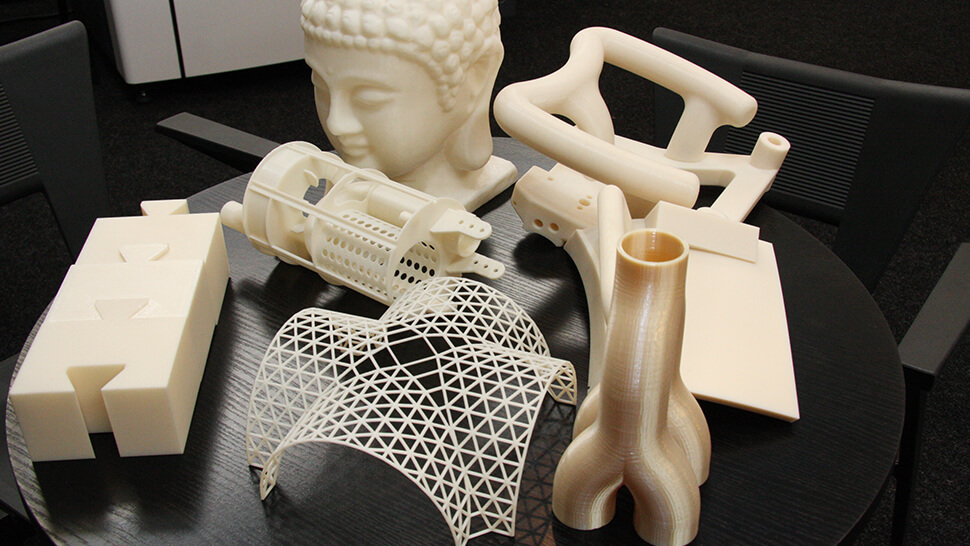
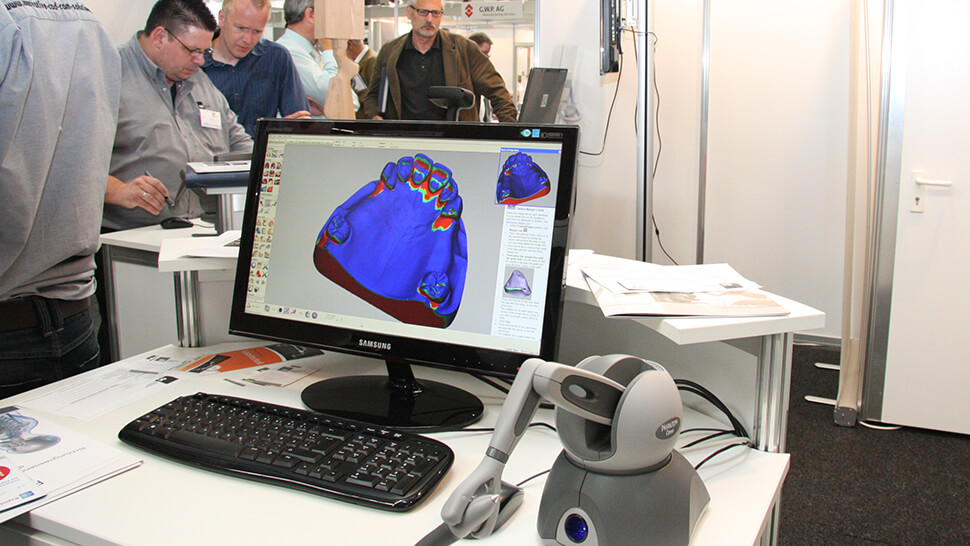
Werkzeuglose Fertigung
Ein besonderes Merkmal der additiven Fertigung ist die Herstellung von Bauteilen ohne werkstückspezifische Werkzeuge mit Endproduktcharakter. Die Materialeigenschaften, insbesondere die Festigkeitskennwerte, sind mit denen von konventionell hergestellten Bauteilen vergleichbar. Verwendete Werkstoffe sind Edelstähle, Aluminium-, Titan- oder Nickelbasislegierungen. Zusätzlich wurden mit Fokus auf die Medizintechnik Materialien wie Reintitan oder Kobaltchromlegierungen für den SLM-Prozess qualifiziert, die neben einer Herstellung von medizinischen Instrumenten oder Gerätebauteilen die Produktion von Implantaten oder Prothesen ermöglichen.
Der Markt der Medizintechnik gilt als der ein Leitmarkt für die additive Fertigung. Wachstumsraten von mehr als 20 Prozent pro Jahr verdeutlichen das hohe Potenzial durch die große Nachfrage nach patientenindividuellen Teilen. So werden in der Dentaltechnologie Zahnkronen und Käppchen mit einem Kostenvorteil von Faktor zwei im Vergleich zur Zerspanung produziert. Zusätzliche Anwendungsfelder sind in der Orthopädie beispielsweise für die Herstellung von Schienen und Orthesen, der Hüftimplantologie und in der Fertigung individueller Operationsinstrumente zu finden. Die Fertigung von Bohrschablonen, so genannter Drillguides aus Kunststoffmaterialien, mit Hilfe der additiven Fertigung ermöglicht eine Erleichterung der operativen Behandlung und dient der präziseren Operationsführung des Chirurgen.
Hauptbarrieren für eine höhere Verbreitung der additiven Fertigungstechnologien stellen das mangelnde Vertrauen in die Materialeigenschaften, die aufwendige Zertifizierung in Abhängigkeit des Medizinproduktegesetzes sowie Unkenntnis der Gestaltungsfreiheit beziehungsweise der geometrischen Realisierungsmöglichkeiten dar. Für einen erfolgreichen Technologieeinsatz ist zudem zwingend eine Anpassung der Prozesskette in nahezu allen Prozessschritten der Produktentstehung erforderlich, um Potenziale effizient zu nutzen.
Die Anstrengungen in Forschung und Entwicklung richten sich auf eine Steigerung der Oberflächenqualität, der Aufbaurate, des Auflösungsvermögens, der verfügbaren und qualifizierten Werkstoffpalette sowie der realisierbaren Werkstückgröße. Insbesondere im Bereich der Medizintechnik spielen auch die Abmessungen der Produktionsanlagen eine besondere Rolle. So ist in der Dentaltechnologie der Trend zu kleinen Maschinen, so genannten Desktopmaschinen, erkennbar. Solche Systeme sprechen insbesondere kleinere Dentallabore oder Zahnärzte direkt an und ermöglichen eine individuellere und wirtschaftliche Patientenversorgung.
Kontakt
Jakob Fischer
Wissenschaftlicher Mitarbeiter
Institut für Produktionsmanagement, Technologie und Werkzeugmaschinen (PTW)
Technische Universität Darmstadt
Tel. +49 6151 16-6616
E-Mail senden
Prof. Dr.-Ing. Eberhard Abele
Institutsleiter
Institut für Produktionsmanagement, Technologie und Werkzeugmaschinen (PTW)
Technische Universität Darmstadt