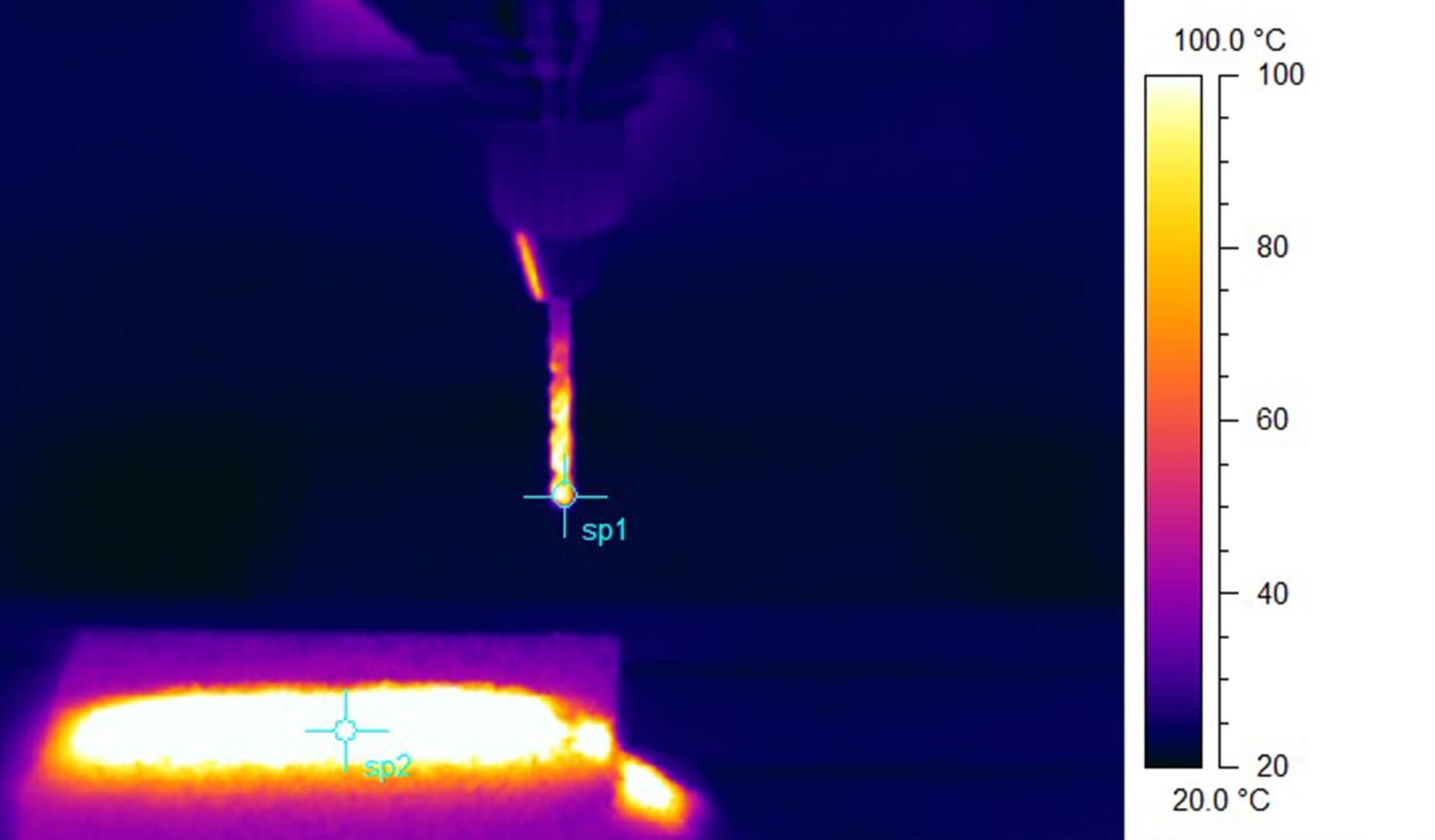
TOOLS Arena
Weniger kann mehr sein
Der Begriff Minimalmengenschmierung ist seit mehr als einem Jahrzehnt verbreitet. Als eine Möglichkeit, die Menge an herkömmlichen Kühlschmierstoffen zu reduzieren, wurde die Minimalmengenschmierung Ende der 1990er Jahre entwickelt. Seitdem hat die Technik verschiedene Entwicklungsstufen durchschritten. Im Rahmen der Effizienz- und Nachhaltigkeitsdiskussionen in der Produktionstechnik gewinnt sie an Bedeutung.
Um die Minimalmengenschmierung effektiv zu nutzen, muss man sich über den Begriff, über die Technik und über die technologischen Einflüsse Gedanken machen. Nur über ein optimales Zusammenwirken zwischen Mensch – Werkzeug/Aufnahme – Maschine und Technologie lässt sich diese noch relativ junge Kühlschmiermethode prozesssicher und damit kostenoptimal nutzen. Was versteht man unter dem Begriff Minimalmengenschmierung und wie ist seine Charakteristik? In der DIN 69090-1 sind die Begriffe für die Systemelemente im Gesamtsystem der Minimalmengenschmierung (MMS) festgelegt. Sie beziehen sich auf die spanende Bearbeitung mit Werkzeugen mit geometrisch bestimmter Schneide, schwerpunktmäßig für den Einsatz von rotierenden Werkzeugen (Quelle 1).
Die besondere Charakteristik lässt sich in drei Punkten zusammenfassen:
- Verbrauchs-, Verlustschmierung
- Verbrauch etwa fünf bis 50 Milliliter pro Stunde
- Zwei der drei Hauptaufgaben des üblichen Kühlschmierstoffs, nämlich Kühlung und Spänetransport, werden nur teilweise erfüllt.
Damit steht die Minimalmengenschmierung in Konkurrenz zu den herkömmlichen Kühlschmierstoffen und der Trockenbearbeitung. Diese Konkurrenz spiegelt sich in den Kosten, dem Verbrauch, der Unterhaltung, der Kühlung, dem Spänetransport, der Reibungsminimierung, der Bearbeitungstechnologie, den Werkzeugen, den Maschinen und der Arbeitsmedizin wider. Bei aller anfänglichen Euphorie unterliegt die Minimalmengenschmierung einer stetigen Veränderung und Anpassung, die abhängig von den verschiedensten Einflussgrößen ist (Bild 1). Nur durch ein zielgeführtes Anpassen der einzelnen Einflussgrößen lässt sich die Minimalmengenschmierung optimal und nachhaltig einsetzen. Als Basis dienen detaillierte Kenntnisse über die einzelnen Einflussgrößen.
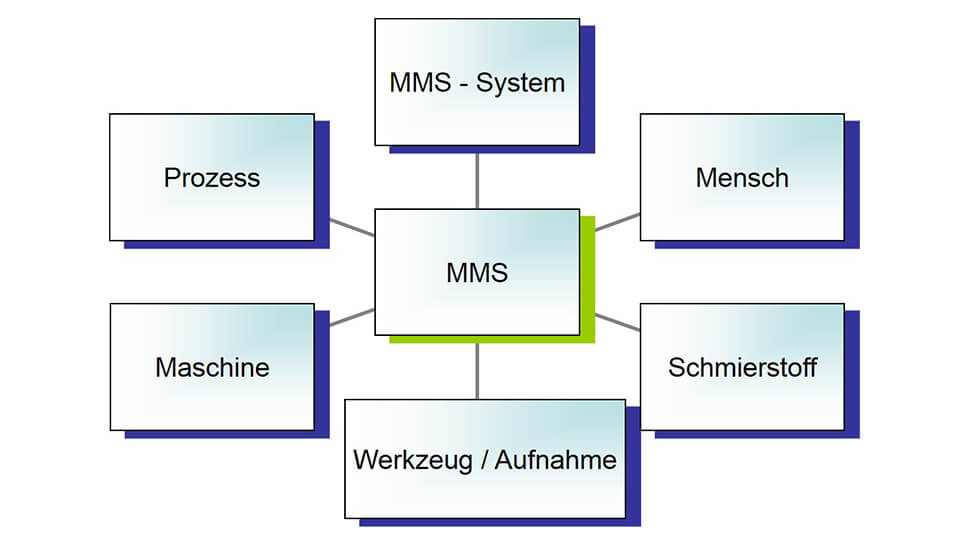
Bild 1. Einflussgrößen auf die Minimalmengenschmierung. Grafik: Bielomatik
Einflussgrößen
Es ist sehr wichtig, sich die einzelnen Einflussgrößen im Detail anzusehen. Es gibt unterschiedliche Grundausführungen des Minimalmengenschmiersystems (Bild 2). Die Auswahl hängt vom Bauteil, dem Werkzeug, dem Fertigungsverfahren und der Maschine ab. Die Einflussgröße Mensch ist ein wesentlicher Gesichtspunkt und nicht zu unterschätzen. Hier wird schon im Vorwege die Entscheidung getroffen, ob die Minimalmengenschmierung eingesetzt wird oder nicht. Zudem entscheiden die beteiligten Personen über Erfolg und Misserfolg. Deshalb ist es von immenser Bedeutung, dass alle betroffenen Bereiche mit einbezogen werden, damit das Projekt „Minimalmengenschmierung“ zum Erfolg wird. Es ist ein Lernprozess.
Beim Schmierstoff kann man sich auf die Erfahrungen der Aggregatehersteller (MMS) und der Lieferanten/Hersteller der Schmierstoffe beziehen. Wichtig sind ein gutes Schmiervermögen und eine hohe thermische Belastung des Schmierstoffes. Es wird zwischen synthetischen Esterölen und Fettalkoholen unterschieden.
Bei der Kombination Werkzeug/Aufnahme geht es im Wesentlichen um die Übergabepunkte des Aerosols. Es gibt verschiedene Werkzeug- und Aufnahmehersteller, die optimale Übergabesysteme anbieten. Wichtig ist es, dass keine Versackung (Prallkanten und Hohlräume) entsteht. Ein besonderes Augenmerk muss man den Kühlkanälen widmen. Hier sind die Lage, Form und Größe von Bedeutung. An Bedeutung nimmt der Faktor Beschichtung und Grundgeometrie des Werkzeugs beim Einsatz von Minimalmengenschmierung zu.
Die DIN 69090-3 bezieht sich auf die technischen Voraussetzungen und Anforderungen an die spanende Bearbeitung mit Werkzeugen mit geometrisch bestimmter Schneide bei der Minimalmengenschmierung (MMS) (Quelle 2).
Die Einflussgrößen Prozess und Maschine unterliegen einer Wechselbeziehung, die darin besteht, ob der bestehende Prozess überarbeitet werden kann oder neu definiert werden muss. Hier ist dann auch die Frage zu beantworten: Gilt das für eine vorhandene Maschine oder für eine Neubeschaffung? Aus diesem Grund muss man betonen, dass die Minimalmengenschmierung ein wesentlich kleineres Technologiefenster hat als die herkömmliche Nassbearbeitung. Zudem sind keine Grundlagen in Tabellenbüchern zu dieser Thematik vorhanden.
Die Maschine legt mit fest, ob man sich für eine externe oder interne Zuführung entscheidet. Das Fertigungsverfahren hat auch Einfluss auf die Zuführung des Aerosols. Bei den Fertigungsverfahren Bohren und Fräsen sollte eine interne Zuführung genutzt werden. Wird eine Neubeschaffung einer Werkzeugmaschine geplant, sollten die Absaugung, der Spänetransport und die Zuführung durch die Spindel berücksichtigt werden.
Die DIN 69090-2 enthält Festlegungen für Werkzeugmaschinen, die für den Betrieb mit Minimalmengenschmierung vorgesehen sind, und beschreibt die technischen Voraussetzungen und Anforderungen an diese Maschinen. Es werden ebenfalls Anforderungen für die mechanischen und elektrischen Schnittstellen der einzelnen Systemelemente im Gesamtsystem der Maschine zu den MMS-Systemen und zum Werkzeug hin festgelegt, mit dem Ziel der Austauschbarkeit und der modularen Weiterentwicklung (Quelle 3).
Kontakt
Thomas Hänert
Wissenschaftlicher Mitarbeiter
Hochschule für Angewandte Wissenschaften Hamburg (HAW)
Fakultät Technik und Informatik
Department Maschinenbau und Produktion
Institut für Produktionstechnik
Hamburg
Tel. +49 40 42875 8665
E-Mail senden
Prof. Dr.-Ing. Christian Stark
Professor für Produktionstechnik
Institut für Produktionstechnik an der Hochschule für angewandte Wissenschaften
Hamburg
Anzeige
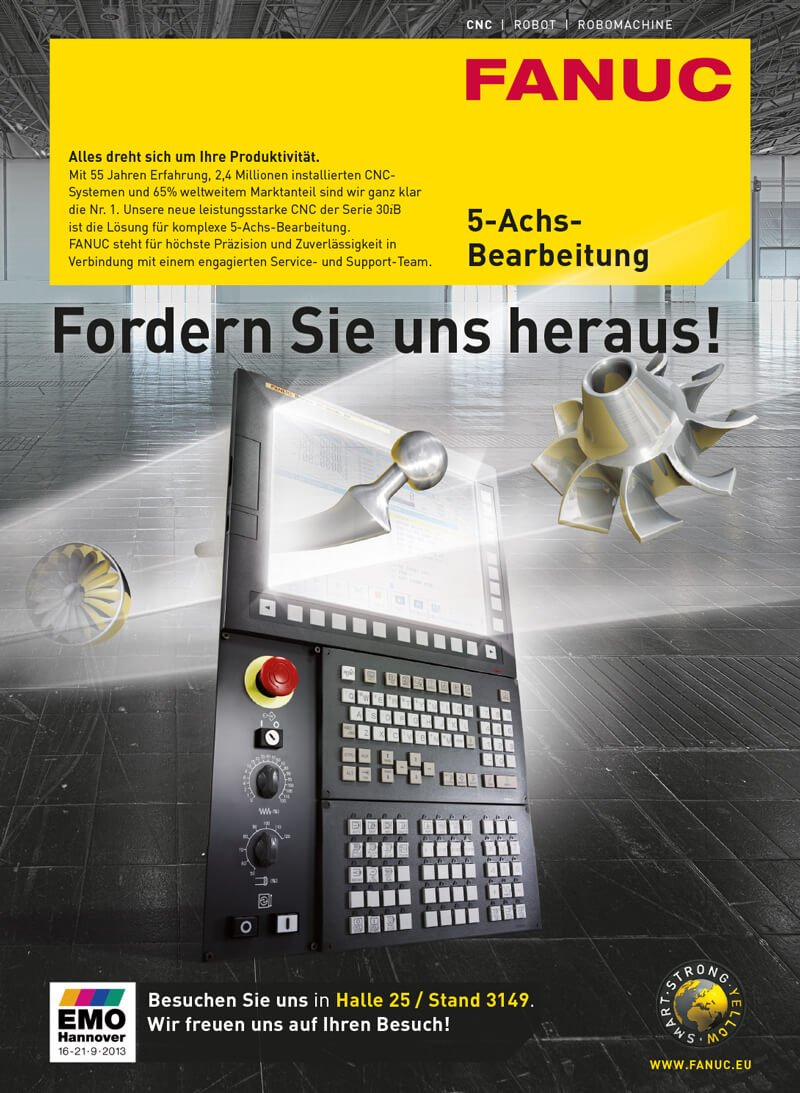