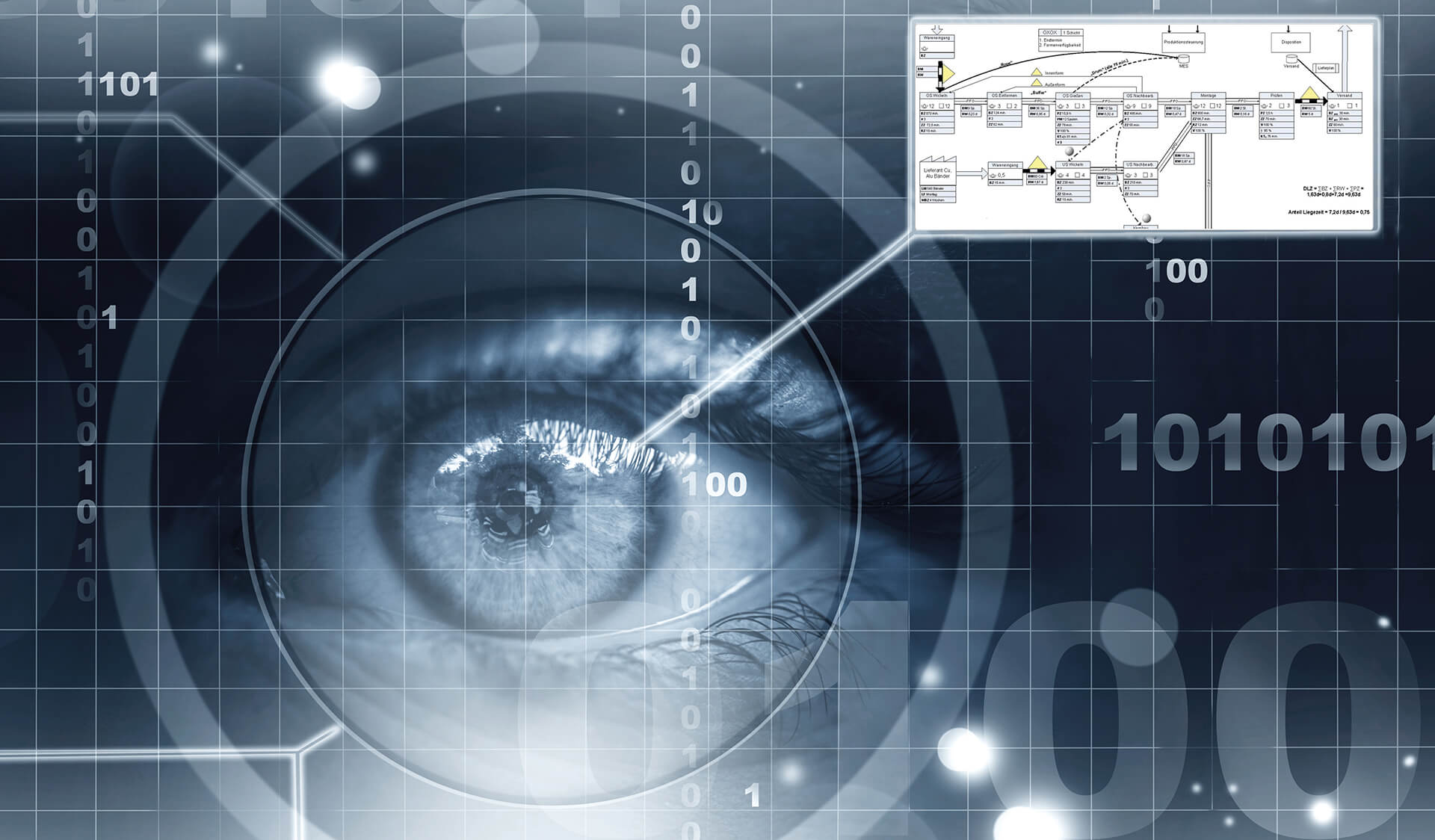
Management
Lean Factory Design:
Den Wertstrom im Blick
Studien zeigen, dass im Produktionsbetrieb nur noch 20 Prozent der Prozesskosten mit vergleichsweise hohem Aufwand beeinflussbar sind. Idealerweise muss die Optimierung also in der Planungsphase ansetzen. Gerade im Mittelstand wird dieses Potenzial nur unzureichend genutzt. Häufig werden scheinbare Verbesserungsmaßnahmen zu schnell umgesetzt, ohne dass die eigentlichen Problemursachen identifiziert wurden. Mit Lean Factory Design (LFD) bietet die Pull Beratung GmbH mittelständischen Fertigungsunternehmen einen ganzheitlichen Ansatz, um ihre Produktion und Logistik schlanker und wettbewerbsfähiger aufzustellen. Immer im Blick: Der Wertstrom.
Optimierungsprojekte und Lean-Einführungen in Unternehmen scheitern oder bringen nicht die erwarteten Ergebnisse. Die Gründe dafür sind vielfältig. Zum einen mag der Misserfolg daran liegen, dass Lean nicht im Sinne einer wissenschaftlichen Theorie systematisch dokumentiert vorliegt. Weil dadurch die Basis für ein Wissensmanagement fehlt, ist es erfahrungsgemäß schwierig, die Projektbeteiligten in ihrer Denkweise und im Methodeneinsatz auf einen gemeinsamen Stand zu bringen. Um dieses Problem zu beheben, wäre ein „Lean-Produktionssystem“ nötig, doch den Zeit- und know-how-intensiven Aufbau eines derartigen Methodenbaukastens können viele Mittelständler selbst nicht leisten.
Punktuelle, von nur einzelnen Fachabteilungen vorangetriebene Verbesserungsmaßnahmen sind ein häufiges Phänomen. Sie erweisen sich jedoch oft als ein weiteres Manko, weil sie ohne das notwendige interdisziplinäre Verständnis für das gesamte System angegangen werden. Es kommen Methoden in Kombination zum Einsatz, die zu widersprüchlichen Ergebnissen führen, nicht mit dem Lean-Gedanken kompatibel sind und dadurch unlösbar erscheinende Zielkonflikte, meist an Abteilungsgrenzen, erzeugen.
Viele Optimierungsprojekte werden im laufenden Serienbetrieb durchgeführt. In diesen Fällen kann eine Vielzahl von Restriktionen das erwartete Ergebnis negativ beeinflussen. Faktoren wie vorhandene Platzverhältnisse, bereits beschaffte Werkzeuge und Maschinen, für Prozesse erteilte Kundenfreigaben sowie Zertifizierungen, eingefahrene Abläufe und vieles mehr erschweren Veränderungen. Studien zeigen, dass im laufenden Betrieb nur noch ein Fünftel der Kosten bei hohem Änderungsaufwand beeinflussbar sind. Der große Hebel zur Optimierung liegt also in der Planungsphase, vorm Produktionsbeginn. Gerade im Mittelstand wird dieses Potenzial jedoch aufgrund fehlender Planungskapazitäten nur unzureichend genutzt.
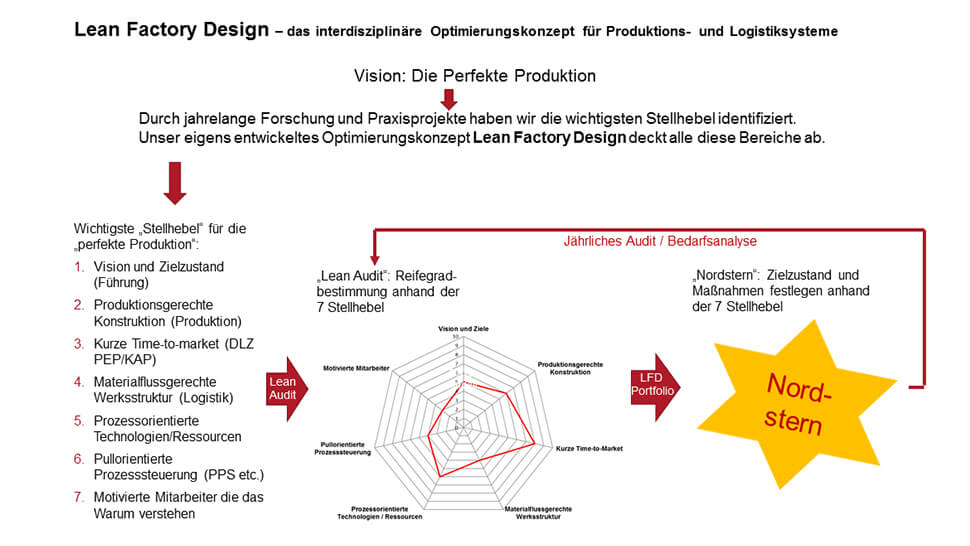
Quelle: Pull Beratung
Den Kern dieses Ansatzes bildet das Landshuter Produktionssystem. Darin werden etwa 100 Lean-Prinzipien und die notwendigen Methoden systematisch und in sich schlüssig aufeinander aufgebaut. Dies ist die Basis für ein Wissensmanagement und dient den Planern als Leitplanke bei ihrem Handeln. Das Landshuter Produktionssystem kann mittelständischen Unternehmen als Vorbild zur Ableitung eines eigenen Lean-Produktionssystems dienen.
LFD betrachtet immer eine komplette Fabrik vom Wareneingang bis Warenausgang mit allen ablaufenden Wertströmen für Kundenprodukte. Diese werden ganzheitlich aus den drei Dimensionen Prozess, Technik und Mensch beleuchtet. Das Konzept ist bewusst interdisziplinär gestaltet und hilft, vielfach vorhandene Zielkonflikte zwischen Produktion und Logistik, auch Einkauf, technischer Entwicklung, IT und vor allem dem Controlling aufzulösen und die gesamte Fabrik zielgerichtet in eine Richtung zu entwickeln.
Der Begriff Design steht dafür, dass LFD den gesamten Lebenszyklus einer Fabrik umfasst und bewusst auf die Phase der Gestaltung und Planung vor Produktionsbeginn fokussiert, denn hier können 70 bis 80 Prozent der späteren Kosten bei vergleichsweise geringem Aufwand beeinflusst werden. Design bedeutet auch das bewusste Gestalten des Systems. Dabei wird das umfassende Wissen um die richtigen Stellhebel zur Produktionsoptimierung, die häufig nur indirekt in einem Gesamtsystem wirken, vorausgesetzt.
Zu Beginn eines Optimierungsprojekts misst ein speziell entwickeltes Lean-Audit-System den Lean-Reifegrad einer Organisation in Bezug auf die sieben Stellhebel. In Form einer Begehung wird ermittelt, wie effizient die Prozesse im Unternehmen aktuell ablaufen, ob und wie die wichtigsten Stellhebel zur Produktionsoptimierung genutzt werden und in welchen Bereichen bislang unentdeckte Potenziale schlummern. Zur Standortbestimmung wird zudem ein Vergleich mit anderen Unternehmen gezogen.
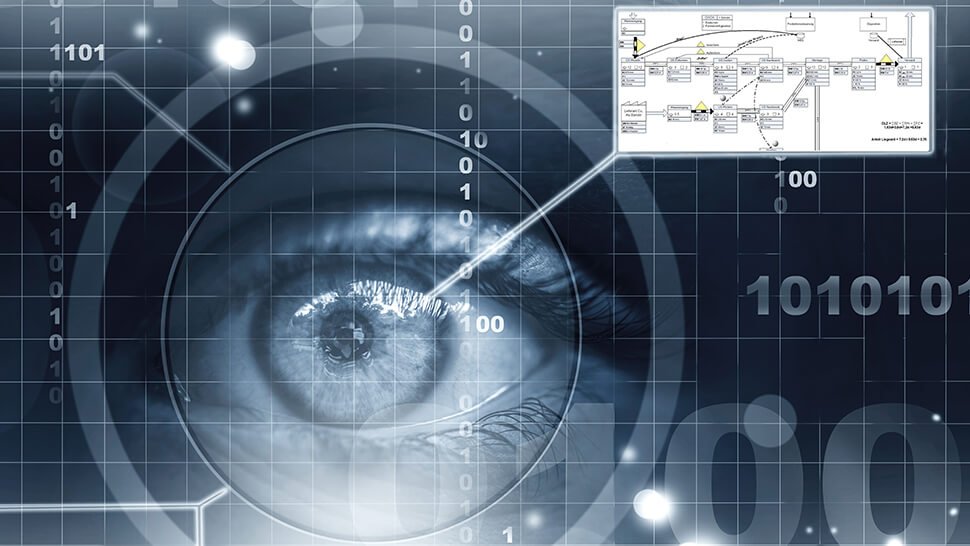
Foto: Pull Beratung/iStockphoto
Das Management wird im Rahmen eines Nordstern-Workshops eingebunden. Die aufgedeckten Potenziale im Lean Audit bieten eine zielführende Orientierung (wie der Nordstern), worauf aus Unternehmenssicht in der nächsten Planungsperiode zu fokussieren ist. Die zur Erreichung dieser Zielvorgaben notwendigen Maßnahmen werden mit dem Methodenbaukasten des LFD geplant und umgesetzt. Dieser ist so konzipiert, dass er einerseits alle sieben Stellhebel der Produktionsoptimierung berücksichtigt, andererseits nur Methoden und Werkzeuge enthält, die auf ihre Lean-Kompatibilität geprüft und gegebenenfalls weiterentwickelt wurden. Der Grundaufbau orientiert sich an den drei Dimensionen eines Unternehmens als sozio-technisches System: Prozess, Technik und Mensch.
Ausgangspunkt eines Optimierungsprojekts bildet meist die wertstromorientierte Materialflussplanung. Hier werden Lean-Methoden wie das Wertstromdesign mit ausgewählten Vorgehensweisen der klassischen Fabrikplanung und einer Fabrikplanungssoftware kombiniert. Der Kunde erhält einen Masterplan je Standort in Form von 2D-Layout, Wertstrom und Maßnahmenplan für mehrere Jahre in die Zukunft. Ein Masterplan hilft sicherzustellen, dass die hohen Investitionen in Gebäude und Infrastruktur langfristig richtig ausgerichtet sind.
Dieser top-down-orientierte Ansatz wird im so genannten Gegenstromverfahren mit einer bottom-up-orientierten Lean-Produktionsoptimierung kombiniert. Es wird zwiebelscheibenartig vom Arbeitsplatz nach außen optimiert. Während der Masterplan die langfristige Orientierung sicherstellen soll, bringt der Bottom-up-Ansatz direkt und kurzfristig spürbare Erfolge.
Eine besondere Herausforderung bei jedem Veränderungsprojekt stellt die Dimension Mensch dar. Schließlich hilft der beste Plan nichts, wenn die Mitarbeiter die Ideen nicht annehmen, das Warum nicht verstehen und die Prozesse nicht leben.
LFD enthält ein zielgruppenspezifisches Schulungskonzept, das mit dem Prozessoptimierungsablauf abgestimmt ist und neben den Lean-Methoden auch Themen wie Führen vor Ort oder Shopfloormanagement abdeckt.
Kontakt
Prof. Dr. Markus Schneider
PuLL Beratung GmbH
Landshut
Tel. +49 871 95347394
E-Mail senden