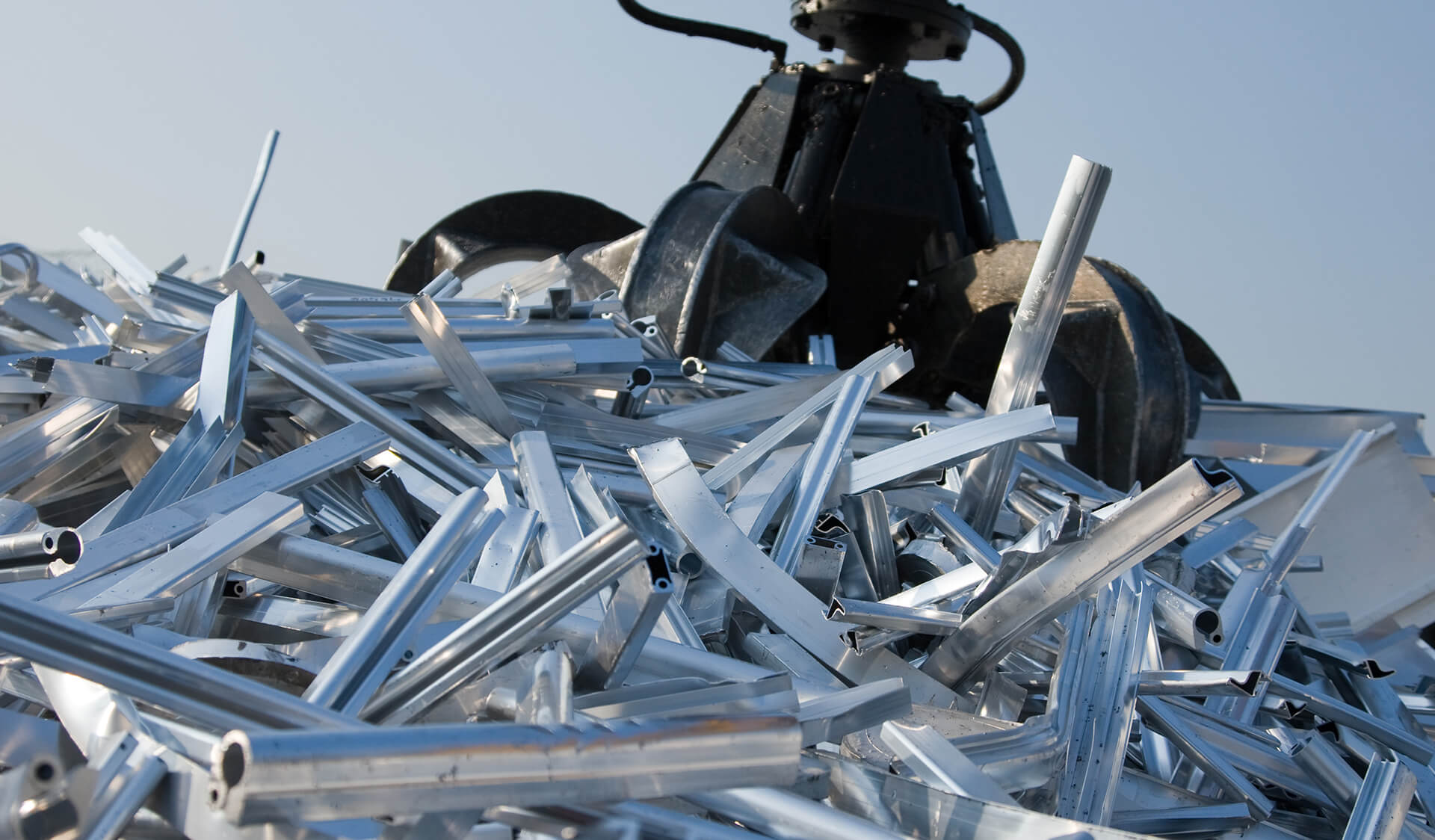
Titelthema
Aluminium ist ein Trumpf
Als Konstruktionswerkstoff ist Aluminium ein Synonym für automobilen Leichtbau. Dass die Entwicklung nicht stillsteht und das Leichtbaupotenzial des NE-Metalls noch lange nicht gehoben ist, machten Experten aus Wissenschaft und Industrie am Beispiel innovativer Ergebnisse aus Forschung und praxisnaher Zusammenarbeit während des AMAP-Forums in Aachen deutlich.
Leichtmetalle wie Aluminium und Magnesium sind bestens geeignet, die zunehmenden Anforderungen künftiger Fahrzeuggenerationen zu erfüllen: Einhaltung der Emissionsobergrenzen bei Autos mit klassischem Verbrennungsmotor und Forderungen der Verbraucher nach mehr Reichweite bei Elektrofahrzeugen zu bezahlbaren Kosten.
Höhere Festigkeit bei geringerem Gewicht
Die Bedeutung von Aluminium als Konstruktionswerkstoff hat über die vergangenen Jahrzehnte kontinuierlich zugenommen. Heute ist ein Pkw in Europa im Durchschnitt mit mehr als 150 Kilogramm Aluminium unterwegs, wobei der Löwenanteil des NE-Metalls mit knapp 100 Kilogramm auf Guss für Motor- und Antriebsstrang entfällt sowie auf die Räder.
Automobiler Leichtbau mit einer Karosserie vollständig aus Aluminium war lange Zeit Premiummarken wie Jaguar vorbehalten. Der Durchbruch in den Volumenmarkt gelang Ford 2015 in den USA mit der Neuauflage des Klassikers F-150, wie Dr. Jürgen Wesemann vom Ford-Forschungszentrum in Aachen berichtete. Der Pick-up-Truck mit seiner Leichtbaukarosserie aus hochfestem Aluminium markiert die Abkehr von der jahrzehntelang eingesetzten Stahlbauweise bei diesem in Amerika geradezu legendären Fahrzeug. In Europa so gut wie unbekannt, sind Pick-up-Trucks der F-Serie in den USA seit 36 Jahren die bestverkauften Fahrzeuge.
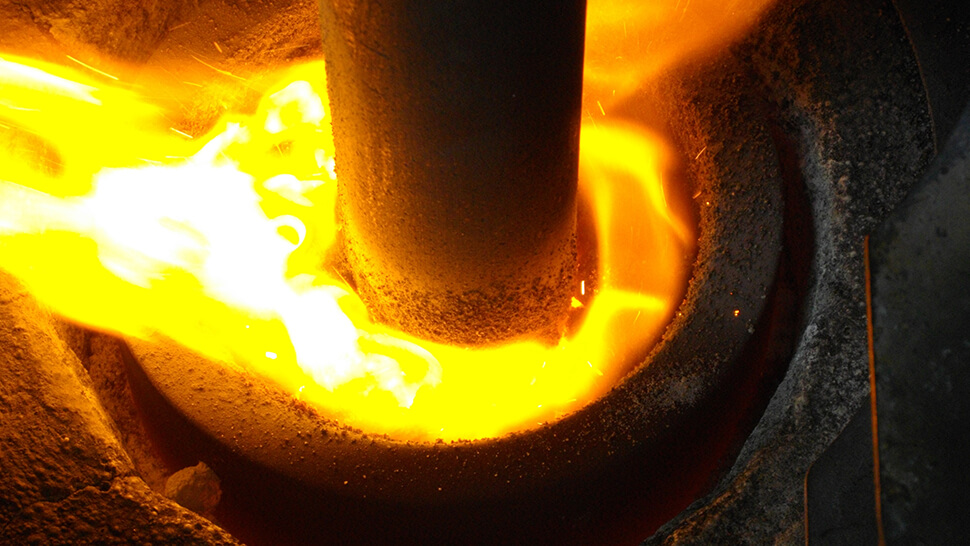
Fotos: Marcel Dohmen, pictures of life
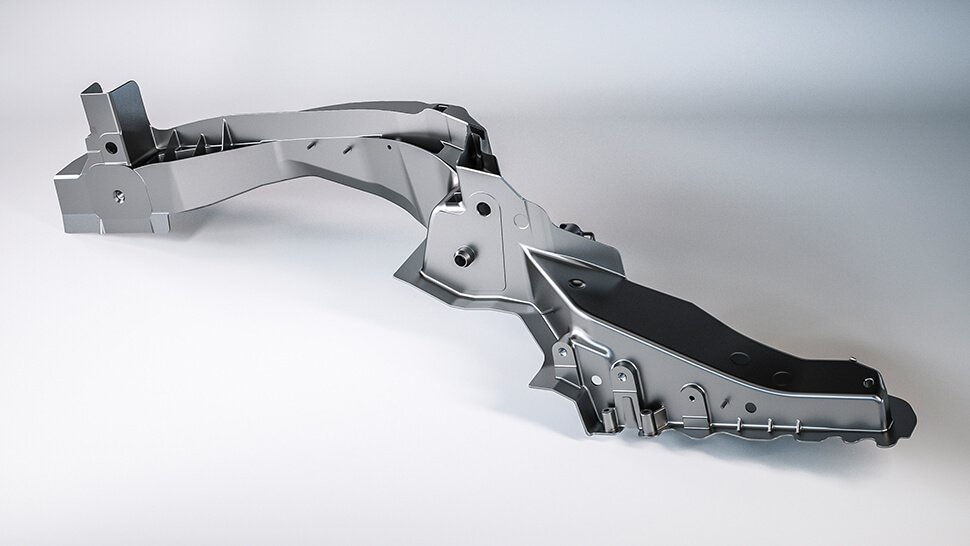
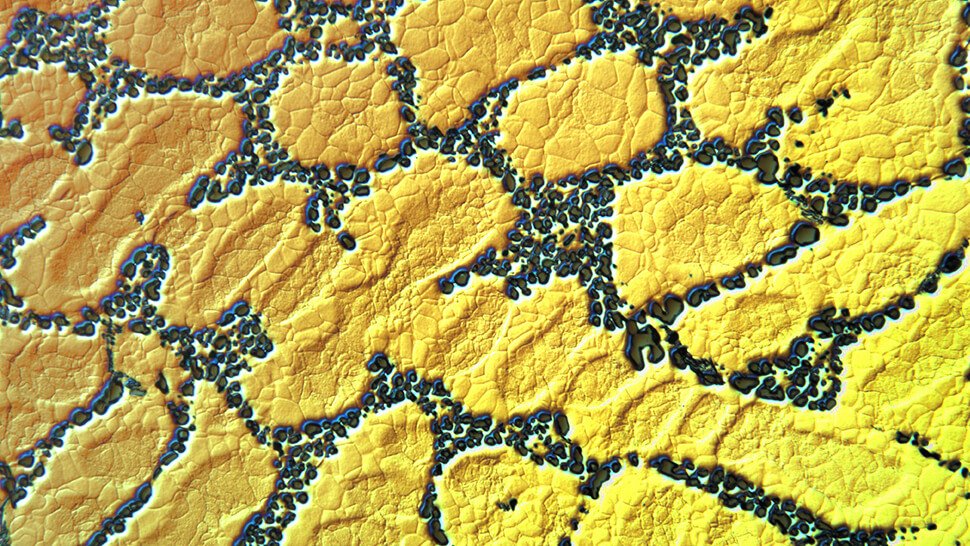
Durch die Verwendung hoch- und höchstfester Aluminiumlegierungen in Form von Blechen und Strangpressprofilen ist die Rohkarosserie des F-150 um 45 Prozent leichter, als das Vorgängermodell in Stahlbauweise. Bezogen auf Nutzlast und Zugkraft hat der Pick-up-Truck mit Benzinmotor den Best-in-Class-Kraftstoffverbrauch. Für die aluminiumintensive Bauweise spielt das Beherrschen der richtigen Fügetechnologie eine wesentliche Rolle.
Künftige Forschungsschwerpunkte sieht der Ford-Experte beispielsweise in der Entwicklung neuer hochfester Aluminiumlegierungen zur Fortsetzung der Gewichtsreduzierung, maßgeschneiderte Werkstoff- und Bauteileigenschaften und in der Weiterentwicklung fortschrittlicher Gusstechnologien mit dem Ziel weiterer Gewichtseinsparung und Kostenreduzierung. Auch bei den Fügeverfahren besteht nach seiner Ansicht Entwicklungspotenzial. So befasste sich Ford im Rahmen eines AMAP-Projekts zusammen mit dem RWTH-Institut für Schweiß- und Fügetechnik (ISF) mit dem Fügeverfahren Refill Friction Stir Spot Welding. Wichtige Bausteine wirtschaftlicher Aluminium-Leichtbaulösungen seien zudem CAE und virtuelle Optimierung. Erfolgreicher Leichtbau ist nicht nur dem Konstruktionswerkstoff Aluminium geschuldet, fasst Wesemann zusammen. Damit aus Innovationen erfolgreiche Produkte und Lösungen werden, ist eine enge Zusammenarbeit von Werkstoffforschung, Aluminiumherstellern, Bauteilelieferanten und Automobilindustrie erforderlich. Der Ford-Manager machte deutlich, dass nur ein ganzheitlicher Ansatz über die gesamte Wertschöpfungskette von Aluminium zum Ziel führt – ein Ansatz wie ihn das Forschungscluster AMAP verfolgt.
Maßgewalzte Aluminiumbleche
Ein Beispiel für innovative Aluminiumtechnologien liefert Dr. Udo Brüx, Leiter Leichtbauzentrum Mubea. Der Automobilzulieferer arbeitet in einem AMAP-Projekt gemeinsam mit Ford und dem Aluminiumhersteller Constellium daran, die ursprünglich für Stahlblech von Mubea entwickelte Technologie des flexiblen Walzens auf Aluminium zu übertragen.
Bei der Technologie zur Herstellung sogenannter Tailor Rolled Blanks (TRB) handelt es sich um einen Kaltwalzprozess, bei dem durch einen veränderlichen Walzspalt variable Blechdicken entsprechend der lokal geforderten Festigkeiten und Steifigkeiten eingestellt werden. Diese innovative Technologie für maßgeschneiderte Material-Lösungen erlaubt bei Stahl Dickenunterschiede bis zu 50 Prozent innerhalb eines Bauteils.
Ziel des Forschungsvorhabens ist eine industrielle Fertigung von maßgeschneiderten Blechen zur Realisierung gewichtsoptimierter Strukturbauteile aus hochfestem Aluminium. Dazu wird die gesamte Prozesskette betrachtet: Vom Flexwalzen über die Wärmebehandlung und die Kaltumformung sowie die künstliche Alterung des Bauteils bis hin zur Fügetechnik. Begleitet wird die Entwicklung durch umfangreiche Methoden zur Materialcharakterisierung und Prognose des Umformverhaltens bis hin zum Crashverhalten des Bauteils.
Die Ergebnisse des flexiblen Walzens mit den bisher eingesetzten Aluminiumlegierungen sind vielversprechend. Nach entsprechender Wärmebehandlung erreicht das Material eine hohe Festigkeit bei ausreichender Duktilität.
Additive Fertigung mit Aluminium
Mit Aluminium-Legierungen für additive Fertigung befasst sich Dr. Andreas Weisheit vom Fraunhofer-Institut für Lasertechnik ILT. Der Fraunhofer-Forscher betrachtete dabei die beiden Verfahren Laser Powder Bed Fusion (L-PBF) und Laser Metal Deposition (LMD).
Beim L-PBF-Verfahren, einem selektiven Laserstrahlschmelzen wird eine 30-50 Mikrometer dünne Schicht Metallpulver flächig auf einer Bauplattform aufgetragen und vom Laser entsprechend den CAD-Daten schichtweise geschmolzen. Die Plattform wird abgesenkt, eine neue Schicht Metallpulver aufgetragen und der Vorgang wiederholt. Das fertige Bauteil wird dem Pulverbett entnommen.
Beim LMD, einem Laserpulverauftragsschweißen, erfolgt die additive Fertigung mit direktem Metallauftrag. Metallpulver wird über eine Düse zugeführt und mit dem Laser geschmolzen. Durch Mehrlagenauftrag entsteht schichtweise das Bauteil.
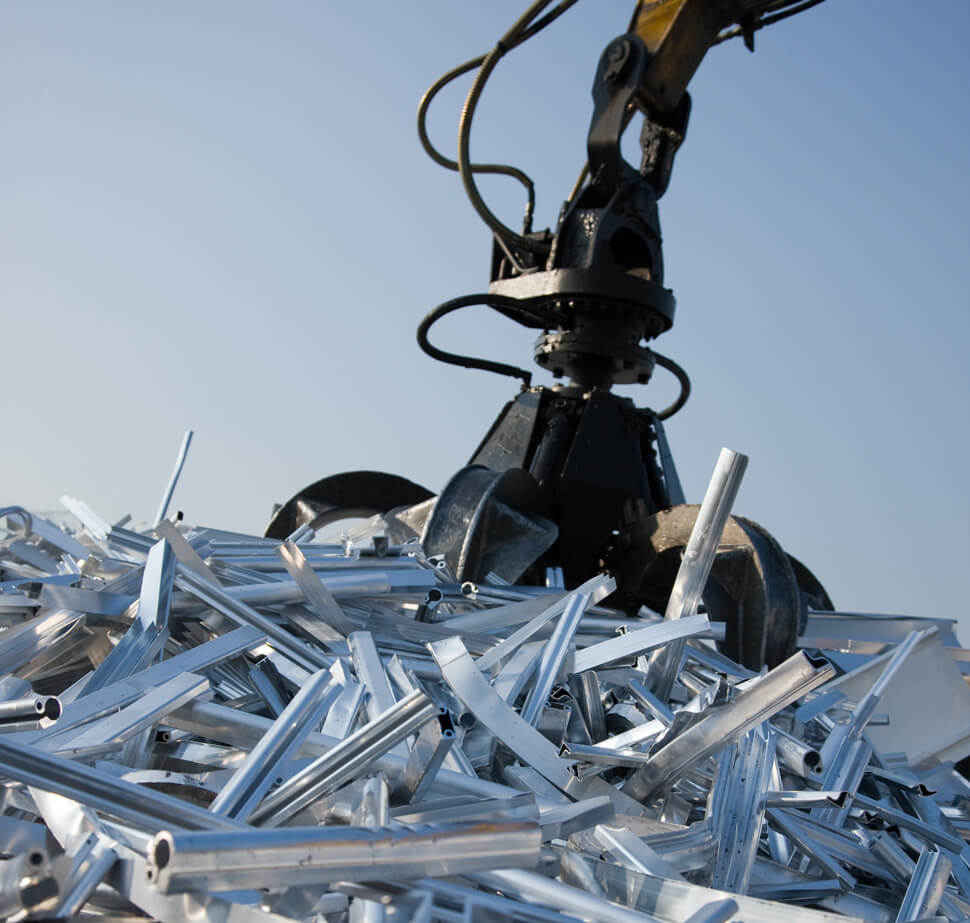
Foto: Marcel Dohmen, pictures of life
Trotz hoher Festigkeit und den hervorragenden Materialeigenschaften: Einem breiteren Einsatz von Hochleistungslegierungen wie Scalmalloy stehen die hohen Kosten gegenüber. Fraunhofer-Forscher Weisheit plädiert daher für weitere Forschungen zur Legierungsentwicklung. Als Legierungselemente könnten an Stelle des teuren Scandiums beispielsweise Nickel (Ni) oder Kalzium (Ca) dienen.
Ende des Jahres soll mit dem Start des BMBF-Projekts MAYFEST zur hybriden Fertigung die Herausforderung angegangen werden. An einem Zylinderkopf als Demonstrator wollen die Partner aus Wissenschaft und Industrie das Zusammenspiel von Gießtechnik und additiver Fertigung mit neuen Legierungen erforschen.
Additive Fertigung in der industriellen Anwendung
Den praktischen Nutzen additiver Fertigung kann der Anlagenbauer SMS am Beispiel eines im 3D-Druck gefertigten Sprühkopfes für Gesenkschmiedepressen unter Beweis stellen. Der Sprühkopf erfüllt beim Gesenkschmieden eine wichtige Funktion: Er entfernt den Zunder von Gesenken, kühlt die Gesenkoberfläche, bringt Schmierstoffe auf und trocknet die Gesenke. Wie Axel Roßbach, Technology Extrusion and Forging Presses SMS Group darstellte, sind die Werkzeugräume von Gesenkschmiedepressen in Teilen geometrisch so komplex, dass die konventionelle Fertigung von Sprühköpfen hier an ihre Grenzen stößt. Die additive Fertigung zeigt genau dort ihre Stärken: Ein geringes Materialgewicht, ein gewichtsoptimiertes Design bei freier Geometrie, denn Material findet sich nur an den Stellen, an denen es gebraucht wird. Die 3D-Sprühköpfe sind extrem leicht, woraus sich Vorteile wie ein geringerer Verschleiß und höhere Taktzeiten beim Schmieden ergeben.
Der 3D-Druck ermöglicht die Fertigung verschiedenster Düsenformen und Ausrichtungen. Die Positionierung der Düsen ist hochflexibel und wird vom Kunden bestimmt, wie Roßbach berichtet. Gleichzeitig haben die 3D-Sprühköpfe eine geringe Bauhöhe, sodass der Werkzeugraum anderweitig genutzt werden kann.
SMS hat ein eigenes Know-how zum Erstellen der 3D-Sprühköpfe entwickelt, dass die Konstruktionszeit auf ein Minimum reduziert, wie Roßbach erläutert. Dank automatisierter Fertigung kann ein Sprühkopf je nach Material über Nacht geliefert werden. Die Sprühköpfe werden nach Kundenwunsch wahlweise in Kunststoff (Polyamid) oder Metall (Aluminium) gefertigt.
Kontakt | Autor
Gerd Krause
Technik- und Wirtschaftsjournalist Krause & Partner Media Redaktionsbüro MEDIAKONZEPT Düsseldorf E-Mail senden
Kontakt | Unternehmen
Dr.-Ing. Rolf Weber
Geschäftsführer AMAP GmbH Aachen Tel. +49 157 30878676 E-Mail senden