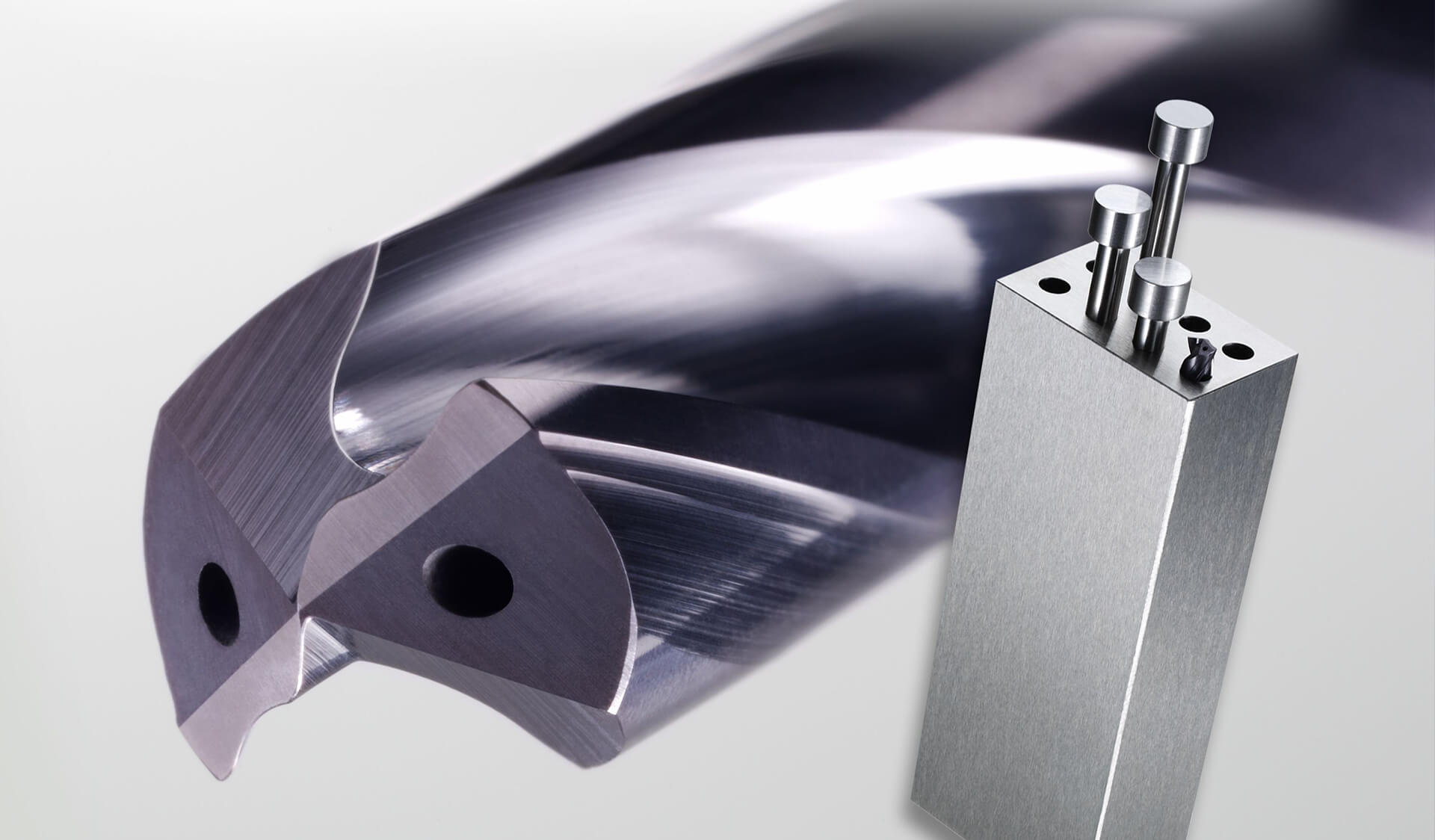
Aktuelles
Sondermaschine überflüssig
Löcher mit Tiefen bis zum 60fachen des Werkzeugdurchmessers lassen sich günstig wie präzise und prozesssicher fertigen. Die ZF Friedrichshafen AG in Passau setzt Bohrer der Reihe „MHS“ auf Standardbearbeitungszentren ein und nicht auf Sondermaschinen. Gebohrt werden Wellen aus Einsatz- und Vergütungsstahl.
30xD galt 2005 noch als sensationell. Heute sind Werkzeuge mit einem Längen/Durchmesser-Verhältnis bis 40xD bereits Standard. „Wendelbohrer mit 50xD sind bislang noch die Sonderlösung“, sagt ZF-Mitarbeiter Volker Lang. Aber auch sie liefen in den Betrieben der ZF Friedrichshafen AG ohne Probleme. Lang ist Industrietechniker und im Werk Passau-Grubenweg zuständig für Planung und Projekte. Eines seiner Vorhaben ist, das Tieflochbohren voranzubringen. Der derzeitige Stand bei vergütetem und bei Einsatzstahl liegt bei 60xD. Möglich machen dies mit Titanaluminiumnitrid (AlTiN) beschichtete und innen gekühlte Wendelbohrer von MMC Hartmetall GmbH, Meerbusch, die Lang auf regulären Bearbeitungszentren einsetzt. Der Prozess sei sicher, der geldwerte Nutzen erheblich, betont Lang.
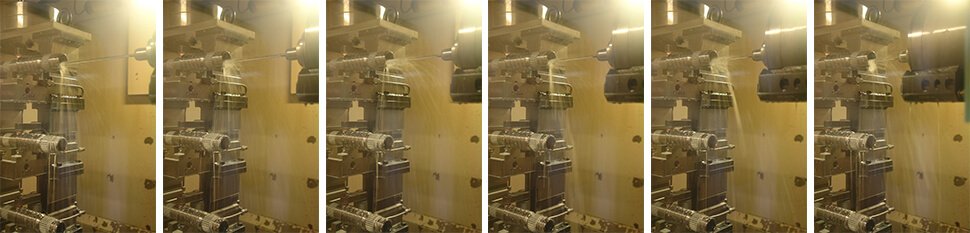
Die Löcher bis 7,5 Millimeter im Durchmesser werden bis 600 Millimeter tief. Davon werden derzeit 410 Millimeter mit Vollhartmetallbohrern erreicht. Den Rest erledigen Einlippenbohrer. Fotos: facts-and-figures/Filì
Passau ist Produktions- und Entwicklungsstandort der ZF Friedrichshafen. Dort werden Achsen und Getriebe sowie Antriebskomponenten hergestellt für Bau- und Landmaschinen, Busse und Pkw, darunter auch 700 Millimeter lange Zentral-, An- und Abtriebswellen für die Getriebe von Personen- und Nutzfahrzeugen, Land- sowie Baumaschinen. Zwischen 14.000 und 16.000 werden pro Jahr produziert. Hinzu kommen so genannte Exoten: Wellen für Schlepper- und Automatikgetriebe. Gängige Stähle sind 16MnCr5 (Werkstoffnummer 1.7131) und 42CrMo4 (1.7225). Bei manchen werden fünf Bohrungen eingebracht, bei anderen nur eine.
Größte Tiefe der Kanäle mit bis zu 7,5 Millimetern Durchmesser sind 600 Millimeter. Davon werden derzeit 410 Millimeter mit MMC-Vollhartmetall-Werkzeugen erreicht. Den Rest besorgen Einlippenbohrer. Vorgabe für Toleranz und Oberflächenqualität sind jeweils 0,2/-0,1 Millimeter beim Durchmesser, 1 Millimeter Symmetrie, 2 Millimeter bei der Tiefe sowie Rz100 max. als Rautiefe. Je nach Werkstoff liegt der Standweg der Bohrer zwischen 40 und 100 Metern.
Stahl bis 60xD prozesssicher bohren
„Wir machen das auf einem ohnehin vorhandenen Standardbearbeitungszentrum“, sagt Fertigungsmeister Franz Schwarzmüller, „und eben nicht auf einer eigenen Tiefbohr- oder Spezialmaschine.“ Diese Investition wäre ZF beim Einsatz anderer Tools nicht erspart geblieben. Vielmehr würden die MMC-Bohrer wie jedes gewöhnliche Werkzeug auch aus dem Zentrumsmagazin gewechselt: „Das spart erheblich Zeit und Geld.“ Voraussetzung sei indes, dass der Ablauf verlässlich ist. Bricht der Bohrer, addieren sich die Kosten für Werkstück, Werkzeug und Maschinenausfall schnell auf eine vierstellige Summe.
ZF Passau und die Berater von MMC hatten die Werte seit 2005 - dem Beginn der Zusammenarbeit und 30xD-Bohrern – Schritt für Schritt ausgereizt und gesichert. Das Zwischenergebnis rechnet sich. Der 6,83 Millimeter durchmessende „MHS0683-L60CVP15TF“ bohrt 410 Millimeter in 1,2 Minuten aus.
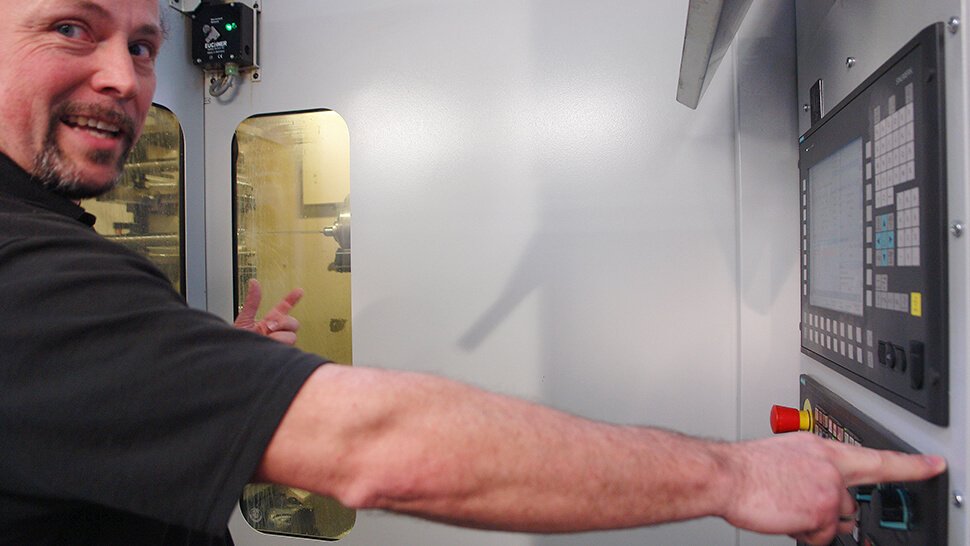
Volker Lang, Planung und Projekte, ZF Friedrichshafen AG in Passau: „Stand beim Bohren von vergüteten und Einsatzstählen ist 60xD.“ Foto: facts-and-figures/Filì
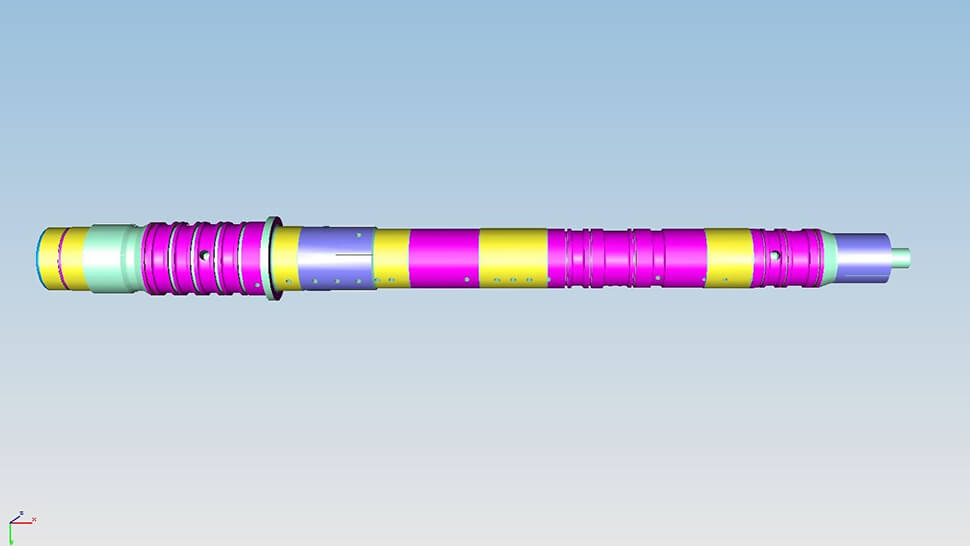
Antriebswelle als 3D-Modell: Als Toleranz und Oberflächengüte gelten 0,2/-0,1 Millimeter beim Durchmesser, 1 Millimeter in der Symmetrie, 2 Millimeter bei der Tiefe sowie Rz 100 max. Bild: ZF Friedrichshafen
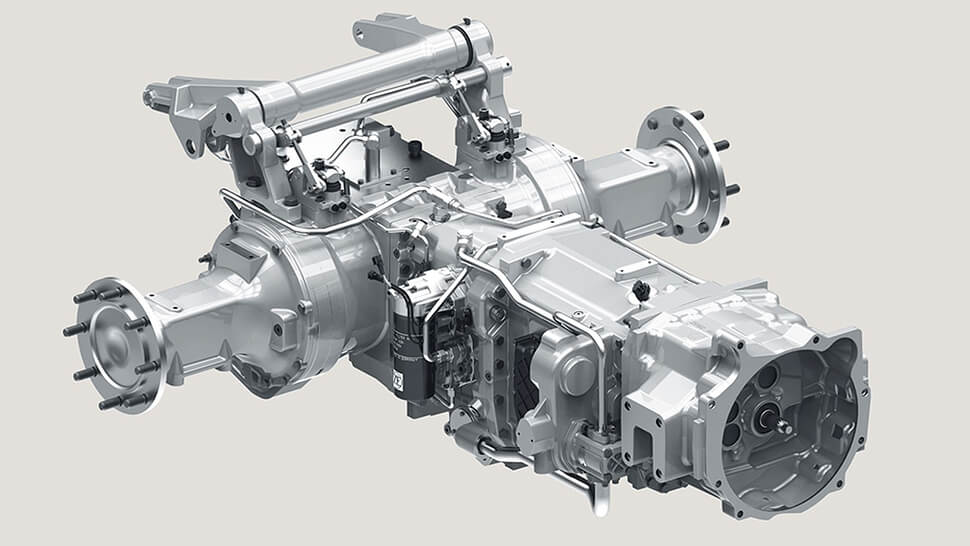
ZF Friedrichshafen setzt die Antriebswellen in Getriebe für Bau- und Landmaschinen, Busse und Pkw, Personen- sowie Nutzfahrzeuge ein. Bild: ZF Friedrichshafen
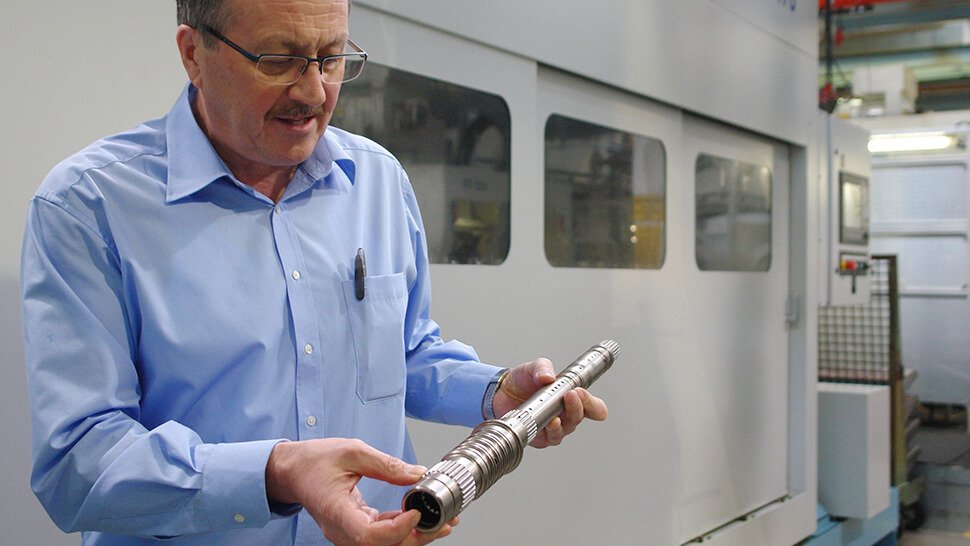
Bearbeitet auf einem Standardbearbeitungszentrum von Hüller Hille statt auf Sondermaschinen: Franz Schwarzmüller, Fertigungsmeister bei ZF Friedrichshafen in Passau, mit einer fertig tiefgebohrten Welle. Foto: facts-and-figures/Filì
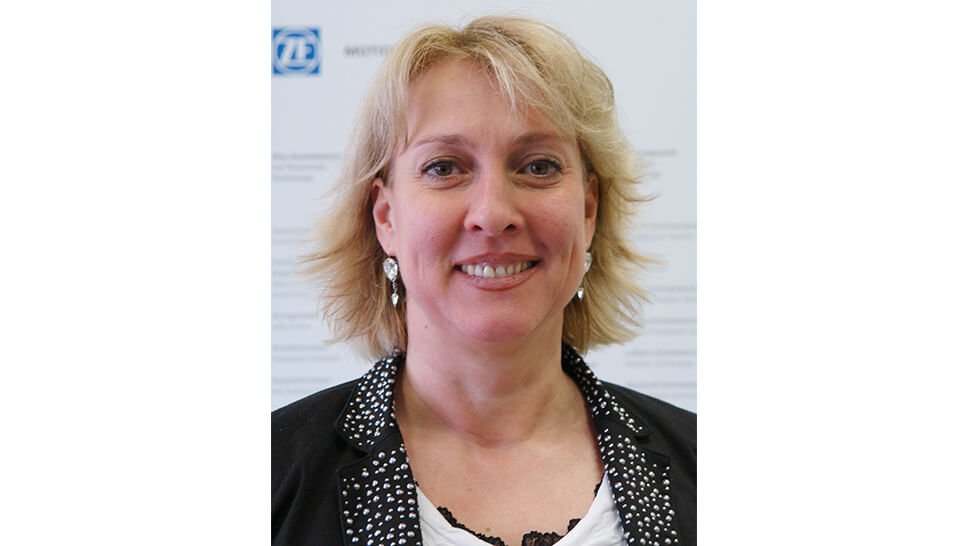
Petra Reinhold, Technisches Management bei MMC Hartmetall: „Auch bei schwankender Werkstoffqualität identische Bearbeitungsergebnisse.“ Foto: facts-and-figures/Filì
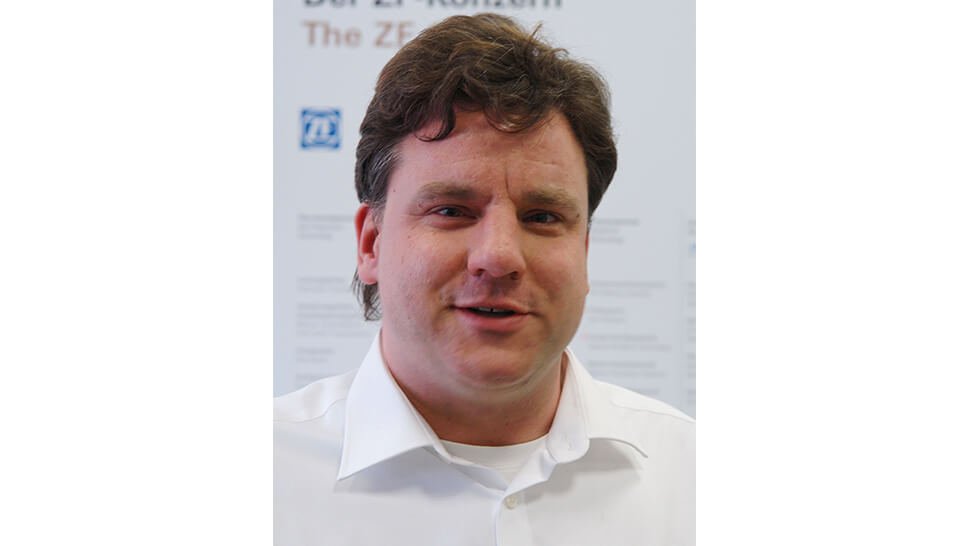
Wilfried Dyduch, Anwendungstechnik MMC Hartmetall: „Ursprünglich als Tieflochbohrer mit innerer Kühlmittelzufuhr für gehärtetes Material bis 52 HRC entwickelt worden.“ Foto: facts-and-figures/Filì
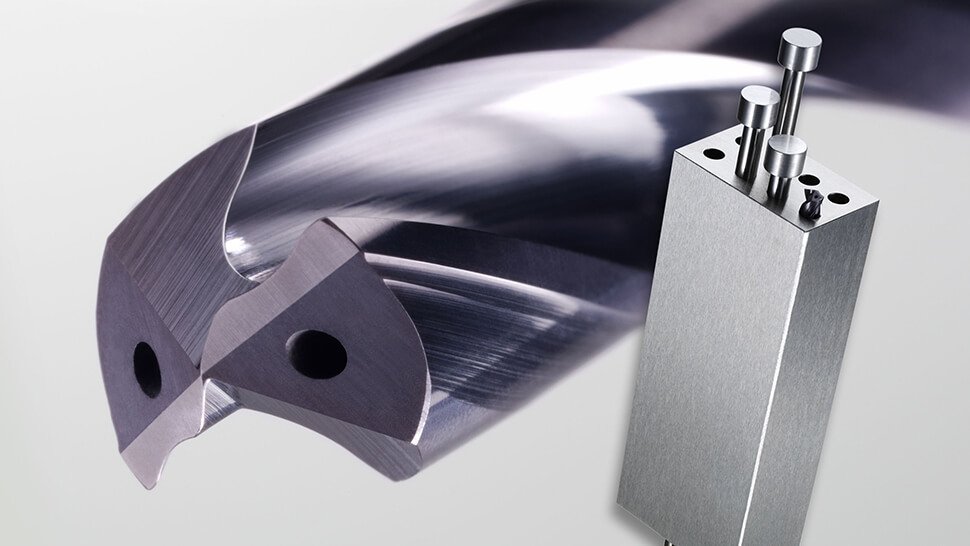
Tiefbohrer MHS. Foto: MMC
Dabei fährt das lange Tool in den Stahl als wäre es Butter. „Wenn der Span dabei aus dem Bohrloch spritzt, dann ist das Qualität“, freut sich Manfred Bartl, der das Hüller-Hille-Bearbeitungszentrum führt. Außer ihm haben 25 weitere Werker mit dem Tiefbohrer zu tun. Rund 30 Werkzeuge gehen jede Woche zum Nachschleifen und erneuten Beschichten in den Service. ZF in Passau arbeitet dreischichtig. Probleme beim Handling oder Qualitätsschwankungen sind nicht bekannt. Das mit 50 bar Kühlschmierstoffdruck beaufschlagte MMC-Tool arbeite doppelt so schnell wie herkömmliche Bohrer, sagt Bartl. Ob sich der Prozess noch weiter tunen lasse, ist einstweilen offen.
Auslegung hat auf Anhieb gepasst
Wilfried Dyduch, Anwendungstechniker bei MMC, hat das Tiefbohren vom Start weg begleitet. 2005 war 30xD das Maß aller Dinge und nicht entschieden, wer sich beim Tieflochbohren etablieren könnte: Im Wettbewerb standen sämtliche Hersteller mit Rang und Namen. Beharrliche Weiterentwicklung, Präsenz beim Kunden und schnelles Feedback zahlten sich letztlich aus. Jede zweite Woche, erzählt Dyduch, sei ZF-Passau-Termin. „Die Auslegungen haben auf Anhieb gepasst, die Abstimmung ist immer kompetent und gut“, bestätigt ZF-Planer Lang, „wir arbeiten hier im Werk mit jedem namhaften Hersteller. Wenn es um Tiefbohren geht, ist das MMC.“
Petra Reinhold ist bei MMC für das Technische Management zuständig. Sie fasst den großen Trend bei Tiefbohrtools zusammen: „Alle zehn Jahre werden sie 100 Millimeter länger. Im Frühjahr 2014 sind 490 Millimeter Gesamtlänge das Maximum.“ Der interne Kühlmitteldruck von 30, 50 und mittlerweile 70 bar mache ähnliche Sprünge. Hinzu kommt die Beschichtung. MMC setzt alles daran, auch bei schwankender Werkstoffqualität identische Bearbeitungsergebnisse möglich zu machen.
Kontakt | Autor
Wolfgang Filì
Freier Journalist
Köln
Tel. +49 221 8999196
E-Mail senden
Kontakt | Hersteller
MMC Hartmetall GmbH
European Commercial Marketing
Tel. +49 2159 9189-0
E-Mail senden
Kontakt | Anwender
ZF Friedrichshafen AG
Anzeige
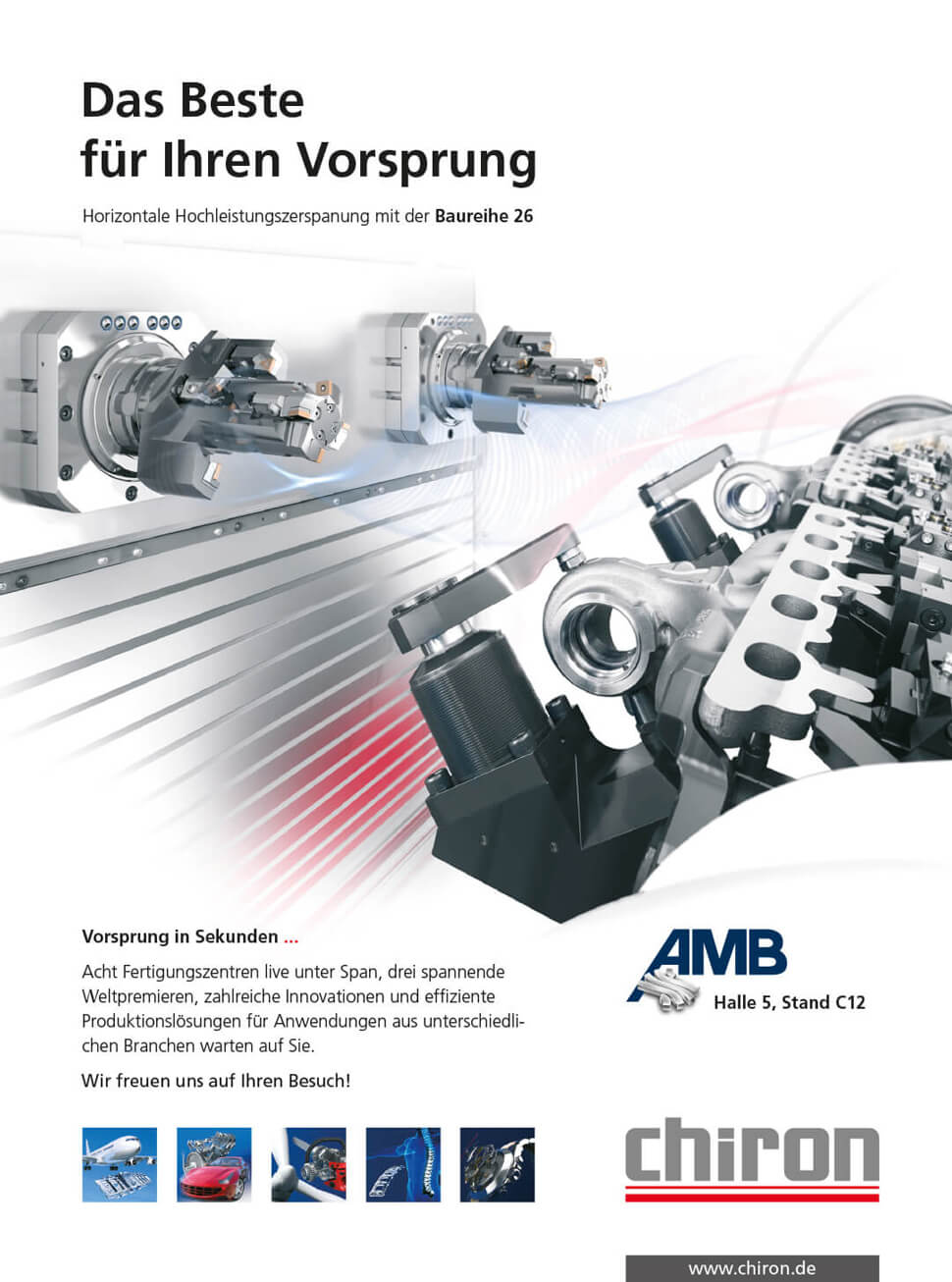