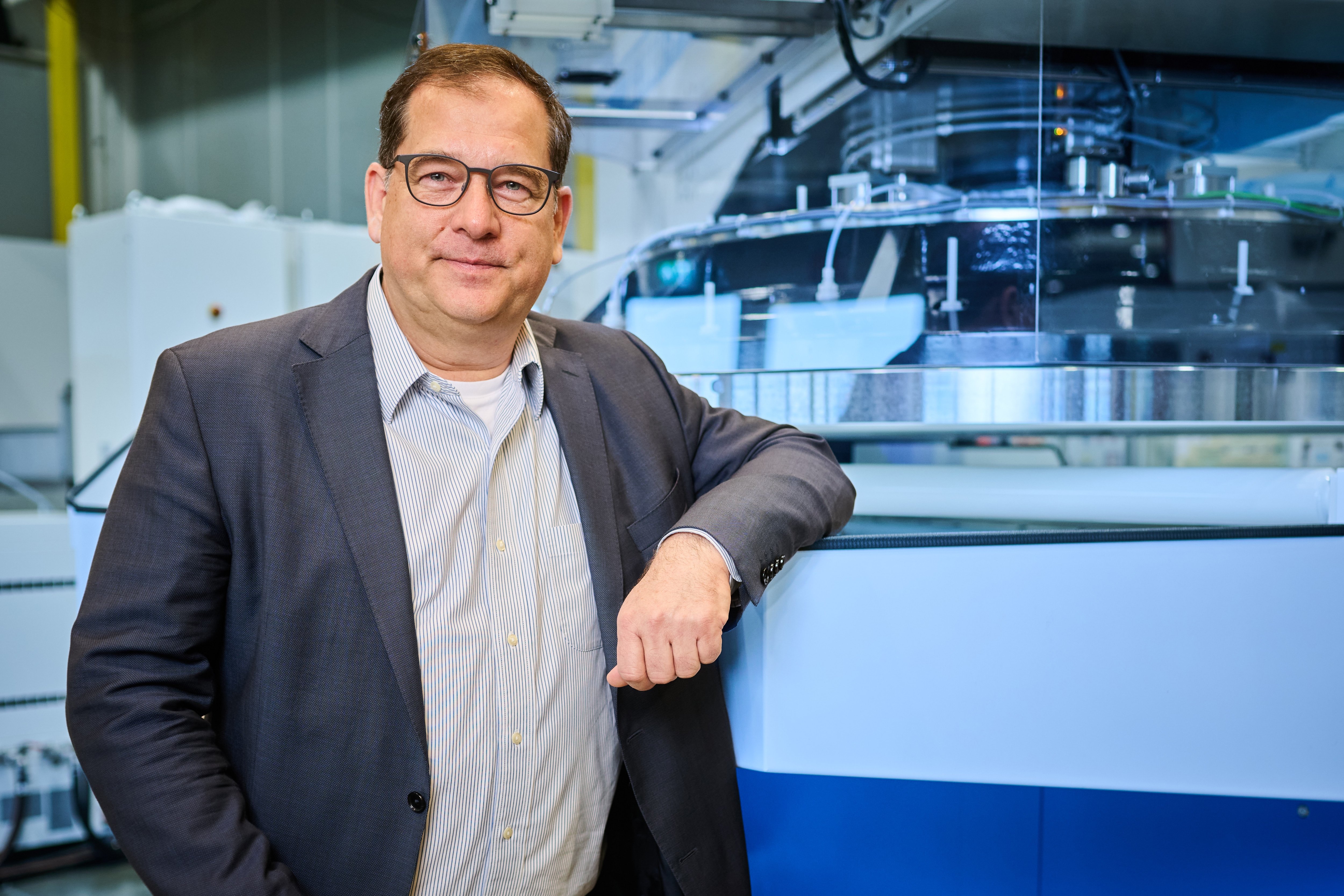
Titelinterview
Mit KI als Werkzeug zur hochfeinen Oberfläche
Die Einführung von künstlicher Intelligenz (KI) in die Schleiftechnik verändert die Industrie und eröffnet neue Möglichkeiten zur Optimierung von Prozessen. Ein Vorreiter dieser Entwicklung ist die Lapmaster Wolters GmbH mit Sitz in Rendsburg. Das Unternehmen wurde 1804 in Deutschland gegründet und stellt seit 1936 Polier-, Läpp- und Feinschleifmachinen her. Aus Anlass der Fachmesse GrindingHub, die in Stuttgart Hersteller von Schleif- und Poliertechnik zusammenbringt, sprach das IndustryArena eMagazine über die Entwicklungen im Unternehmen und in der Branche mit Geschäftsführer Matthias Mantel. Für die Hersteller ist die Anforderung an feinere Oberflächenrauigkeit, vor allem im Halbleiterbereich, ein entscheidender Treiber. KI-basierende Analysewerkzeuge helfen, die Prozesse zu verstehen und zu optimieren.
Was bewegt die Unternehmen der Schleif- und Poliertechnik?
Mantel: Die Globalisierung und die Veränderungen im globalen Umfeld sind ein wichtiges Thema. Wir stellen auch fest, dass es viel mehr Projekte speziell aus den USA gibt. In dem Re-Balancing der Welt von der Globalisierung, die in den vergangenen Jahrzehnten sehr stark in Richtung Asien ging, erkennt man eine Trendwende in Richtung USA. Den Ausschlag geben auch die Subventionspakete, die in den USA geschnürt werden. In diesem Umfeld fällt es Europa noch schwer, mit den USA Schritt zu halten. Wenn die Amerikaner einen Trend erkannt und gesetzt haben, dann sind sie relativ schnell in der Umsetzung. Europa braucht nicht zuletzt aufgrund der Komplexität durch die vielen Staaten im Vergleich zu den USA relativ lang.
Mantel: Technisch betrachtet sehen wir eine klare Tendenz hin zu größerer Präzision. Um die Ziele zu erreichen, wird auch zunehmend künstliche Intelligenz, KI, eingesetzt. In den vergangenen drei Jahren haben wir festgestellt, dass unsere Bearbeitungsmaschinen immer komplexer werden. An und für sich werden inzwischen alle Prozesse über Daten gesteuert.
Mantel: Vor allem im Halbleiterbereich ist die Feinheit der Oberflächen von entscheidender Bedeutung. Die Computerchips müssen leistungsfähiger, kleiner und schneller werden. Mit den künftigen Generationen von Lithografiemaschinen wird der Anteil an superflachen Wafern wachsen. Entsprechend werden die Anforderungen an uns herangetragen, von 50 Nanometern Ebenheit beim Silizium-Wafer auf 30 Nanometer zu gehen. Das ist gleichbedeutend mit einem technischen Entwicklungssprung. Es bedeutet fast eine Halbierung auf einem bereits sehr niedrigen Niveau. 50 Nanometer totale Ebenheit auf einer 300 Millimeter kreisrunden Platte bedeutet im Vergleich mit einem Wafer, der so groß ist wie Deutschland, also etwa 870 Kilometer im Durchschnitt, einen minimalen Höhenunterschied. Dann dürfte die Differenz zwischen dem höchsten und dem niedrigsten Punkt nicht größer als ein Smartphone sein. Damit kann man sich vorstellen, in welchen Dimensionen wir uns bereits bewegen. Der Sprung zur nächsten Generation der Wafer ist etwa die Breite einer Visitenkarte als Höhenunterschied. Um den Prozess und die Maschinen zu optimieren, benötigten wir folglich viel bessere Analyse-Tools. Deshalb mussten wir zur KI greifen, ansonsten hätten wir dieses Ziel nicht erreichen können.
Mantel: Absolut, wir haben intensiv mit Siemens als Technologiepartner zusammengearbeitet, um das Potenzial der KI auszuschöpfen. Durch den Aufbau eines eigenen KI-Teams können wir maßgeschneiderte Lösungen entwickeln, die genau auf die Anforderungen unserer Kunden zugeschnitten sind.
Mantel: Die KI basiert auf einer anderen Mathematik. Sie wird auf Daten wie Motorströme oder Temperaturen angewandt, die während des Prozesses generiert werden. Sie ermöglicht es uns, komplexe Beziehungen zwischen den Daten zu erkennen und Anomalien im Prozess frühzeitig zu identifizieren. Früher haben sich die Anwender davorgesetzt und die Kurven von Hand verglichen und aus der Erfahrung beurteilt, worin sich die unterschiedlichen Prozesse äußern. Die KI, also die Anomalie-Detektion, baut im Prinzip ein mathematisches Modell auf, in das die Ist-Daten geschoben werden. Man erkennt sofort, bei welchem Sensor die Anomalie im aktuell laufenden Prozess auftritt. Zukünftig werden Empfehlungen und Selbstoptimierung durch KI möglich sein.
„Künftig wird sich alles um Daten drehen. Das beflügelt auch den Maschinenbau.“ – Matthias Mantel, Lapmaster Wolters
Mantel: Man kann es mit dem Sprichwort vergleichen, eine Stecknadel im Heuhaufen zu suchen. Der Unterschied: Die KI sagt uns genau, wo die Nadel sich im Heuhaufen versteckt. Keiner muss künftig in analogen Vorkommnissen Interpretationen machen. Im Prinzip ist der komplette Standardprozess, den der Kunde als gut definiert, klar, und jede Abweichung ist sofort erkennbar. Bei welchem Sensor in welcher Millisekunde ist eine Abweichung aufgetreten. Dann entfallen alle Vermutungen, was die Ursache gewesen sein könnte, sondern der Grund ist live erkennbar, und wir können sofort reagieren, um die Qualität der Produkte sicherzustellen.
Mantel: Vollkommen richtig. Die Standardmaschine wird zusätzlich noch mit dem KI-Modell auf den Kunden ausgerichtet. Im Prinzip ist es nichts völlig Neues, weil wir schon immer Kundenprozesse etabliert haben. Denn der Kunde will eine bestimmte Lösung haben. Immer wichtiger wird es, im Spannungsfeld zwischen Präzision, Zeit und Kosten die Lösung zu finden. Der eine Kunde will Kostenoptimierung mit minimaler Präzision, der andere höchste Präzision. Dabei hilft uns die KI. Sie gibt uns Hinweise für die Feinabstimmung dieser Prozessabläufe.
Mantel: Am Anfang stand die Aufgabe, dass wir ein neues Analyse-Tool brauchten, um dem Anwender zu helfen. Die Maschinen wurden komplexer, und die Kundenanforderungen wurden noch genauer. Deshalb brauchten wir neue Werkzeuge. Dann haben wir festgestellt, dass letzten Endes alles von dem zeitlichen Prozess abhängt. Das bedeutet, die Werkzeuge sind nicht nur für unsere Maschinen hervorragend geeignet, sondern wir können sie bei den Schleifmaschinen wie bei den Drahtsägen einsetzen. Anhand der Definition, wie der Kunde seinen optimalen Prozess definiert, berechnet die KI den Prozess. Bei Berücksichtigung vieler Parameter benötigt sie durchaus ein paar Tage, bis das Ergebnis feststeht.
Mantel: Bei den Drahtsägen haben wir festgestellt, dass wir einen Drahtriss sogar im Voraus bestimmen können. Dabei ist der Draht lediglich halb so dick wie ein menschliches Haar, aber wenn der Draht reißt, muss die Maschine komplett wieder aufgeräumt werden. Bis sie wieder in Produktion gehen kann, vergehen mitunter acht Stunden. Deshalb war es wichtig, diesen Zeitpunkt schon im Vorfeld zu erkennen, um einen Drahtriss zu verhindern. Da halfen uns alte Daten aus Testserien, aus denen wir ungefähr zwei Minuten vor dem Crash eine Art Fingerabdruck zwischen drei Parametern erkannt haben. Auf dieses Indiz haben wir spezifische, kleinere KI-Modelle angesetzt, während die Mutter-KI immer im Hintergrund läuft.
Mantel: Die Komplexität eines Polierprozesses ist gigantisch. Das hängt nicht nur von unserer Maschine ab, oder wie der Kunde ein neues Polier-Pad auf die Scheiben appliziert hat. Durch die KI bekommt man einen Einblick in die Prozesswelt, wie man ihn noch nie hatte. Sie spüren aus meiner Begeisterung, es ist unglaublich, was wir an Sichtbarkeit und Transparenz durch dieses neue Analysewerkzeug künstliche Intelligenz gewinnen konnten.
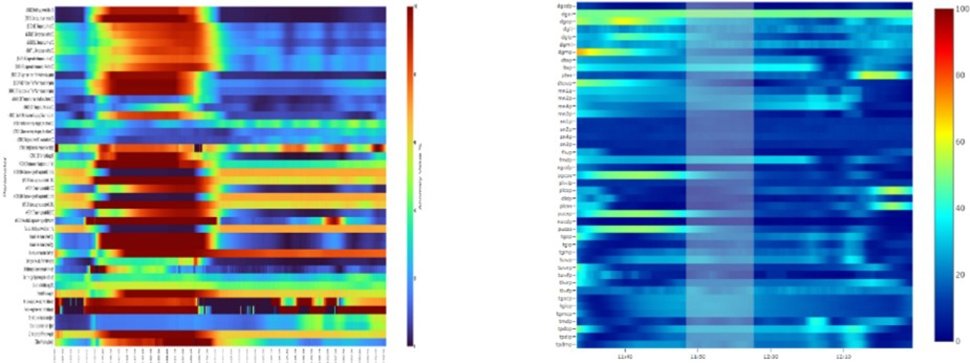
Anwendungen wie der Anomalie-Detektor werden auf einem Edge-Gerät ausgeführt und auf der Benutzeroberfläche angezeigt. Die Prozessdaten verlassen nie die Maschine und können auch nicht von außen abgerufen werden. Bild links: Erkennung und Ursachenanalyse. Bild rechts: AI-basierende Prozessanpassung. Bilder: Lapmaster Wolters
Mantel: Die Maschine muss selbstverständlich mit der entsprechenden Sensorik aufgerüstet werden. Auch die Betriebssysteme der Maschinen benötigten ein Update, um genügend Sensorik einzubinden. Ohne Daten funktioniert es nicht.
Mantel: Ich sehe nicht, dass wir einen Anwender einsparen können. KI hilft uns, neue Level zu erreichen, und das in kürzerer Zeit. Wir sehen es selbst als ein Lernwerkzeug. Wir lernen jetzt Dinge, die wir vorher noch nie gesehen haben. Es sind ganz andere Einsichten, die wir bekommen. Unsere Kunden sind mega-interessiert. Das Interesse, an diesen Entwicklungen teilzuhaben, ist riesig. Alle erhoffen sich stabilere Prozesse. Allein die Frage, wann das Polier-Pad gewechselt werden muss, ist aktuell noch eher ein Bauch- oder Erfahrungsgefühl, künftig kann die KI trotz der üblichen kleinen Unterschiede bei den Pads den exakten Zeitpunkt bestimmen, wann es gewechselt werden muss. Für mich ist KI eher ein Job-Generator. Zudem ist die junge Generation von diesen Themen total begeistert. Wenn man solche Themen als Firma nicht anbietet, dann verliert man Bewerber, weil das Unternehmen als veraltet gilt. Anders formuliert ist KI richtig sexy. Die Begeisterung, an solchen coolen Projekten teilzunehmen, ist immens.
Mantel: Zunächst sind die Fortschritte im Maschinenbau zu nennen. Genauigkeit und Geschwindigkeit mussten verbessert werden. Dann konnte man feststellen, dass der Bereich der Schleifmittel und der Maschinenbau viel enger zusammenarbeiten. Wir haben Partnerschaften mit den Herstellern von Verbrauchsmitteln angestrebt. Mit drei sehr guten Verbindungen entwickeln wir in neue Applikationsfelder unabhängig vom Kunden. Dabei haben wir festgestellt, dass der Schleifmittelhersteller – sei es Polier-Pad, Slurry oder Schleifscheibe – ebenfalls wie wir als Maschinenhersteller auch viele Parameter einstellen kann. Daraus ergibt sich eine sehr gute Kombination. Und die letzte Entwicklung hatte ich bereits angesprochen mit dem Hinweis auf Daten, Daten, Daten. Was ist denn gut für einen Schleifprozess? Welche Veränderungen ergeben sich mit neuen Schleifmitteln? Diese Fragen beantwortet die KI sofort. Das konnten wir vorher nicht beantworten. Dafür mussten lange Auswertungen gemacht werden. Auch die Entwicklung von Prozessen, Verbrauchsmitteln und Maschinen sind sehr schnell zu erkennen. Künftig wird sich alles um Daten drehen. Das beflügelt auch den Maschinenbau. Dadurch haben wir viele Dinge erkannt, um die Maschinen zu verbessern.
Mantel: Wir haben zwei Standbeine. Das eine ist der Halbleitersubstratbereich, also alles rund um den Wafer, teilweise mit höchstem Anspruch an die Präzision bei Materialien wie Silizium oder Siliziumkarbid. Das zweite Standbein nennen wir General Industry. Dabei handelt es sich um feinmechanische Bauteile – Glas, Keramik, Metallen – durch alle Applikationen.
Mantel: Wir wollen noch bessere, also präzisere Maschinen entwickeln und bauen. Die Prozesse selbst sollen stabiler werden. Also Präzision und Prozessstabilität werden zunehmend gefragt. Darin zeigt sich der Wandel in der Industrie. Früher haben Kunden eine Maschine gekauft und dann versucht, die Maschine und ihre Prozesse zu verstehen. Mit dem Hersteller von Verbrauchsmitteln haben sie ihre Prozesse selbst entwickelt. Diese Prozesse sind inzwischen so komplex geworden, dass ein Game Changer da ist. Wir wollen dabei auch Vorreiter sein und gehen aktiv in die neuen Partnerschaften, um dem Kunden Lösungen anzubieten. Das Interessante an unseren Prozessen ist, dass wir immer etwas Neues lernen können. Das Zusammenbringen in dem Spannungsdreieck ist das Entscheidende.
Foto: Lapmaster Wolters
Kontakt
Matthias Mantel
Geschäftsführer
Lapmaster Wolters GmbH
Rensburg
Tel. +49 4331 458-0
E-Mail senden