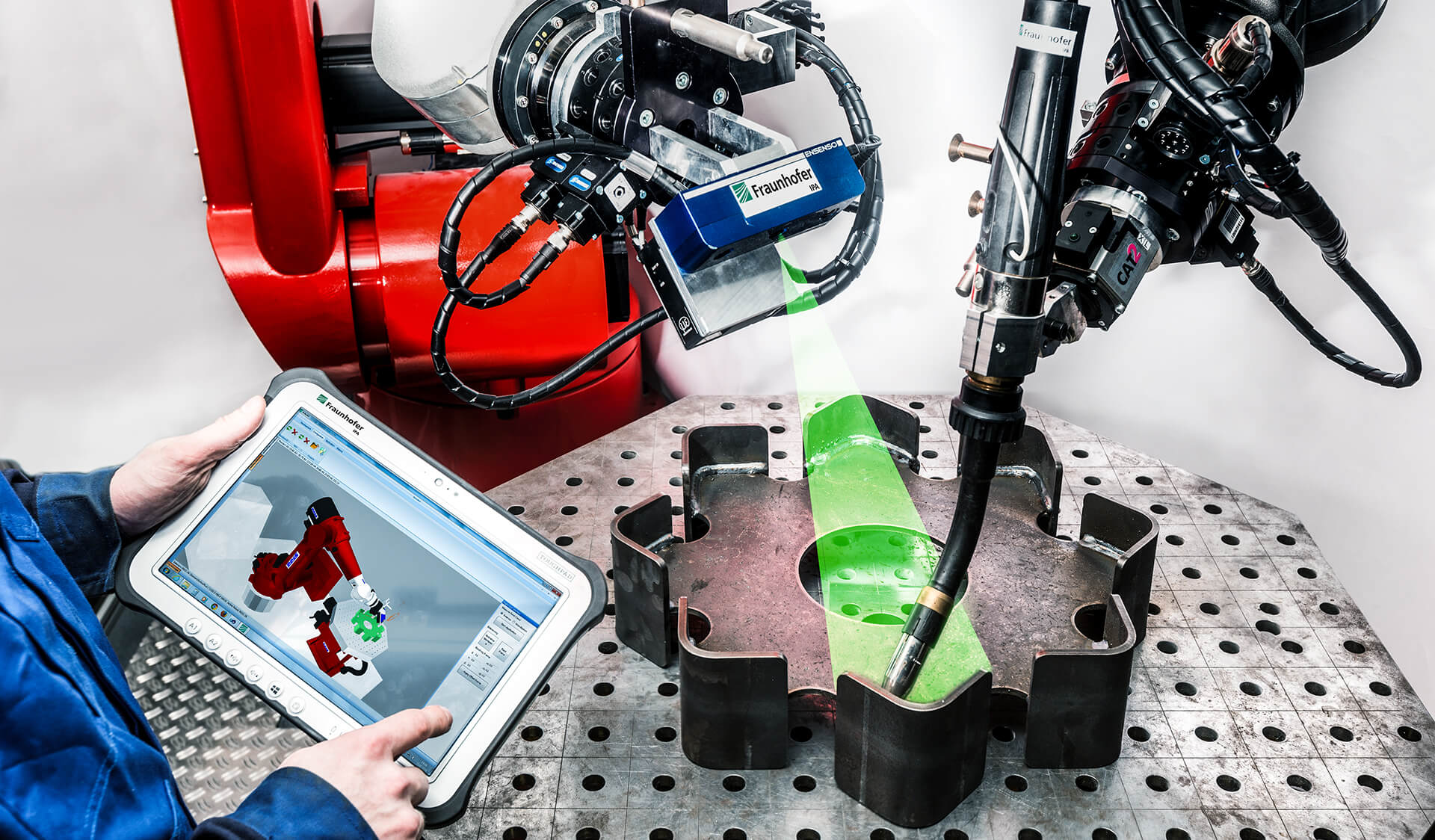
Automatisierung
Technologieschub
für die Robotik
Stellt eine Automatisierungslösung technisch ambitionierte Anforderungen an Roboter, hilft das EU-Projekt Robott-Net: In mehr als 70 Kooperationen unterstützen die Projektpartner Unternehmen von der Beratung bis zur Umsetzung innovativer Robotiktechnologien, die eine hohe wirtschaftliche Auswirkung versprechen. Die Lösungen stehen außerhalb des Projekts zum Praxiseinsatz bereit.
Eine nachhaltige europäische Infrastruktur für die Entwicklung von Roboterlösungen insbesondere für den Mittelstand zu schaffen, ist das Ziel von Robott-Net. Das Projekt hilft von der Technologieberatung über passende Geschäftsmodelle bis hin zur Realisierung von Demonstratoren. Im Fokus: der Transfer von Forschungsergebnissen in die Praxis. Hierfür sind neben der Technologie weitere Faktoren entscheidend. Dazu zählen die Robustheit und Verlässlichkeit der Lösung auch unter Produktionsbedingungen, ein überzeugendes Geschäftsmodell, Sicherheitsaspekte, Nutzerfreundlichkeit, Integrationsfähigkeit in bestehende Abläufe und nicht zuletzt eine sehr gute Performanz.
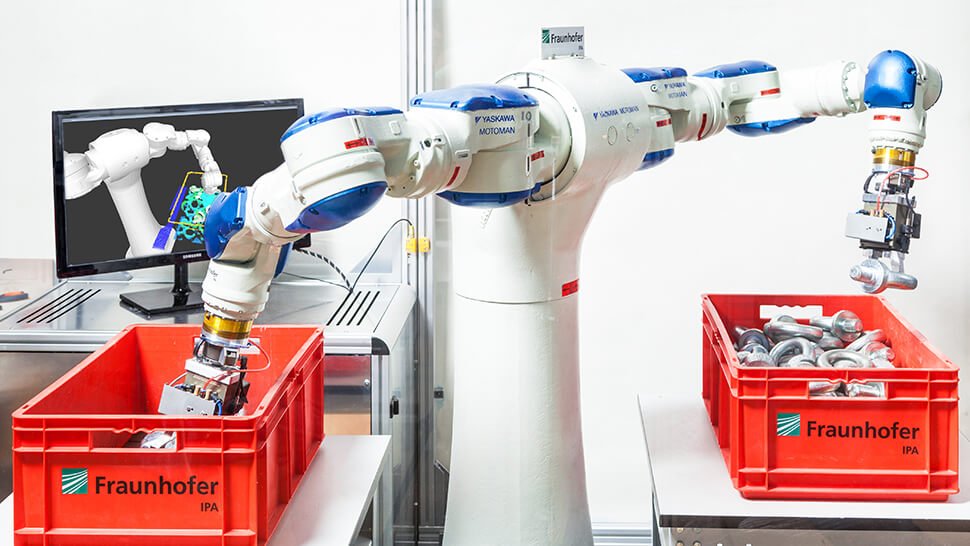
Die Software für den Griff-in-die-Kiste ermöglicht das Vereinzeln ungeordnet vorliegender Werkstücke durch den Roboter. Fotos: Rainer Bez/Fraunhofer IPA
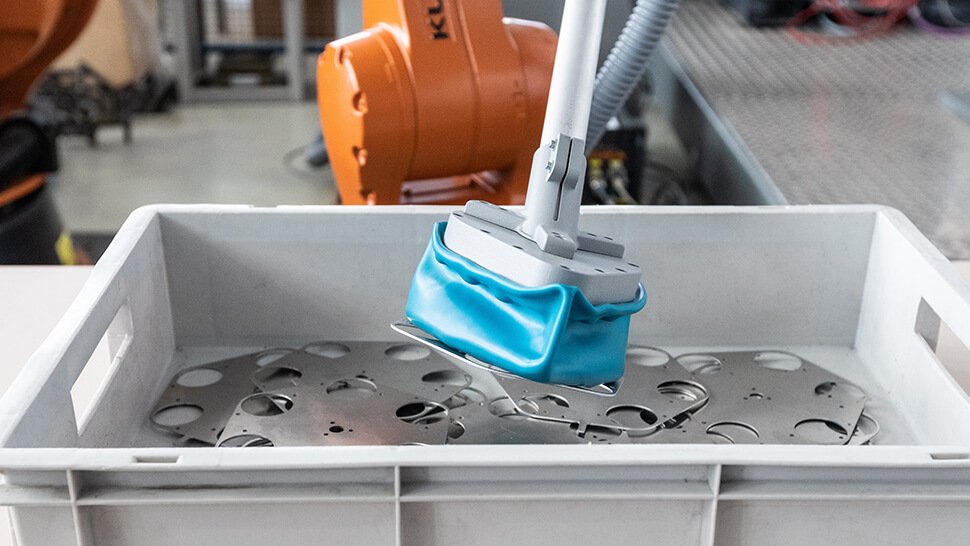
Zur passgenauen Griff-in-die-Kiste-Anwendung kann auch die Entwicklung eines spezifischen Greifers gehören, der genau auf die Werkstücke abgestimmt ist.
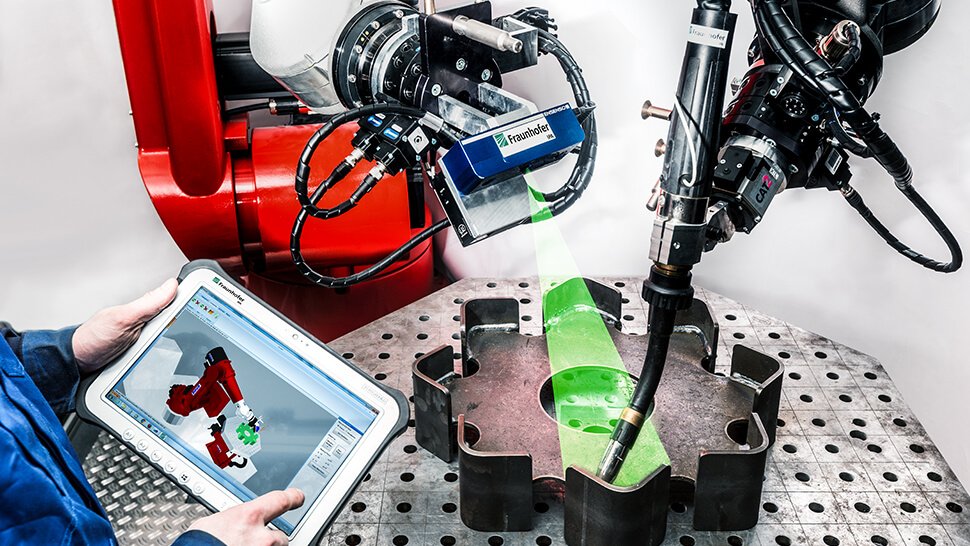
Die Software für Schweißroboter erkennt das Bauteil automatisch und erzeugt daraufhin die kollisionsfreie Bahn.
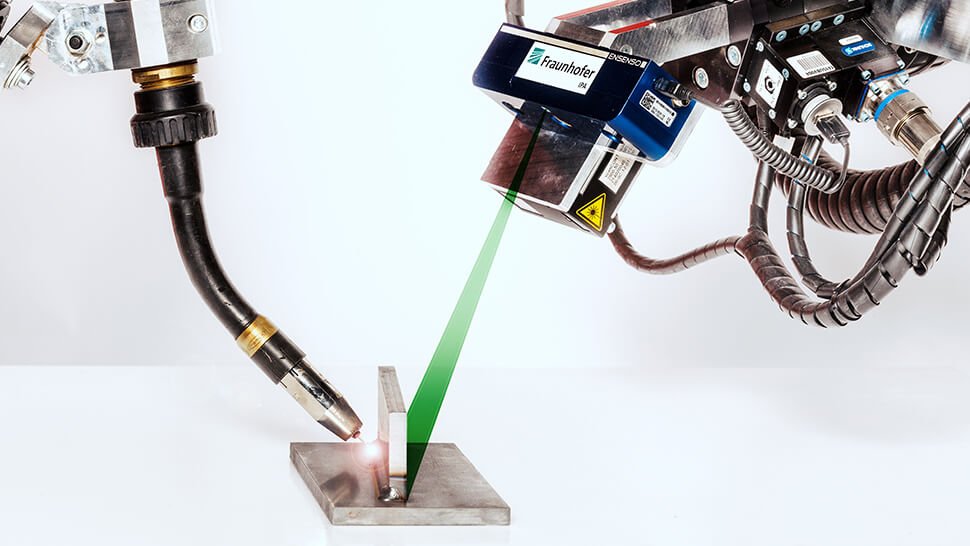
Die Nahtqualität beim roboterbasierenden Schweißen ist hoch.
Um dies zu erreichen und somit die Produktion nachhaltig zu steigern, bündelt das Projekt vier Forschungsorganisationen Europas in Robotik und Automatisierungstechnik: Danish Technological Institute (DTI, Dänemark), Fraunhofer-Institut für Produktionstechnik und Automatisierung (IPA, Deutschland), Tecnalia (Spanien) und Manufacturing Technology Centre MTC (Großbritannien). Aus 160 Bewerbungen von Unternehmen für die Zusammenarbeit wählten die Partner 64 aus und untersuchten die technische Machbarkeit sowie das Geschäftsmodell der angedachten Automatisierungslösung. Aus diesen 64 werden derzeit acht Pilotprojekte realisiert. Die Technologien haben sich entsprechend dem Technologiereifegrad verbessert und sind bereit für den Serieneinsatz.
Verschiedene Branchen sind beteiligt: So profitierten neben produzierenden Firmen auch Unternehmen aus der Medizin- und Baubranche und sogar Astronauten. Die bearbeiteten Themen reichten von der Montage über das Greifen, Navigieren, Löten, Sortieren, Scannen, Stapeln, Schneiden und Inspizieren bis zum Schweißen, Kommunizieren und Kommissionieren.
Zuverlässiger Griff in die Kiste
Eine der bearbeiteten Herausforderungen ist das prozesssichere Vereinzeln chaotisch gelagerter, reflektierender Werkstücke durch einen Roboter, was bisher an einer geeigneten Objekterkennung und Greiftechnik scheiterte. Diese Hürde nahmen erfolgreich das DTI und Fraunhofer IPA im Pilotprojekt SoSta in Zusammenarbeit mit Trumpf, Arnold und dem Startup für flexible Greiftechnik Formhand Automation GmbH.
Grundlage für die Anwendung ist die vom Fraunhofer IPA entwickelte Software bp3. Diese ermöglicht einem Industrieroboter, mithilfe von optischen 3D-Sensoren wie Laserscannern und Stereokameras ungeordnet gelagerte Werkstücke zu erkennen. Die Lokalisierung der Werkstücke erfolgt anhand eigens entwickelter, effizienter Algorithmen auf Basis des zugehörigen CAD-Modells. Zudem berechnet die Software die Roboterbahn entsprechend dem berechneten Greifpunkt und der Orientierung des Werkstücks automatisch und übermittelt sie herstellerunabhängig mittels TCP/IP an die Robotersteuerung. Die Ablage erfolgt lagerichtig.
Im Projekt SoSta geht es darum, zu untersuchen, inwieweit eine roboterbasierende Griff-in-die-Kiste-Lösung bei komplexen Blechteilen möglich ist, auch wenn die Bereitstellungssituationen anspruchsvoll sind und die Teile je nach Folgeprozess getrennt gestapelt werden müssen. Besonders herausfordernd: Die Teile sind glänzend und dünn und besonders die letzten Teile am Kistenboden sind schlecht zu erkennen, weil sie in der 3D-Punktewolke mit dem Kistenboden verschmelzen und nur schwer für Bildverarbeitungsalgorithmen wahrnehmbar sind.
Das vollständige Entleeren von Kisten, das heißt, auch das Entnehmen dieser letzten Teile vom Kistenboden, ist für den Griff-in-die-Kiste ein praxisrelevantes Qualitätsmerkmal. Deshalb kommt an dieser Stelle erstmals unterstützend Deep Learning, ein Verfahren des maschinellen Lernens, zur Segmentierung der Punktewolke zum Einsatz. Anschaulich gesprochen, schneidet das neuronale Netz die Bereiche der Punktewolke mit Werkstücken aus und übergibt diese an die weitere Bildverarbeitung. In Kombination mit dem flexiblen Sauggreifer von Formhand ergibt sich für den Griff-in-die-Kiste das Potenzial für eine entscheidende Verbesserung bei der Vereinzelung von Blechteilen.
Für Nissan fertigen das MTC und Fraunhofer IPA eine modulare und skalierbare Roboterzelle für das automatisierte Kitting. Dabei werden für die Endmontage so genannte Car Sets bestehend aus unterschiedlichen Bauteilen wie Schaltknäufen oder Lenkrädern aus verschiedenen Kisten zusammengestellt. Bei der großen Bandbreite der Artikel in Bezug auf Größe, Gewicht und Form muss einerseits die Greiftechnik flexibel und anderseits der Programmieraufwand angesichts der hohen Variantenvielfalt gering sein. Der Markt für eine Roboterlösung ist groß, da in jeder Automobilendmontage die Car-Set-Erstellung heute noch manuell erfolgt und personalintensiv ist.
Roboterschweißen für kleine Losgrößen
Im Zeitalter von personalisierten Produkten zu Kosten einer Massenproduktion, sinken praktisch in allen Fertigungen die Losgrößen. Für den Robotereinsatz bedeutet dies, dass die Höhe des Programmieraufwands über die Frage der Wirtschaftlichkeit entscheidet. In dem Pilotprojekt Autoweld werden neuartige Technologien eingeführt, um den Programmieraufwand bei Schweißrobotern erheblich zu senken. Die Technologien werden in eine etablierte Offline-Programmiersoftware als Plug-in integriert und sind nach Projektende unmittelbar einsetzbar.
Die Technologien basieren auf einer Software zur Programmierung von Schweißrobotern, die das Fraunhofer IPA entwickelt hat und im Rahmen von Robott-Net entscheidend voranbringen konnte. Der Schweißroboter kann dank 3D-Sensorik das Bauteil sehen und basierend auf dessen Position und möglichen Geometrieabweichungen die Schweißbahn selbstständig anpassen. Außerdem plant die Software die Bahn kollisionsfrei und erzeugt den erforderlichen Roboterprogrammcode automatisch.
Im Projekt integrierte das Fraunhofer IPA die Technologiekomponenten der IPA-Software in die Offline-Programmiersoftware Delfoi ARC 4.0 aus Finnland. Zusammen mit dem Projektpartner MTC wurde zudem eine neuartige Sensorbox entwickelt, die den 3D-Sensor vor den Einflüssen des Schweißprozesses schützt. Weiterer Projektpartner ist die Systemworkx AG, die die Delfoi-Software im deutschsprachigen Raum vertreibt. In den nächsten Monaten startet der Test bei Piccolo K+L Behältertechnik GmbH in der Produktion. Piccolo stellt Gitter- und Transportboxen her, die in der Automobilindustrie Verwendung finden. Weil sie in relativ kleinen Stückzahlen und hoher Variantenvielfalt gefertigt werden, schweißen die Fachkräfte in der Produktion ausschließlich von Hand. Der Einsatz von Robotersystemen ist unter solchen Bedingungen bisher unwirtschaftlich. Im Zuge von Autoweld wird der erste Roboter in der Produktion installiert, dessen Programmierung durch die Projektergebnisse signifikant leichter von der Hand geht und keine Roboterkenntnisse voraussetzt.
Dank der Technologiekomponenten mit den neuartigen Algorithmen zur Bahnplanung und 3D-Erkennung der Bauteile wurde im ersten Testszenario die Programmierzeit im Vergleich zur manuellen Teach-in-Programmierung von 90 auf sieben Minuten reduziert. Auch bei dem Mittelständler Cedis Components GmbH wurden die Technologiekomponenten bereits getestet. Dort konnte die Programmierzeit des Schweißroboters in einem ersten Szenario ebenfalls signifikant reduziert werden.
Kontakt
Thilo Zimmermann
Projektmanager
Fraunhofer-Institut für Produktionstechnik und Automatisierung IPA
Stuttgart
Tel. +49 711 9 70 12 40
E-Mail senden