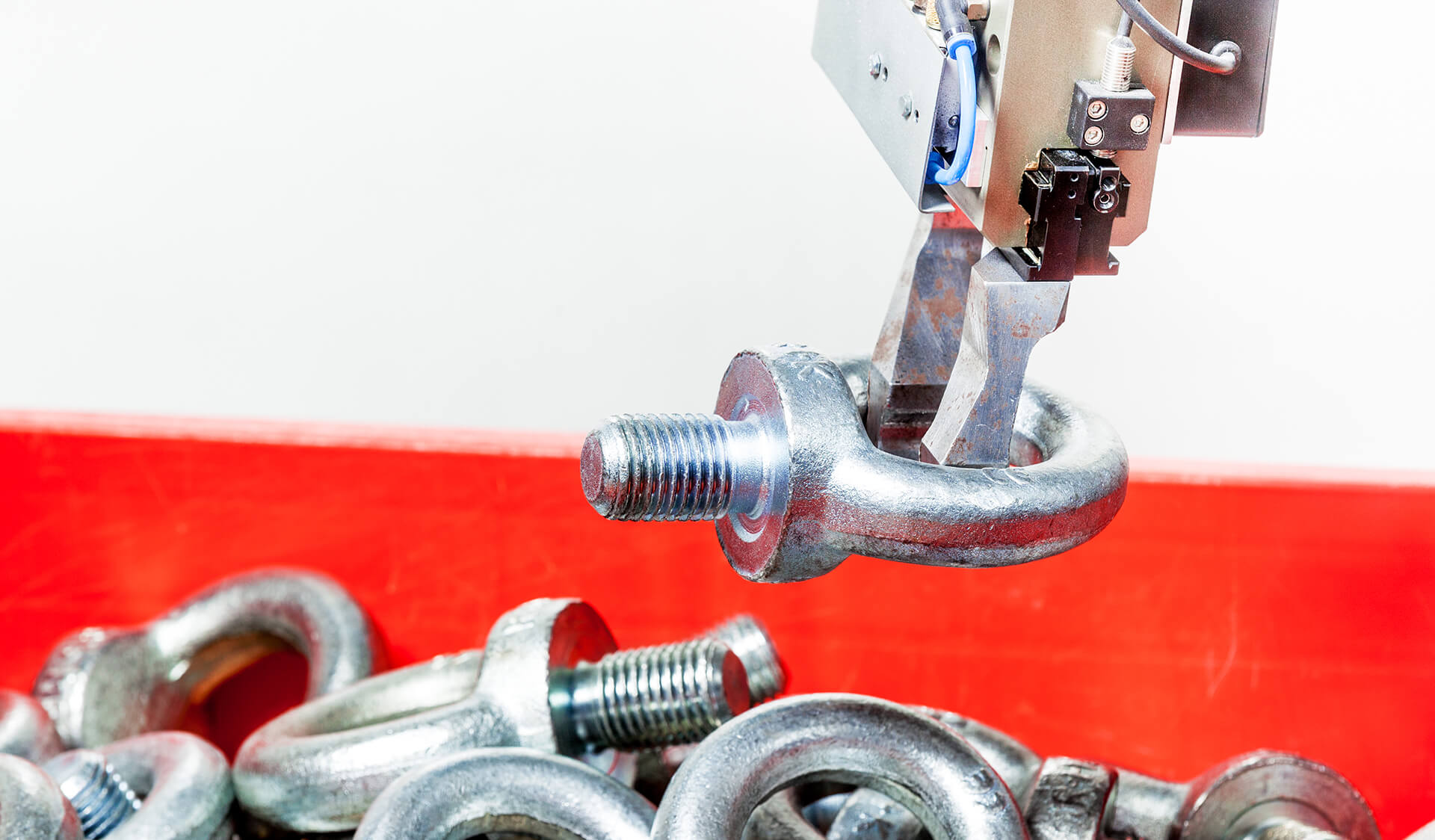
Titelthema
Der vernetzte Griff in die Kiste
Schnell und zuverlässig können künftig Roboter unsortierte Werkstücke aus Ladungsträgern entnehmen und gezielt ablegen. Jetzt haben die Experten des Fraunhofer-Instituts für Produktionstechnik und Automatisierung (IPA) eine Variante der Software bp3 entwickelt, mit der die Griff-in-die-Kiste-Lösung flexibler und effizienter einsetzbar ist: Das Programm steht als verteilte Anwendung über eine Cloud-Architektur bereit. So lässt es sich in Industrie-4.0-Architekturen integrieren.
In nahezu jeder Produktion fällt Schüttgut an, das auch bei einem hohen Automatisierungsgrad der Anlage oft noch von Hand oder mit komplizierten mechanischen Verfahren aus Ladungsträgern entnommen und abgelegt wird. Dies ist mitunter mit Gesundheitsrisiken für den Werker verbunden, zudem entstehen dem Unternehmen Kosten, weil bisherige automatisierte Lösungen oft zu langsam und nur schwer an neue Werkstücke anpassbar sind. Genau diese bisher fehlende Flexibilität eines automatisierten, roboterbasierenden „Griff-in-die-Kiste“ bei gleichzeitig sehr hoher Zuverlässigkeit und Verfügbarkeit bietet die industrieerprobte Software bp3 (BinPicking3D). Zusammen mit Systemintegratoren wurde die Software bereits in mehrere Produktionsanlagen eingebunden, wo sie im Dreischichtbetrieb im Einsatz ist.
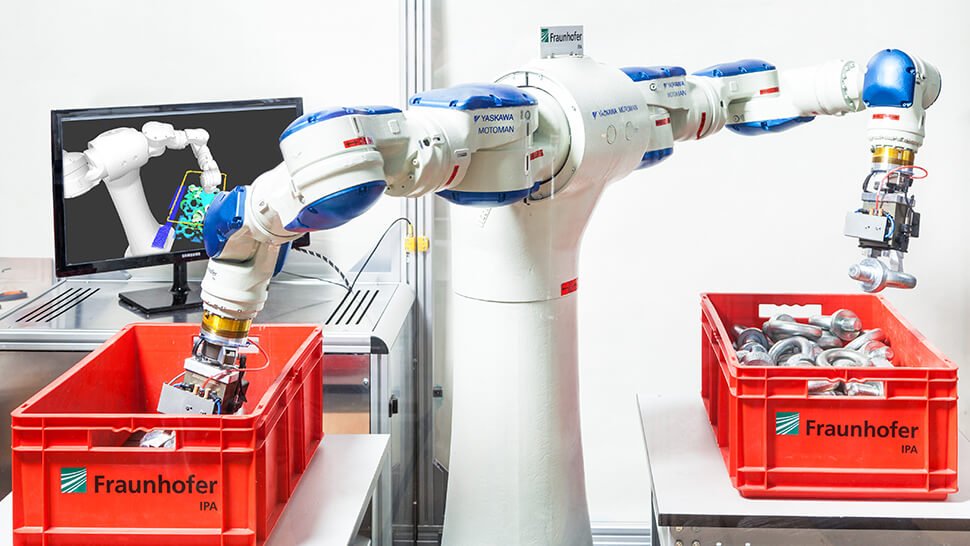
Der zweiarmige Roboter greift in die Kiste, um die Teile des Schüttguts zu vereinzeln. Die Software lässt sich mit unterschiedlichen Robotern und Sensoren verwenden. Auch zweiarmige Roboter werden unterstützt, um die Taktzeiten zu reduzieren und die Flexibilität des Vereinzelns zu erhöhen. Fotos: Fraunhofer IPA
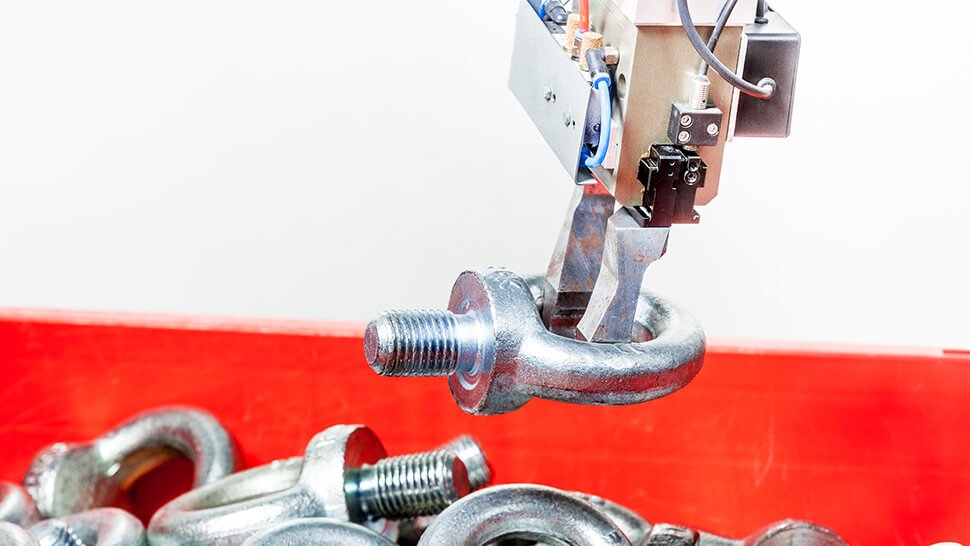
Um das Bauteil prozesssicher entnehmen zu können, verfügt die Software bp3 über eine kollisionsfreie Greifpunktbestimmung und Bahnplanung. Dadurch können Bauteile auch in schwierigen Positionen, beispielsweise am Kistenboden, sicher entnommen werden.
Komplettlösung aus einer Hand
Die Software zeichnet sich dadurch aus, dass sie sowohl die Lage der Objekte in der Kiste erkennen als auch die besten Greifpunkte sowie die Entnahme und damit die kollisionsfreie Bahn des Roboters berechnen kann. 3D-Sensoren über der Roboterzelle und ggf. an den Greifern ermöglichen eine schnelle und zuverlässige Objekterkennung. Sie erzeugen eine Punktwolke des Kisteninhalts und die Software gleicht diese mit eingelernten CAD-Daten der Werkstücke ab.
Ist ein Werkstück erkannt, ermittelt die Software die besten Greifpunkte und generiert die Roboterbahn zur Entnahme. Damit diese prozesssicher durchgeführt werden kann, simuliert die Software den Entnahmeprozess zunächst. Dabei werden neben dem Greifer und eventuellen Zusatzachsen auch die Kinematik des Roboters selbst sowie mögliche Schutzzäune im Umfeld berücksichtigt. Je nach Greifpunkten und möglicher Weiterverarbeitung des Werkstücks passt die Software auch die Roboterbahn für die Ablage an.
Das Fraunhofer-Institut für Produktionstechnik und Automatisierung (IPA) präsentiert die „Cloud Navigation“ anhand zweier mobiler Roboter während der Fachmesse Automatica vom 21. bis 24. Juni in München. Das Exponat ist Teil eines Messeauftritts des Instituts unter dem Motto „Automatisierung 4.0“. Die Experten zeigen mit Exponaten aus den Bereichen Mensch am Arbeitsplatz, Produkt und Automatisierung sowie IT-Infrastruktur und Vernetzung den Mehrwert einer im Sinne von Industrie 4.0 ausgerichteten Produktion.
Die Software lässt sich mit unterschiedlichen Sensoren konfigurieren, besitzt eine neutrale Schnittstelle zu praktisch allen Robotertypen und kann für unterschiedliche Produktgeometrien rasch konfiguriert werden. So kann diese Zuführlösung beispielsweise für Zerspanungsmaschinen wie auch für eine Vielzahl weiterer Produktionsszenarien eingesetzt werden.
Mehrwert der Cloud-Architektur
Eine Variante der Griff-in-die-Kiste-Lösung lässt sich bestens in vernetzte Produktionen integrieren, mit der Unternehmen besonders flexibel und zugleich wirtschaftlich fertigen können, so dass eine Produktion unter „Losgröße-1“-Bedingungen zunehmend machbar wird. In diesen Industrie-4.0-Szenarien agieren alle Betriebsmittel als mit Sensoren und Aktoren ausgestattete cyberphysische Systeme (CPS), die ständig Daten erzeugen und nutzen. Robotersysteme profitieren von zentraler Rechenleistung und Datenhaltung.
Der Roboter agiert dann lediglich als „Lean Client“, also als schlankes System. Die aufwendigeren Berechnungen zur Objekterkennung und Entnahmeplanung werden in einem zentralen Server durchgeführt. Dieser kann Anfragen verschiedener Roboter in kürzester Zeit bearbeiten, was die Taktzeit senkt. Zudem ist die Anlage besser wart- und verfügbar. Komponenten wie Sensoren, Greifer oder Roboter sind leichter austauschbar, wodurch die gesamte Produktion wandlungsfähiger wird. Mittels eines „Dienstekonzepts“, ähnlich einem „App-Store“, können auch neue Funktionen, die in der Cloud bereitstehen, wie eine verbesserte Objekterkennung schneller in die Anlage integriert werden. Der Endanwender muss gegebenenfalls nur noch bestimmte systemspezifische Parameter ergänzen, was den Integrationsaufwand deutlich reduziert.
Diese cloud-basierende Lösung ist besonders ökonomisch, wenn mehrere Roboter mit dem gleichen Datenbestand wie für die Werkstücke arbeiten. Die Daten müssen dann nur einmal zentral verfügbar sein oder geändert werden, und die Robotersysteme können bei Bedarf direkt darauf zugreifen. Weitere Dienste wie das Einlernen neuer Werkstücke oder die Inbetriebnahme der Anwendung bieten zusätzlichen Bedienkomfort und lassen sich einfach anbinden.
Integration auf „Virtual Fort Knox“
Die Werkstückdaten und ausführbaren Programme (Apps) stehen auf Plattformen bereit, die neben CPS einen weiteren Eckpfeiler von Industrie 4.0 bilden. Sie integrieren die unterschiedlichen CPS und verwalten Apps sowie Dienste zum Netzwerk- und Datenmanagement. Das Fraunhofer IPA bietet hier die speziell für produzierende Unternehmen entwickelte, besonders sichere und herstellerneutrale Plattform „Virtual Fort Knox“ an, durch die bp3 als Cloud-Dienst eingebunden werden kann. Sowohl die Sensoren zur Erfassung des Kisteninhalts als auch der Roboter kommunizieren per Ethernet mit dem Dienst, um im Zusammenspiel die Bauteile zu entnehmen. Über den offenen Manufacturing Service Bus (MSB) lassen sich die aktuellen Prozessdaten an jeden beliebigen Ort übertragen und dort visualisieren. Dadurch können die aktuellen Leistungsdaten mehrerer Anlagen effektiv überwacht werden, und es kann schnell auf Störungen reagiert werden.
Die Software kann über eine Lizenz genutzt und gleichermaßen für lokale Systeme wie auch für vernetzte Produktionen genutzt werden. Überdies unterstützen die IPA-Experten Unternehmen von der ersten Automatisierungspotenzial-Analyse über Machbarkeitsstudien, der Realisierung der Roboterzelle inklusive der Auswahl passender Komponenten wie Sensoren und Greifer bis hin zu Mitarbeiterschulungen.
Kontakt
Felix Spenrath
Projektleiter
Fraunhofer-Institut für Produktionstechnik und Automatisierung (IPA)
Stuttgart
Tel. +49 711-970 1037
E-Mail senden