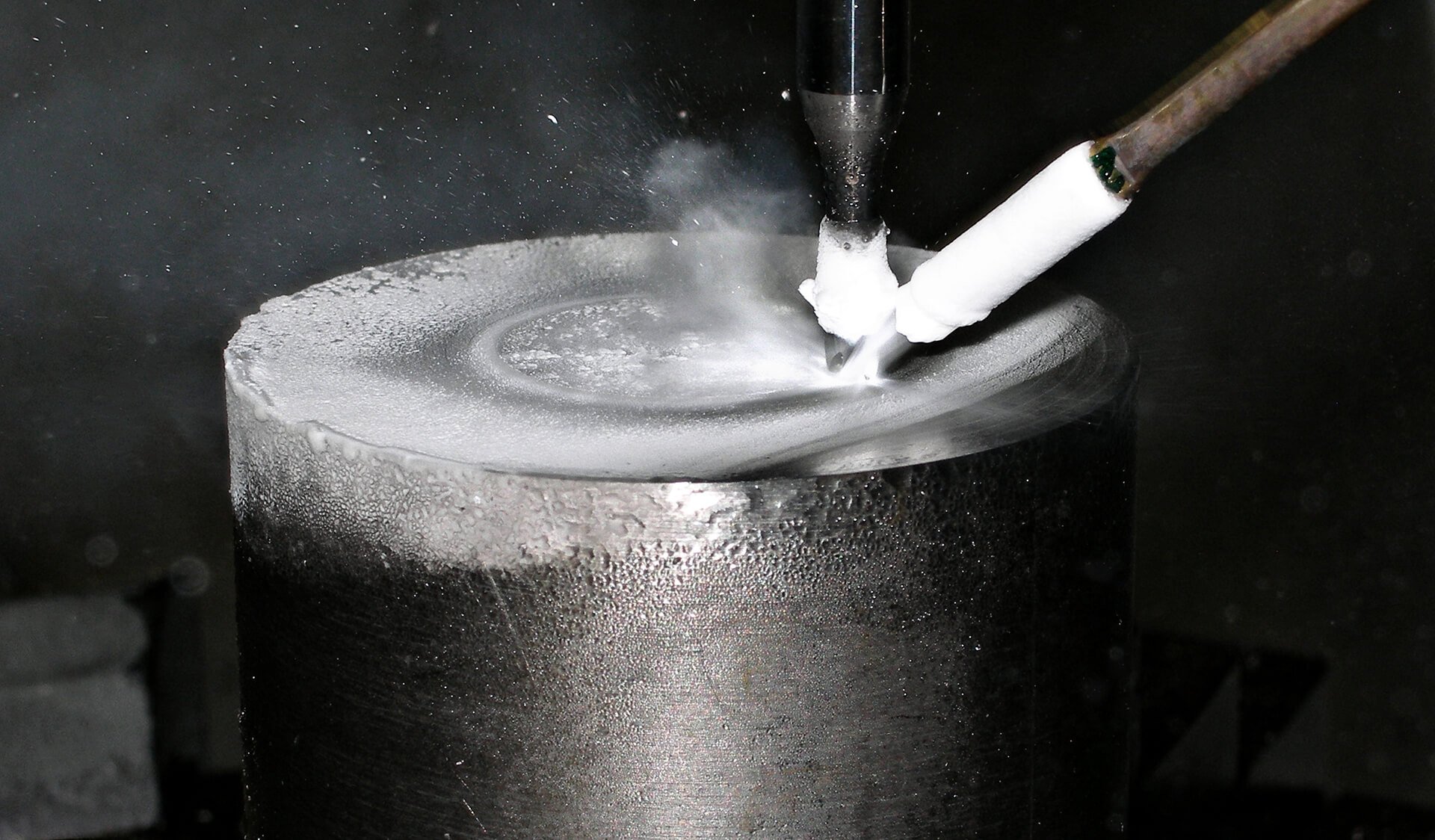
Titelthema
Minimal geschmiert oder trocken-kalt
Der demographische Wandel in Deutschland und steigende Lebensstandards in boomenden Ländern wie China, Indien oder Brasilien lassen die Nachfrage nach Zahnersatz steigen. Die Versorgung mit Zahnimplantaten erfreut sich wachsender Beliebtheit, da den ästhetischen Ansprüchen und dem Wunsch nach festem Zahnersatz vieler Patienten so am besten nachgekommen werden kann.
In Deutschland werden jährlich eine Million Zahnimplantate eingesetzt. Trotz verstärkten Einsatzes von Implantaten ist jedoch das Potenzial der Implantologie lange nicht ausgeschöpft. 2005 wurden in Deutschland in nur 15 Prozent der Fälle Implantate den herkömmlichen Lösungen durch Brücken und Prothesen vorgezogen. In bis zu 90 Prozent der Fälle wäre ein Implantateinsatz medizinisch möglich gewesen. Dentalimplantate werden zu über 90 Prozent aus Titan, insbesondere Reintitan, hergestellt.
Aufgrund von Biokompatibilität, Korrosionsbeständigkeit und hoher spezifischer Festigkeit ist Reintitan ein häufig verwendetes Material für dentale Anwendungen. Allerdings gilt Titan wegen seiner geringen Wärmeleitfähigkeit, niedrigem E-Modul und Neigung zur Segmentspanbildung als schwer zu zerspanendes Material. Hoher Verschleiß und kurze Standzeiten bei geringer Produktivität sind die Folge. Die technologische Entwicklung für die Dentaltechnik schreitet jedoch rasant voran. 2009 wurde bereits ein Drittel der in Deutschland produzierten Brücken und Prothesen automatisch gefertigt. Studien sagen eine Verdoppelung bis 2015 voraus. Für die Zerspanung stehen dabei leistungsfähige und speziell auf den Einsatz in der Dentaltechnik ausgelegte Fräsmaschinen zur Verfügung. Die für die Bearbeitung von Titan eingesetzten Fräswerkzeuge kleineren Durchmessers weisen allerdings erhebliches Verbesserungspotenzial auf. Die Leistungen der Dentalfräsmaschinen hinsichtlich Spindeldrehzahlen und Maschinenbeschleunigungen können nicht voll ausgenutzt werden. Es ist daher erforderlich, die Leistungsfähigkeit der Fräswerkzeuge zu verbessern. Der Markt bietet trotz hoher Nachfrage für die Bearbeitung von Reintitan Grade 4 jedoch keine speziell ausgelegten Dentalfräswerkzeuge mit kleinem Durchmesser.
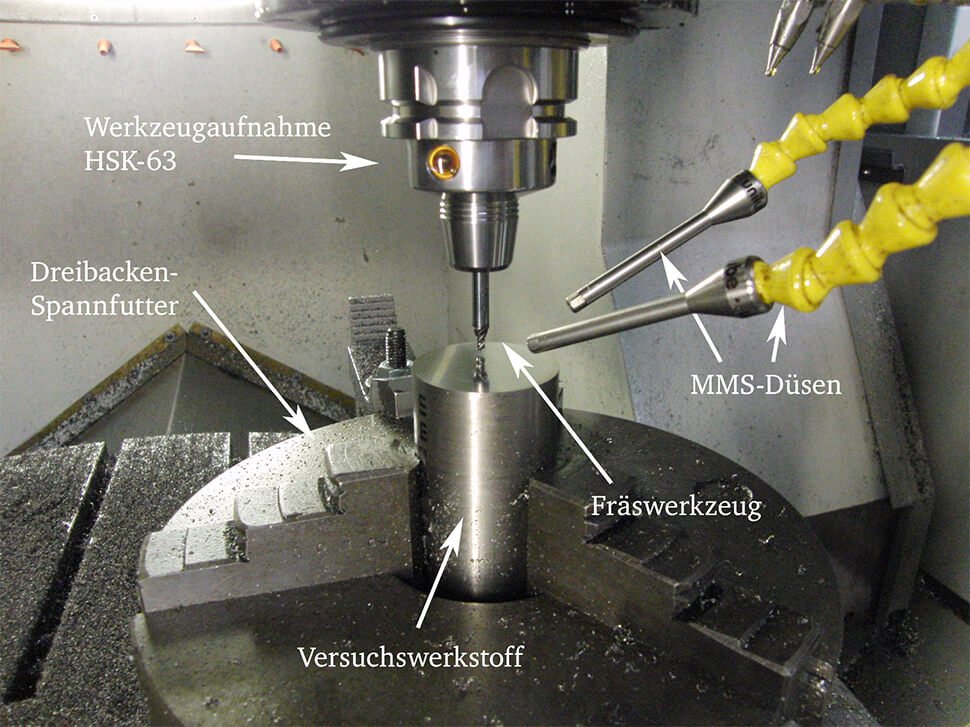
Versuchsaufbau; Fräsprozess mit Minimalmengenschmierung. Foto: TU Darmstadt
Am Institut für Produktionsmanagement, Technologie und Werkzeugmaschinen (PTW) der TU Darmstadt wird zurzeit die Eignung von Hartmetallfräswerkzeugen im Durchmesserbereich drei Millimeter für die Schruppbearbeitung von Reintitan Grade 4 untersucht. Dabei wird der Einfluss der Technologieparameter Schnittgeschwindigkeit, Zahnvorschub, axiale Zustellung, Werkzeugbeschichtung und -geometrie sowie der Prozesskühlung auf das Verschleißverhalten von Fräswerkzeugen analysiert. Basierend auf den Untersuchungen soll so die Optimierung eines Fräswerkzeugs erreicht werden, um Reintitan in der Medizintechnik wirtschaftlicher und ökologischer zerspanen zu können, als dies heute der Fall ist.
Versuchsaufbau
Die Zerspanungsversuche wurden unter Verwendung von MMS (Esteröl, 20 Milliliter pro Stunde) mit fünf verschiedenen Fräsertypen dreier Hersteller durchgeführt (Durchmesser drei Millimeter, Schneidenanzahl vier, Schaftdurchmesser sechs Millimeter). Zum Einsatz kamen Torusfräser und Schaftfräser mit gefasten Schneidecken, drei Beschichtungstypen und verschiedene Schneidengeometrien. Der Werkstoff lag als Rundmaterial vor und wurde zur Bearbeitung mittels eines Dreibackenfutters gespannt. Ein Versuchsplan mit drei Faktoren zu je zwei Stufen diente als Versuchsgrundlage. Das Abbruchkriterium wurde auf einen Freiflächenverschleiß VBmax = 200 Mikrometer und ein maximal zerspantes Volumen festgelegt, das einem Maß der Titanrondenzerspanung in der Dentalindustrie entspricht. Die Verschleißmessung erfolgte auf einem Auflichtmikroskop. Zusätzlich wurden die Fräsergeometrien durch 3D-Messverfahren analysiert.
Um den Einfluss der Prozesskühlung auf den Verschleiß zu untersuchen, wurden weiterführende Versuche unter Einsatz von CO2-Schnee-Kühlung mit verschiedenen CO2-Durchflussvolumina durchgeführt. Mittels Schlitzdüsen entsteht ein gebündelter Kühlstrahl mit hohem Anteil an festen Kohlendioxidpartikeln, die beim Auftreffen auf die Schneidstoffoberfläche sublimieren und damit einen erhöhten Wärmeentzug ermöglichen. Die Zuführung des CO2-Schnees wurde durch seitliches Freistrahlen als auch axial geführtes Strahlen durch einen werkzeugseitigen Düsenaufsatz variiert. Der außerordentliche Vorteil dieser Kühlmethode nebst Tiefsttemperaturen bis zu minus 76Grad Celsius ist die Rationalisierung einer reinigenden Nachbehandlung des Werkstücks.
Zerspanergebnisse
In den Parameteruntersuchungen zum Verschleißverhalten von Hartmetallfräswerkzeugen wurden zunächst Schnittgeschwindigkeit, Zahnvorschub und Schnitttiefe variiert. Die Versuche wurden mit einer Esteröl-Minimalmengenschmierung von 20 Milliliter pro Stunde durchgeführt. Eine Parameterkombination aus vc = 130 Meter pro Minute, fz = 0,02 Millimeter und ap = 0,15 Millimeter zeigte die bisher höchsten Standzeiten und das stabilste Verhalten in Bezug auf den Verschleißverlauf bei gleichzeitig hoher Produktivität. Die Untersuchungen zur Beschichtungsauswahl detektierten den geringsten Freiflächenverschleiß bei Verwendung einer Aluminium-Chrom-Mitrid-Beschichtung (AlCrN). Plastische Verformung, Abrasion und Adhäsion traten im Vergleich zu mit Titan-Aluminium-Nitrid (TiAlN) oder Titan-Chrom-Nitrid (TiCN) beschichteten Werkzeugen in geringerem Maße auf.
Die Untersuchungen zur Werkzeuggeometrie zeigten, dass eine torische Geometrie zu bevorzugen ist. In Hinblick auf das Schlichten lagen nahezu gratfreie Werkstückkanten vor, wohingegen mit Schaftfräsergeometrien um Faktor 36 größere Grathöhen erreicht wurden. Eine Prozessanfälligkeit durch hochabrasive Gratbildung kann hierdurch ausgeschlossen werden.
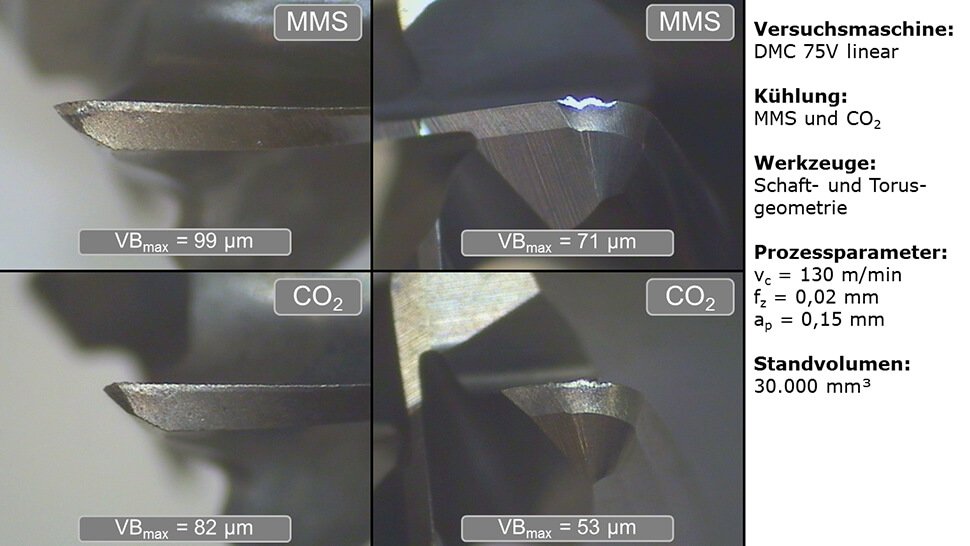
Verschleißerscheinung mit Minimalmengenschmierung (oben) und CO2-Schneekühlung (unten). Fotos: TU Darmstadt
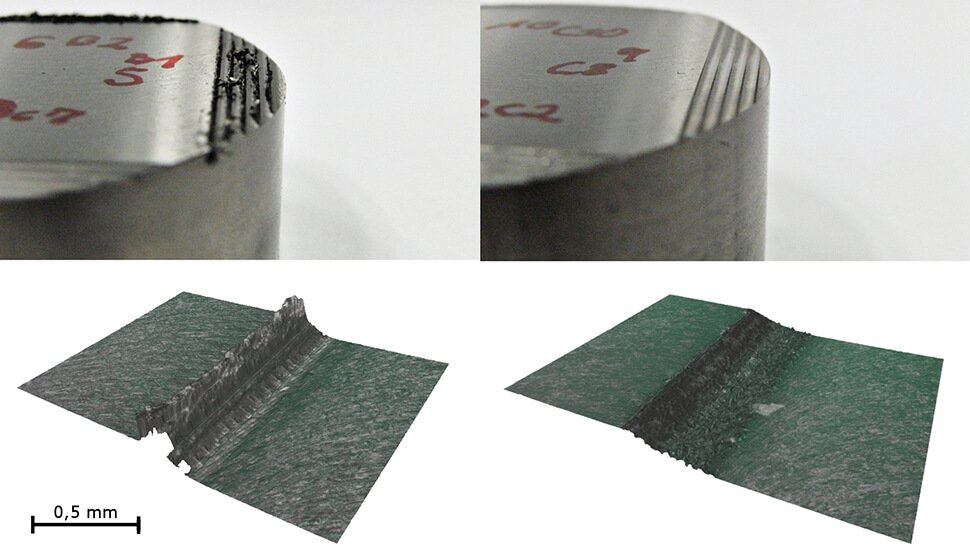
Gratbildung durch unterschiedliche Geometrien; Versuchswerkstück (oben) und 3D-Scans (unten)
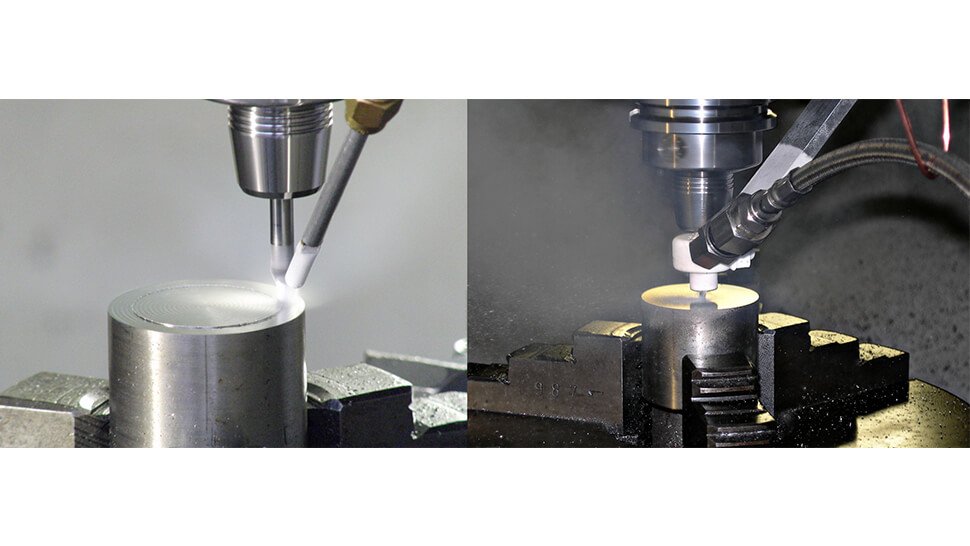
Zerspanung mit CO2-Schneekühlung, Freistrahl (links) und mit axialer Aufsteckdüse (rechts)
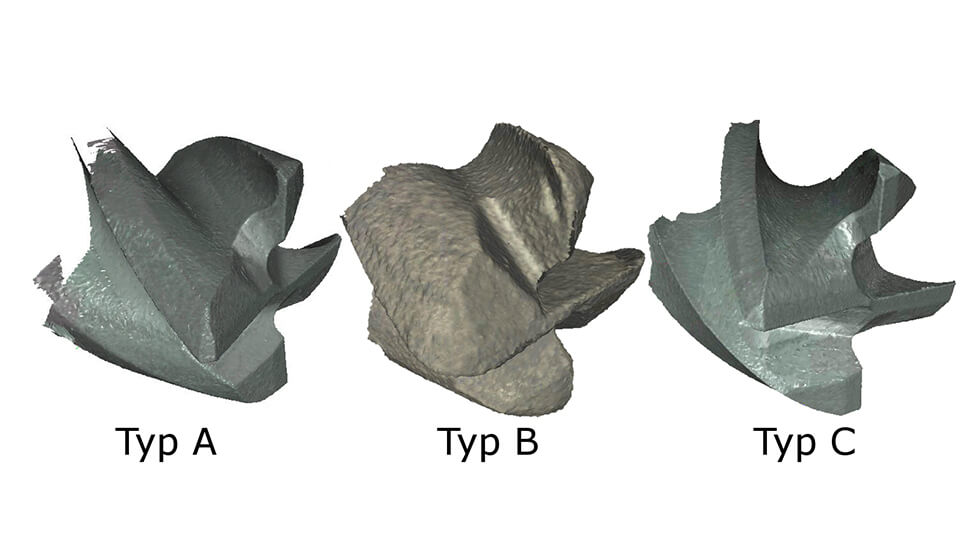
Exemplarische 3D-Darstellung der Fräsergeometrien
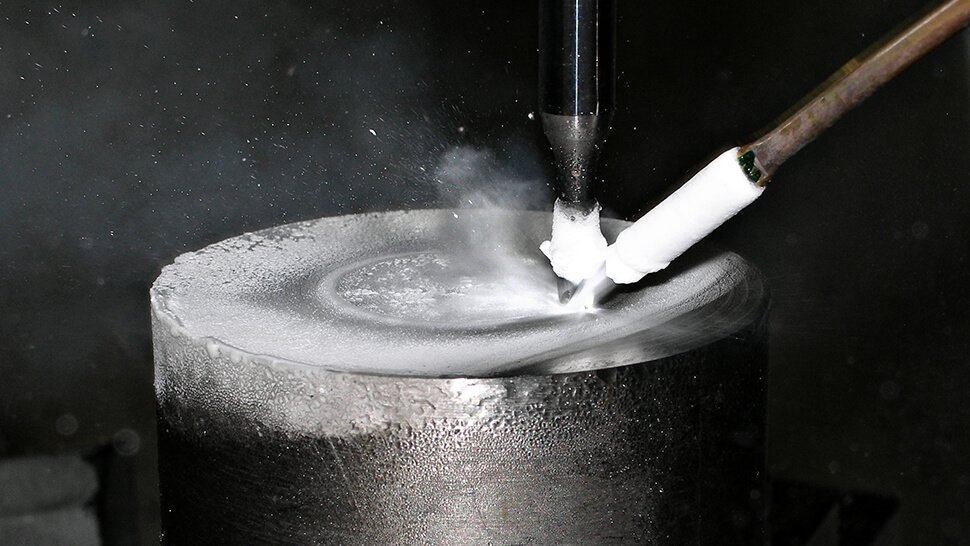
Zerspanung von Reintitan Grade 4 unter der Verwendung von CO2-Schneestrahlkühlung.
Die Substitution der MMS-Kühlschmierung durch CO2-Schneestrahlen in weiteren Versuchsreihen zeigte eine Verringerung des Freiflächenverschleißzuwachses. Freiflächenverschleiß als auch Kanten- und Eckenausbrüche wurden fast gänzlich unterdrückt. Gründe hierfür sind u.a. die Verringerung oxidativer und diffusiver Vorgänge in der Spanungszone. Weiter konnte der Volumenstrom des kryogenen Kühlmediums im Vergleich zu vorhergehenden Untersuchungen am PTW auf ein Minimum reduziert werden, ohne Einbußen beim Verschleißverhalten aufzuzeigen. Aus den Untersuchungen am TW wurde eine für die Reintitanzerspanung geeignete Werkzeuggeometrie ermittelt. Die Weiterentwicklung des Fräswerkzeugs befindet sich derzeit im Versuch. Weiterführend wird die Leistungsfähigkeit des kryogenen Fräsprozesses gegenüber der Nass- oder Minimalmengenschmierung in der Zerspanung ganzheitlich betrachtet.
Studien ließen schon sowohl auf einen ökonomischen als auch ökologischen Vorteil der CO2-Kühlung gegenüber der Minimalmengenschmierung und vor allem der Überflutungskühlung schließen. Mit der gezeigten massiven Reduzierung des CO2-Durchsatzes von bis zu 96 Prozent gegenüber anderen Versuchsreihen werden sich weitere Vorteile der kryogenen Titanzerspanung offenbaren.
Quellen
Klug, Elmar (2012): Biokompatible Werkstoffe prozesssicher zerspanen. Komplettes Werkzeugportfolio für Implantate und medizinische Instrumente. In: WB Werkstatt + Betrieb (4), S. 40–44. Online verfügbar unter www.werkstatt-betrieb.de/dl/WB110559.html, zuletzt geprüft am 13.05.2012.
Kaiser, Mirjam (2006): Dentalimplantate – hohes Wachstum garantiert. Innovation und Ästhetik sind die wichtigsten Akzeptanztreiber. In: GoingPublic Magazin (Sonderbeilage "Medizintechnik 2006"), S. 16–17.
Abele, E.; Dietz, S.; Santin, R. (2012): Produktionstechnik für die Fertigung von Zahnersatz. Dentaltechnische Produkte prozesssicher ohne technisches Fachpersonal fertigen. In: wt Werkstatttechnik online 102 (1/2), S. 62–67.
Abele, E.; Sieber, M. (2011): CO2 fördert den Klimaschutz. Flüssiggaskühlung verlängert bei der Titanzerspanung die Standzeit von HM-Werkzeugen. In: WB Werkstatt + Betrieb (10), S. 26–29. Online verfügbar unter www.werkstatt-betrieb.de/WB110478, zuletzt geprüft am 14.05.2012.
Kontakt
Marc Sieber
Forschungsgruppe Technologie
Wissenschaftlicher Mitarbeiter
Technische Universität Darmstadt
Institut für Produktionsmanagement, Technologie und Werkzeugmaschinen (PTW)
Darmstadt
Tel. +49 6151 16-6624
E-Mail senden
Anzeige
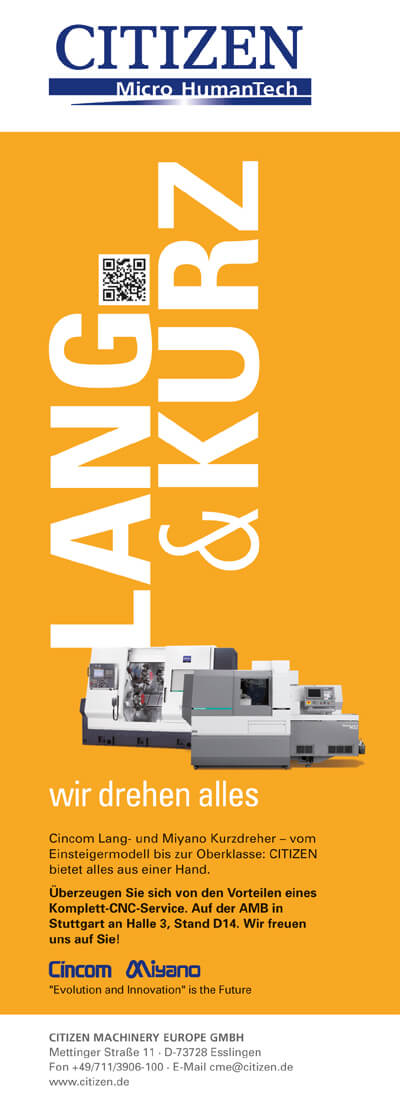