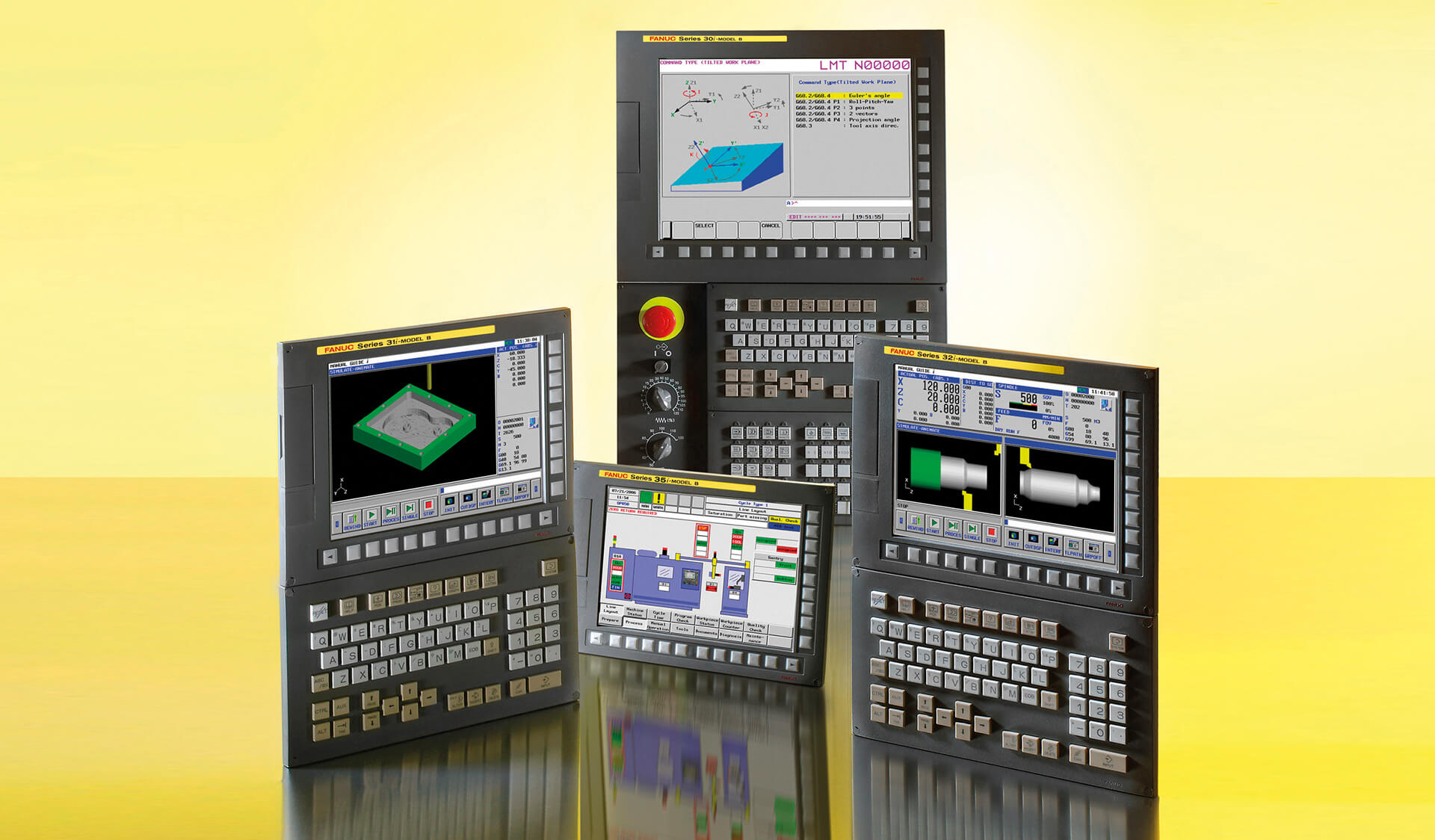
Aktuelles
Schluss mit überflüssigem Energieverbrauch
Energieeffizienz ist ein Schlagwort unserer Zeit. Um der damit verbundenen Anforderung gerecht zu werden, achten immer mehr Unternehmen darauf, ihre Produktion von Grund auf energiesparend zu gestalten. Insbesondere die Steuerungs- und Antriebshersteller haben in Sachen Energieeffizienz bei Werkzeugmaschinen einiges zu bieten.
Energie wird in den nächsten Jahren ein entscheidender Kostenund damit Wettbewerbsfaktor sein. Daher durchforsten viele produzierenden Unternehmen ihren gesamten Herstellungsbereich nach Energiefressern. Zweifellos beanspruchen Infrastrukturbereiche wie Klimatisierung, Beleuchtung oder Druckluftanlagen einen Großteil des Gesamtenergieverbrauchs. Auch Produktionsanlagen und Maschinen werden unter die Lupe genommen und auf Optimierungsmöglichkeiten untersucht.
Das bestätigen zahlreiche Werkzeugmaschinenhersteller, die immer häufiger von Kunden auf die Energieeffizienz ihrer Produkte angesprochen werden. Nicht ohne Grund: Schließlich haben wissenschaftliche Untersuchungen gezeigt, dass die Kosten für die elektrische Energie eines Bearbeitungszentrums mittlerer Leistung je nach Einsatzbedingungen mit bis zu 8800 Euro im Jahr zu Buche schlagen und damit bis zu 20 Prozent der Gesamtbetriebskosten ausmachen können. Ein Potenzial, bei dem das genauere Hinsehen lohnt.
Ausschalten ohne Zeitverlust
Um die Energieeffizienz einer Werkzeugmaschine zu verbessern, wird zunächst ihre Nutzung untersucht. Denn der Energieverbrauch verteilt sich auf die tatsächliche Betriebszeit und die Stand-by- Zeit, in der die Maschine in eingeschaltetem Zustand unproduktiv verweilt. Um den überflüssigen Energieverbrauch im Stand-by zu vermeiden, sind besonders die CNC-Steuerung und die integrierte SPS gefragt.
Sie sind in der Lage, abhängig vom Maschinenzustand – Einrichtbetrieb, kurzfristiger Teilemangel oder längerer Stillstand – Einzelkomponenten wie Beleuchtung, Lüftung, KSS-Versorgung oder Druckluft einzuschränken und auszuschalten.
Häufig kommt es zu Stillstandszeiten, in denen sogar das Komplettabschalten der Maschine in Frage käme. Doch lange Hochlauf- und Ausschaltzeiten, die vor allem bei PC-gesteuerten Maschinen auftreten, halten die Anwender davon ab. Fanuc CNCSteuerungen warten mit extrem kurzen Hochlaufzeiten auf: Weniger als 30 Sekunden dauert es, bis Steuerung und Motoren einsatzbereit sind. Das Ausschalten funktioniert gänzlich ohne Zeitverlust, so dass es sich im Hinblick auf die Energieeinsparung lohnt, selbst bei kurzen Stillstandszeiten die Maschine herunter zu fahren.
Seit der Gründung 1956 betreibt die FANUC CORPORATION die Automatisierung von Werkzeugmaschinen und gilt als Pionier bei der Entwicklung von CNC-Steuerungssystemen. Fanuc, mit Firmenhauptsitz am Fuß des Berges Fujiyama in Japan, ist weltweit das am stärksten diversifizierte Unternehmen von Produkten der Fabrikautomation (FA), Robotern sowie Werkzeug- und Spritzgussmaschinen.
Sehr effizient arbeitet die Fanuc Antriebstechnik mit ihren Versorgungsmodulen, Reglern und Motoren. Parallel zur Entwicklung der neuen CNC-Systeme der Serie 30i/31i/32i Modell B ist es gelungen, durch den Einsatz innovativer Leistungsmodule die Verlustleistung um zehn Prozent zu reduzieren. Weitere aktuelle Funktionen zur Energieeinsparung sind lastabhängige Lüfterdrehzahlen, eine Motortemperatur abhängige Regelung sowie kürzere Reglertaktzeiten. So weisen Fanuc Servomotoren und Antriebsregler Wirkungsgrade von nahezu 100 Prozent auf.
Auch im Schaltschrank lässt sich Energie einsparen. Fanuc Leistungsverstärker sind zum Beispiel für die so genannte Durchstecktechnik aufgebaut. Das heißt, die Kühlkörper befinden sich auf der Rückseite der Verstärker und somit hinter der Montageplatte, außerhalb des Gerätebereiches des Schaltschrankes. Der Klimatisierungsaufwand des Schaltschranks wird dadurch drastisch reduziert.
Den Energieverbrauch der Maschine darstellen
Seit 2009 erleichtert in den Fanuc Highend-CNC-Steuerungen der Serien 30i/31i/32i die Funktion „Energy Monitoring Function“ das optimale Einstellen der Achsen, wobei der effiziente Energieeinsatz berücksichtigt wird.
Die Funktion erlaubt das detaillierte Überwachen der Verbrauchs- und Rückspeisedaten aller Achsen während des Bearbeitungsprozesses.
Zusätzlich zu den Einzelwerten stehen kumulierte Werte zur Verfügung. Alle Überwachungsdaten können über FOCAS2 gelesen und über die Funktion Fanuc Picture oder Fanuc Auto HMI-NC ausgegeben werden. Das heißt, die Darstellungen sind nicht nur in der Standardanzeige verfügbar, sondern können auch in kundenspezifische Oberflächen integriert werden. Neu ist die „Energy Saving Level Function". Sie ermöglicht es, die Kenntnis über den achsenspezifischen Energieverbrauch zur Einstellung von Bearbeitungsgeschwindigkeiten zu nutzen.
CO2-Emissianen reduzieren
Fanuc CNC-Systeme zeichnen sich durch Nachhaltigkeit aus: Hohe Lebensdauer, niedriger Verschleiß und eine Ersatzteilversorgung von mindestens 25 Jahren sind obligatorisch. Durch die hohe Lebensdauer des CNC-Systems bleiben die Maschinen sehr lange in der Produktion, wodurch weniger Rohstoffe für die Herstellung neuer Maschinen verbraucht werden.
Energieverbrauch und CO2-Ausstoß sind nach wie vor eng aneinander gekoppelt. Man rechnet im Allgemeinen, dass eine erzeugte Kilowattstunde einem CO2-Ausstoß von 0,43 Kilogramm gleichzusetzen ist. Daher ist es auch in dieser Hinsicht interessant, aktuelle Motortechnologien unter energetischen Gesichtspunkten zu betrachten.
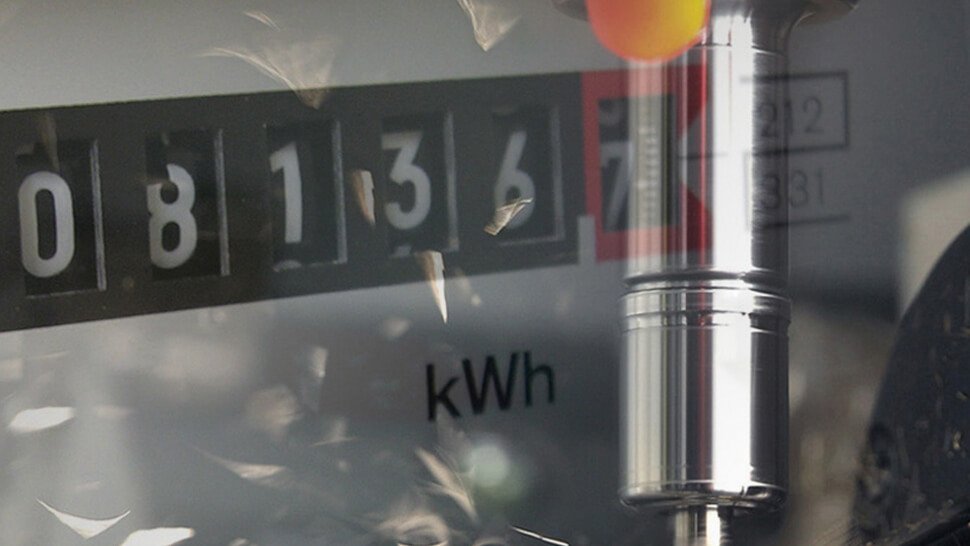
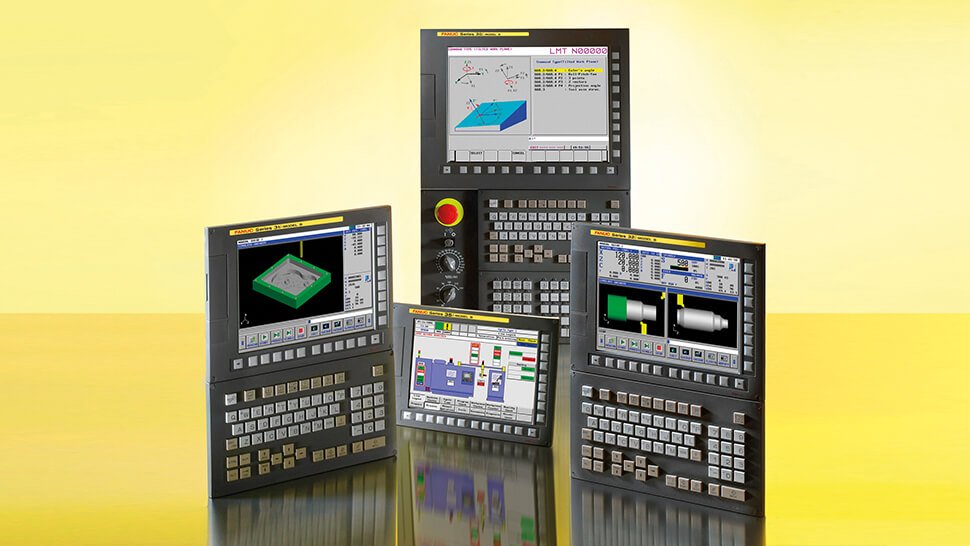
Energetisch ungünstig ist zum Beispiel der Einsatz eines Linearantriebs gegenüber dem eines Servomotors, denn Linearantriebe haben hohe Anschlussleistungen und benötigen daher häufig externe Kühlung. Auch bei den Spindelmotoren gibt es Unterschiede: Synchron-Spindelmotoren haben gegenüber Asynchron-Spindelmotoren insbesondere im Leerlaufverhalten und bei geringer Leistungsabgabe höhere Verlustleistungen und benötigen häufig zusätzliche Kühlung. Bei Asynchron-Spindelmotoren senkt beispielsweise die Absenkung der Erregung im Leerlauf den Wärmeeintrag in die Spindel der Maschine um rund 30 Grad Celsius.
Rückspeisung senkt den Energieaufwand
Seit mehr als 20 Jahren ist es bei Fanuc üblich, dass beim Bremsen von Servo- und Hauptspindelmotoren die Energie nicht über einen Widerstand in Wärme umgewandelt wird, sondern rückgespeist werden kann. Aus energetischer Sicht lassen sich dadurch beispielsweise bei einem Bohrzyklus auf einem Bearbeitungszentrum bis zu 34 Prozent Energie einsparen. Bei einer angenommener Gesamtleistung von 13,2 Kilowatt, einem 2D-Stunden-Tag und 20 Tagen pro Monat entspricht das einer CO2 -Reduzierung von jährlich 2,3 Tonnen.
Speziell für die Anwendung großer Servomotoren – im Programm sind Modelle bis zu 3000 Newtonmeter – hat Fanuc einen eigenen Zwischenspeicher entwickelt, das „Energy Charge Modul" (ECM). Anstatt die Energie direkt ins Netz zurückfließen zu lassen, nimmt das ECM die beim Bremsen frei werdende Energie aus dem Zwischenkreis der Servoverstärker auf und stellt sie den Servomotoren für den erneuten Beschleunigungsvorgang wieder zur Verfügung. Nur die darüber hinaus benötigte Energie wird aus dem Netz zugeführt. Damit lassen sich nicht nur Leistungsspitzen vermeiden, sondern die Energie wird zudem effizienter genutzt, zum Beispiel bei regelmäßiger Beschleunigung und Bremsung. Ein typischer Einsatzfall ist die Anwendung bei Servopressen.
Kontakt
Thomas Unterricker
Manager Application
FANUC FA Deutschland GmbH
Neuhausen a. d. F.
Tel. +49 7158 187 400
E-Mail senden