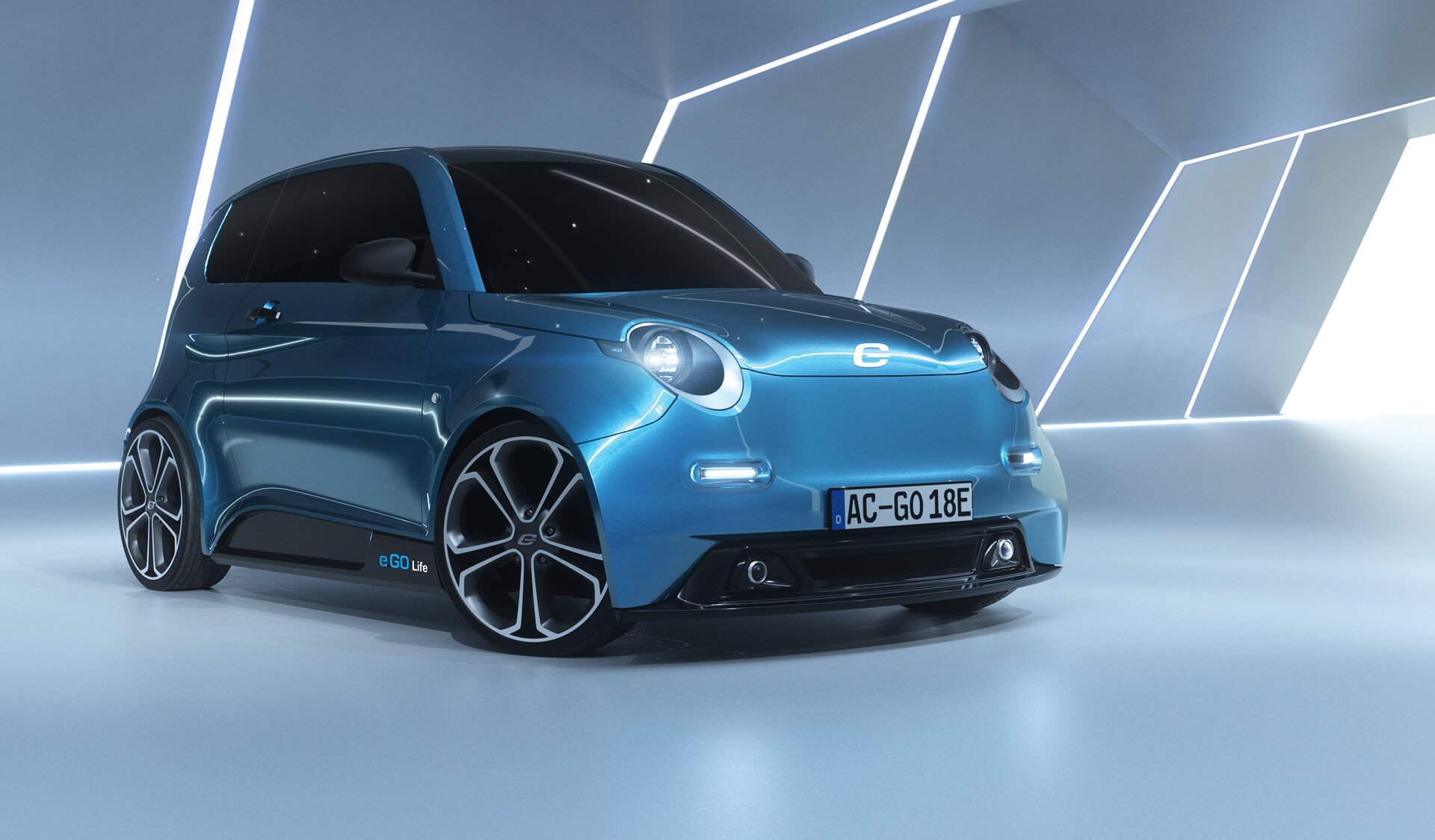
Forschung
Bezahlbare E-Mobilität durch Industrie 4.0
Premiere beim Aachener Werkzeugmaschinen-Kolloquium: Mit dem e.GO Life wurde das erste Industrie-4.0-Serienauto vorgestellt. Der e.GO Mobile AG ist es gelungen, auf dem RWTH Aachen Campus ein besonders günstiges Elektrofahrzeug zu entwickeln. Damit zeigen die Produktionsforscher um Prof. Günther Schuh, CEO der e.GO Mobile AG, Direktor des Werkzeugmaschinenlabors (WZL) der RWTH Aachen und des Fraunhofer-Instituts für Produktionstechnologie, dass mit Industrie 4.0 eine kostengünstige Kleinserienproduktion möglich ist. Der e.GO Life ist das erste, mit Industrie 4.0 entwickelte Elektrofahrzeug, das ab April 2018 in Serie produziert wird.
Die Entwicklung erfolgt gemeinsam mit einem Netzwerk aus Wissenschaft und Wirtschaft. Bosch liefert beispielsweise den 48-Volt-Antriebsstrang und übernimmt zusätzlich den After-Sales-Service, der unter anderem die In-Car-Fahrzeugdiagnose, Werkstatttechnik oder Reparaturen über das Bosch-Werkstattnetzwerk umfasst.
Die kostengünstige und schnelle Entwicklung des e.GO Life basiert auf einer agilen Produktentwicklung, die auf einer gemeinsamen, internetbasierenden Plattform stattfindet, über die der aktuelle Stand jeder Komponente in Echtzeit zugänglich ist. Jedes Team kann unmittelbar Änderungen nachvollziehen, die andere Entwicklungsteams vorgenommen haben. Das ist gerade für den Prototypenbau wichtig, da eine schnelle und fehlerfreie Umsetzung von Produktänderungen sowie das Zurückspielen von Fehlern aus der Produktion notwendig sind. So können durch Prototypen Lerneffekte erzielt und schnelle Fortschritte in der Entwicklung ermöglicht werden.
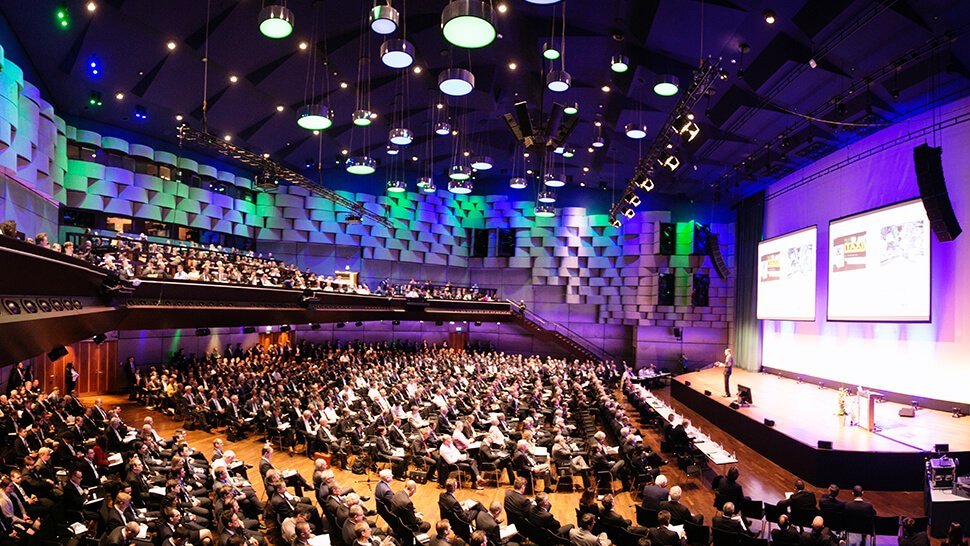
Mehr als 1200 Fachbesucher aus aller Welt nahmen am AWK 2017 teil. Foto: WZL der RWTH Aachen | Strauch
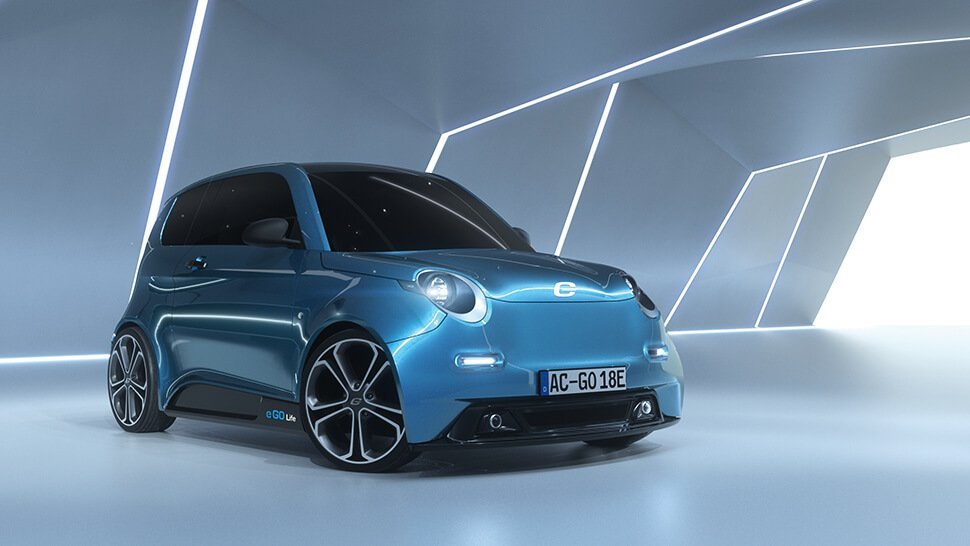
Das erste Serien-Elektrofahrzeug nach dem Maßstab von Industrie 4.0 wurde auf dem RWTH-Campus entwickelt. Foto: e.GO Mobile
In der frühen Phase der Produktentwicklung sind die Anforderungen an ein Produkt oft unklar oder volatil. Klassische, phasenorientierte Entwicklungsprozesse wie der Stage-Gate-Prozess kommen schnell an ihre Grenzen. Produktänderungen, die in einer späten Entwicklungsphase auftreten, können nur noch schwer berücksichtigt werden. So sind klassische Entwicklungsansätze geprägt von Suchen und Warten. Anders ist das bei agilen Entwicklungsansätzen, wie sie beispielsweise aus der Software-Industrie bekannt sind.
Auf die Entwicklung mechatronischer Produkte angewandt, stellen sie einen vielversprechenden Ansatz dar, um diese Randbedingungen handhabbar zu machen. Hierfür wurde am WZL eine eigene Methodik entwickelt, nach der die Definition der so genannten User-Story Startpunkt der Entwicklung ist. So kann ein Lösungsraum für Innovationen gezielt an den Nutzeranforderungen ausgerichtet werden. In klassischen Entwicklungsprojekten ist hingegen die Vollständigkeit des Lastenheftes zu Beginn eine notwendige Voraussetzung für die Fortsetzung des Projektes.
Anzeige
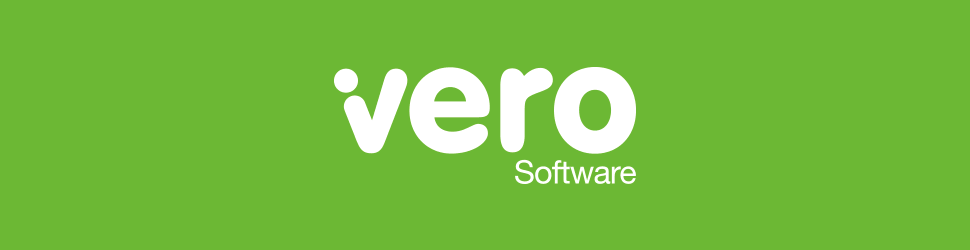
In agilen Entwicklungsprojekten definiert die Beantwortung priorisierter Fragestellungen ein neues Verständnis von Vollständigkeit. Für die agile mechatronische Produktentwicklung ist es darüber hinaus besonders wichtig, mit der zunehmenden Interdisziplinarität durch eine entsprechende Teamzusammensetzung umzugehen. Kurzzyklische Abstimmungen in Stand-up-Meetings helfen, alle Beteiligten mit den relevanten Informationen zu versorgen und das oft vorhandene Arbeiten und Denken in Silos zu beenden. Die Transformation zum agilen, lernenden Unternehmen bricht gewohnte Denkmuster auf und ermöglicht neue Lösungsräume für Innovationen.
Dieses Vorgehen der agilen mechatronischen Produktentwicklung erfordert allerdings, mehrere Prototypen herzustellen, um die geforderten Funktionen auf Machbarkeit prüfen zu können. Dabei ist es entscheidend, dass die sich ändernden Produktanforderungen schnell und fehlerfrei an die Produktion übergeben werden. Hierfür stoßen Konstruktionsänderungen – so genannte Change Requests – Änderungen am Produkt während der Entwicklung oder nach bereits erfolgter Freigabe zur Herstellung an.
Heutzutage ist die Umsetzung dieser Change Requests noch von zu vielen Schnittstellen im Prozess zwischen Entwicklungs- und Produktionsabteilungen geprägt. Informationen sind in unterschiedlichen proprietären Systemen gespeichert, auf die nicht alle Anwender zugreifen können. Aktuell sind Unternehmen noch nicht in der Lage, einen schnellen und gleichzeitig qualitätsgesicherten Change Request durchzuführen. Soll eine Änderung möglichst schnell umgesetzt werden, scheitert es häufig an nicht nachvollziehbar dokumentierten Informationen.
Um Change Requests zukünftig fehlerfrei bearbeiten zu können, wird eine weitestgehend automatisierte Informationslogistik benötigt, die sich mit der Bereitstellung der benötigten Daten und Informationen in adressatengerechter Form befasst. Die drei Erfolgsprinzipien sind ein fehlerfreier Zugang zu allen benötigten Informationen, konsistente Daten trotz mehrerer Bearbeiter und die Priorisierung von benötigten Informationen.
Dazu wird eine neue Infrastruktur für die Daten der Produktionstechnik benötigt – das Internet of Production. Es ermöglicht produzierenden Unternehmen, Daten verschiedener proprietärer Systeme zu verknüpfen, und befähigt sie außerdem, fundierte Entscheidungen auf Basis von Daten und Informationen aus den unterschiedlichen Domänen der Produktionstechnik zu treffen. Hierfür müssen sowohl Daten aus der Entwicklung und Produktion als auch produktionstechnisches Vorwissen durch Experten verfügbar gemacht werden.
Dann nämlich ermöglicht das Internet of Production eine echtzeitfähige, sichere Informationsverfügbarkeit zu jeder Zeit an jedem Ort. Generierte Informationen werden zum digitalen Schatten der Produktion verdichtet, der über kontinuierliche Datenanalysen Mustererkennungen ermöglicht. So entsteht eine Prognosefähigkeit für die beherrschte Produktion. Der Wettbewerbsvorteil durch aggregierte Informationen in Echtzeit ermöglicht neue Dimensionen der Agilität.
Kontakt
Prof. Dr.-Ing. Günther Schuh
Werkzeugmaschinenlabor WZL der RWTH Aachen Tel. +49 241 80-27404 E-Mail senden