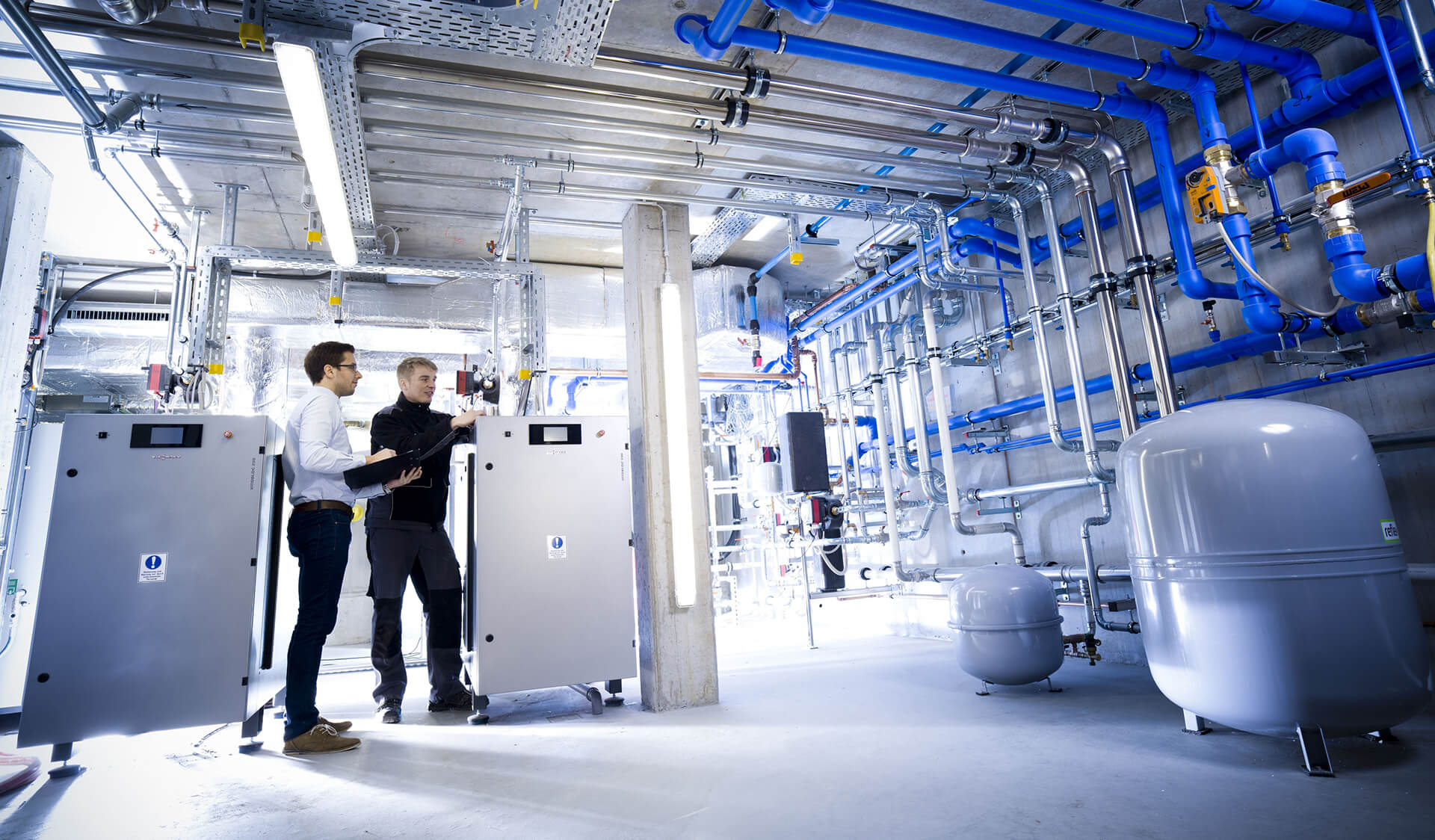
Messe
Energieeffizienz: Wärmelecks und Stromfresser im Visier
Gemeinsam mit Unternehmen geht die ETA-Fabrik der Technischen Universität Darmstadt ein zentrales Thema der EMO Hannover 2017 an: Wie lässt sich der Energieappetit von Werkzeugmaschinen im Zusammenspiel mit allen Systemen einer Fabrik erkennen und zügeln? Wie können Unternehmen dieses Anliegen konkret umsetzen? In Hannover werden konkrete Lösungen für die energieeffiziente Produktion von morgen vorgestellt.
Einen Herzenswunsch hat sich Prof. Eberhard Abele, Leiter des Instituts für Produktionsmanagement, Technologie und Werkzeugmaschinen (PTW) an der TU Darmstadt, erfüllt. Der Kybernetiker und promovierte Maschinenbauer aus Waldstetten (Kreis Schwäbisch Gmünd) hat nach 15 Jahren in der Industrie an der Technischen Universität eine Fabrik aufgebaut, um Studenten praxisnah auszubilden. Der umtriebige Schwabe aus dem Ostalbkreis gründete in Darmstadt 2007 die Prozesslernfabrik (CiP) und 2016 das Energieeffizienz,- Technologie- und Anwendungszentrum (ETA-Fabrik).
Energieeffizienz schulen und erforschen
Die Motivation liegt auf der Hand: Während CiP als Kompetenzzentrum für schlanke Produktion und Industrie 4.0 dient, soll in der ETA-Fabrik auf dem Gebiet Energieeffizienz geschult und geforscht werden. Sie soll als Lernfabrik dienen, mit deren Hilfe die TU auch das Thema Energieeffizienz in die Studiengänge für Maschinenbau- und Bauingenieure integrieren will. „Schon heutzutage werden Erstsemesterstudenten im Maschinenbau mit dem Potenzial für Energieeinsparung im Produktionsbetrieb konfrontiert. Sie finden zudem ein nahezu ideales Umfeld, um in Bachelor- oder Masterarbeiten ihre eigenen kreativen Ansätze für bessere Energieeffizienz zu erproben“, betont Abele.
Die ETA-Fabrik hilft vor allem als Großforschungslabor für industrielle Energieeffizienz der deutschen Regierung dabei, bis zum Jahr 2050 den Energieverbrauch im Vergleich zu 2008 zu reduzieren. Dabei spielt die Industrie eine Hauptrolle, verbraucht sie doch laut Bundesumweltamt fast ein Drittel der gesamten Energie in Deutschland. Grund genug für das Bundesministerium für Wirtschaft und Energie, für mehr als 30 Industriepartner und das Land Hessen, den Bau, die komplette Einrichtung und die langjährige Forschungsarbeit der ETA-Fabrik mit 15 Millionen Euro zu fördern.
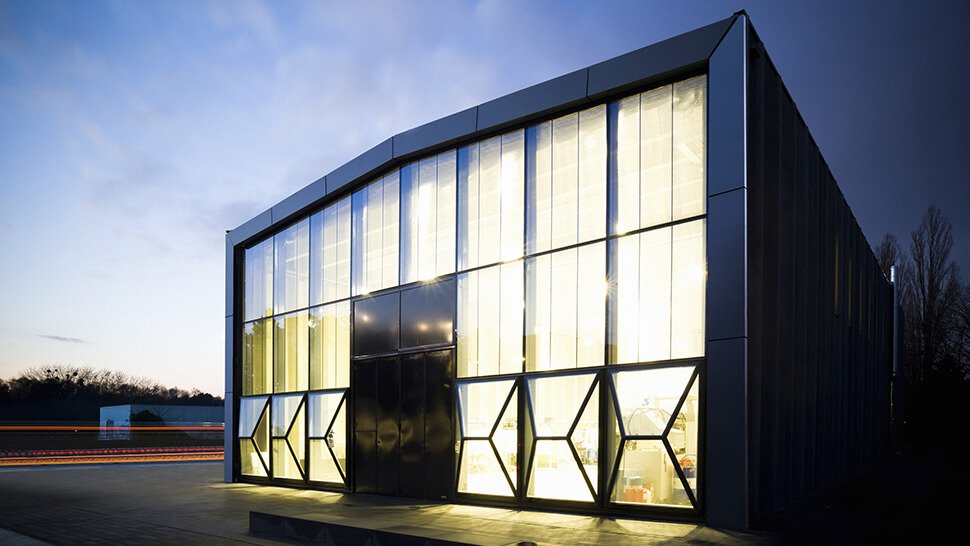
Großforschungslabor für industrielle Energieeffizienz: Die ETA-Fabrik unterstützt das ehrgeizige Ziel, bis zum Jahr 2050 den Energieverbrauch in Deutschland im Vergleich zu 2008 zu halbieren. Foto: PTW
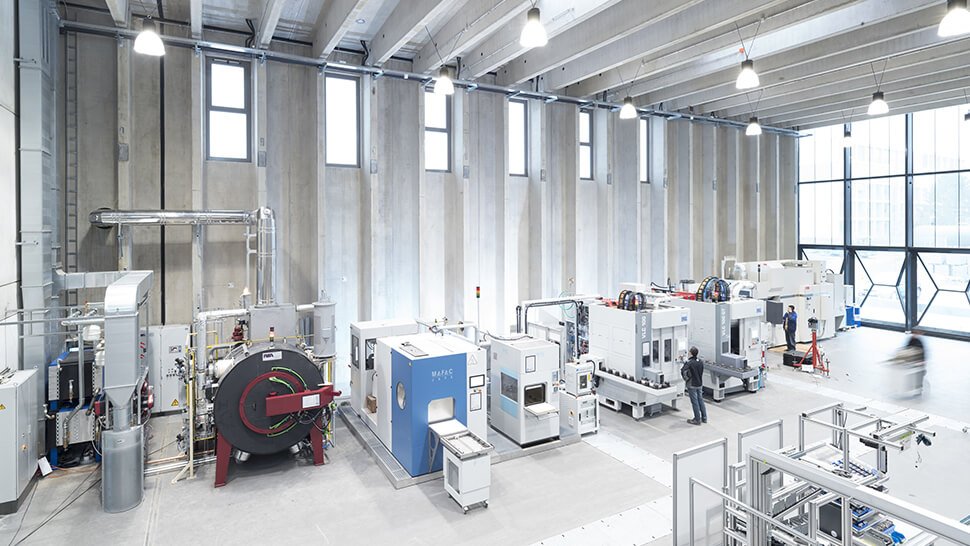
Spanende Forschung: Außer einem Lernfeld für Studenten und Mitarbeiter aus der Industrie besitzt die ETA-Fabrik eine Produktion für Pumpenkomponenten. Foto: PTW
Zusammenspiel aller Komponenten verbessern
Die ETA-Fabrik soll das Zusammenspiel aller Komponenten und Systeme einer Fabrik – von der Werkzeugmaschine bis hin zur Gebäudeausrüstung und -hülle – ganzheitlich verbessern, um den gesamten Energieverbrauch zu senken. Auf der Fläche eines typischen Hallenhandballfelds (800 Quadratmeter) gibt es außer einem Lernfeld für Studenten und Mitarbeiter aus der Industrie einen Maschinenpark mit Werkzeug- und Reinigungsmaschinen sowie einen Härteofen – ein Umfeld, in dem Komponenten für Pumpen (Steuerscheiben für Hydraulikaxialkolbenpumpen) entstehen: Die ETA-Fabrik umfasst alle Stufen der industriellen Fertigung, vom Roh- bis zum Fertigteil.
Die Produktion der Pumpenkomponenten ist nur Mittel zum Zweck, denn dort werden unter realen Bedingungen einer Metallbearbeitung neue Konzepte zum Energiesparen entwickelt. „Zum bisherigen Stand der Technik zählt, dass einzelne Komponenten für sich unter die Lupe genommen werden“, sagt der Institutsleiter, „wir wollen mit Maschinenbauern, Bauingenieuren und Architekten disziplinübergreifend Maschinenkomponenten, Produktionsmaschinen, Prozesskette, technische Gebäudeausrüstung und -hülle aus dem Blickwinkel Energieeffizienz analysieren und optimieren.“
„Wir analysieren und optimieren mit Maschinenbauern, Bauingenieuren und Architekten disziplinübergreifend Maschinenkomponenten, Produktionsmaschinen, Prozesskette, technische Gebäudeausrüstung und -hülle aus dem Blickwinkel Energieeffizienz.“ – Prof. Dr.-Ing. Eberhard Abele, </br> Leiter des Instituts für Produktionsmanagement, Technologie und Werkzeugmaschinen (PTW), TU Darmstadt
Neben der Weiterentwicklung von Fertigungsverfahren geht es um das Zusammenwirken des Fabrikgebäudes und seiner technischen Ausstattung mit dem Maschinenpark. Der rote Faden ist die mehrfache Vernetzung der einzelnen Bausteine der Fabrik: Ein Wärmenetz verbindet über Wasserrohre die Maschinen untereinander und mit der Gebäudehülle. Die von sehr kleinen Rohren durchzogene Fassade reagiert auf die Temperaturen der Außenwelt und passt sich an sie an, indem sie entweder das Wasser in den Rohren kühlt oder erhitzt. Unterstützung erhält sie beim Erhitzen der Halle über das Wärmenetz von der Abwärme der Maschinen. „Üblicherweise wird das zum Kühlen der Antriebselemente der Maschine eingesetzte Wasser ständig wieder gekühlt“, erläutert Abele, „das ist Energieverschwendung in Reinkultur. Wir kühlen nun nicht mehr den gesamten Wasservorrat, sondern erhitzen ihn sogar noch etwas, auf 80 Grad Celsius – zum Beispiel für die nachfolgende Reinigungsanlage für die Metallteile.“ Zum Kühlen der Antriebselemente nutzen die Maschinen kaltes Wasser aus der Wasserleitung.
Die ETA-Fabrik besitzt ein Datennetzwerk, das alle Bereiche miteinander verknüpft. „Wir kombinieren das Regeln des Energieverbrauchs mit Industrie 4.0“, betont der Darmstädter Wissenschaftler. Auf diese Weise lassen sich die erfassten und aufbereiteten Daten zum Optimieren des Energieverbrauchs nutzen.
Internationales Vorbild
Nicht nur in Deutschland stößt die neue Form auf Interesse, den Energieverbrauch mit Hilfe einer Forschungsfabrik zu senken. So berät Wirtschaftsingenieur Martin Beck, Gruppenleiter Umweltgerechte Produktion an der ETA-Fabrik, ein Unternehmen beim Aufbau einer energieeffizienten Maschinenfabrik in Singapur. Auch kleinen und mittleren Firmen aus Deutschland macht der Experte Mut, sich bei der ETA-Fabrik oder bei bereits bestehenden energieeffizienten Fabriken beraten zu lassen.
„Es lohnt sich besonders für Mittelständler, die in der Regel keine eigene Energieeffizienz-Abteilung besitzen“, betont Beck, „die Energiekosten machen drei bis fünf Prozent der Gesamtkosten aus, von denen wir durch gezielte, ganzheitliche, oft staatlich geförderte Beratung bis zu 40 Prozent einsparen können.“ Die Ausgaben für die sogenannten energieintensiven Unternehmen in Deutschland (EID) sind laut Verband in Bonn besonders hoch: Sie geben jedes Jahr mehr als fünf Prozent ihres Umsatzes (17 Milliarden Euro) für Energie aus.
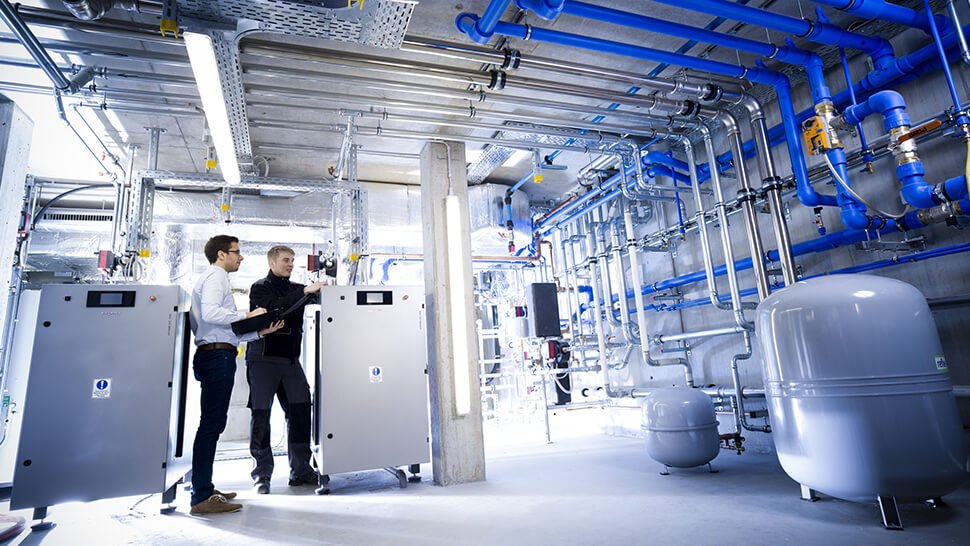
Optimierter Wärmehaushalt: Ein Wärmenetz verbindet über Wasserrohre die Maschinen untereinander und mit der Gebäudehülle. Foto: PTW
Die ETA-Fabrik dient darüber hinaus – so Informationen aus dem PTW – als „Großforschungsgerät“ für ehrgeizige Projekte. Dazu zählt das aktuell mit 30 Millionen Euro staatlich geförderte Kopernikus-Projekt „SynErgie – Synchronisierte und energieadaptive Produktionstechnik zur flexiblen Ausrichtung von Industrieprozessen auf eine fluktuierende Energieversorgung“. An dem Projekt beteiligten sich rund 100 Partner aus Industrie, Forschung und Gesellschaft, darunter IG Metall, Bund Naturschutz. Die Zielrichtung nennt Projektleiter Abele, der auch Präsident der Wissenschaftlichen Gesellschaft für Produktionstechnik (WGP) ist: „Wir vernetzen Windrad und Solarmodul mit der Produktionsmaschine.“ Alternative Energien wie Wind und Sonne produzieren meist entweder zu wenig oder zu viel Energie.
„Wir wollen die produzierenden Betriebe so flexibilisieren, dass sie selbst auf dieses schwankende Energieangebot reagieren können“, sagt PTW-Oberingenieur Stefan Seifermann. Ein wichtiges Unterfangen, betrug doch der Anteil der erneuerbaren Energien in Deutschland 2015 bereits 31 Prozent des Bruttostromverbrauchs.
„Wir wollen die produzierenden Betriebe so flexibilisieren, dass sie selbst auf das schwankende Energieangebot reagieren können.“ – PTW-Oberingenieur Stefan Seifermann
SynErgie startet zunächst mit sieben energieintensiven Branchen, zu denen auch der Maschinen- und Anlagenbau zählt. Die Anschlussleistung der einzelnen Betriebsmittel ist in dieser Branche zwar wesentlich kleiner, dafür kommen sehr viel mehr Maschinen und Anlagen als in anderen Industriezweigen zum Einsatz. Das Interesse aus dieser Branche ist groß, wie ein Blick auf die Teilnehmer zeigt: Unter Leitung von Prof. Matthias Putz vom Fraunhofer IWU aus Chemnitz arbeiten Unternehmen wie Bosch, Festo, Handtmann, Hirschvogel Automotive, Siemens und VW Sachsen zusammen.
Mittel zum Anpassungszweck sind hochdynamische Regelungsplattformen, die das schwankende Energieangebot berücksichtigen und die Energieverteilung zwischen Industrieprozessen wie Reinigen, Härten oder Metallbearbeitung regeln. „Nur wenn Unternehmen wissen, wann gerade sehr viel oder sehr wenig Strom aus erneuerbaren Energien erzeugt wird und die Börse das durch niedrige Strompreise signalisiert, können sie darauf reagieren“, sagt Abele.
Titelbild: PTW
Kontakt
Nikolaus Fecht
Technik-Texte à la carte - wenn Ihnen die Worte fehlen Gelsenkirchen Tel. +49 209 26575 E-Mail senden www.torial.com/nikolaus.fecht
VDW Verein Deutscher Werkzeugmaschinenfabriken
Sylke Becker Presse- und Öffentlichkeitsarbeit Frankfurt am Main Tel. +49 69 756081-33 E-Mail senden www.vdw.de
Bosch Rexroth AG
Susanne Herzlieb Corporate Communications DC/MKT3 Lohr am Main Tel. +49 9352 18-1573 E-Mail senden www.boschrexroth.com
Technische Universität Darmstadt
Institut für Produktionsmanagement, Technologie und Werkzeugmaschinen (PTW) Prof. Dr.-Ing. E. Abele Institutsleiter Darmstadt Tel. +49 6151 16 20080 E-Mail senden www.ptw.tu-darmstadt.de
Anzeige
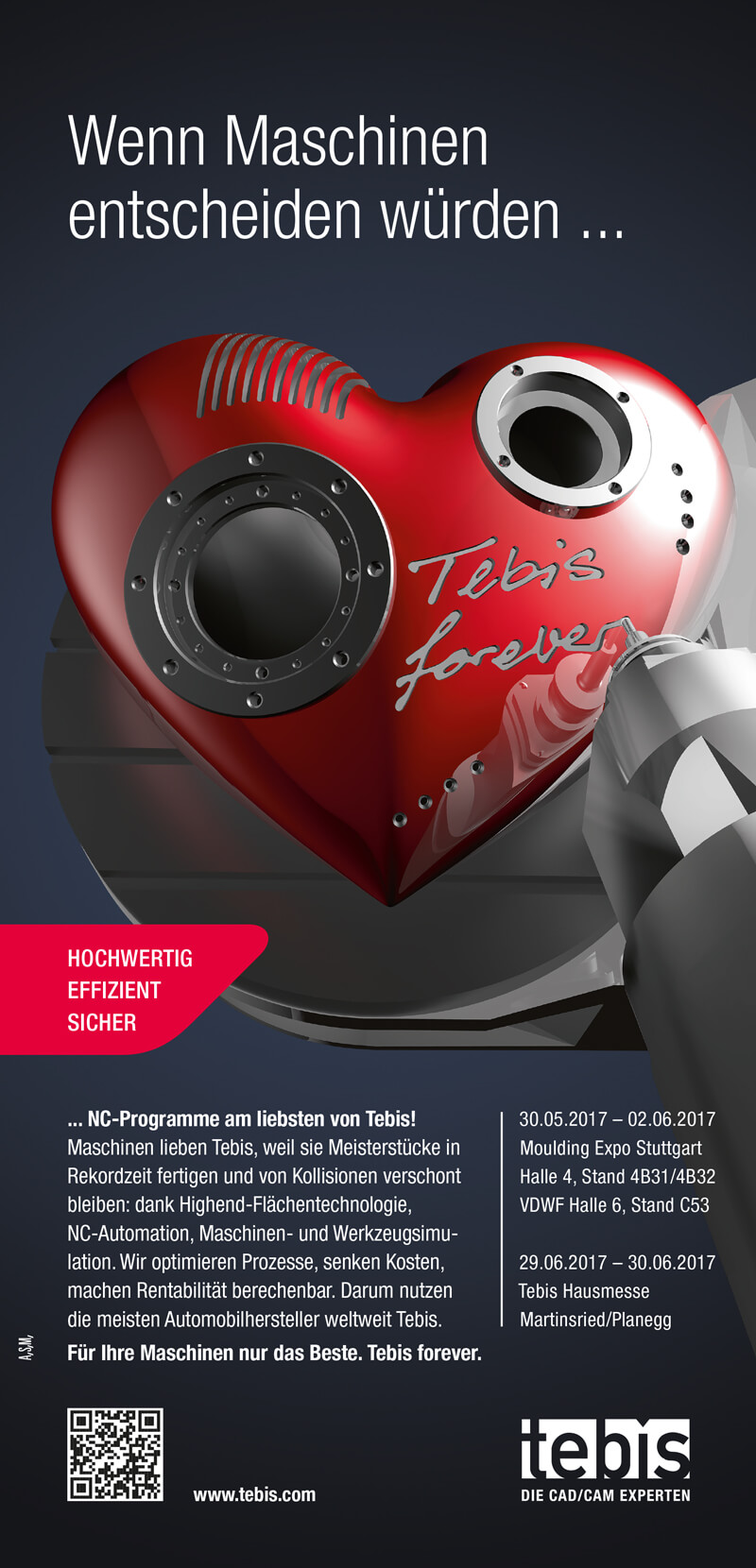