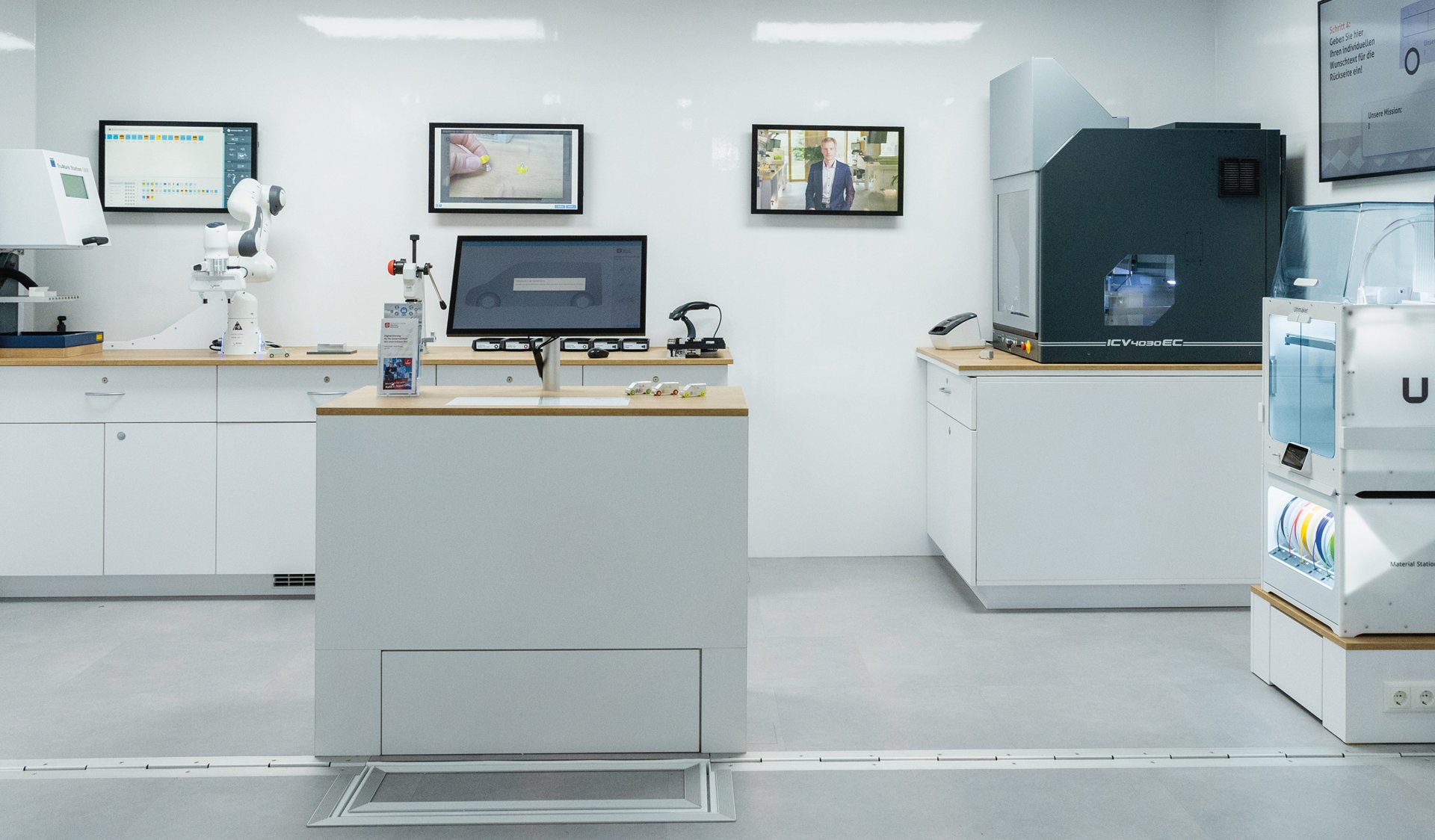
Produktion
Die Fabrik kommt zu den Unternehmen
Mit der Mobilen Fabrik ist das Mittelstand-Digital Zentrum Hannover in Niedersachsen und darüber hinaus unterwegs. Die Mobile Fabrik bringt Digitalisierungslösungen direkt zu den Unternehmen. „Mit unserer Mobilen Fabrik zeigen wir, dass Digitalisierung einen Mehrwert bringt. Unser Ziel ist es, den Unternehmen Digitalisierung und Anwendungen Künstlicher Intelligenz anhand der Fertigung eines Fahrzeugmodells schmackhaft zu machen“, sagt Dr.-Ing. Michael Rehe, Geschäftsführer des am Institut für Fertigungstechnik und Werkzeugmaschinen der Leibniz Universität Hannover angesiedelten Mittelstand-Digital Zentrums Hannover.
Für Unternehmen, die sich einen Eindruck über Potenzial und Nutzen der Digitalisierung verschaffen wollen, ist die Fabrik der ideale Einstieg. Die Fabrik ist ein voll ausgestatteter Präsentationsanhänger: Die Technologien reichen vom kollaborativen Roboter, über 3D-Druck bis zum vollständig implementierten digitalen Zwilling. Rehe erklärt: „Die Anlagen stellen eine exemplarische Umgebung des produzierenden Unternehmens dar und sind damit ganz nah dran an der Praxis.“
Die Mobile Fabrik ist eines von zahlreichen Angeboten des Zentrums: In Informationsveranstaltungen, Firmengesprächen, Workshops und Webinaren sowie durch die Begleitung von Digitalisierungsprojekten macht das Zentrum Unternehmen fit für die Zukunft. Dank der Förderung durch das Bundesministerium für Wirtschaft und Klimaschutz sind die Angebote kostenfrei.
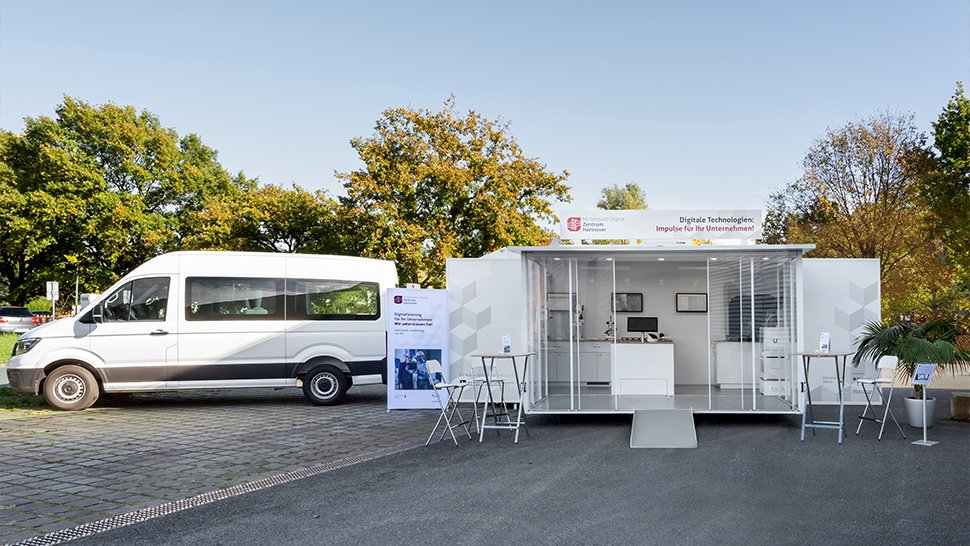
Unterwegs in ganz Niedersachsen und darüber hinaus: Die Mobile Fabrik des Mittelstand-Digital Zentrums Hannover. Fotos: Mittelstand-Digital Zentrum Hannover
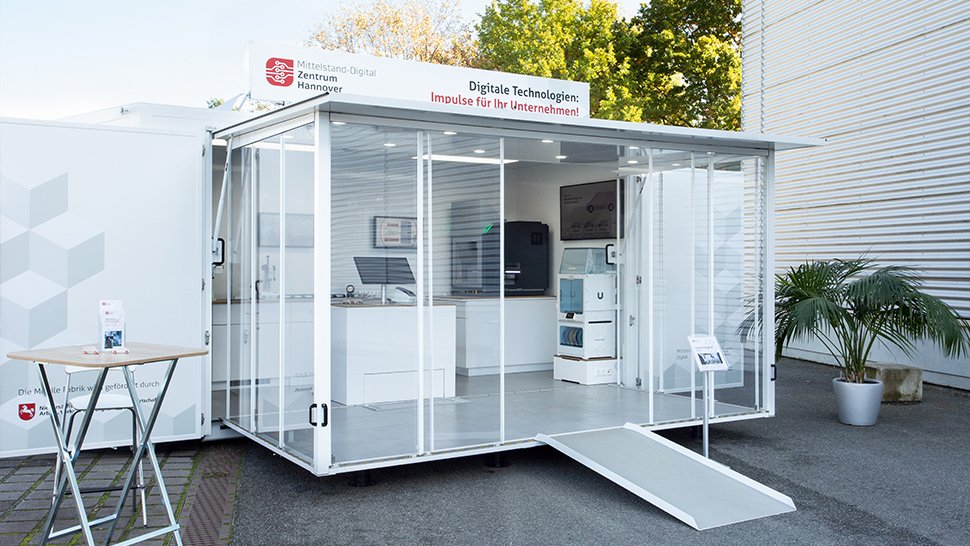
Der Präsentationsanhänger zeigt unterschiedliche Digitalisierungslösungen für Unternehmen.
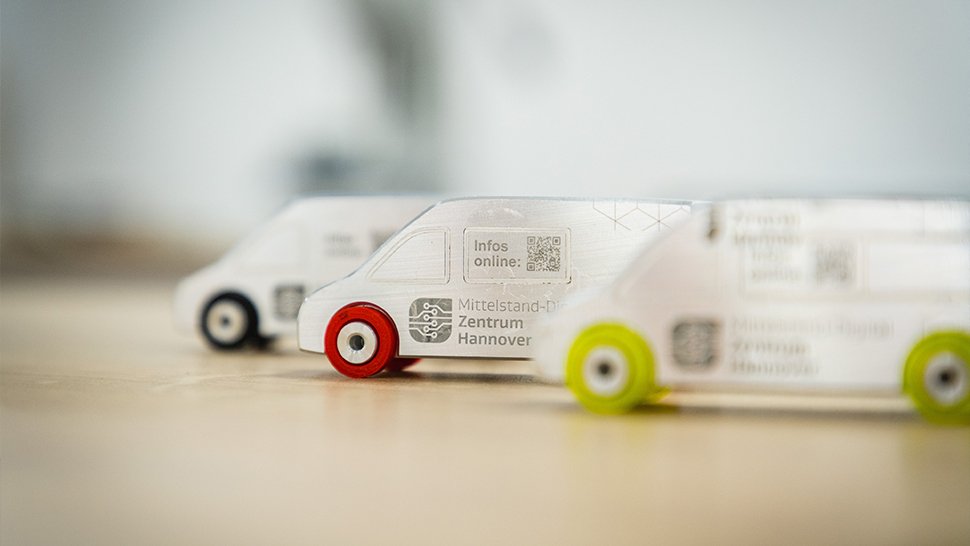
Die digitale Prozesskette in der mobilen Fabrik wird anhand der Fertigung eines individualisierbaren Fahrzeugmodells demonstriert.
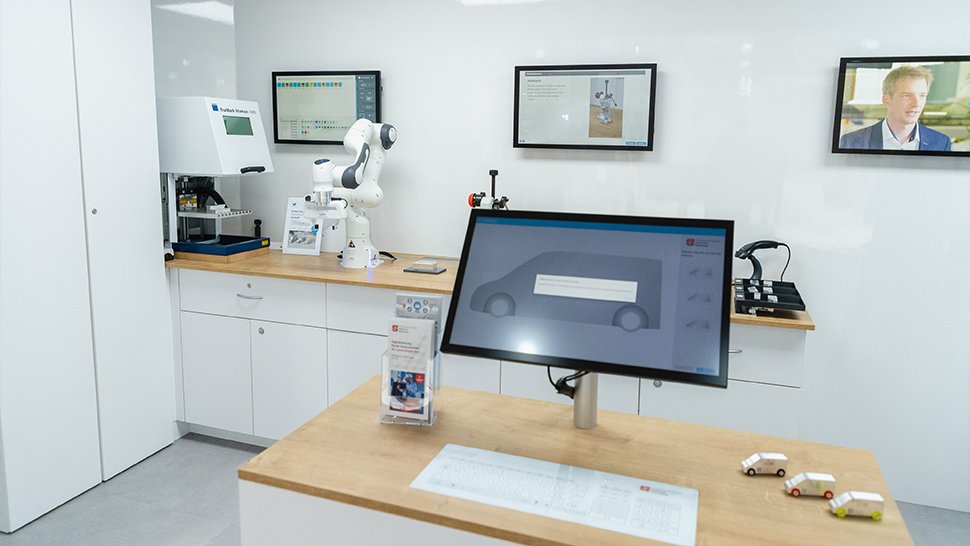
Am Konfigurator wird das Modell wunschgemäß erstellt, danach geht es in die individuelle Fertigung in Losgröße 1.
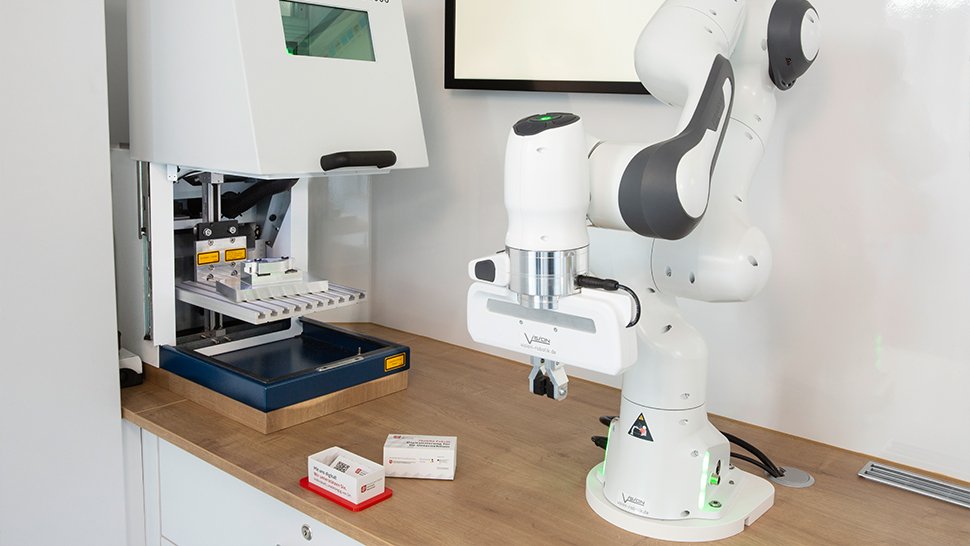
Der kollaborative Roboter transportiert das Fahrzeugmodell aus der Retrofit-Kniehebelpresse zur Laserbeschriftung.
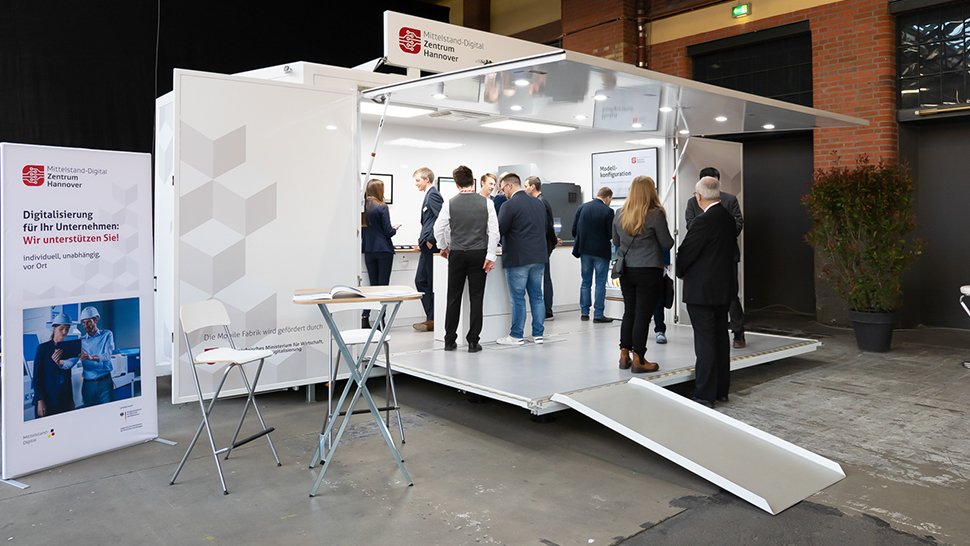
Die mobile Fabrik im Einsatz beim Zukunftstag des Bundesverbands mittelständische Wirtschaft in Berlin.
Die Mobile Fabrik im Detail
In der Fabrik bilden sieben Stationen die gesamte Prozesskette anhand der Fertigung eines Fahrzeugmodells ab.
1. Konfiguration und digitaler Zwilling
An einem Terminal können Besucher über einen Terminal ein individualisierbares Fahrzeugmodell konfigurieren. Nach Abschluss der Konfiguration wird ein digitaler Zwilling erzeugt. Hierfür wird der neue Standard verwendet, die Verwaltungsschale. Durch einheitliche Datenstrukturen, eindeutige Identifikation, einheitliche Semantik und nicht-proprietäre Kommunikationsstandards werden digitale Zwillinge mit der Verwaltungsschale zur herstellerübergreifenden Interoperabilität befähigt. Sie ist damit die Grundlage für vielfältige innovative Anwendungsfälle und 4.0-Geschäftsmodelle wie für herstellerübergreifende Monitoring-Anwendungen oder den KI-basierenden Business Excellence.
2. Additive Fertigung
Für die Reifen des Fahrzeugs stehen unterschiedliche Farben zur Auswahl. Sie werden entsprechend der Konfiguration im 3D-Druck hergestellt. Die additive Fertigung eignet sich insbesondere für die Fertigung komplexer Bauteile mit funktionalem Design. Mit ihr lassen sich Gewicht und Kosten einsparen.
3. Zerspanung
Eine Fräsmaschine stellt aus Halbzeugen (bereits vorgefertigte Bauteile) Fahrzeugkarosserien aus Aluminium her. Die Fräsbearbeitung erfolgt mit drei unterschiedlichen Werkzeugen: Die Radkästen und Fenster werden gefräst sowie die Außenkontur durch eine Fase entgratet. Dabei ist die Maschine über den offenen Standard für die industrielle Kommunikation OPC UA an das übergeordnete System angebunden, um
4. Kommissionierung
Die für den Montageprozess erforderlichen Komponenten werden in Sortierkästen am Arbeitsplatz vorgehalten. Während die Reifen, Felgen und Achsen in großer Stückzahl vorrätig sind, werden die Fahrzeugkarosserien nur in kleinerer Stückzahl gefertigt. Die Lagermenge wird daher kontinuierlich über Wägezellen überwacht und der digitale Zwilling in Echtzeit aktualisiert. Ist der Lagerbestand unterschritten, wird ein Auftrag an die Zerspanung gesendet. Welche Komponenten für den jeweiligen Auftrag erforderlich sind, zeigt ein Pick-by-Light-System.
5. Montage
Die Montage der Fahrzeuge erfolgt manuell. Eine digitale Lerneinheit (Lern-Nugget) dient der Einarbeitung und befähigt auch unerfahrene Anwender, den Montageprozess mit geringem Aufwand zu erlernen und durchzuführen. Über eine Kniehebelpresse erfolgt das Zusammenfügen der Räder und Felgen mit der Karosserie. Dieser Prozess wird über nachgerüstete Sensorik überwacht und gibt nach Erkennen der vollständigen Montage den nachfolgenden Prozess frei.
6. Handling
Das Handling des montierten Fahrzeugs übernimmt ein kollaborativer Roboter. Aufgrund seiner sensorischen Fähigkeiten ermöglicht er die Zusammenarbeit mit Menschen ohne Sicherheitszaun. Bereits bei einer leichten Kollision bleibt der Cobot stehen und fährt erst bei Bestätigung durch den Bediener mit seinem Programm fort. Dabei übernimmt der Cobot sowohl die Entnahme des Fahrzeugs aus der Kniehebelpresse als auch das Öffnen und Beladen der Laseranlage.
7. Laserbeschriftung
Nachdem der Cobot das Bauteil in die Maschine eingelegt hat, wird das Fahrzeug mittels Laser beschriftet. Die Auftragsdaten erhält der Laser aus der Produkt-Verwaltungsschale des Fahrzeugs über eine Schnittstelle des Lasers. Der Zeitstempel der Laserbeschriftung sowie die zeitliche Erfassung aller zuvor aller zuvor durchgeführten Prozessschritte wird an die Produkt-Verwaltungsschale des Fahrzeugs gesendet. Somit kann der Fertigungsstatus vollständig nachverfolgt werden. Nach Abschluss der Laserbeschriftung öffnet der Cobot den Laser erneut und entnimmt das fertige Fahrzeug.
Interoperabilität ist das Ziel
Die Mobile Fabrik - insbesondere der Bereich des Digitalen Zwillings über die Verwaltungsschale wird vom Mittelstand-Digital Zentrum Hannover kontinuierlich weiterentwickelt. „Wir wollen eine herstellerübergreifende Interoperabilität entlang der gesamten Lieferkette ermöglichen und damit die praktische Umsetzung von Manufacturing-X vorantreiben“, erläutert Zentrumsgeschäftsführer Rehe. Ein weiterer wichtiger Schritt in dieser Richtung ist die Erfassung des CO2-Fußabdrucks über alle Fertigungsschritte.
Um die Qualitätssicherung zu verbessern, wird eine innovative Methode eingesetzt: Eine künstliche Intelligenz mit Bildverarbeitung (Vision) überprüft das Fahrzeug auf mögliche Montage- und Fertigungsfehler. „Diese Technologie wird dazu beitragen, die Produktionsprozesse zu optimieren und die Qualität der Endprodukte zu erhöhen,“ betont Rehe.
Kontakt
Gerold Kuiper
Leiter Presse- und Öffentlichkeitsarbeit
Mittelstand-Digital Zentrum Hannover
Garbsen
Tel. +49 511 762 18325
E-Mail senden