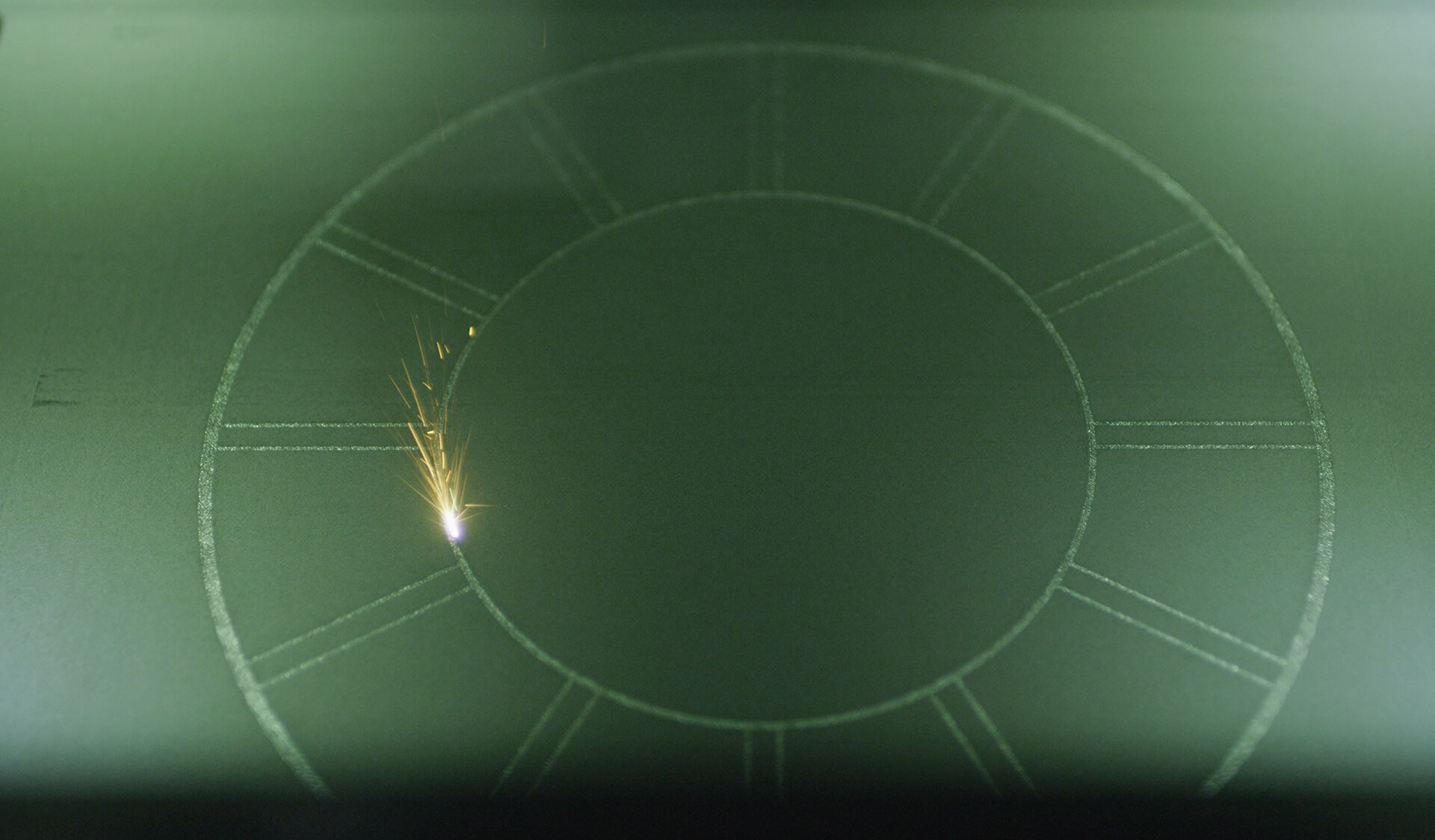
Titelinterview
Von der CAD-Konstruktion
direkt ins Pulver
Laserschmelzen von Metallen findet verstärkten Einsatz – aufmerksam schaut die Zerspanungsbranche auf die additive Fertigung. Welche Konsequenzen hat die neue Art der Metallbearbeitung, fragt man sich. Luftfahrt, Medizintechnik oder Formenbau haben sich damit schon stark angefreundet. Mit Frank Herzog, dem geschäftsführenden Gesellschafter der Concept Laser GmbH, sprachen wir über Vorteile und Fortschritte des 3D-Metal-Printing, der Schwestertechnologie für das Zerspanen. Das Interview führte Georg Dlugosch, Chefredakteur des CNC-Arena eMagazines.
Beginnt eine neue Ära der Metallbearbeitung?
Herzog: In fränkischer Bescheidenheit – ja, absolut! Es ist eine durchgehend neue Technologie. Ich würde auch den Begriff „revolutionär“ benutzen. Die digitale Prozesskette ist als Fertigungsstrategie zu sehen. Sie tritt zunächst als Ergänzung zur klassischen Metallbearbeitung in Erscheinung, aber in einigen Bereichen wie Gießen kommt es sogar zur Substitution anderer Verfahren. Beim Übergang von generativen Fertigungsstrategien gibt es zum Beispiel keine Kosten für Formen und Werkzeuge. Die Entwicklung wird schneller durchgezogen durch das formlose Fertigen. Bauteile werden funktional besser und günstiger. Hinzu kommt die Topologieoptimierung, in die bionische Verfahren einfließen. Das sind Argumente, denen man sich nur schwer entziehen kann.
Oft ist von Einschränkungen die Rede. Gilt das für alle Bauteile?
Herzog: Viele Firmen sind nicht auf dem neuesten Stand der Dinge, jedoch nicht, weil sie sich nicht dafür interessieren, sondern eher, weil die Entwicklung so rasant voranschreitet. Concept Laser ist seit 15 Jahren am Markt. Damals waren wir die ersten, die die Technologie in Form von Maschinen auf dem Markt präsentiert haben. Wir sind richtige Pioniere. Damals haben wir einen Festkörperlaser mit 100 Watt und einer Aufbaurate von einem Kubikzentimeter pro Stunde gehabt. Heutzutage sprechen wir über Multisysteme, das sind Maschinen, die zwei Laser in Kilowattstärke an Bord haben. Als weltweit erste Firma haben wir 2012 mit der X line 1000R das 1-Kilowatt-System vorgestellt. Nach zwei Jahren Beta Phase schließt sich jetzt die Serienproduktion an. Seit Ende 2014, also kaum zwei Jahre später, ist schon die X line 2000R angekündigt, die den Bauraum auf 800 Millimeter vergrößert und ein Doppel-Lasersystem bietet. Innerhalb eines Jahres verdoppelt sich die Baurate. Das ist eine enorme Entwicklungsgeschwindigkeit, die die Technologie durchmacht. Wir landen mit der X line 1000R bei Aluminiumbearbeitung teilweise bei 80 bis 100 Kubikzentimetern pro Stunde Aufbaurate. Das sind Steigerungen um 600 bis 800 Prozent zur Ausgangssituation. Mit der X line 2000R wird sich die Steigerungsrate sogar noch deutlich erhöhen.
Welche Möglichkeiten bietet eine durchgängige digitale Prozesskette?
Herzog: Digitale Prozesskette bedeutet, dass man von der CAD-Konstruktion direkt in die Fertigung geht. Concept Laser ist eines von drei eigenständigen Unternehmen. In Lichtenfels gibt es auch die Werkzeugbau Siegfried Hofmann GmbH und die Robert Hofmann GmbH. Die Inhaber-Familien sind Herzog und Hofmann. Deshalb haben wir eine starke Verknüpfung zur Fertigungstechnologie über den Formenbau. Nehmen wir als Beispiel einen Formensatz. In der klassischen Fertigung muss man aus dem Lager einen Rohling herausholen, ablängen und bearbeiten. Bis das Bauteil auf die Fräsmaschine kommt, sind wir von der CAD aus schon weit in der Fertigung mit der Laserschmelzmaschine. Wir überspringen die ganzen Vorbereitungen und gehen von der CAD direkt ins Pulver und bauen ohne Umschweife das Bauteil auf. Damit können wir werkzeuglos formen, auch beim Stanzen oder Gießen. So zieht sich die digitale Prozesskette durch bis zur Dokumentation.
Wie ist das Kosten-Nutzen-Verhältnis im Vergleich zur Serienfertigung?
Herzog: Das additive Verfahren steht an der Schwelle zur Produktionslandschaft. Sicherlich werden keine Motorblöcke in Serie gefertigt oder Türmodule von Autos. Die neue Technologie entfaltet sich bei individueller Serienfertigung, Beispiel Zahnersatz, wo sich das Verfahren bereits etabliert hat. Bei Implantaten für Knie oder Hüfte ist die Technologie zur Produktion geeignet. Auch im Formenbau sprechen wir von Produktionstechnologien, wenn konturnah gekühlte Formeneinsätze in Serie verwendet werden. Wo es um große Stückzahlen geht, trennen sich die Wege. Einen Vorsprung hat die neue Technologie in der Vorentwicklung und Entwicklung bei Stückzahlen bis zu einigen 100. Das additive Verfahren entfaltet sich auch bei der Funktionsintegration. In der Raketentriebwerkstechnik werden beispielsweise Bauteile aus einem Stück gefertigt. In die Zündstufen wird der Treibstoff eingespritzt und gezündet. Diese Baugruppen müssen hoch präzise gefertigt und montiert sein. Das Laserschmelzverfahren muss schneller sein, teils bis zu 70 Prozent Kosten reduzieren und dann noch die Performance des Bauteils verbessern, indem es mehr Belastungen aushält. Die Herstellung aus einem Stück mit ideal geformten Zuführkanälen, um die Verbrennungseffektivität zu erhöhen, ist ein anderes Beispiel für den Vorteil.
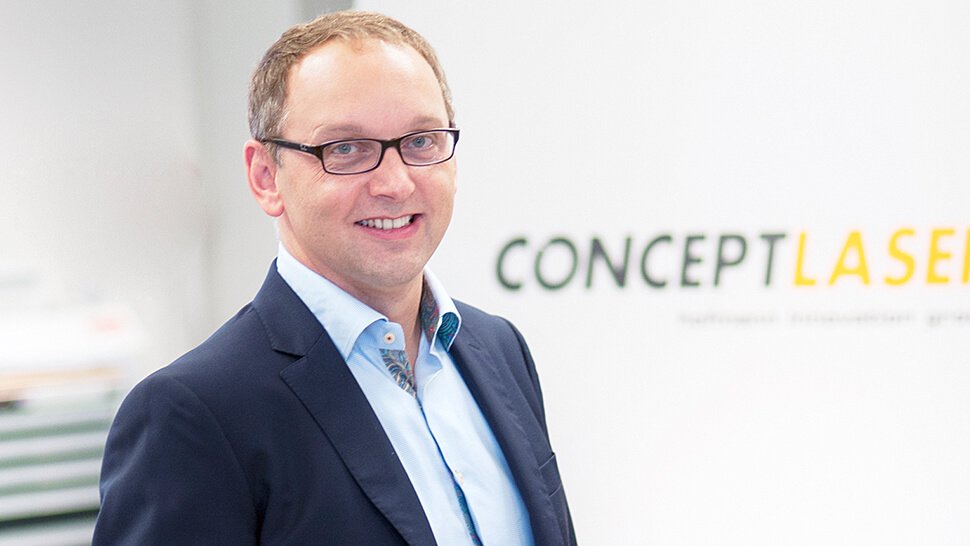
Frank Herzog, geschäftsführender Gesellschafter der Concept Laser GmbH. Fotos: Concept Laser
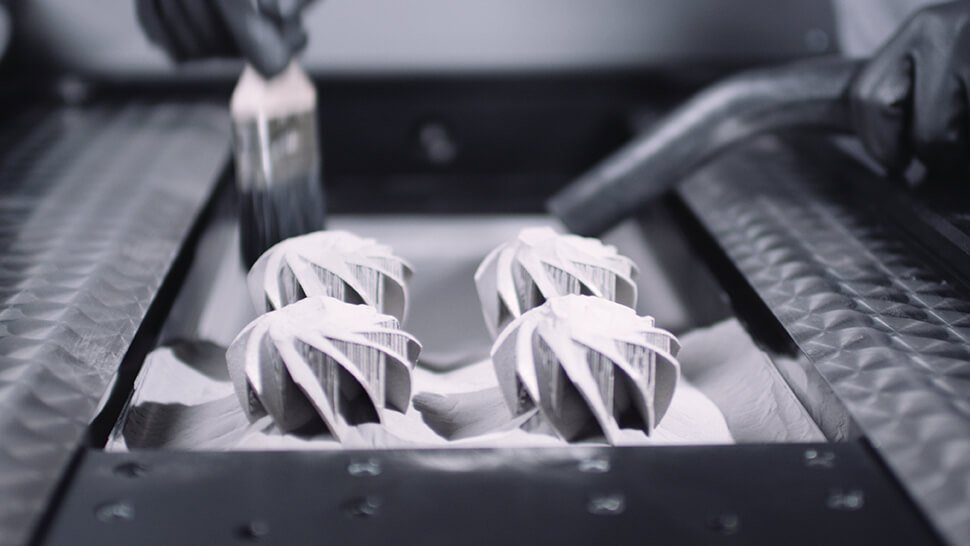
Im Pulverbett
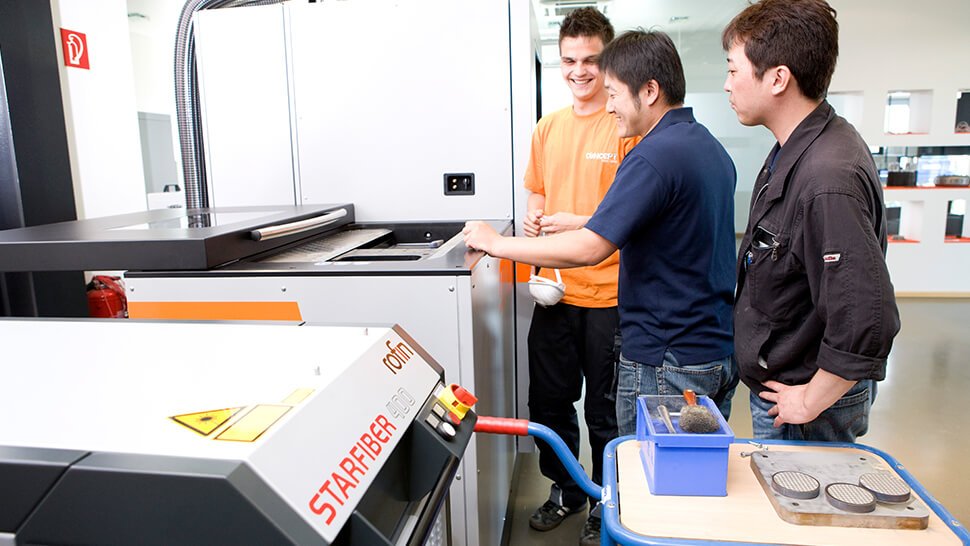
Arbeiten bei Concept Laser
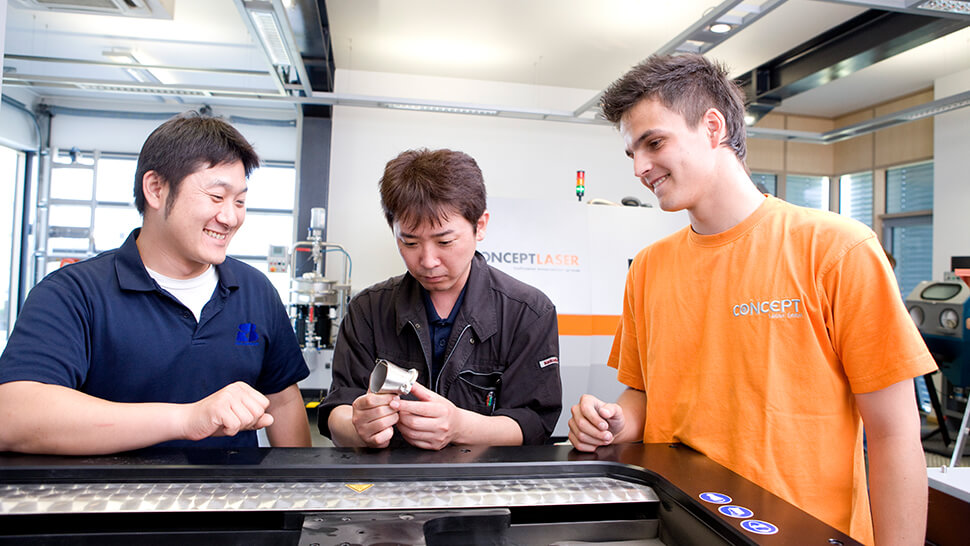
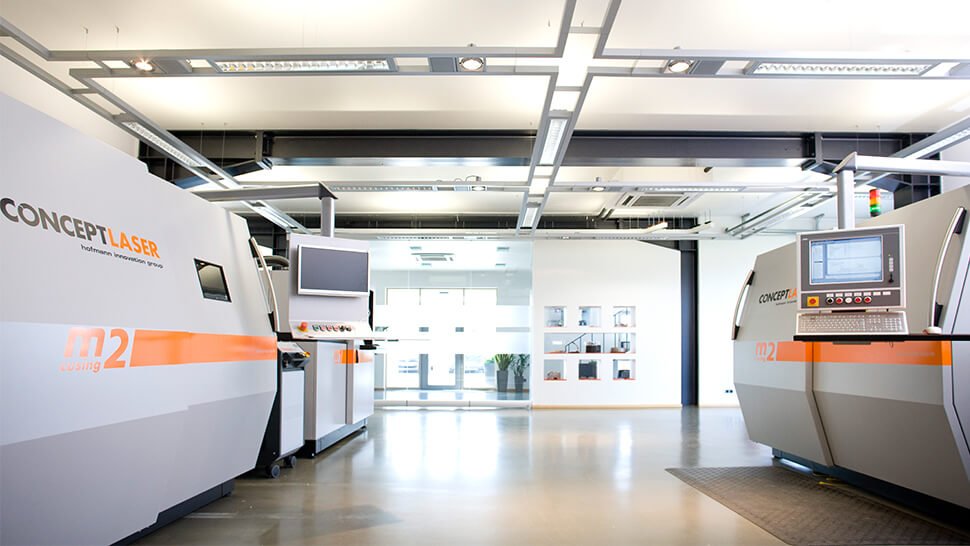
m2 Multilaser Cusing
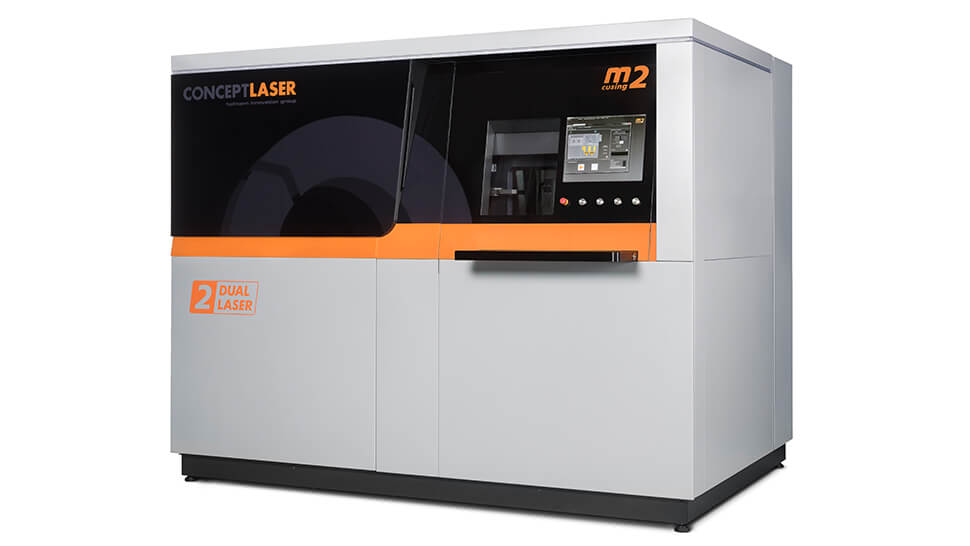
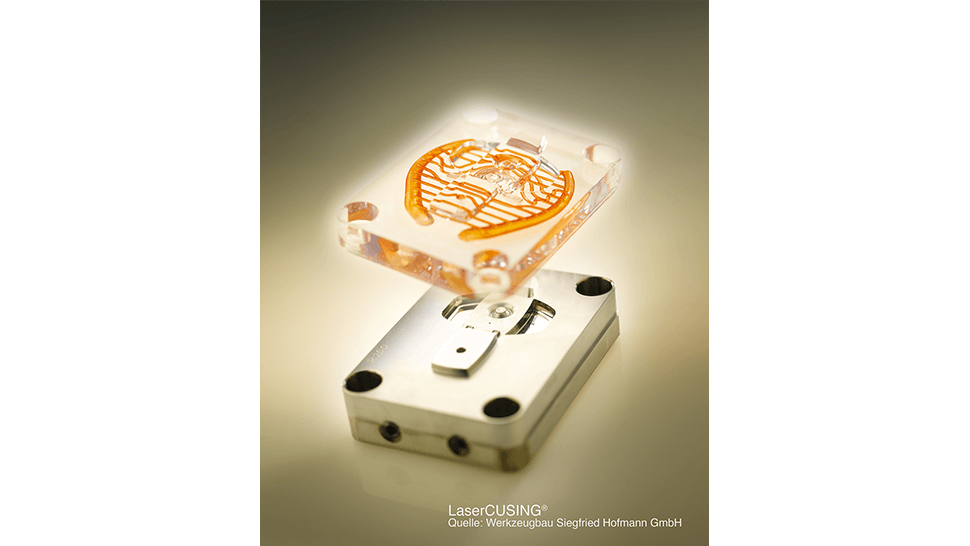
Werkzeugbau
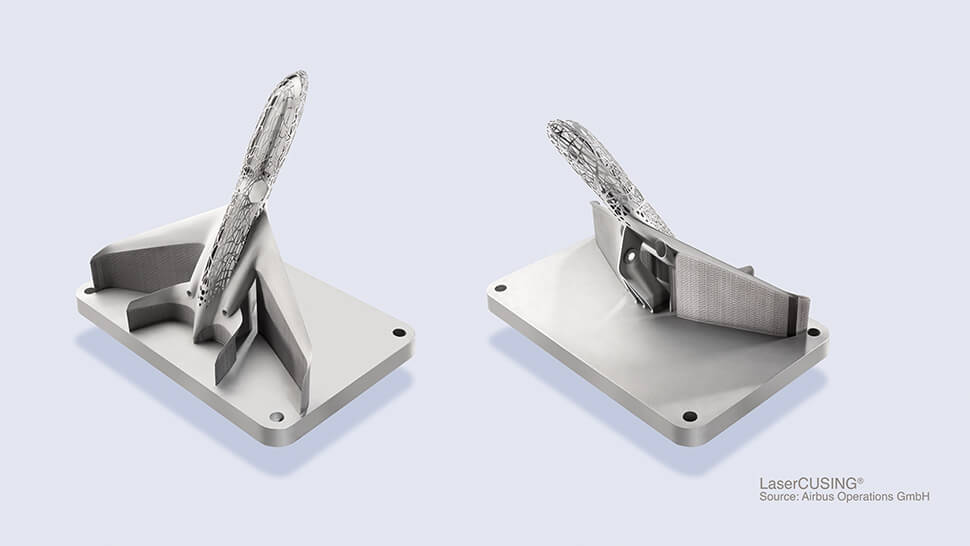
Flugzeugmodell
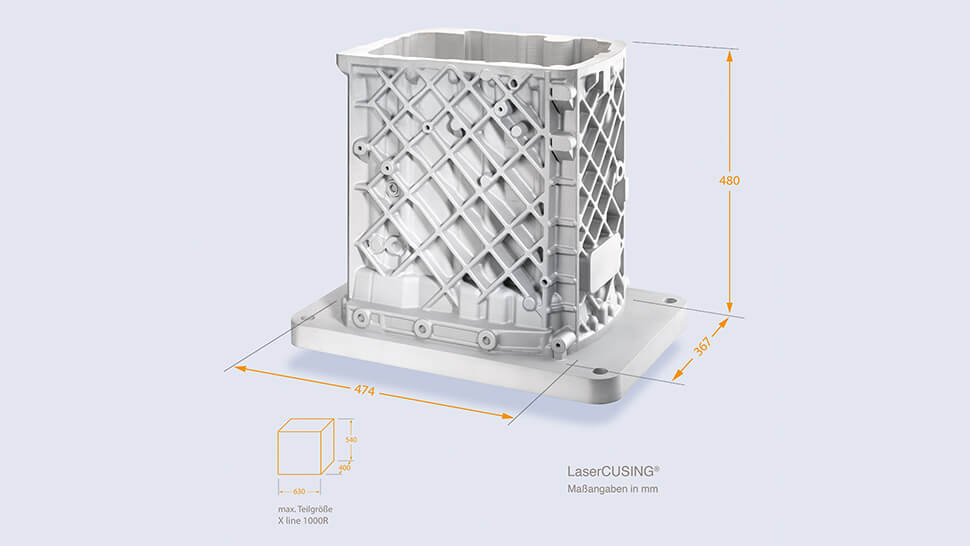
Getriebekasten
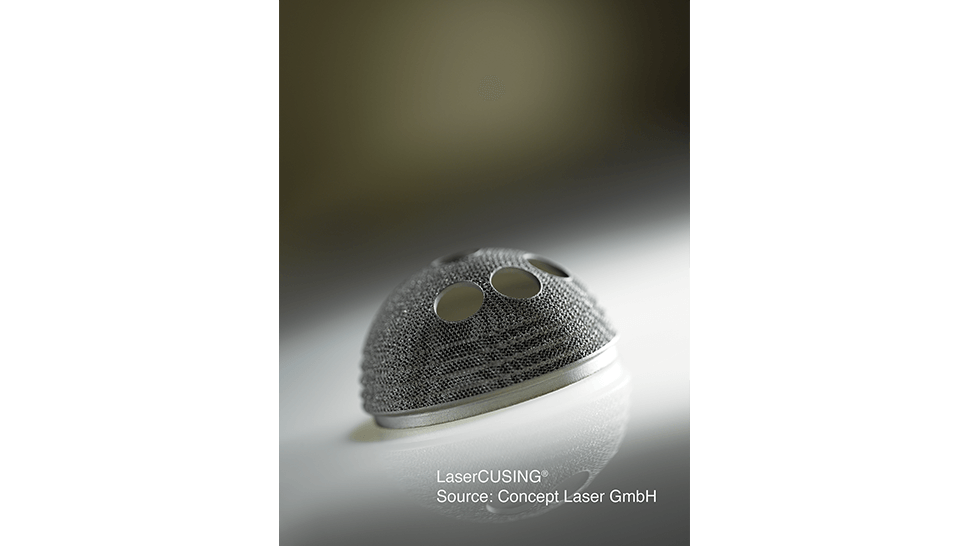
Kopf einer Hüftkugel
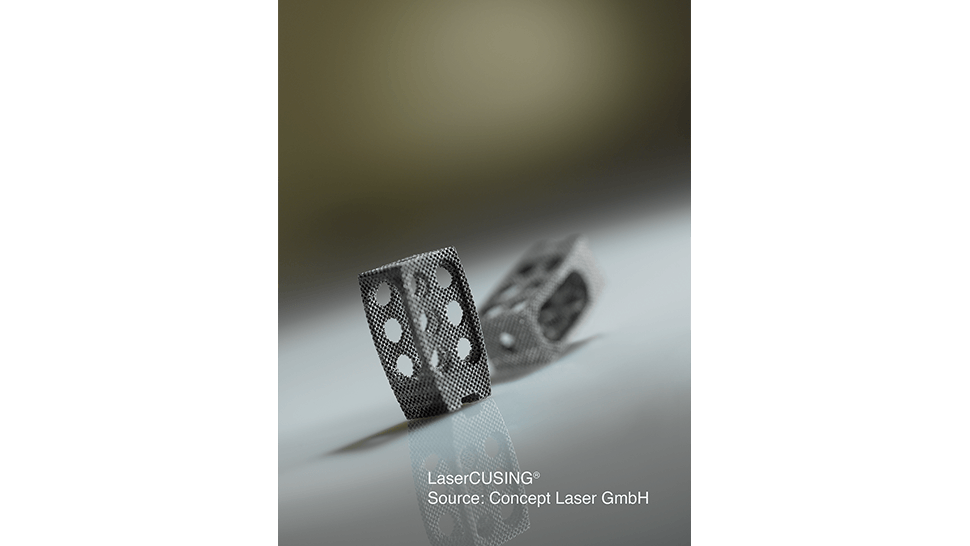
Wirbelimplantat
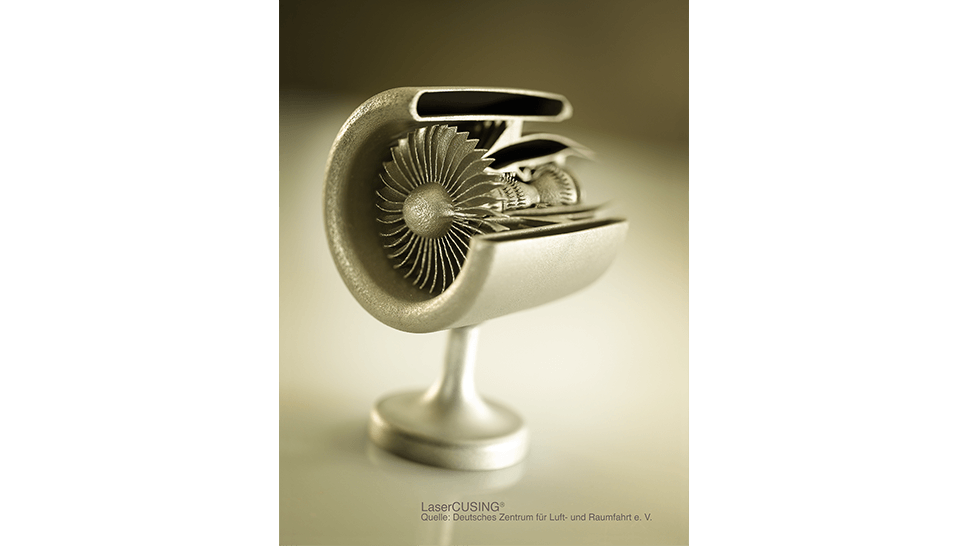
Turbine
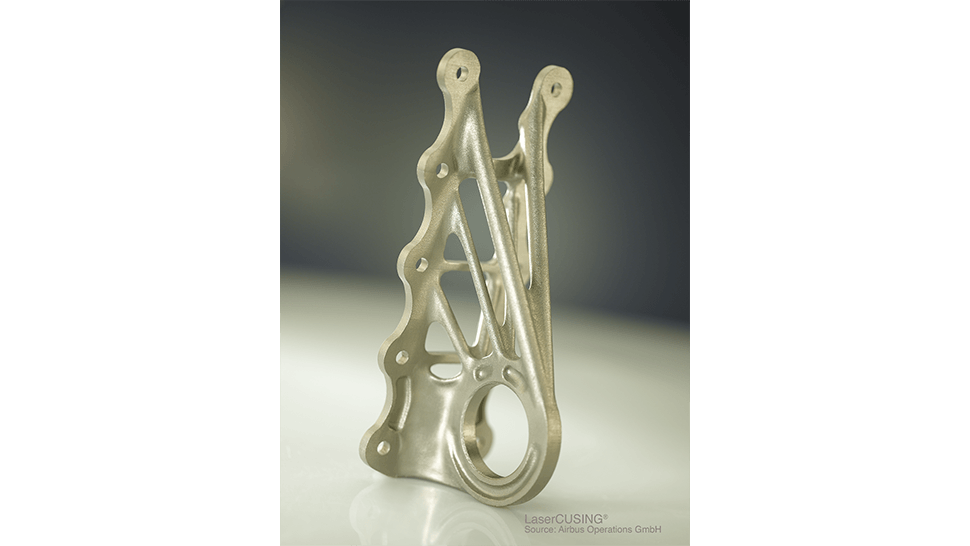
Bauteil
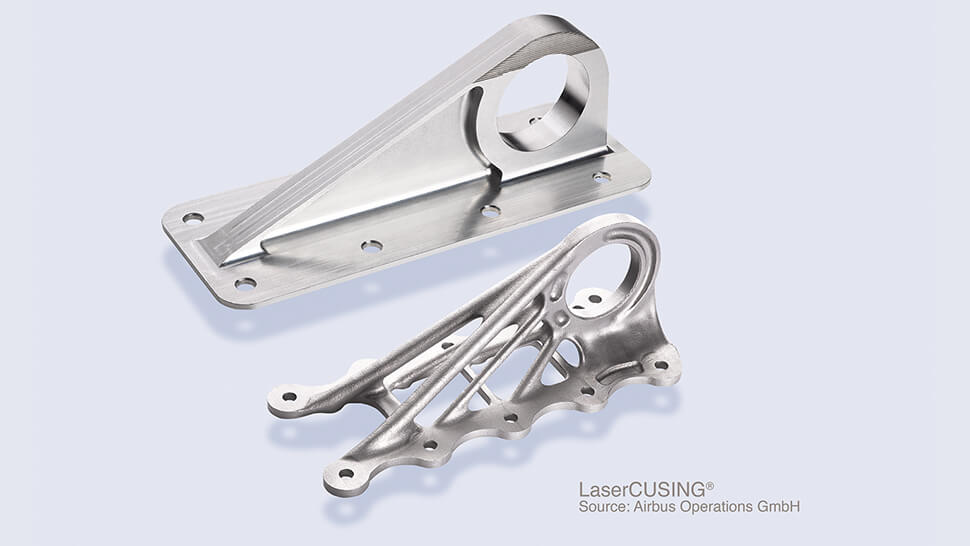
Vergleich der Bautelle: Konventionell gefertigt (oben) und mit Laser Cusing erstellt
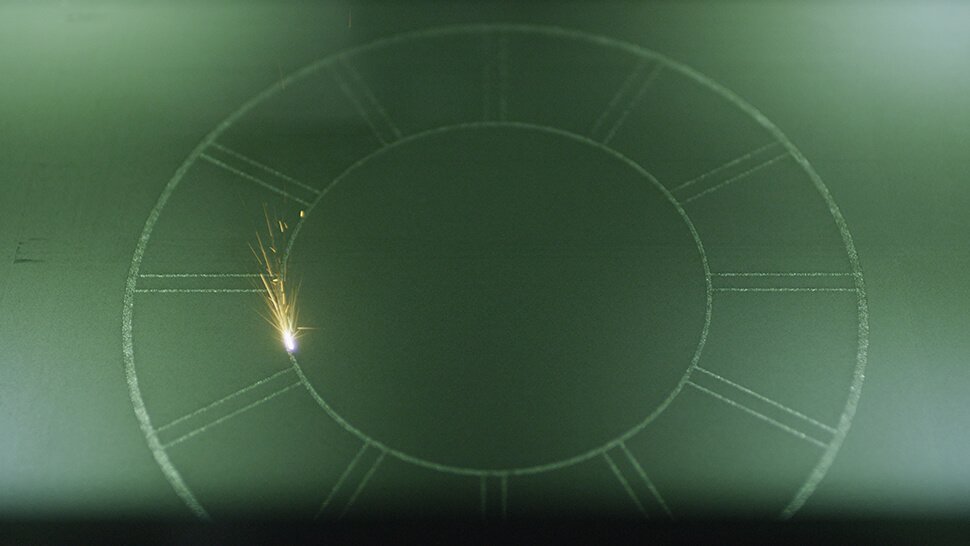
Wie stehen Sie zu dem Begriff „3-D-Druck“?
Herzog: Das Wort 3-D-Druck haben wir ursprünglich mit dem Hype um die Drucker verbunden, mit denen man sich selbst ausdrucken oder Spielzeugteile herstellen kann. Anfangs haben wir ein bisschen die Nase gerümpft, aber jetzt sind wir eigentlich froh über den 3-D-Druck oder 3D-Metal-Printing, weil man durch diesen Hype der vergangenen drei Jahre – der momentan nachlässt – auch in der Industrie bis in die Vorstandsetagen hinauf auf solche Verfahren aufmerksam geworden ist. Dadurch wurde die Produktionstechnologie des Laserschmelzens in deren Köpfe transportiert. Seit zwei bis drei Jahren wird von ihnen Druck ausgeübt, solche Technologien nicht nur zu betrachten, sondern Strategien zu entwickeln, um sie zu implementieren und die Vorteile für die Produktion der Zukunft zu nutzen. Den Begriff kapiert jeder, sogar die Oma im Lichtenfelser Kaffee, die behauptet, dass Concept Laser mit 3-D-Druck Raketen baut – was so nicht korrekt ist, aber man merkt, der Begriff ist für die breite Masse einfach geläufig, und man kann das Thema besser transportieren. Ursprünglich sagen wir zu unserer Technologie Laser-Cusing, aber 3-D-Metal-Printing passt auch. Als Ingenieur sehe ich additive Fertigung als richtigen Begriff an, um an den Einsatzzweck zu erinnern und in Abgrenzung zur abtragenden Technik.
Wie hängt der 3D-Druck mit Industrie 4.0 zusammen?
Herzog: : Additive Fertigung verändert die Konstruktion, den Prozess und seine Stufen bis hin zu den Geschäftsmodellen. Das ist im wesentlichen Industrie 4.0. Letztlich geht es auch um Fabrikautomation, um die Anlagen mit Intelligenz zur Selbstorganisation auszustatten. Die digitale Prozesskette verändert das Denken. Die Generierung von CAD-Daten mit Scannen, der Bauteilaufbau mit dem Laser – so können CAD-Daten überall verfügbar gemacht werden. Das sind Geschäftsmodelle, die neue unternehmerische Chancen bieten.
Ist eine Weiterentwicklung von additiver Fertigung schon erkennbar?
Herzog: Zumindest weiß ich derzeit noch nichts von neuen Fertigungstechnologien. Wir sind momentan in der Phase, wo die Bauräume größer werden. Da hat Concept Laser die weltweit größte Plattform, aber der Bedarf nach größerem Bauraum und mehr Produktivität ist vorhanden. Die Lasertechnik kann man multiplizieren auf vier oder acht Laserköpfe, aber das ist kein Ingenieursansatz mehr. Wir gehen davon aus, dass es irgendwann in der Zukunft noch einen Innovationssprung geben wird. Die Maschinen von heute werden in fünf Jahren sicher ganz anders aussehen. Dazu helfen auch die Innovationsaktivitäten der EU, die dem Laserschmelzen eine Schlüsselrolle in der Fertigung zuschreiben. Bei den Möglichkeiten dieser Technik stehen wir noch ganz am Anfang. Bei Gründung der Firma haben wir ja eigentlich Verrücktes gedacht. Keiner hat für möglich gehalten, was heute gemacht wird. Unser Bestreben ist es auch, immer weit über den Tellerrand hinaus zu gucken und als Technologietreiber zu wirken. Wir haben konkrete Vorstellungen, aber es ist noch zu früh, darüber zu sprechen. Ganz klar: Automation und Produktion und Baugröße sind als Thema gesetzt.
Der Markt für grüne Technologien wächst. Gehört additive Fertigung auch dazu?
Herzog: Der Umweltgedanke ist ein wichtiger Aspekt. Energieaufwand und Ressourcenschonung sind gravierende Merkmale des Laserschmelzens. Deshalb behaupte ich, Laser-Cusing oder 3-D-Metalldruck ist definitiv eine grüne Technologie.
Wie sieht Ihre Marktanalyse aus?
Herzog: Eine Studie von Roland Berger erwartet innerhalb von zehn Jahren eine Marktausweitung um 400 Prozent. Concept Laser hat in den ersten Jahren hart kämpfen müssen, bis zur Wirtschaftskrise, die dann allerdings weniger gravierend ausfiel. Seit 2009 steigern wir unser Wachstum und unsere Mitarbeiteranzahl stetig. Das ergänzen die Zahlen des Wohlers-Reports beeindruckend. In 2013 ist der Umsatz des gesamten Marktes auf 3,07 Milliarden Dollar (plus 35 Prozent) geschätzt worden. Im Metallbereich der additiven Fertigungsbranche wurden 2013 über 345 Maschinen verkauft, was einem Wachstum von ca. 75 % gegenüber dem Vorjahr entspricht. Concept Laser selbst hat im vergangenen Jahr 45 Millionen Euro Umsatz erzielt, nach 23 (2013) und 16 (2012) Millionen Euro. Jetzt sind ungefähr 500 Anlagen weltweit installiert, davon wurden allein 105 im Jahr 2014 ausgeliefert. Aktuell haben wir 110 Mitarbeiter, deren Zahl bis Jahresende auf mindestens 130 wächst. Mit dem Thema 3-D-Metalldruck werden sich zum Jahresende am Standort Lichtenfels übergreifend etwa 200 Mitarbeiter beschäftigen.
Sie sind zusammen mit Ihrer Frau geschäftsführender Gesellschafter?
Herzog: Wir sind die Gründer. In den 1990er Jahren habe ich die ersten Patente entwickelt, meine damalige Freundin und jetzige Frau hat parallel im elterlichen Betrieb eine neue Technologie zum Abtragen im Formenbau eingeführt. Sie hatte einen vielversprechenden Laser, den wir benutzt haben, um gemeinsam Versuche weiterzuführen. Die Kombination beider Arbeiten hat zur Firmengründung geführt. Wir sind auch Hauptgesellschafter der Firma.
Wie steht Deutschland am Weltmarkt da?
Herzog: Das Laserschmelzen mit Metallen ist eine deutsche Technologie. Deutschland ist herausragend aufgestellt am Weltmarkt. Einer der wesentlichen Gründe ist die Kooperation von Hochschulen und Industrie. Damit sind wir in der Lage, Lösungen auf kurzen Wegen zu schaffen. Nur in einem Punkt wünsche ich mir mehr Dynamik: bei Nutzung und Anwendung der Technologie. In den USA gibt es eine positivere Herangehensweise, während man in Deutschland eher skeptisch ist. Aber ich sehe die riesige Dynamik, die man nutzen könnte.
Müssen wir Angst haben, dass uns amerikanische Unternehmen überholen?
Herzog: Man sollte nie Angst, aber immer Respekt vor Herausforderern haben, auch vor Unternehmen aus China oder Japan. Wir haben in Deutschland eine hervorragende Infrastruktur. Mit dem Tüftlertum in Kombination mit der Forschungslandschaft sind wir gut aufgestellt. Es gibt viele Unternehmen in Deutschland, die innovativ denken und vorpreschen in der Anwendung der Technologie, nur in der Breite wünsche ich mir mehr Schwung. Deutschland ist absolut der Spitzenreiter in additiver Fertigung.
Sie haben eine Initiative zur Ausbildung in 3-D Konstruktion gestartet?
Herzog: Entscheidend für die Technologie wird sein, was auch vor der Anwendung passiert, nämlich in der Konstruktion. Wir haben bewiesen, dass sich ein großer Erfolg einstellt, wenn wir in der richtigen Richtung denken. Die Technologie wird nur vorankommen, wenn im Vorfeld viel Know-how aufgebaut wird. Dann kann man schneller, günstiger, funktionsintegriert und mit wesentlichem Mehrwert Bauteile aufbauen. Dazu brauchen wir Initiativen, wie es sie bereits bei einigen Firmen gibt. Das Umdenken findet statt, steht aber noch am Anfang und ist eine der wichtigsten Bausteine, wenn wir additiv denken. Wir haben in Lichtenfels 2008 die Concept Laser Academy gegründet, weil ich aus eigener Erfahrung weiß, wie schwierig es in den 1990er Jahren war, an Praktikumsplätze heranzukommen. Deshalb wollte ich etwas verändern und jungen Ingenieuren die Möglichkeit zur Weiterbildung geben. Derzeit betreuen wir fast 20 junge Ingenieurinnen und Ingenieure bis hin zu Promotionsarbeiten und verbreiten damit auch das Gedankengut der additiven Fertigung.
Muss der Konstrukteur umdenken?
Herzog: Additive Fertigung schenkt dem Konstrukteur Freiheiten für seine Kreativität. Mit konventionellen Techniken sind solche Bauteile nicht produzierbar. Ich kann beispielsweise von einem Schilfrohr oder einem Ast einen bionischen Abdruck erstellen, weil die Struktur vorteilhaft bei Wechsel-Biege-Belastungen ist. Aus der Natur kopiert und konstruktiv in die Technik eingesetzt. Das kann keine andere Technologie. Wenn wir diese Idee in den Köpfen der Konstrukteure verankern, dann kommen wir mit der Technologie noch einen wesentlichen Schritt voran.
Kontakt
Frank Herzog
Geschäftsführender Gesellschaft
Concept Laser GmbH
Daniel Hund
Leiter Marketing
Concept Laser GmbH
Tel. +49 9571 1679-251
E-Mail senden