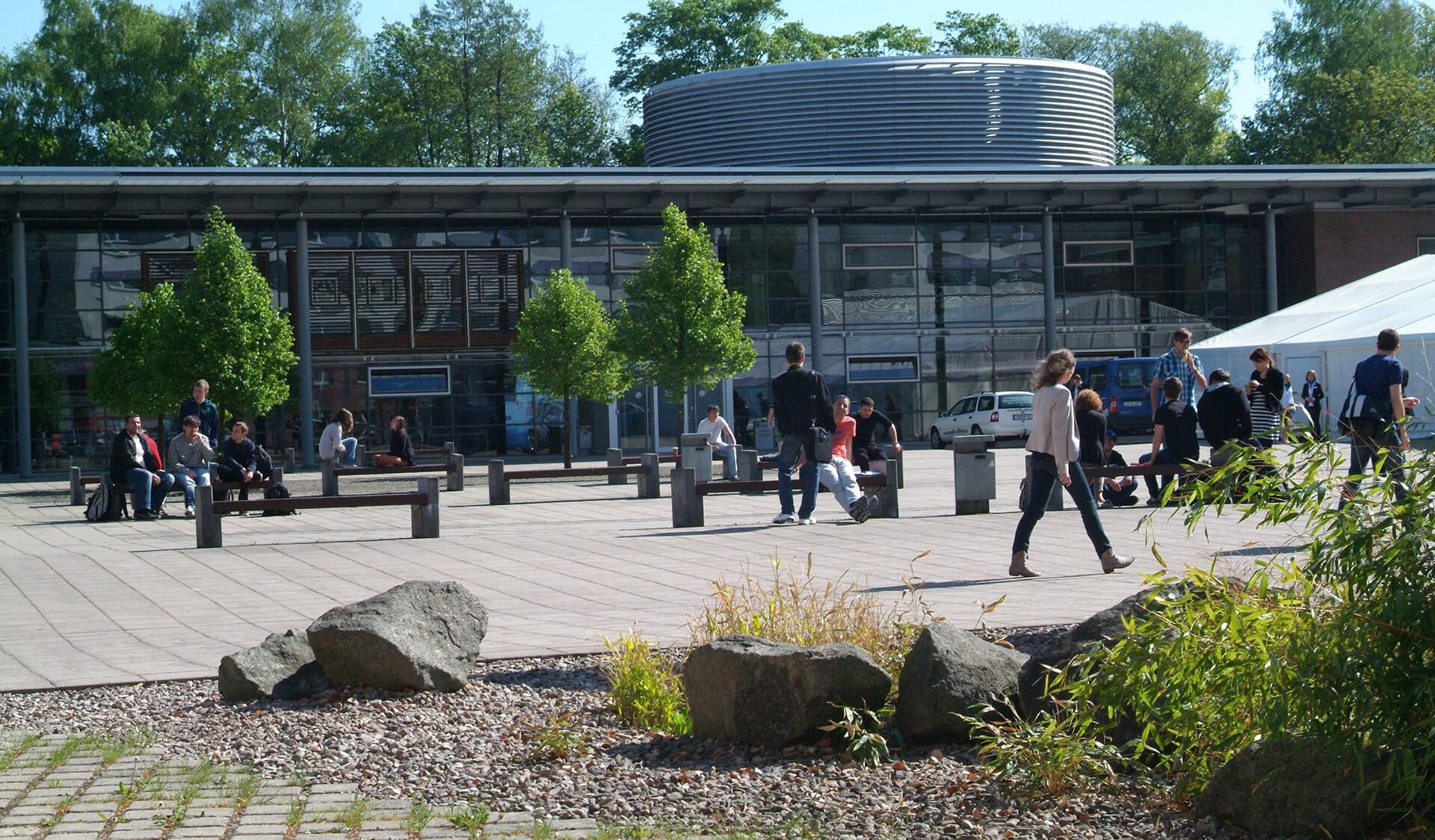
Titelinterview
Additive Fertigung
bleibt ein hybrides Verfahren
Die Auswirkungen der Megatrends sind im Werkzeug- und Formenbau deutlich spürbar, wie Prof. Dr.-Ing. Thomas Seul, Verbandspräsident der deutschen Werkzeug- und Formenbauer (VDWF) bestätigt. Die additive Fertigung hat sich stark entwickelt. Insbesondere die Frage nach dem Nachwuchs und einem Konzept für lebenslanges Lernen beschäftigt den Werkzeug- und Formenbau, wie er im Gespräch mit Georg Dlugosch, Chefredakteur des CNC-Arena eMagazines, erläuterte.
Professor Seul, Sie sind Prorektor für Forschung und Transfer der Hochschule Schmalkalden. Was beschäftigt den Werkzeug- und Formenbau im Blick auf das kommende Jahr?
Seul: Über mein Amt als Prorektor der Fachhochschule in Schmalkalden bin ich auch der Verbandspräsident der deutschen Werkzeug- und Formenbauer und zudem haben wir ein Arbeitsgebiet der angewandten Kunststofftechnik hier in Schmalkalden. Was uns in diesem Jahr und in den kommenden Jahren bewegt, sind Themen der Globalisierung, das heißt, wie können wir uns dem Markt stellen, wie können wir im Endeffekt die Schlagfähigkeit des deutschen Werkzeug- und Formenbaus nach außen hin weiter vertreten und verteidigen? Es ist so, dass der Werkzeug- und Formenbau eine Marke ist, die global bekannt ist. Wie jede Marke ist man dem Wettbewerb ausgesetzt, und entsprechend muss man schauen, wie man dem begegnen kann. Sie wissen sicherlich, dass der Werkzeug- und Formenbau zu 80 Prozent aus Unternehmen besteht, die etwa 25 Mitarbeiter haben, und mit solch einer Mannschaft möchte man natürlich auch die globalen und inländischen Märkte gut bedienen. Es gab einen Strukturwandel, was auch Organisation und Abläufe im Werkzeugbau angeht, das heißt, viel mehr Standardisierung, IT, organisatorische Strukturen, die umgesetzt werden müssten. Zum anderen: Wenn wir mit globalen Märkten Geschäfte machen, müssen wir auch entsprechend nicht nur die Sprache Englisch beherrschen, sei es mündlich als auch in schriftlicher Form, wenn es um Verträge und ähnliches geht, sondern natürlich auch die Kommunikation, das heißt, das ganze Thema Projektkoordination, -durchführung, -überwachung und vor allem auch das Thema der Qualität, Risikobetrachtung, Prozessqualifizierung und -validierung. Das sind wichtige Dinge, die heute auch auf einen Werkzeug- und Formenbauer zukommen, wenn er im globalen Markt bestehen will.
Welche Megatrends beobachten Sie, die die Produktion in Deutschland bestimmen?
Seul: Es sind nicht die Megatrends, die bestimmend sind, sondern es sind die Auswirkungen der Megatrends, die einen Einfluss auf den Werkzeug- und Formenbau haben. Als Beispiel könnte man die Mobilität nennen – und von ihr ausgehend, gibt es vielleicht neue Konzepte der Antriebssysteme, der Antriebsstränge und allem, was damit zusammenhängt. Dann ist man ganz schnell beim Leichtbau oder den biobasierenden Kunststoffen. Das hat wiederum auf die Werkzeugtechnologie Auswirkungen. Das heißt, es muss neue Werkzeugkonzepte geben, die mit diesen neuen Werkstoffen klar kommen und Serienprodukte fertigen können.
Wenn man diesen Gesichtspunkt auf den Leichtbau anwendet: Was ist die Auswirkung auf den Werkzeugbau?
Seul: Da muss man beispielsweise auf die Kunststoff-Weltleitmesse K schauen. Es sind immer mehr thermoplastische, faserverstärkte Kunststoffe, die eingesetzt werden, oder auch Faserverbundstrukturen, die mit duroplastischer Matrix verwendet werden – das hat natürlich Auswirkungen auf den Werkzeugbau und das Werkzeugkonzept. Aber es kann auch sein, dass es nur ein Hype ist – das wird sich zeigen, aber viele Unternehmen beschäftigen sich mit diesem Thema.
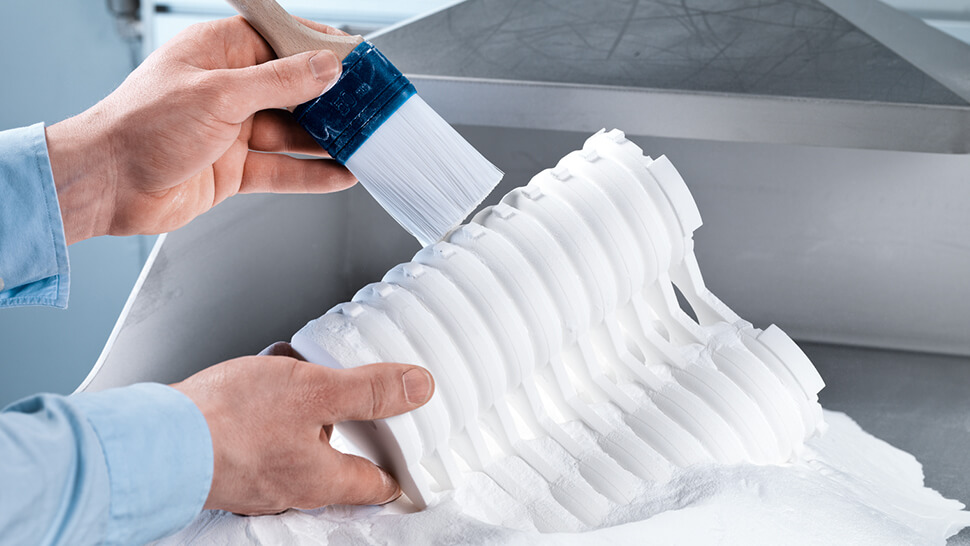
Ein Bauteil wird von dem Pulver befreit, aus dem es entstanden ist: Rapid Manufacturing hat die Fertigungsvoraussetzungen für den bionischen Handling-Assistenten von Festo geschaffen. Das generative Verfahren erlaubt die Herstellung individueller, beweglicher Systemteile aus Polyamid und macht das individuelle 3D-Drucken von komplexen Produkten möglich. Foto: Festo
Auch die additive Fertigung hat im Moment eine sehr starke Beobachtung gefunden. Sehen Sie das auch als eine Spitze an, oder handelt es sich um einen Trend, der im Maschinenbau noch zunehmen wird?
Seul: Ich verfolge diesen Trend schon sehr lange. Ich bin schon lange in diesem Geschäft, sicherlich seit mehr als 16 Jahren, und die additive Fertigung wird meines Erachtens auch in Zukunft immer eine Art hybrides Fertigungsverfahren bleiben, welches den traditionellen oder konventionellen Werkzeugbau ergänzt, aber nie ersetzen wird.
Wo sind die Stärken der additiven Fertigung?
Seul: Wenn wir daran denken, dass wir Werkzeugkonzepte haben, bei denen wir bestimmte Konturen brauchen wie Kühlkanäle und ähnliches um beispielsweise konturnahe Kühlung unterzubringen, dann hat sich innerhalb der letzten fünf Jahre sehr, sehr viel getan, aber es wird meines Erachtens nie so sein, dass wir eine Form zum Beispiel für Mineralwasserkästen in den additiven Fertigungsverfahren herstellen können. Da sind die konventionellen Verfahren viel genauer, stabiler, robuster und natürlich preiswerter.
Diese Fertigungstechnologie hat sicherlich auch ihre Schwächen?
Seul: Nein, ich rede gar nicht von einer Schwäche. Warum muss man immer von der Schwäche eines Verfahrens sprechen? Viel intelligenter ist es, das Positive zusammenzutragen und dann die Karten neu zu legen. Es geht nicht um Schwächen.
Was beschäftigt den Formenbau aus Ihrer Sicht?
Seul: Das sind die Themen, die wir zu Anfang angesprochen haben. Ein ganz wichtiges Thema ist natürlich, wie kriegen wir es hin, dass wir auch in Zukunft Mitarbeiter haben, die es verstehen, Werkzeuge intelligent aufzubauen. Das Geheimnis des Werkzeug- und Formenbaus liegt mit Sicherheit auch in einer intelligenten Konstruktion. Die Werkzeuge werden immer komplexer, das heißt, sie müssen flexibler und präziser sein, es gibt ressourcenschonende Aspekte, die auch ein Werkzeug enthalten muss, und die Technologien, die eingesetzt werden – seien es moderne Fertigungsverfahren oder komplexe, dreidimensionale Berechnungsprozesse – alles das muss natürlich auch ein Konstrukteur beherrschen, und das Thema Nachwuchs, Nachwuchsförderung und insbesondere das lebenslange Lernen. Wir haben eine erstklassige Erstausbildung im Formen- und Werkzeugbau, aber was passiert nach der Erstausbildung? Es sind sehr wenige Ingenieure im Formen- und Werkzeugbau unterwegs. Das heißt, wie können wir eine intelligente Weiterbildung, ein lebenslanges Lernen auf die neuesten Technologien abstimmen, um so auch wettbewerbsfähig zu sein. Das ist eines der wichtigsten Themen überhaupt.
Sehen Sie besondere Ansätze, um Fachkräfte zu fördern oder überhaupt erst anzusprechen?
Seul: Da hat der VDWF, der Verband der Werkzeug- und Formenbauer, eine Ausbildungsinitiative gegründet, die sich insbesondere um die Erstausbildung kümmert, und es wird für den Werkzeug- und Formenbau auch ein Studium angeboten, wo ich Studenten habe, die zwischen 25 und 60 Jahren alt sind, die dort die neuesten Technologien, aber auch die neuesten Managementstrukturen in der Lehre vorfinden. Das wird sehr gut angenommen. Diese Studiengänge sind berufsbegleitend, wozu man auch kein Abitur braucht, sondern nur eine Berufserfahrung. Entsprechend ist das sehr anwendungsnah, was dort gelehrt wird.
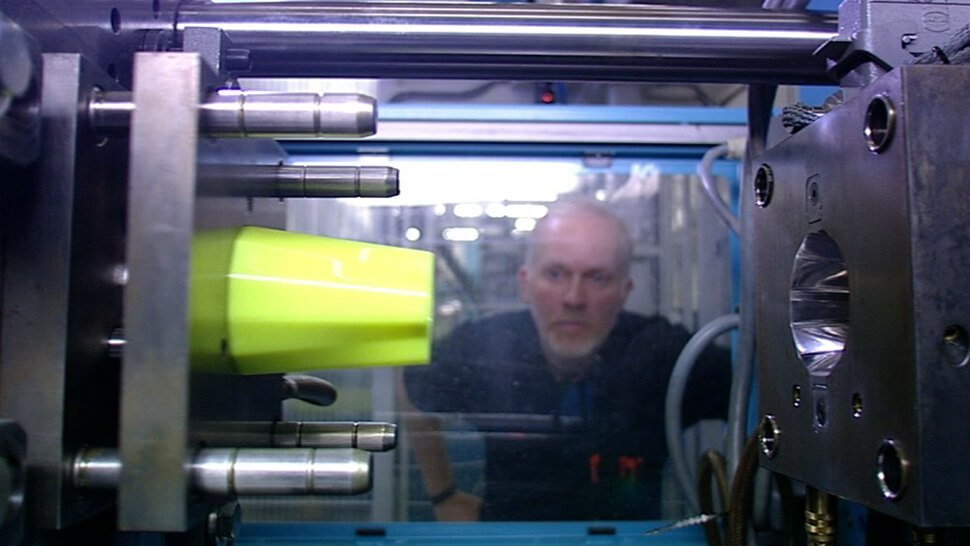
Konturnahe Kühlkanäle sorgen für schnelle Zykluszeiten bei der Herstellung eines Plastikbechers. Foto: EOS
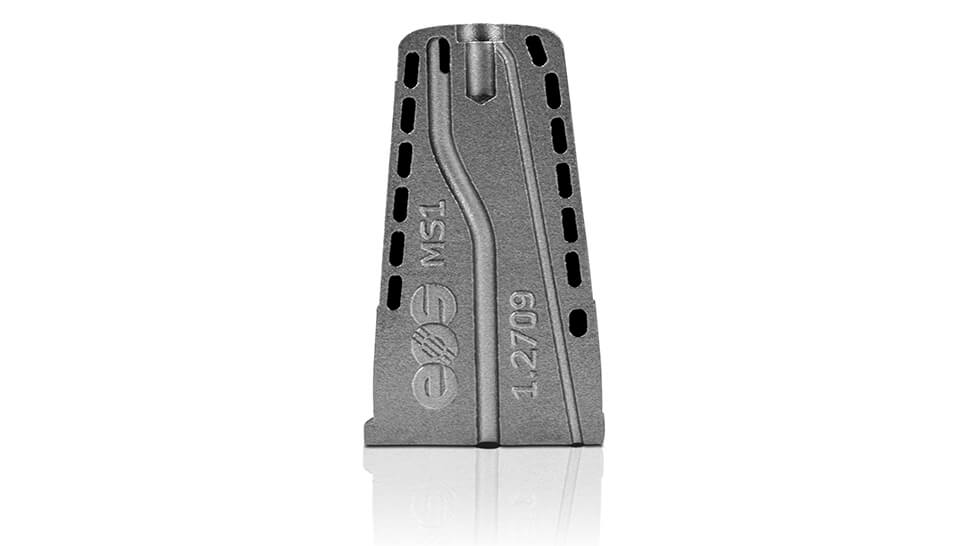
Erst mit Hilfe von Rapid Manufacturing ist die Gestaltung des Werkzeugs für die Herstellung von Plastikbechern in dieser Form möglich geworden. Die Kühlkanäle ziehen sich spiralförmig durch die Form. Foto: EOS
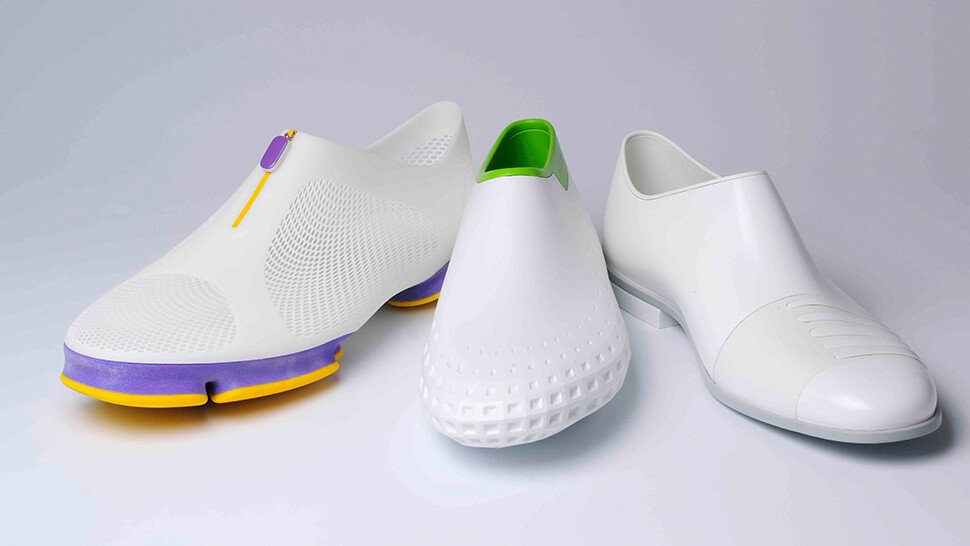
Schuhe oder Kleidungsstücke aus dem Drucker gehören zu den jüngsten Entwicklungen der additiven Fertigung. Das Produkt entsteht, indem Schicht für Schicht aufgetragen und das Pulver mit einem Laser verschmolzen wird. Bild: Barbara Neumann/Messe Erfurt
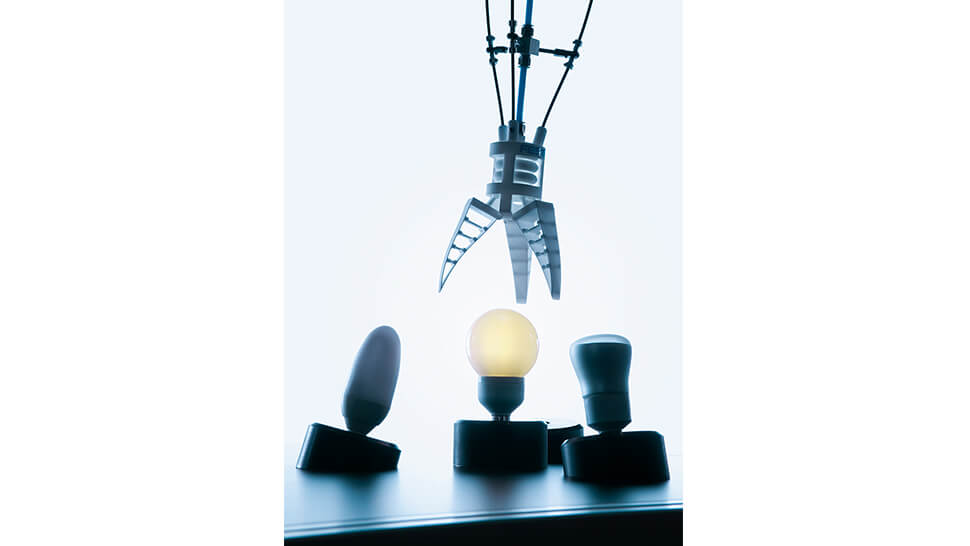
Von der Fischflosse zum BionicTripod: Durch die Reduzierung der zu bewegenden Masse mit Hilfe der additiven Fertigung ist der BionicTripod 2.0 effizient im Verbrauch und kann sich energieeffizient bewegen. Foto: Festo
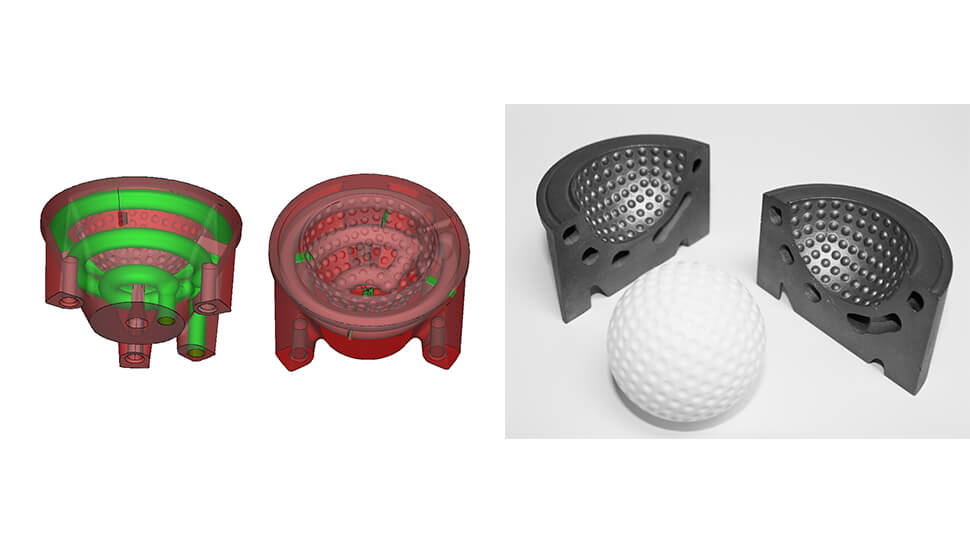
Konturnahe Kühlung verhindert den Verzug von kugelförmigen Spritzlingen. Dadurch wurde die Zykluszeit bei der Herstellung der Golfbälle deutlich reduziert. Bilder: EOS
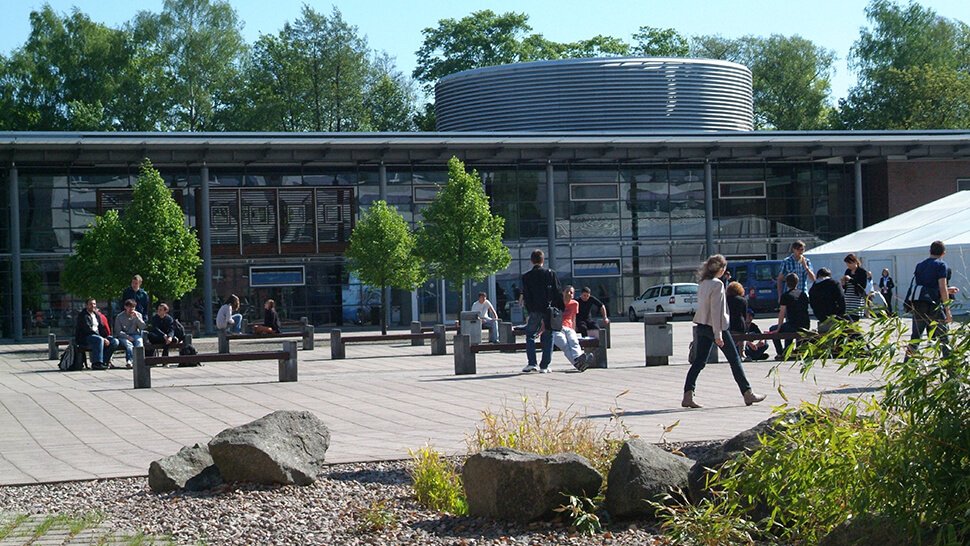
Foto: FH Schmalkalden
Und ist auch nicht nur auf die Jugend bezogen?
Seul: Nein, nein. Meine Studenten sind zwischen 25 und 60, mit einer Riesen-Berufserfahrung, und Sie wissen sicherlich auch aus Erfahrung, dass es sehr wichtig ist, sich auch mit 30, 40 oder 50 Jahren in den Technologien weiterzubilden, wenn man noch mitreden möchte.
Das ist sicherlich der Punkt, der in die Zukunft führen wird?
Seul: Definitiv. Da beneiden uns auch andere Länder definitiv drum. Vom Verband her machen wir immer so genannte Delegationsreisen, bei denen wir in andere Länder schauen, sei es Japan, Südafrika oder die Türkei. So ein Ausbildungssystem, wie wir es jetzt hier in Deutschland haben, auch mit dem großen Schwerpunkt der Ausbildung in Aachen am WZl, dem Werkzeugmaschinenlabor der RWTH, was Großwerkzeugbau und Werkzeugbaustrategien angeht. Das ist sicherlich ein Unikat, welches wir eindeutig global verteidigen müssen.
Im Blick auf den Formenbau gilt es sicherlich, auch Aspekte der Serienfertigung stärker zu berücksichtigen. Welche Voraussetzungen sehen Sie?
Seul: Ein Spritzgießwerkzeug oder auch ein Stanz- und Umformwerkzeug sind ja immer ein Unikat. Wenn man Glück hat, muss man zwei oder drei so genannte Copy-Tools herstellen, aber strategische Prozesse bedeuten auch Standardisierung. Dort gibt es einige Unternehmen, die sehr stark sind. Ich denke, dieser Trend zur Standardisierung und Automatisierung wird auch im Werkzeugbau immer mehr Einzug finden. Das hat auch mit sehr kurzen Lieferketten zu tun, die dann entsprechend bedient werden müssen, weil der Werkzeugbau per se immer unter Zeitdruck ist, für FOT oder SOP sehr schnell agieren muss. Die Werkzeuge müssen ja innerhalb von wenigen Wochen, zwischen 12und 16 Wochen, betriebsbereite Produktionsmittel sein. Entsprechend muss alles, was damit zusammenhängt wie Heißkanalsysteme, Standard- oder Normbauteile, fertig sein. Das muss alles Hand in Hand gehen.
Gibt es noch einen Aspekt, den Sie ansprechen möchten?
Seul: Ich gehe davon aus, dass das ganze Thema Mikroelektronik, mikroelektronische Systeme – so genannte Embedded Systems – immer mehr Einzug finden wird in den Werkzeug- und Formenbau. Das hat auch mit robusten Prozessen und Routinen zu tun. Wir haben Forschungstätigkeiten in diesem Bereich, die wir auch weiter verfolgen werden. Ich gehe davon aus, dass wir solche Systeme – Bussysteme oder Sensortechnologien – in Zukunft im Werkzeug haben werden, so ähnlich wie wir es im Kraftfahrzeug haben. Also, dass das Werkzeug von sich aus sagt, wann es gewartet werden muss, wie mit ihm umgegangen wurde, dass es in einem bestimmten Betriebspunkt gefahren wurde. Das wird man sicherlich in Zukunft in einem qualifizierten und validierten Verfahren – im Spritzguss oder Umformverfahren – wiederfinden, weil wir immer mehr robuste Anlagen und Systeme liefern müssen. Ein Werkzeug ist ja nur Teil einer Prozesskette, und dieses Teil muss 24 Stunden an sieben Tagen in der Woche funktionieren. Das geht natürlich nur, wenn man diese Routinen, die man anbietet, auch beweist.
Kontakt
Prof. Dr.-Ing. Thomas Seul
Prorektor für Forschung und Transfer
Fachhochschule Schmalkalden
Tel. +49 36 83 / 688-1004
E-Mail senden