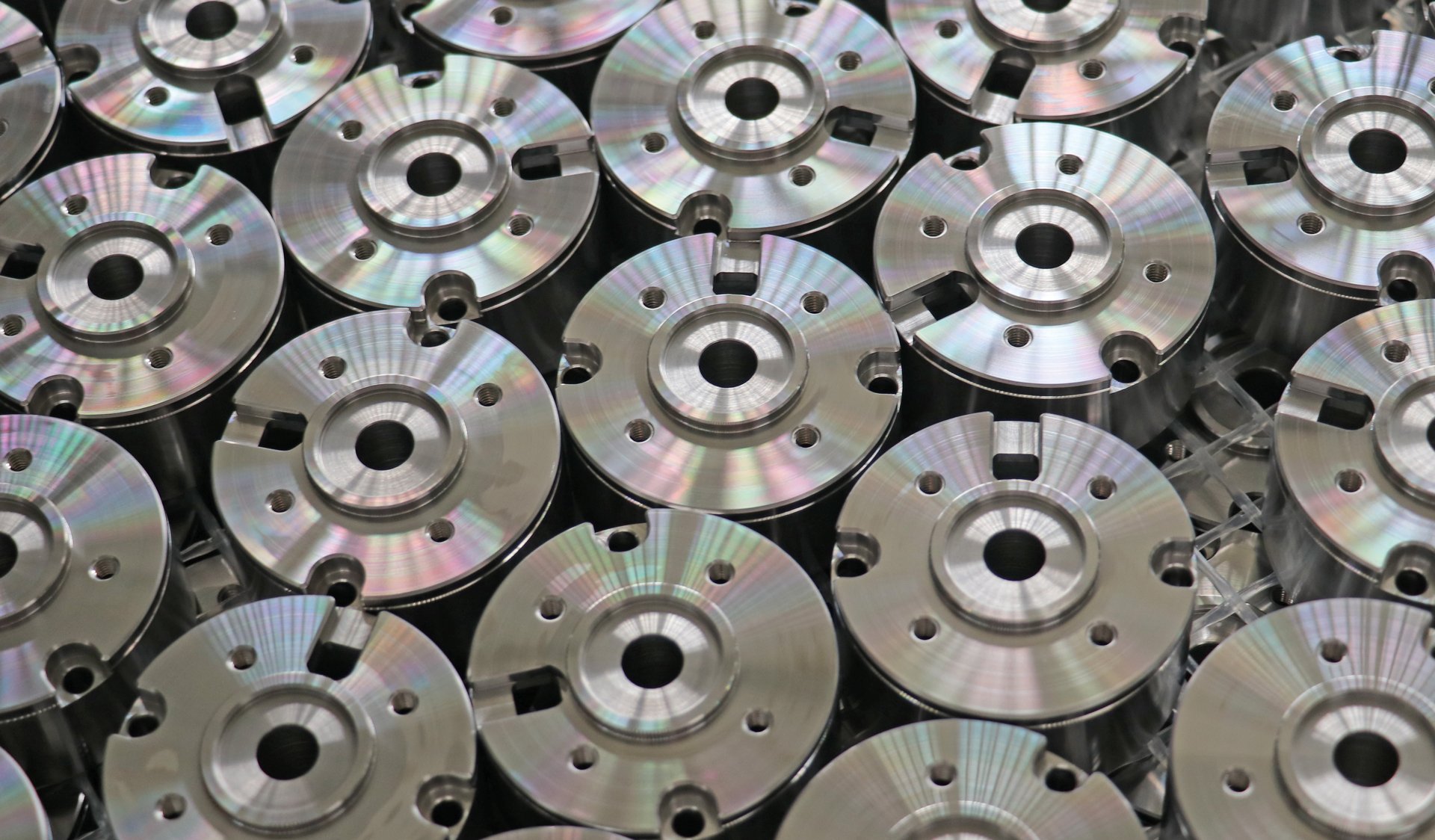
Titelthema
Drehen wird durchgängig digital
Lauble Präzisionsdrehteile hat den gesamten Werkzeugbestand digitalisiert. Da sich jetzt die 3D-Werkzeug-Zwillinge quasi auf Knopfdruck in die virtuelle Maschine laden lassen, wurde die Software zum festen Baustein in der Prozesskette. So kann sie ihre Stärken wie kürzere Umrüstzeiten an der realen Maschine, reduziertes Kollisionsrisiko und vereinfachte Optimierung der Teileprogramme voll ausspielen.
Bei der Lauble GmbH in Dunningen, Kreis Rottweil, dreht sich alles um Präzision und Oberflächengüte. Damit Drehteile in Losgrößen bereits ab 500 Stück wirtschaftlich zerspant werden können, bedarf es einer durchdachten Fertigungsstruktur, wie Geschäftsführer Sascha Auber betont. Er hat sich in den vergangenen Jahren intensiv mit der Thematik beschäftigt und gemeinsam mit seinem Assistenten Florian Kreuzberger Optimierungen an Maschinen, Peripherie, Software und vor allem an den Abläufen vorgenommen. Zentrale Absicht der beiden: „Um Kundenwünsche hinsichtlich Stückzahl, Qualität und Preis optimal erfüllen zu können, müssen wir sehr flexibel sein und schnell umrüsten können.“
Neben den Mitarbeitern sind die Maschinen das wichtigste Element in der Lauble-Produktion. „Nur wenn sie leistungsfähig sowie hoch verfügbar sind und auch nach Jahren noch ihre Präzision bringen, haben sie einen Platz in unserer Fertigung“, sagt Auber. Dort stehen derzeit 31 Drehmaschinen, davon sind 19 von Index: Produktionsdrehautomaten Index C200, C100, C65 und ABC, jeweils in mehrfacher Ausführung. „Auf Index-Produkte können wir uns verlassen – auch in der Peripherie, was beispielsweise die Software Virtuelle Maschine anbelangt“, bekräftigt der Geschäftsführer.
Den Nutzen früh erkannt
Bereits 2008 investierte er – zu einer damals neu angeschafften Index C65 – in diese Softwarelösung, welche die reale Maschine 1:1 in 3D abbildet. Mit ihr lässt sich die komplette Zerspanung simulieren. Auber beschreibt: „Wir nutzen sie nicht nur, um Kollisionen zu vermeiden, sondern auch um Umrüstzeiten zu verkürzen und um Teileprogramme zu optimieren. Zudem ist die virtuelle Maschine ideal, um neue Mitarbeiter auf die dreikanalige Programmierung zu schulen.“
Einzig der Aufwand, sie virtuell zu rüsten, war nicht zu unterschätzen. Schließlich muss jedes Werkzeug mit seinen exakten Maßen dreidimensional erstellt und eingepflegt werden – eine Aufgabe, die nicht nur CAD-Kenntnisse erfordert, sondern auch Zeit kostet.
Schon seit Jahren wird bei Lauble die Digitalisierung intensiv vorangetrieben, unter anderem mit der Installation eines Produktionsplanungssystems inklusive CAQ, BDE/MDE und DNC, das alle Maschinen mit den benötigten Programmen versorgt. In diesem Umfeld reifte bei den Verantwortlichen die Idee, die im Werk vorhandenen Zerspanungswerkzeuge mit Hilfe eines Toolmanagementsystems neu zu strukturieren, dazu jedes einzelne als digitalen Zwilling anzulegen und diesen auch für weitere Prozesse zu nutzen.
„Zum Beispiel für die virtuelle Maschine. Denn damit müsste sich das Rüsten enorm vereinfachen lassen“, war Auber überzeugt. 2018 machte er sich gemeinsam mit Kreuzberger an diese Aufgabe, der sich daraufhin federführend mit der Digitalisierung der Werkzeuge beschäftigte.
Viel Handarbeit erforderlich
„Zehn Jahre waren seit dem Kauf der virtuellen Maschine vergangen. Zehn Jahre, in denen CAD- und CAM- sowie Datenbank-Software große Fortschritte gemacht haben“, sagt Auber. „Umso überraschter war ich, dass für die Digitalisierung der Drehwerkzeuge noch ein so großer Aufwand betrieben werden muss.“ Kreuzberger konkretisiert: „Wir dachten ursprünglich, dass wir die meisten Modelle samt Geometriedaten aus dem Internet beziehungsweise von den Homepages der Werkzeuganbieter ziehen und per Mausklick zusammensetzen können.“
Weit gefehlt. Sofern Daten zur Verfügung stehen, müssen diese vor dem Zusammensetzen des Gesamtwerkzeugs geprüft werden, ob sie vollständig sind, die Bemaßung einheitlich und die Koordinatensysteme richtig platziert sind – und so weiter. Index ist diesbezüglich eine rühmliche Ausnahme, erzählt Kreuzberger: „Über den iXshop konnten wir uns alle 3D-Daten der Werkzeughalter und Werkzeuge problemlos besorgen. Da merkt man, dass die Digitalisierung bei Index schon weit fortgeschritten ist.“
Selbst beim 2019 gekauften Toolmanagementsystem eines renommierten Anbieters waren für die Drehwerkzeuge noch Anpassungen erforderlich. „Die Software ist zweifellos eine der besten. Aber man merkt, dass die Standardisierung bei Fräswerkzeugen einige Jahre Vorsprung hat. Der ist wohl auf den schon lange üblichen automatisierten Werkzeugwechsel aus großen Werkzeugspeichern zurückzuführen“, mutmaßt Kreuzberger.
Der Aufwand hat sich gelohnt
Zwei Jahre war Lauble mit der Neustrukturierung und Umsetzung aller Werkzeuge in 3D-Zwillinge beschäftigt. „Aber es hat sich auf jeden Fall gelohnt“, bestätigt Auber. „Wir haben im Toolmanagement eine Struktur geschaffen, die es auch neuen Mitarbeitern ermöglicht, sich – visuell unterstützt – sehr schnell einen Überblick über das Lauble-Werkzeug-Portfolio zu verschaffen.“
Da jedes vorhandene Werkzeug angefasst werden musste, beseitigten die Mitarbeiter Dubletten und bereinigten den Bestand. Alle Werkzeuge sind mittlerweile aus den bisher fast 30 Schubladenschränken in ein automatisiertes Hochregallager umgezogen. Via Barcode wählt der Mitarbeiter das benötigte Werkzeug aus und bekommt es in einer maßgeschneiderten Palette – von einem Laserpointer angestrahlt – ausgeliefert. Verwechslungsgefahr ausgeschlossen.
So kann Lauble besondere Vorteile für den Produktionsprozess realisieren. Denn die digitalisierten Werkzeuge lassen sich jetzt über eine speziell generierte Schnittstelle in die virtuelle Maschine übertragen. Eberhard Beck, Leiter Steuerungstechnik bei Index, erklärt: „Unsere Software beruht auf einem offenen Datenformat, das es den Anbietern von CAD/CAM-Software oder von Toolmanagementsystemen ermöglicht, passende Schnittstellen zu programmieren. Ist das Werkzeug eindeutig beschrieben, was bei Lauble nun der Fall ist, kann die virtuelle Maschine die Daten lesen und nutzen.“
Digital – vom Eingang bis zum Einsatz
Kreuzberger beschreibt das heutige Werkzeugmanagement im Rahmen der Prozesskette: „Jedes Werkzeug, das bei uns neu ankommt, wird zunächst in der Werkzeugverwaltung digital angelegt. Wenn der Einrichter für ein bestimmtes Bauteil seinen Werkzeugplan erstellt, pickt er sich dazu die benötigten Komponenten aus dem Toolmanagementsystem. Falls erforderlich baut er noch andere Werkzeuge und Aufnahmen zu digitalen Komplettwerkzeugen zusammen. Wenn er Bedarf zum Optimieren des NC-Programms sieht und die virtuelle Maschine rüsten will, öffnet er die Schnittstelle und zieht den kompletten Werkzeugplan rein. Dann wird eine Datei erzeugt, die er in die virtuelle Maschine überträgt. Dort stehen ihm alle Werkzeuge im 3D-Format zur Verfügung, so dass er damit per Drag-and-Drop den Revolver bestücken kann.“
Der Effekt: Dank der digital angelegten Werkzeuge kann der Mitarbeiter die virtuelle Maschine sehr viel schneller rüsten als früher. Fehler sind so gut wie ausgeschlossen. Das motiviert die Mitarbeiter, die virtuelle Maschine zu nutzen und mit ihr weitere Sekunden beim Rüstprozess herauszuholen. Zudem lässt das identische Verhalten der virtuellen und der realen Maschine Simulationen zu, die dem Bediener Sicherheit geben beziehungsweise neuen Mitarbeitern die Einarbeitung auf den anspruchsvollen Index-Produktionsautomaten erleichtern.
Kreuzberger hat ein praktisches Beispiel parat: ein Magnetgehäuse, das mehrere Fräsungen und Bohrungen aufweist. „Wir fertigen dieses Bauteil auf der Index C200. Der Maschineneinrichter, der auch fürs Programmieren zuständig ist, nutzte fürs Optimieren der komplexen Bearbeitungen mit teilweise drei gleichzeitig im Span befindlichen Werkzeugen die virtuelle Maschine. Dafür benötigte er etwa drei Stunden – eine Zeit, die er sonst an der realen Maschine gebraucht hätte. Anstatt fürs Optimieren stillzustehen, kann sie jetzt produzieren.“
Über Lauble
Die Lauble GmbH ist auf hochpräzise Drehbearbeitung spezialisiert. Am Stammsitz Dunningen produzieren 50 Fachkräfte auf mehr als 30 hochwertigen CNC-Maschinen anspruchsvolle Bauteile aus Automatenstahl, korrosionsfreien Stahllegierungen, NE-Metallen und Kunststoffen in Serien ab 500 Stück bis zu einer Million. Die Drehteile können bis zu 1200 Millimeter lang und im Durchmesser von drei bis 65 Millimetern sein. Lauble bedient verschiedene Industriezweige wie die Steuer- und Regelungstechnik, den Maschinenbau, die Elektrotechnik, die Medizintechnik und den Automobilzuliefererbereich.
Kontakt
Rainer Gondek
Leiter Global Marketing
INDEX-Werke GmbH & Co. KG Hahn & Tessky
Esslingen
Tel. +49 711 3191 1286
E-Mail senden
Anwenderkontakt
Lauble GmbH PräzisionsdrehteileDunningen
Tel. +49 7403 92908-0
E-Mail senden