
Produktion
Mittelständische Impulse für die
E-Mobilität
Die Verkehrswende steht und fällt mit einer Frage: Wie lassen sich Elektrofahrzeuge nachhaltig und wirtschaftlich herstellen? Das sechste Laser-Symposium Electromobility (6. LSE) des Fraunhofer-Instituts für Lasertechnik (ILT) lieferte Antworten. Fachleute von mittelständischen Unternehmen sowie aus Forschungsinstituten zeigten anhand von Anwendungen aus der Praxis, wie sich Batterien und Hochleistungselektronik effizienter, präziser und nachhaltiger herstellen lassen.
Die Bandbreite reichte von Spanntechnik zum Laserschweißen von Batteriekontakten bis zum Laserschneiden von Batterieelektroden.
Lasertechnik erobert Batterieproduktion
Laserbasierende Fertigungsmethoden für die Produktion von Batteriemodulen und -packs stehen im Mittelpunkt der Forschungsarbeit des Fraunhofer ILT. Die bisherigen Symposien zeigten, dass der Laser bereits an vielen Stellen zum Einsatz kommt – etwa bei der Oberflächenbehandlung, Reinigung, der Entfernung von Isolationsschichten oder als energiesparende Alternative zu gasbetriebenen Trocken-Öfen.„Ich freue mich, dass dieses Jahr bewährte Laserverfahren wie Löten, Schneiden und Schweißen bei Lösungen für die Batterietechnik auf dem LSE dominierten“, erklärte Dr. Alexander Olowinsky, Abteilungsleiter Fügen und Trennen am Fraunhofer ILT. „Ich bin überzeugt, dass diese weiterentwickelte Lasertechnik nicht nur bei der Präzision, sondern auch bei Wirtschaftlichkeit und Nachhaltigkeit dem Wettbewerb Paroli bietet.“

Der Einsatz von Lasertechnik in der Batteriezellenproduktion bietet entscheidende Vorteile, berichtete Luca Schmerbeck, Sonplas. Stillstandszeiten sinken und die Batterieleistung wird verbessert.
Trendwende bei Spezialisten für Verbrennungsmotoren
Die Sonplas GmbH kennt den harten internationalen Wettbewerb: Das bayerische Unternehmen hat bereits 1000 Spezialmaschinen zum Montieren und Testen von Einspritzdüsen, Kraftstoffpumpen, den elektrischen Antriebsstrangs und für die Leistungselektronik auf dem globalen Markt etabliert.Anlagen für die Produktion von Batteriezellen waren jedoch Neuland, das Sonplas 2020 betrat. Luca Schmerbeck, Produktmanager Batterie, erklärte: „Wir wollen die Produktionsqualität verbessern und die Ausschussquote senken, die bei konventionellen Produktionsmethoden oft zu hoch ausfällt.“
Das Unternehmen beschäftigt sich mit Lithium-Ionen-Batterien und nutzt Laserverfahren, um die Qualität der Batteriezellenproduktion zu verbessern. Diese Verfahren umfassen vorwiegend das Laserschneiden von Rolle zu Rolle, das Aufteilen großer Rollen in kleinere und das Schneiden von Rolle zur Platte.
Der unternehmensspezifische Ansatz zielt darauf ab, Effekte wie Delamination und Gratbildung zu überwinden, die bei mechanischen Schneideprozessen auftreten können und die Batteriezellenqualität beeinträchtigen. Schmerbeck berichtete: „Wir konzentrieren uns auf das Kerben, Schneiden und Trennen des Materials.“
Laserschneiden erhöht Batterieleistung
Forschungsergebnisse des Unternehmens liefern ein ausgezeichnetes Argument für laser-geschnittene Batterieelektroden, mit denen sich die Entladekapazität im Vergleich zu mechanisch gestanzten Elektroden signifikant steigern lässt. Die Studien berichten laut Schmerbeck nicht nur von höherer Homogenität und geringeren Ausreißern bei laser-geschnittenen Proben, sondern weisen auch eine verbesserte Gesamtleistung des Batteriesatzes auf.Laserstrahlschneiden verbessert die Kantenqualität sowie Delamination des Aktivmaterials. „Der Einsatz von Lasertechnik in der Batteriezellenproduktion bietet unseren Kunden entscheidende Vorteile“, sagte der Produktmanager. „Zum einen senkt es Werkzeugstillstandszeiten und -kosten, zum anderen sehen wir eine merkliche Verbesserung der Batterieleistung.“ Präzise Lasertechnik sei kein teurer Luxus, sondern – clever eingesetzt – auf lange Sicht ein klarer Wettbewerbsvorteil.
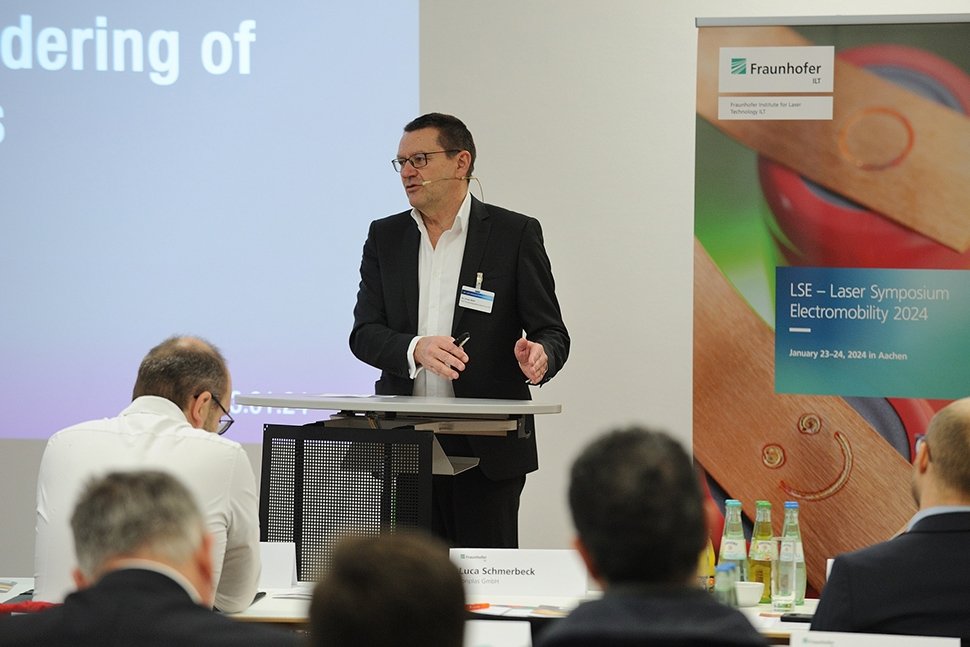
Ein Vorteil des Lötens liegt in der Diffusion. schilderte Dr. Ernst Wolf, Wolf Produktionssysteme, die Entwicklung.
Präzision in der Montagelinie
Dieser Trend zur Präzision und Kosteneffizienz durch den Einsatz modernster Technologien setzt sich bei der Wolf Produktionssysteme GmbH & Co. KG aus Freudenstadt fort. Ein Beispiel nennt Entwicklungsleiter Nico Reinheimer: „Mit der Automatisierungsplattform SkyLine erreichen wir dank unseres eigenen Transfersystems beeindruckende Taktzeiten zwischen fünf und 15 Sekunden.“Der Sondermaschinenbauer entwickelte auf dieser Basis Produktionssysteme zum Schweißen von Batteriekontakten, für die das Unternehmen Verfahren für das Verbinden von Materialien wie Aluminium und Kupfer entwickelte. Die Herausforderung ist hoch, denn die Materialstärken betragen lediglich 0,2 bis 0,4 Millimeter. Daher besteht stets die Gefahr, dass der Laser durch die Zelle schießt und sie beschädigt.
Wer winzige, passgenaue Bleche verbinden möchte, benötigt einen Laser mit hoher Qualität und einer speziellen Strahlformung. Reinheimer schildert die Erfahrung: „Es handelt sich um einen Taumelprozess. Diese Kombination aus punktueller und linearer Bewegung erzeugt ein breiteres Schmelzbad.“ Der Taumelprozess biete eine genaue Kontrolle über die Schweißtiefe und die Qualität der Schweißnaht, was besonders in der Präzisionsfertigung von entscheidender Bedeutung sei. „Zusätzlich verhindert das Taumeln Durchschüsse.“
Wolf setzt außerdem auf die „Floating-Grip«-Technologie: Diese Spanntechnik positioniert Aluminium und Kupfer so, dass eine gleichmäßige Schweißverbindung entsteht. Floating Grip passt sich automatisch den Positionen der zu verbindenden Teile an.
Reinheimer erläutert: „Das reduziert den Druck auf die Batteriezellen und vermeidet unnötige Beanspruchung, weil der Floating Grip in der Mitte der Kontakte zentriert. Im Ergebnis können beide Materialien ohne zusätzliche Kraftanwendung präzise verbunden werden.“ Diese Technologie korrigiert Unregelmäßigkeiten bei der Positionierung der Materialien und sorgt für optimale Schweißbedingungen.
Material und Prozesse im Griff
Leistungselektronik reagiert noch empfindlicher auf Hitze als Batteriekontakte. Die Alternative benennt Firmeninhaber Dr.-Ing. Ernst Wolf: „Laser-Löten schont hitzeempfindliche Komponenten, da es bei niedrigeren Temperaturen operiert, wodurch die Integrität von Leiterplatten bewahrt bleibt. Ein wesentlicher Vorteil des Lötens liegt in der Diffusion, durch die eine dünne, aber robuste intermetallische Verbindung entsteht.“ Zahlreiche Parameter wie Löt-Temperatur, Löt-Zeit und Zusatzstoffen beeinflussen die Dicke der intermetallischen Phase.Sein Unternehmen hat das Laserlöten zu einem präzisen und effizienten Fügeverfahren weiterentwickelt. Ebenso wie beim Laserschweißen kommt es auf die richtige Position an. „Wenn wir den Laser einschalten, muss das Zinn die Lötstelle erreichen“, nannte Wolf ein Beispiel. „Wenn die Laserleistung jedoch zu hoch ist, wird das Zinn nie seine Position erreichen, weil es vorher geschmolzen ist.“ Das Laserlöten erfordert daher eine exakte Steuerung der Laserleistung und -position, um optimale Ergebnisse zu erzielen.
Die präzise gesteuerte Laserlöttechnik von Wolf verbindet hochempfindliche Elektronikkomponenten mit weniger Hitze. Dadurch spart sie Energie, schont Materialien und sorgt für langlebigere Produkte: Das senkt die Kosten und macht den Herstellungsprozess umweltfreundlicher.

Statt einer festen wird eine mobile Klemme eingesetzt, um auch bei hohen Kapazitäten präzise zu arbeiten, berichtete Dr. Lars Helmich, Hesse, vpm Draht-Bonden.
Drahtloses Schweißen
Hitzeempfindlichkeit ist ebenfalls ein Schwerpunkt für die Hesse GmbH aus Paderborn, einem Hersteller von Ultraschall-Drahtbondern und -Schweißanlagen. Die Paderborner entschieden sich bei der Entwicklung von Fügetechnik für neue Hochleistungselektronik bewusst gegen traditionelles Drahthandling.Im SmartWelder, einer Ultraschallschweißanlage mit 1,5 Kilowatt Leistung, verwenden sie stattdessen eine flexible, zylinderförmige Klemmvorrichtung. Entwicklungsingenieur Dr. Lars Helmich sagte: »Es gibt verschiedene Ansätze, wie man Module einspannen kann. Wir setzen statt einer festen eine mobile Klemme ein, die sich von einer Verbindung zur anderen bewegt. Dieses System ermöglicht es uns dank seiner stabilen Struktur, auch bei hohen Kapazitäten präzise zu arbeiten.“

Von der weiterentwickelten Lasertechnik ist Dr. Alexander Olowinsky, Fraunhofer ILT, nicht nur bei der Präzision, sondern auch bei Wirtschaftlichkeit und Nachhaltigkeit überzeugt.
Mit Hilfe des Lasers
Die Workshops und Vorträge beim LSE 24 zeigten die vielfältigen Möglichkeiten, wie Laser dazu beitragen, die Effizienz, Qualität und Skalierbarkeit in der Produktion von Batterien zu verbessern. Ein zentrales Thema war die Prozessüberwachung, die durch moderne Technologien wie KI-basierende Ansätze und Echtzeitmessungen entscheidende Fortschritte gemacht hat.Olowinskys Fazit lautete: „Ich bin immer wieder erstaunt, wie viel mittelständische Betriebe mit innovativen Fertigungsmethoden zur Mobilitätswende beitragen. Ihre Entwicklungen rund um die Lasertechnik stärken nicht nur die Effizienz und Nachhaltigkeit in der Batterieproduktion, sondern auch Deutschlands Position im globalen Wettbewerb.“
Die enge Zusammenarbeit zwischen Industrie und Forschungsinstituten wird eine Schlüsselrolle spielen, um die Herausforderungen der E-Mobilität erfolgreich zu bewältigen und die Idee einer nachhaltigen und emissionsfreien Mobilität voranzutreiben.
Autor des Artikels: Presseagentur Nikolaus Fecht, Gelsenkirchen
Fotos: Fraunhofer ILTKontakt
Dr.-Ing. Alexander Olowinsky
Leiter der Abteilung Fügen und Trennen
Fraunhofer-Institut für Lasertechnik ILT
Aachen
Tel. +49 241 8906-491
E-Mail senden