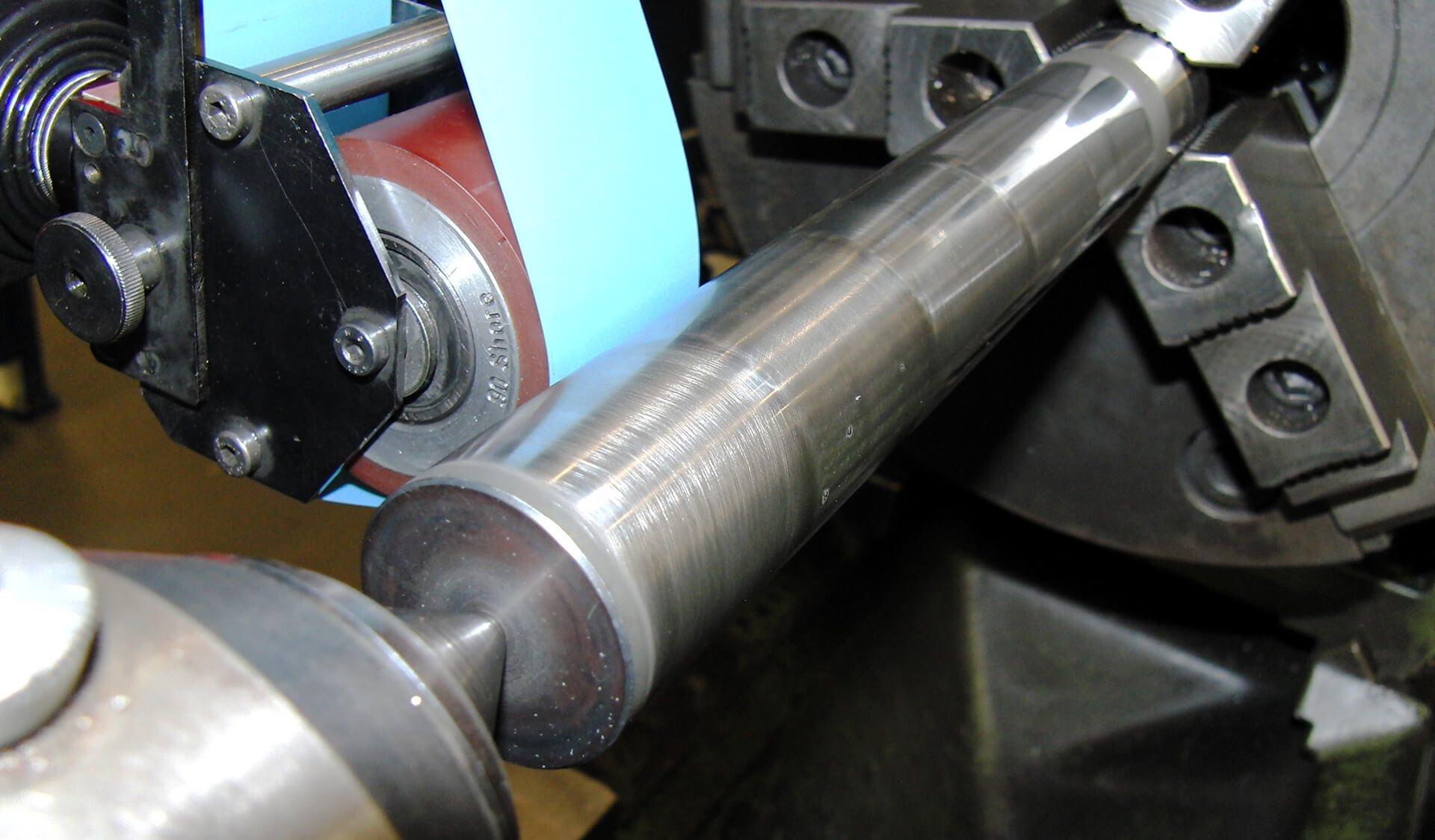
CNC Arena
Microfinishen: Strukturierung
funktionaler Oberflächen
Steigende Anforderungen an das Funktionsverhalten von Oberflächen erfordern spezielle Verfahren. Das Kurzhubhonen, auch Mikrofinishen, Superfinishen oder einfach Finishen genannt, ist ein Endbearbeitungsverfahren, durch das höchste Oberflächengüten und definierte Oberflächentopographien bei reduzierten Formabweichungen erzeugt werden.
Konventionell wird das Mikrofinishen bei der Endbearbeitung zylindrischer Bauteile angewendet. Anwendungsbeispiele finden sich in Industriebereichen wie der Automomobil-, Wälzlagerindustrie und Papierindustrie sowie dem allgemeinen Maschinenbau.
Hochbelastete Bauteile wie die Funktionsflächen einer Nocken-, Kurbel- oder Getriebewelle lassen sich durch Mikrofinishen erheblich in ihrer Funktionalität verbessern. Die bearbeiteten Flächen weisen sowohl verbesserte Verschleiß-, Reibungs- als auch Gleiteigenschaften auf.
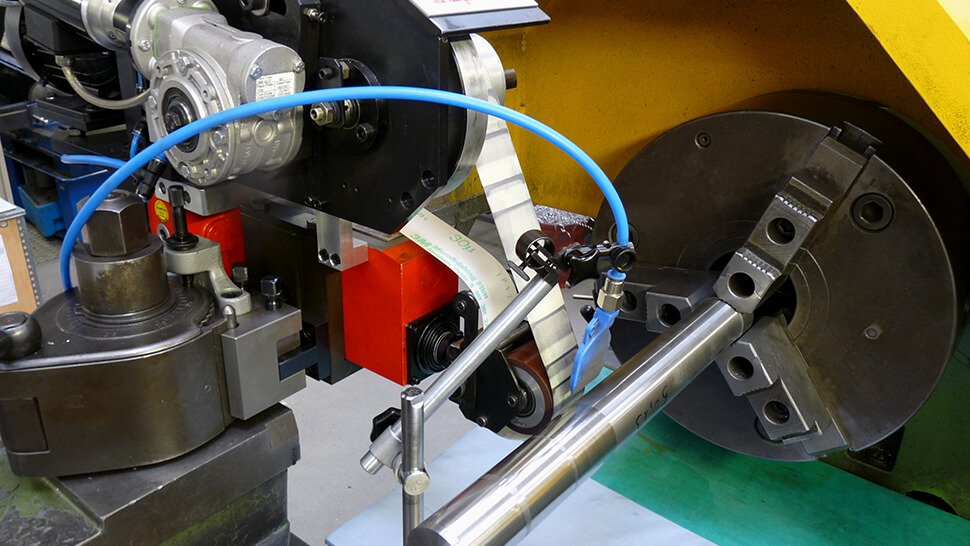
Foto: TU Dortmund
Bearbeitungsprinzip und Verfahrensvarianten
Beim Mikrofinishen wird ein Schleifkörper oder ein Schleifmittel auf einer Unterlage gegen ein meist rotierendes Werkstück kraftgesteuert zugestellt. Gleichzeitig oszilliert das Finishwerkzeug, wodurch sich kreuzende Oberflächenriefen erzeugt werden.
Durch die überlagerte Schnittbewegung aus rotierendem Werkstück und oszillierendem Werkzeug ergibt sich der für das Verfahren und das Honen typische Kreuzschliff. Durch die reversierende Axialbewegung des Werkzeugs werden insbesondere die Profilspitzen der Oberfläche abgetragen. Die Oberflächenstruktur zeichnet sich nach der Finishbearbeitung durch einen hohen Materialtraganteil in geringen Profiltiefen aus.
Aus der ursprünglichen Anwendung für rotationssymmetrische Bauteile haben sich Verfahrensvarianten entwickelt. Durch eine Anpassung des Werkzeugs und der Prozessführung lassen sich auch plane, konkav oder konvex geformte sowie sphärische Bauteile bearbeiten.
Werkzeuge und Werkzeugmaschinen
Je nach Stückzahl und Geometrie der Bauteile eignen sich komplette Finishanlagen oder CNC-Werkzeugmaschinen und konventionelle Drehmaschinen mit adaptiertem Aufsatzgerät für die Bearbeitung. Honsteine oder Finishbänder kommen zum Einsatz. Die Finishbänder lassen sich mit Hilfe von Schalenwerkzeugen oder Andrückrollen mit dem Werkstück in Kontakt bringen.
Bei der Bearbeitung von Lagerstellen an einer Welle bietet sich beispielsweise die Fertigung mit Schalenwerkzeugen an, da auf diese Weise alle Lagerstellen parallel bearbeitet werden können und ein hoher Umschlingungswinkel garantiert wird. Durch die größere Kontaktfläche lässt sich ein erhöhtes Zeitspanvolumen realisieren.
Walzen, die oft sehr lang sind, werden oft mit Hilfe von Andrückrollen oder Honsteinen bearbeitet, wobei das Finishaufsatzgerät einen axialen Vorschub erfährt, um die gesamte Länge der Walze bearbeiten zu können. Eine Durchlaufbearbeitung ohne Aufspannung des Werkstücks ist ebenfalls möglich und wird beispielsweise bei Wälzkörpern durchgeführt.
Eine mehrstufige Bearbeitung mit unterschiedlichen Korngrößen ermöglicht ein großes Zeitspanvolumen und hohe Oberflächenqualität. Durch die simultane Bearbeitung mit unterschiedlichen Korngrößen kann die Vor- und Nachbearbeitung in einer Prozessstufe kombiniert werden.
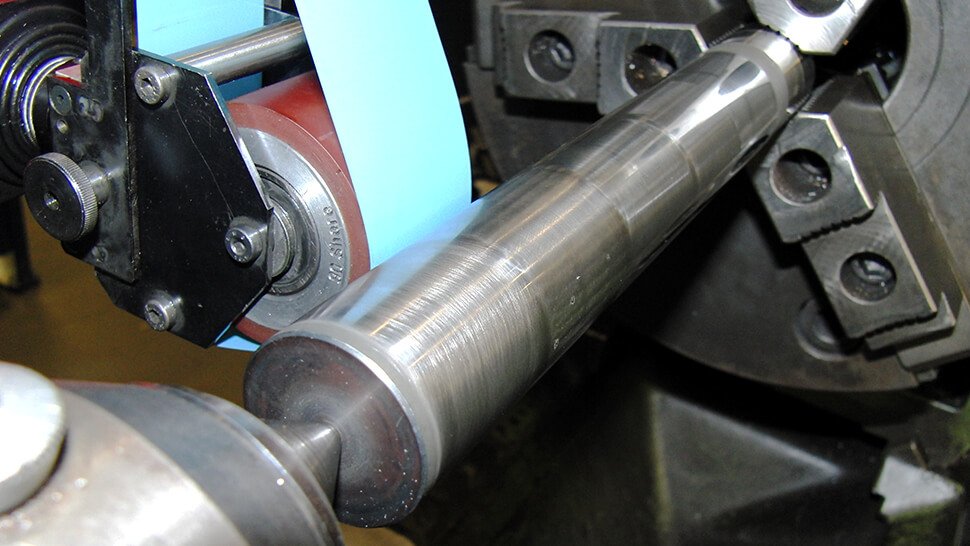
Foto: TU Dortmund
Erzielbare Oberflächenqualitäten
In Abhängigkeit der verwendeten Korngröße und der Bindung des Honsteins beziehungsweise des Finishbands lassen sich Oberflächenqualitäten mit einer gemittelten Rautiefe kleiner als Rz = 0,1 Mikrometer generieren. Die Höhe der Profilspitzen liegt bei wenigen Nanometern, so dass bereits in geringen Profiltiefen ein hoher Materialanteil vorliegt.
Durch eine mehrstufige Bearbeitung mit abnehmender Korngröße lassen sich sowohl sehr glatte Oberflächen als auch ausgeprägte Plateaustrukturen generieren. Die Anpassung der Prozessstufen hinsichtlich der jeweils verwendeten Korngröße und Bearbeitungszeit ermöglicht eine nahezu frei skalierbare Tiefe der Profilriefen.
Stand der Forschung
Neben den erzielbaren Oberflächenqualitäten ist die Prozesseffizienz, insbesondere in der industriellen Fertigung, von entscheidender Bedeutung. Durch eine hochfrequente Anregung des Werkzeugs ergibt sich ein unterbrochener Schnitt, der wiederum zu einer Erhöhung der Zerspanleistung führt. Zusätzlich ist durch die Auslegung der Anregung eine weitere Stellgröße für die gezielte Oberflächenstrukturierung gegeben.
Steigende Anforderungen an die Funktionsflächen erfordern zusätzlich die Entwicklung neuer Werkstoffe und im Speziellen die Aufbringung von Beschichtungen. Diese zur Erhöhung der Verschleißbeständigkeit aufgebrachten Schichten stellen, insbesondere auf komplexen Bauteilgeometrien wie dem Gelenkkopf eines Knie-Implantats erhöhte Anforderungen an den Fertigungsprozess.
Kontakt
Sebastian Goeke
Wissenschaftlicher Mitarbeiter
Abteilung Schleiftechnologie
Institut für Spanende Fertigung
Technische Universität Dortmund
Tel. +49 231 755-2784
E-Mail senden
Prof. Dr.-Ing. Dirk Biermann
Institutsleitung
Kontakt zum Schleifseminar:
E-Mail senden
www.isf.de/schleifseminar2014