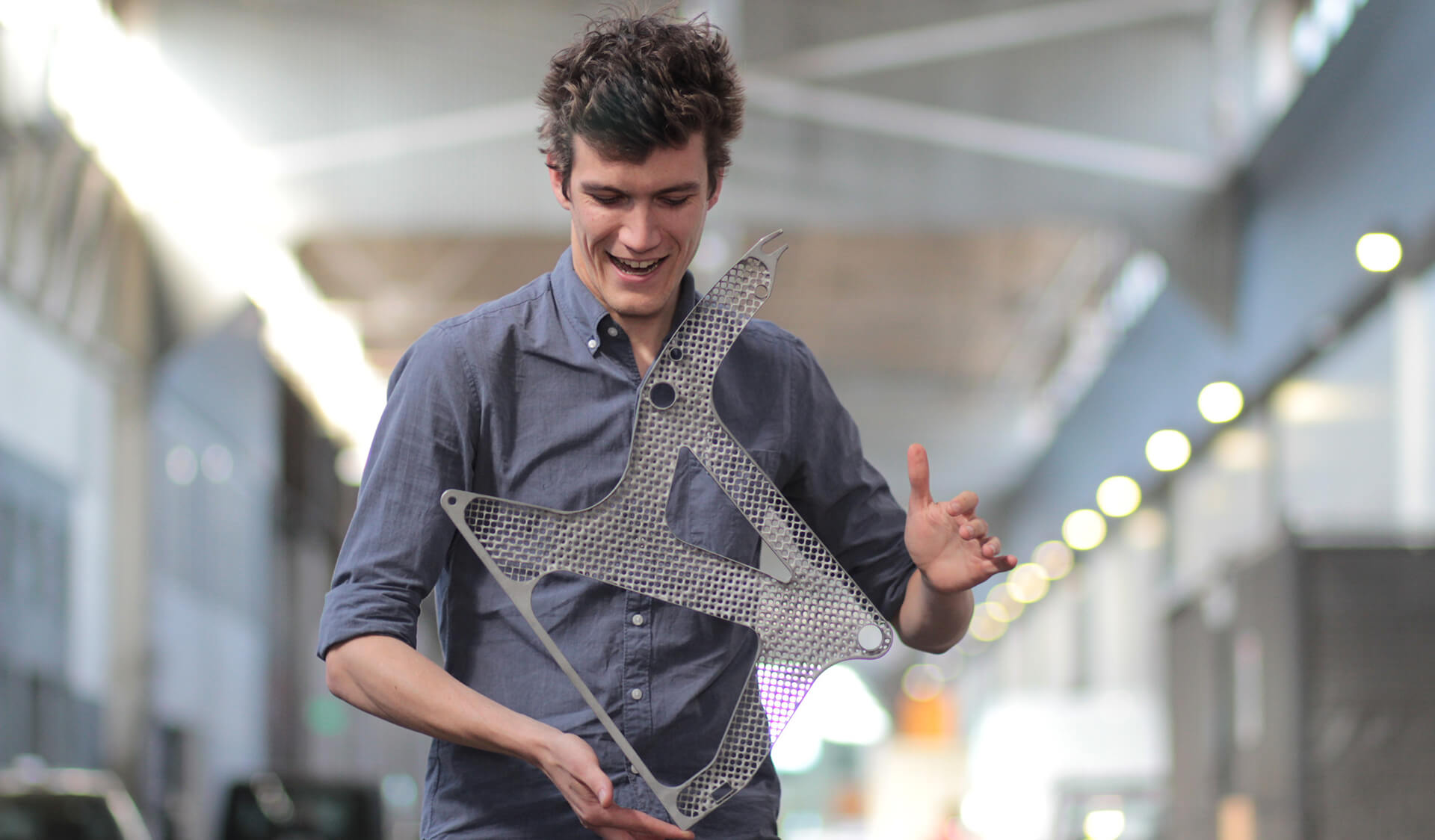
Additive Fertigung
Generatives Design
macht Flugzeuge leichter
Generatives Design und 3D-Druck sind für etliche Unternehmen Neuland. Viele Anwender warten, bis additive Fertigungstechnologien weiter ausgereift sind. Dafür gibt es praktische Gründe, aber dann wird auch wertvolle Zeit verschenkt, um die neue Technologie zu nutzen. Besonders effektiv ist der Einstieg in die additive Fertigung mit Hilfe einer Konstruktionssoftware, die für Metallguss und additive Fertigung geeignet ist. Metallguss und 3D-Druck entfalten in Kombination ihr optimales Potenzial. Ein mit Hilfe von Autodesk generativ gestalteter Leichtbau-Sitzrahmen für Verkehrsflugzeuge ist ein innovatives Anwendungsbeispiel für die Kombination aus bekannter Fertigungsmethode und generativem Design sowie industriellem 3D-Druck. Das Verfahren wurde in Verbindung mit klassischem Metallguss erstmals in der Serienfertigung eingesetzt.
Es gibt durchaus praktische Gründe, mit dem Einstieg in die additive Fertigung zu warten. So können Hersteller bei der additiven Metallfertigung in der Regel auf weniger als ein Dutzend verfügbare Materialien zurückgreifen. Beim klassischen Metallguss stehen ihnen dagegen Hunderte verschiedener Legierungen zur Verfügung. Darüber hinaus lassen sich im Metallguss riesige Bauteile anfertigen, während Metalldrucker eher auf kleine Teile beschränkt sind.
Ein weiterer gewichtiger Faktor ist der mit dem Fertigungsverfahren verbundene Kosten- und Zeitaufwand. Anlagen für direktes Laserschmelzen sind äußerst kostspielig und die produzierten Bauteile erfordern ein hohes Maß an Nachbearbeitung. Auch die Zertifizierung von 3D-gedruckten Teilen ist schwierig. Der Metallguss hingegen ist ein erforschter und bewährter Prozess. Trotz Vorteilen additiver Fertigung wie der Möglichkeit zur Herstellung besonders komplexer Strukturen lässt sich im klassischen Metallgussverfahren in vielen Fällen eine Menge Zeit und Geld sparen.
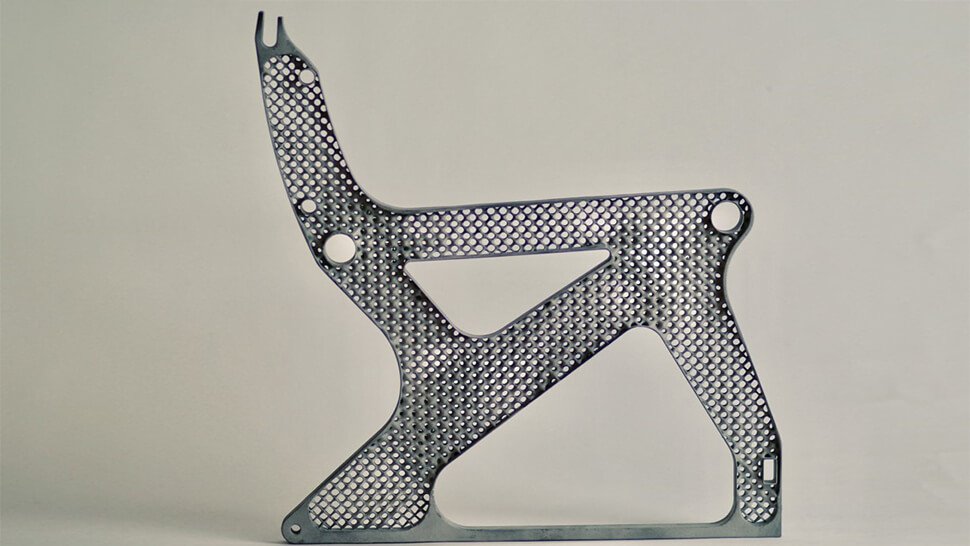
Fotos: Autodesk
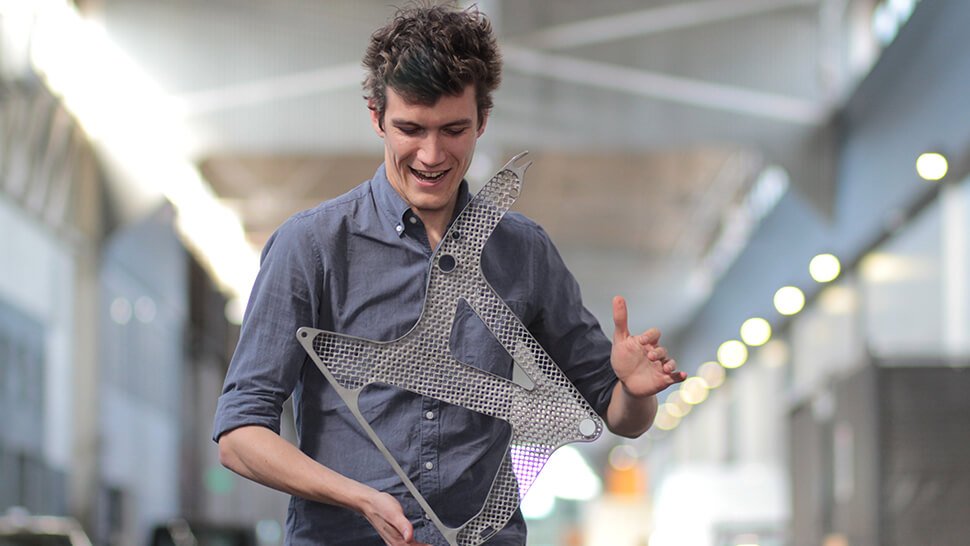
3D-Druck der Gussform
In Kombination entfalten Metallguss und additive Fertigung ihr volles Potenzial. Mithilfe von generativem Design und digitaler Optimierung können Hochleistungsstrukturen per spezialisierter Software entworfen werden, die durch eine metallfreie additive Fertigung zunächst als Gussform umgesetzt werden. Anschließend sorgen moderne Gießverfahren unter Verwendung des passenden Metallmaterials für die endgültige Form.
Ein eindrucksvolles Beispiel für die wirksame Kombination beider Verfahren ist ein im Autodesk Pier 9 Technologiezentrum in San Francisco entwickelter, generativ gestalteter Leichtbau-Sitzrahmen für Verkehrsflugzeuge. Das Projekt vereint klassische Fertigungsmethoden und moderne Technologien wie generatives Design und industriellen 3D-Druck.
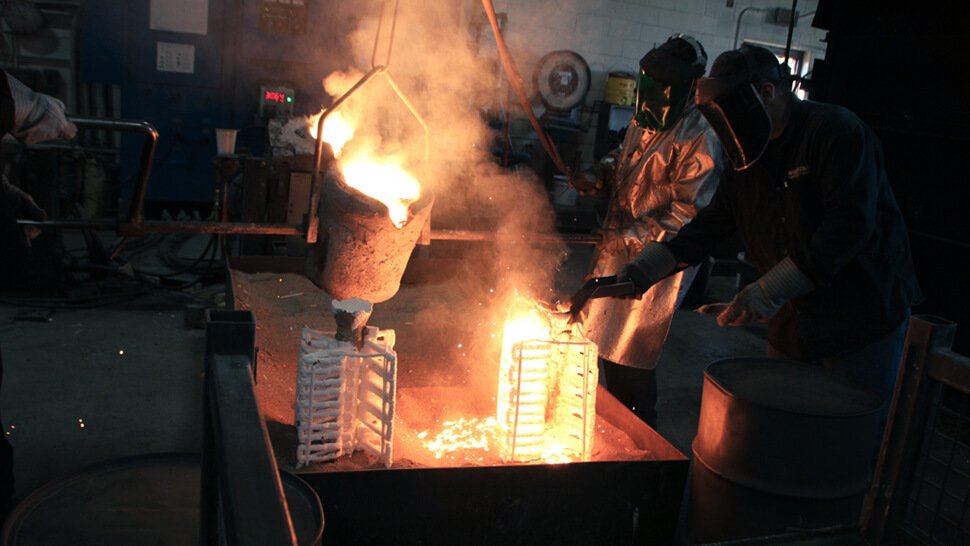
Foto: Autodesk
Der aus Magnesium gefertigte Sitzrahmen beruht auf einem durch einen Software-Algorithmus in Autodesk Netfabb generativ entwickelten Entwurf. Die Serienproduktion des Bauteils erfolgt in einem hybriden Fertigungsverfahren aus 3D-Druck und klassischem Metallgussverfahren. Dabei druckt das verantwortliche Team zunächst ein Kunststoffmodell des Sitzgestells, das dann mit Keramik überzogen wird.
Anschließend kann der Kunststoffanteil weggeschmolzen und flüssiges Magnesium in die so entstandene Keramikform gegossen werden. Das Ergebnis ist ein Sitzgestell, das aufgrund des verwendeten Materials und der generativ erzeugten Gitterstruktur 56 Prozent leichter ist als derzeit im Flugzeugbau gängige Modelle. In der Luftfahrt zählt jedes Gramm. Eine Halbierung des Gewichts kommt einer Revolution gleich. Würde man einen 615 Sitzplatz starken Airbus A380 mit Sitzen dieser Art ausstatten, ließen sich innerhalb eines Jahres Treibstoffkosten in Höhe von 100.000 US-Dollar sparen.
Das Projekt räumt dabei mit dem Mythos auf, die Herstellung von Bauteilen per Metallguss dauere rund anderthalb Jahre. Tatsächlich benötigt ein Unternehmen im beschriebenen Verfahren lediglich zwei Tage für die Herstellung des Endprodukts – weniger Zeit sogar, als dies in vielen Fällen mit Metalldruck der Fall wäre.
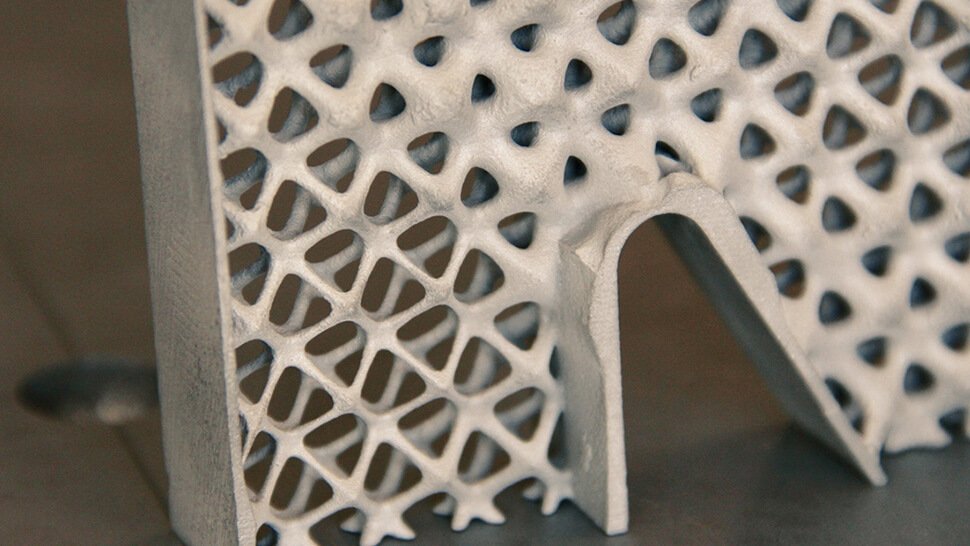
Foto: Autodesk
Feinguss-Verfahren und generatives Design
Das spezielle Gieß- und Ausschmelzverfahren erlaubt Detailtreue im Submillimeterbereich. Schon ein Fingerabdruck auf dem Modell wäre später auf dem Endprodukt sichtbar. Für die Luftfahrtindustrie bietet diese Herangehensweise ungeahnte Möglichkeiten – und kann damit langfristig enorme Mengen an Kerosin, CO2 und Kosten einsparen.
In einem Airbus A380 bedeutet die Verwendung der Sitzrahmen eine Gewichtsersparnis von 557 Kilogramm, was pro Jahr und Flugzeug 63 Tonnen Kerosin und 190 Tonnen Kohlendioxid einspart. Umgerechnet auf eine Flotte von 100 Flugzeugen und eine Zeit von 20 Jahren sind das 126.000 Tonnen CO2 – und damit mehr als 200 Millionen Dollar Treibstoffkosten.
Kontakt
Karl Osti
Industry Manager Manufacturing Autodesk GmbH München
André Pechmann
Communications Manager Germany Autodesk GmbH München Tel. +49 89 547 69 347 E-Mail senden