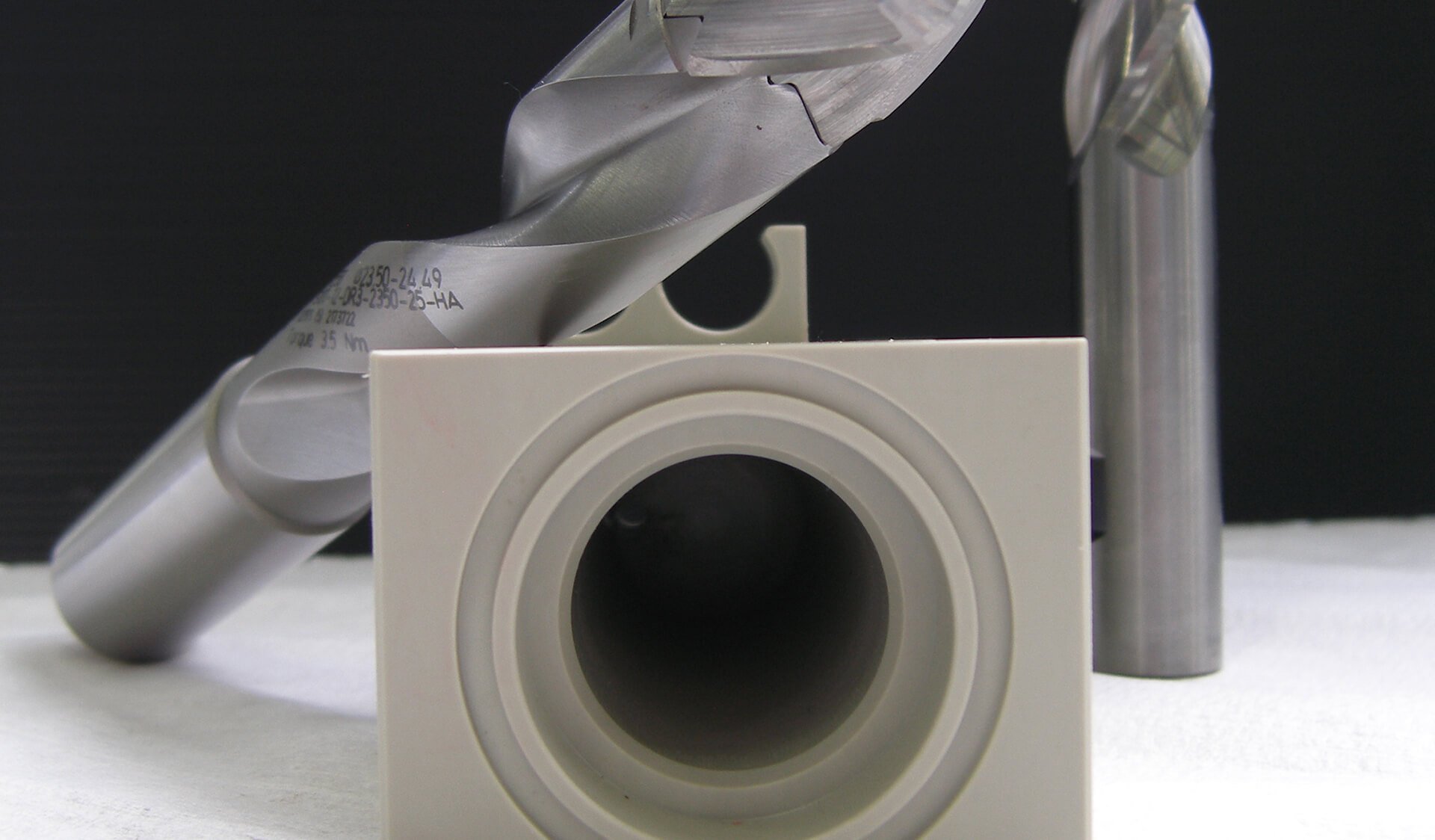
CNC Arena
Bearbeitung von Dialysegeräten
signifikant optimiert
Optimierungspotenziale in der spanenden Fertigung erkennen und nutzen, heißt die Devise. Eine Produktivitätssteigerung ist durch maßgeschneiderte Werkzeuglösungen möglich. Den mannlosen Werkzeugmaschinenbetrieb gesichert, die Bearbeitungszeit halbiert, die Werkzeugstandzeit um das 20-fache gesteigert und die Oberflächenqualität sichtbar verbessert – das sind beeindruckende Ergebnisse der jüngsten Prozessoptimierungen in der spanenden Fertigung von Fresenius Medical Care am Standort Schweinfurt.
Seit 1979 entwickelt und fertigt Fresenius Medical Care in der unterfränkischen Industriestadt mit Erfolg Dialysemaschinen für den internationalen Markt. Mehr als 40.000 Systeme verlassen jährlich das Werk, das sich im internationalen Wettbewerb durch effektives Arbeiten und klare Arbeitsabläufe behauptet. Strategie von Fresenius Medical Care ist es, sich hinsichtlich der Qualität der Dialyseprodukte und den Fertigungskosten von den Mitbewerbern abzuheben.
Für die Umsetzung dieser Ziele setzt der Hersteller von Dialysegeräten in der spanenden Fertigung seit dem Jahr 2000 auf das Know-how und die Werkzeuge von Mapal. „In enger Zusammenarbeit ist es uns wiederholt gelungen, Produktionsabläufe weiter zu straffen, Werkzeugkosten zu senken und Qualitätsverbesserungen zu erreichen“, berichtet Ludwig Schmittlein, der bei der Fresenius Medical Care Deutschland GmbH für den technischen Support Fräsen in der spanenden Fertigung verantwortlich ist.
Mannlose Fertigung
So kann ein aus Polypropylen bestehender „Multiblock“ nach einer Werkzeugumstellung nun auch mannlos und damit rund um die Uhr gefertigt werden. Vor der Umstellung wurden die notwendigen Sacklöcher für diese Baugruppe in drei Schritten realisiert: Wegen des großen Durchmessers von 42 Millimetern wurde erst mit einem Standardbohrer vorgebohrt, die Bohrung dann aufgebohrt und anschließend mit einem Fräser auf das Maß bearbeitet. „Dieses Vorgehen hatte den Nachteil, dass beim Aufbohren lange Bohrspäne anfielen, die zum einen die Werkzeugmaschine verdreckten und zum anderen sehr viel Platz im Spanauffangbehälter in Anspruch nahmen. Beides zusammen verhinderte einen mannlosen Betrieb über Nacht“, beschreibt Benedikt Hetterich, Leiter des Bereichs Fräsen und der Qualitätssicherung in der spanenden Fertigung von Fresenius, die Ausgangssituation.
Da der Maschinenaufbau ein Fräsen aus dem Vollen mechanisch nicht zuließ, schlugen die Mapal-Ingenieure mit Blick auf die Erfahrungen bei anderen Anwendern als Lösung einen Hartmetall-Wechselkopf-Bohrer TTD mit 180-Grad-Geometrie und einen PKD-bestückten Fräser vor, mit dem das Sackloch nach dem Bohren in einer Helix auszirkuliert wird. „Wir arbeiten damit seit einem Jahr sehr erfolgreich“, freut sich Ludwig Schmittlein. „Die Späne sind platzsparend klein, das Aufbohren entfällt komplett und der Fräser kann mit einem viel höheren Vorschub arbeiten, so dass wir mannlos und zudem schneller arbeiten können als vorher.“
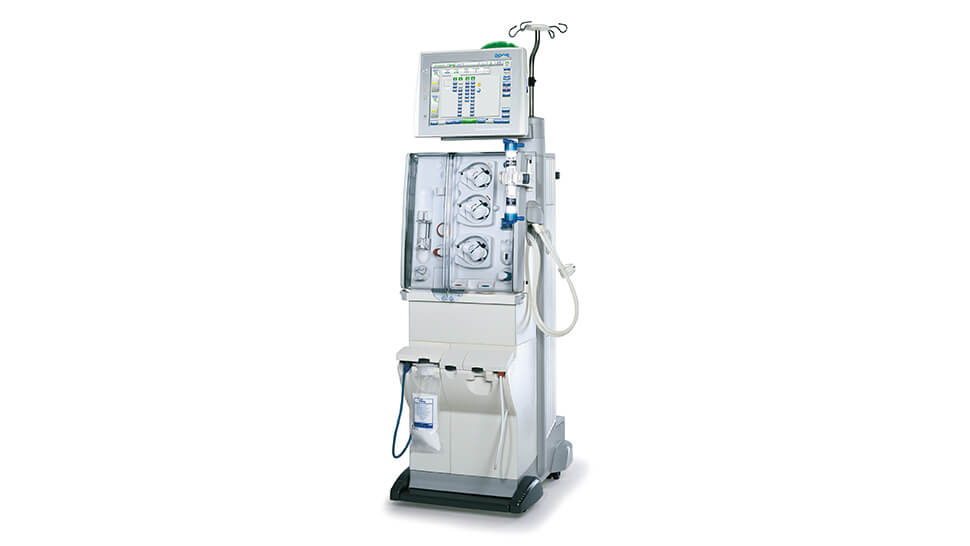
Dialysegerät von Fresenius Medical Care. Fotos: Mapal
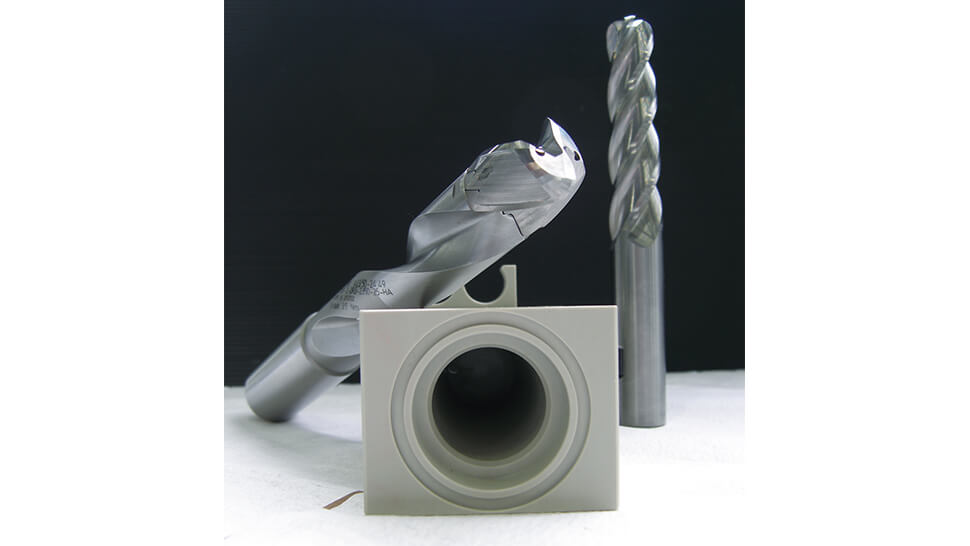
Vollbohren und Auszirkulieren mit optimiertem Spanbruch ermöglicht mannlose Fertigung.
Bearbeitungszeit halbiert
Ein weiteres Optimierungsprojekt stand bei Fresenius ganz im Zeichen der Durchsatzsteigerung: Der ebenfalls aus einem Polypropylenblock hergestellte „Filterblock“ für das Therapie-System 4008 von Fresenius muss mit einem 91 Millimeter tiefen Sackloch versehen werden. Allerdings ist dieses nicht geradwandig, sondern verjüngt sich mit einem Grad nach unten, weist am Übergang vom geraden Lochboden zur Seitenwand einen Radius auf und besitzt zur Öffnung hin einen geraden Teil. Wie beim Multifunktionsblock kamen hier zum Vor- und Aufbohren bis vor kurzem Standardbohrer zum Einsatz. Von einem CAD-Programm gesteuert, wurde dann die Schräge mit 0,2 Millimetern Schnitttiefe mit einem Radienfräser abgezeilt. Alleine dieser Vorgang dauerte 30 Minuten und es konnte zu Übergangsmarkierungen und Rillen in der Oberfläche kommen. „Mit der in enger Abstimmung mit uns durch die Mapal-Fachleute entwickelten Alternative benötigen wir dafür inzwischen nur noch 16 Minuten für die komplette Bearbeitung des Bauteils“, berichtet Schmittlein stolz.
Die Kammeröffnung des Filterblocks wird nunmehr mit einem Wechselkopfbohrer TTD in Sonderausführung in einem Schritt gebohrt. Der Bohrer ist in der MEGA-180-Grad-Geometrie ausgeführt, die die Bearbeitung eines ebenen Bohrungsgrundes von Bohrungen in einem Arbeitsgang ermöglicht. Die Kontur wird dann mit einem kundenspezifischen Hartmetall-Formfräser mit einer Zustellung gefräst. „Damit haben wir auch in diesem Anwendungsfall mit den neuen Werkzeugen kurze Späne, eine hohe Oberflächengüte und fließende Übergänge erzielt“, fügt Hetterich ergänzend an. Darüber hinaus profitiert Fresenius von längeren Werkzeugstandzeiten, wie sein Kollege betont: „Während wir mit einem Eckenradiusfräser etwa 600 Teile produzieren konnten, haben wir jetzt bereits die Marke von 1500 überschritten und müssen den Wechselkopf trotzdem noch nicht tauschen.“
Signifikante Einsparungen
Eine noch deutlichere Steigerung der Standzeiten hat Fresenius durch die Werkzeugoptimierung im Fall eines Bauteils aus Polypropylen mit 30 Prozent Glasfaseranteil erreicht: Vor dem Wechsel wurde ein Einstich mit Hilfe eines konventionellen VHM-Zirkularfräsers erzeugt. „Das Werkzeug ist zwar günstig in der Anschaffung, musste jedoch bereits nach 600 Teilen wegen Verschleißes ausgetauscht werden“, blickt Hetterich zurück. „Jetzt verwenden wir stattdessen einen Zirkularfräser mit PKD-Schneidstoff, der knapp das Dreifache kostet, dafür aber mindestens 16 000 Teile übersteht!“ Bei einer jährlichen Ausstoßmenge von 36 000 Stück bedeutet das alleine bei den Werkzeugkosten jedes Jahr Einsparungen von knapp 6000 Euro.
In partnerschaftlicher Kooperation mit den Werkzeugspezialisten von Mapal konnten die verantwortlichen Fresenius-Mitarbeiter in den vergangenen Jahren an vielen Stellen weitere ähnliche Verbesserungen erreichen. „Wir sind mit der Betreuung und der Qualität der Werkzeuge daher einfach rundum glücklich“, sind sich Hetterich und Schmittlein denn auch einig.
Kontakt
Andreas Enzenbach
Leitung Marketing & Corporate Communications
MAPAL Dr. Kress KG
Aalen
Tel. +49 7361 585 3683
E-Mail senden
Anzeige
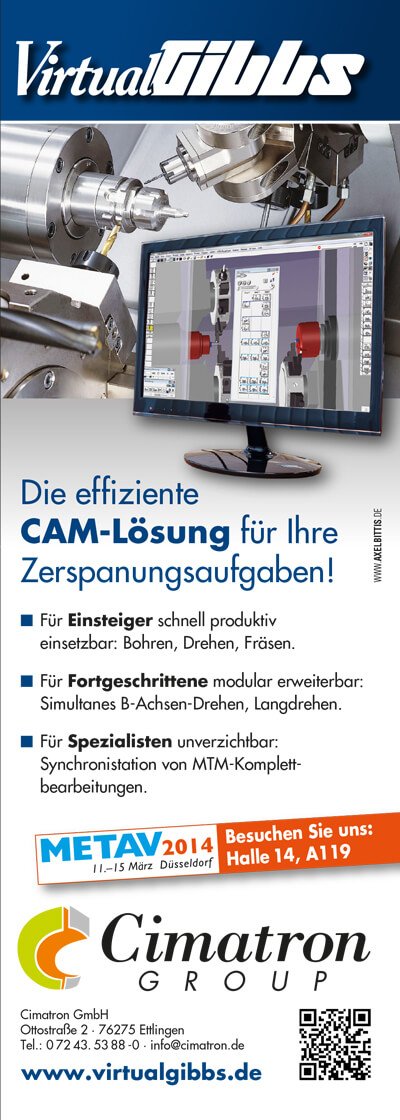