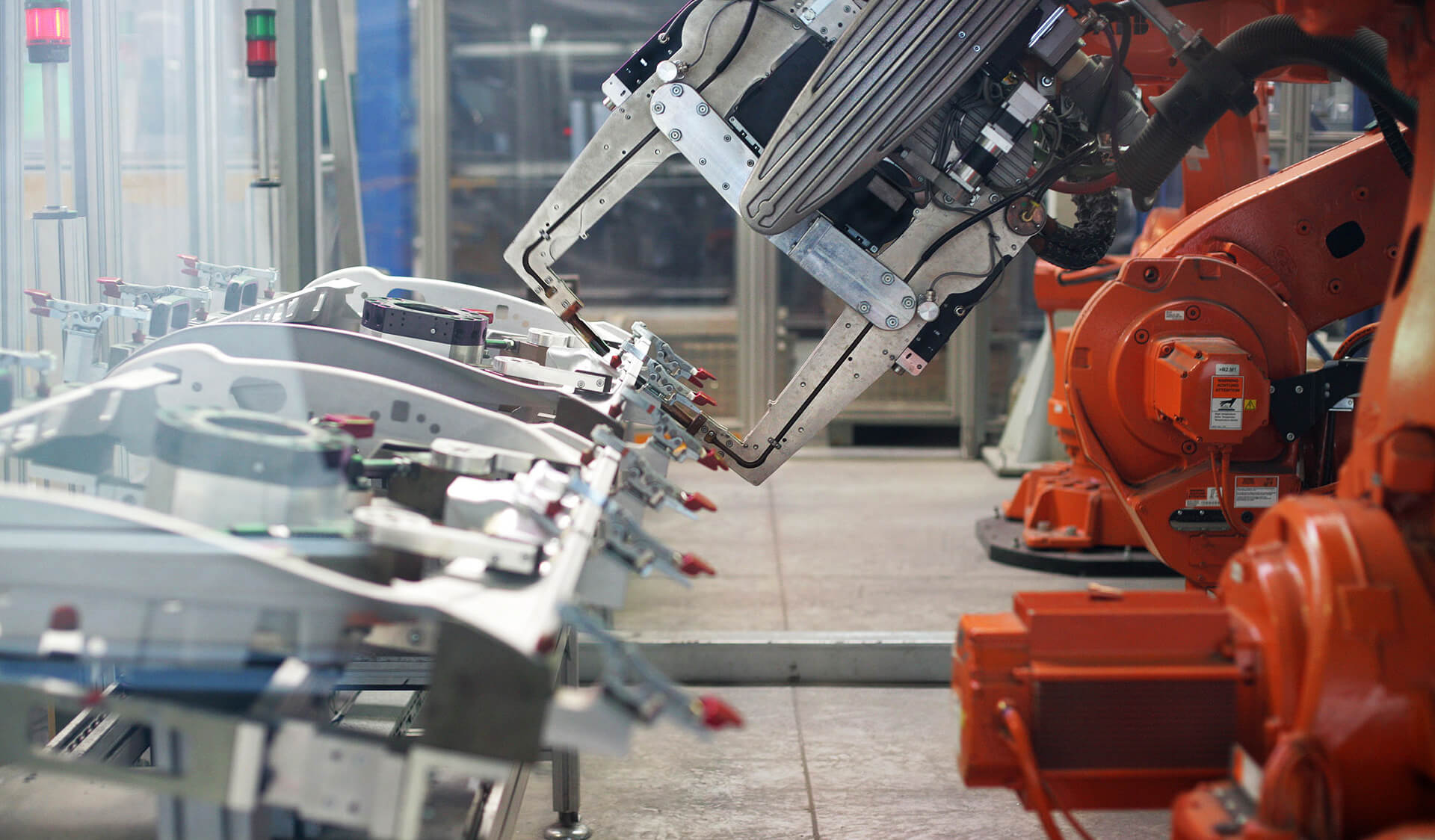
ROBOTIK Arena
Vernetztes Schweißen
Schweißen spielt in nahezu allen Branchen von Industrie und Handwerk eine wichtige Rolle. Industrie-IT perfektioniert die Fügetechnologie.
Neben wirtschaftlichen Zielen rangieren oft Nutzwerte wie höhere Qualität, Zuverlässigkeit und Reproduzierbarkeit an vorderer Stelle einer Automationslösung. Prozessfähigkeit und -sicherheit des Verfahrens sind eine wesentliche Bedingung für solche Lösungen. Beim Lichtbogenschweißen erfüllt die digitale Revolution diese Voraussetzung.
Spezifische Begriffe beschreiben den Nutzen: Gleichmäßige Spaltüberbrückung, homogene Naht, einwandfreie Flanken- und Wurzelbildung, geringer Verzug, wenig oder keine Spritzer, vorhersehbare reproduzierbare Nahtqualität und lückenlose Dokumentation aller relevanten Daten. Eine IT-Lösung, die dem Anwender diese Vorteile erschließt, ist der Xplorer von Fronius.
Automatisiertes Schweißen
Ein Automobilzulieferer der Tier-1-Kategorie setzt an einem Standort rund 100 unterschiedliche Schweißsysteme ein. Die Fachleute fügen Stoßfänger, Abgassysteme und Aluminiumtüren. Die verschiedenen Komponenten stellen hinsichtlich Werkstoff, Materialdicke, Nahtgeometrie, Taktzeit und weiteren Randbedingungen spezifische Anforderungen an die Fügetechnik. Hinzu kommen die Forderungen der Auftraggeber zum Beispiel bezüglich der Dokumentation. Deshalb haben die Verantwortlichen des Unternehmens gemeinsam mit den Roboterherstellern und Fronius die jeweils am besten geeigneten Schweißverfahren und -systeme ausgewählt. Alle sind in ein Netzwerk integriert, das der Xplorer managt.
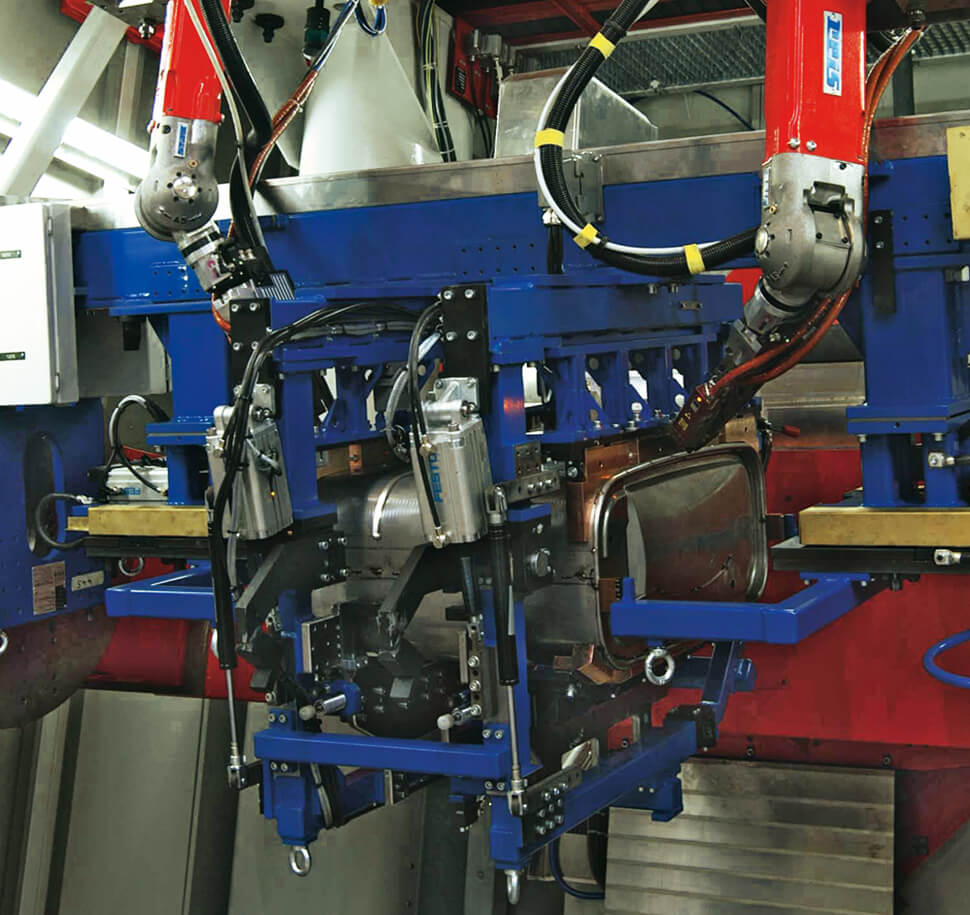
Abgassysteme müssen absolut gasdicht gefügt sein. Dabei kommt der Cold-Metal-Transfer-Prozess von Fronius zum Einsatz. Foto: Eberspächer Unna
Optimale Lösung
Zum Fügen der Stoßfänger aus 2,2 Millimeter dicken Stahlblechen ist das konventionelle Lichtbogenfügen besonders geeignet. Dafür sprechen technische und wirtschaftliche Gründe. Die volldigital gesteuerten universellen TransPuls Synergic 4000 Remote schweißen die Stoßfängerteile mit Geschwindigkeiten bis zu 0,5 Metern pro Minute. Eine Produktionseinheit „Bumperline“ besteht aus drei Schweißzellen mit jeweils zwei Stromquellen, zwei Schweiß- und einem Handlingroboter. In insgesamt elf Schweißstationen fügen sie 14 Einzelteile mit 80 Schweißnähten zu einer kompletten Baugruppe.
Stellen die Fertigungsfachleute ihre Produktion auf ein anderes Modell von Stoßfängern um, dann bestehen die „Umbauarbeiten“ nur in wenigen Mausklicks am PC des Schweißfachingenieurs. In regelmäßigen Abständen sichert der Xplorer Daten der abgearbeiteten Schweißjobs auf dem Server und archiviert sie als Beleg für zukünftige Auswertungen.
Katalysatorsysteme in Abgasanlagen von Diesel-Nutzfahrzeugen müssen Fehlfunktionen definitiv ausschließen. Deshalb dürfen sie keine Fremdkörper wie Schweißspritzer enthalten. Sonst bestünde die Gefahr, dass diese das Katalysatorsubstrat beschädigen. Deshalb fiel die Entscheidung für den CMT-Prozess (Cold Metal Transfer). Das innovative Verfahren kennzeichnet eine Kombination aus reversierender Drahtelektrode und volldigitaler Regelung. Sie erkennt zum Beispiel einen Kurzschluss und unterstützt durch das Rückziehen des Drahtes die Tropfenablöse des Schweißzusatzwerkstoffes. Der nahezu stromlose Werkstoffübergang beim Drahtrückzug und der dadurch unterbrochene Lichtbogen bewirken im bis zu 100-Hertz-Takt den geringen Wärmeeintrag („Cold“). Resultat: Null Spritzer, weniger Nacharbeit, keine Schmelzbadstütze erforderlich, geringerer Verzug und höhere Spaltüberbrückbarkeit.
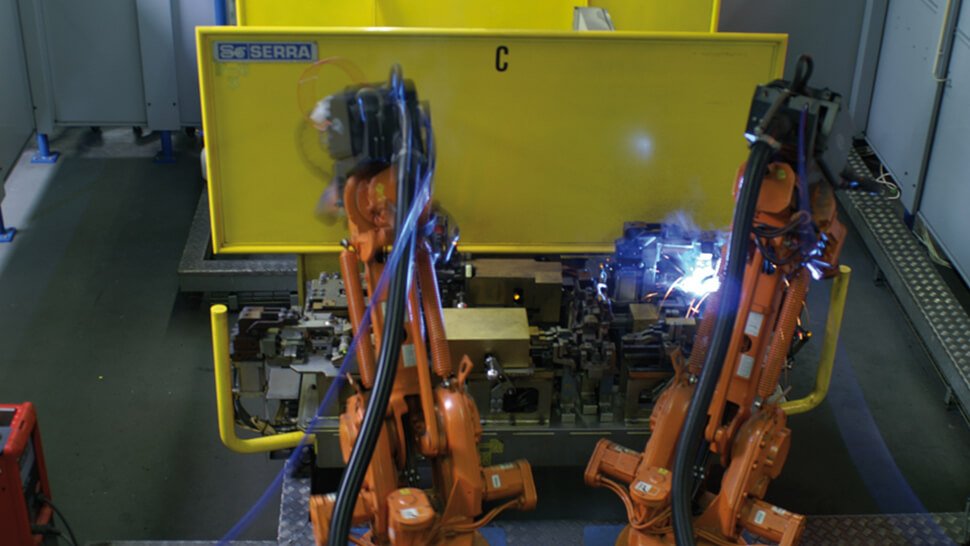
Das Schweißen der Stoßfänger wird vom Schreibtisch aus geregelt. Foto: Griwe
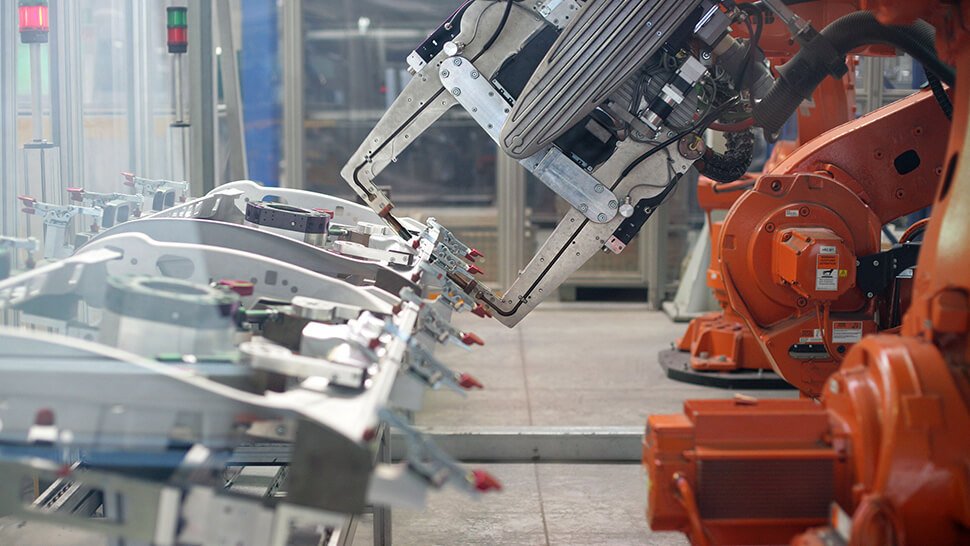
Aluminiumbleche verstärken den Aluminiumdruckgussrahmen der vier Türen eines exklusiven Oberklasse-Autos. Der Roboter schweißt mit einer Geschwindigkeit bis zu neun Metern pro Minute im CMT-Prozess. Foto: Fronius
Vier Roboter-Schweißzellen mit acht TransPuls Synergic 5000 CMT-Schweißsystemen bilden die Linie für die zu fügenden Module. Die Edelstahlbleche sind bis zu 6 Millimeter dick. Der Xplorer übernimmt die integrierte Prozessüberwachung und garantiert, dass nur Abgassysteme in der geforderten Qualität die Produktion verlassen. Außerdem stellt er das komplette Paket relevanter Funktionen zur Verfügung: Speichern der Soll-Prozessdaten (Jobs) unterschiedlicher Schweißprozesse, Dokumentation von Einstellungen und Änderungen sowie der Ist-Werte, Qualitätsmanagement, statistische Auswertungen sowie Back-Up-Funktionen.
Funktionen der Software
Die Freeware Xplorer vernetzt automatisierte Schweißsysteme und erzeugt einen virtuellen Leitstand. Ihre grafische Benutzeroberfläche und selbsterklärende Symbole erleichtern dem Anwender das übersichtliche Verwalten von beliebig vielen Schweißsystemen in seiner Produktion. Deren Standort und Status erkennt er auf einen Blick. Der Anwender kann zwischen vier aufeinander aufbauenden Funktionspaketen des Xplorer wählen. Paket 1 enthält als Basis den Xplorer sowie die mit den entsprechenden Schnittstellen und der aktuellen Firmware ausgestatteten Schweißsysteme. Hinzu kommen bei Paket 2 der JobExplorer und bei Paket 3 zusätzlich die Software zur Dokumentation. Die Funktionen des JobExplorer übernimmt bei Paket 4 die Fernbedienung RCU 5000i.
Für anspruchsvolle Anforderungen
Der Xplorer managt das Schweißen und Löten mit allen automatisierten Schweißsystemen von Fronius. Er bietet umfangreiche Funktionen und Optionen, die auch anspruchsvolle Anforderungen und Wünsche von Fertigungsplanern, Produktionsverantwortlichen, Qualitätsmanagement und Controllern erfüllen. Mit dem kostenfrei zur Verfügung gestellten Xplorer erzielt der Anwender Transparenz in seiner Schweißfertigung sowohl hinsichtlich Organisation, Technik, Wirtschaftlichkeit, Energieverbrauch, Dokumentation und Gewährleistung. Der Anwender kann die Funktionspakete entsprechend seinen Anforderungen wählen.
Kontakt
Gerd Trommer
rgt redaktionsbüro
Gernsheim
Tel. +49 6258 9320-0
E-Mail senden