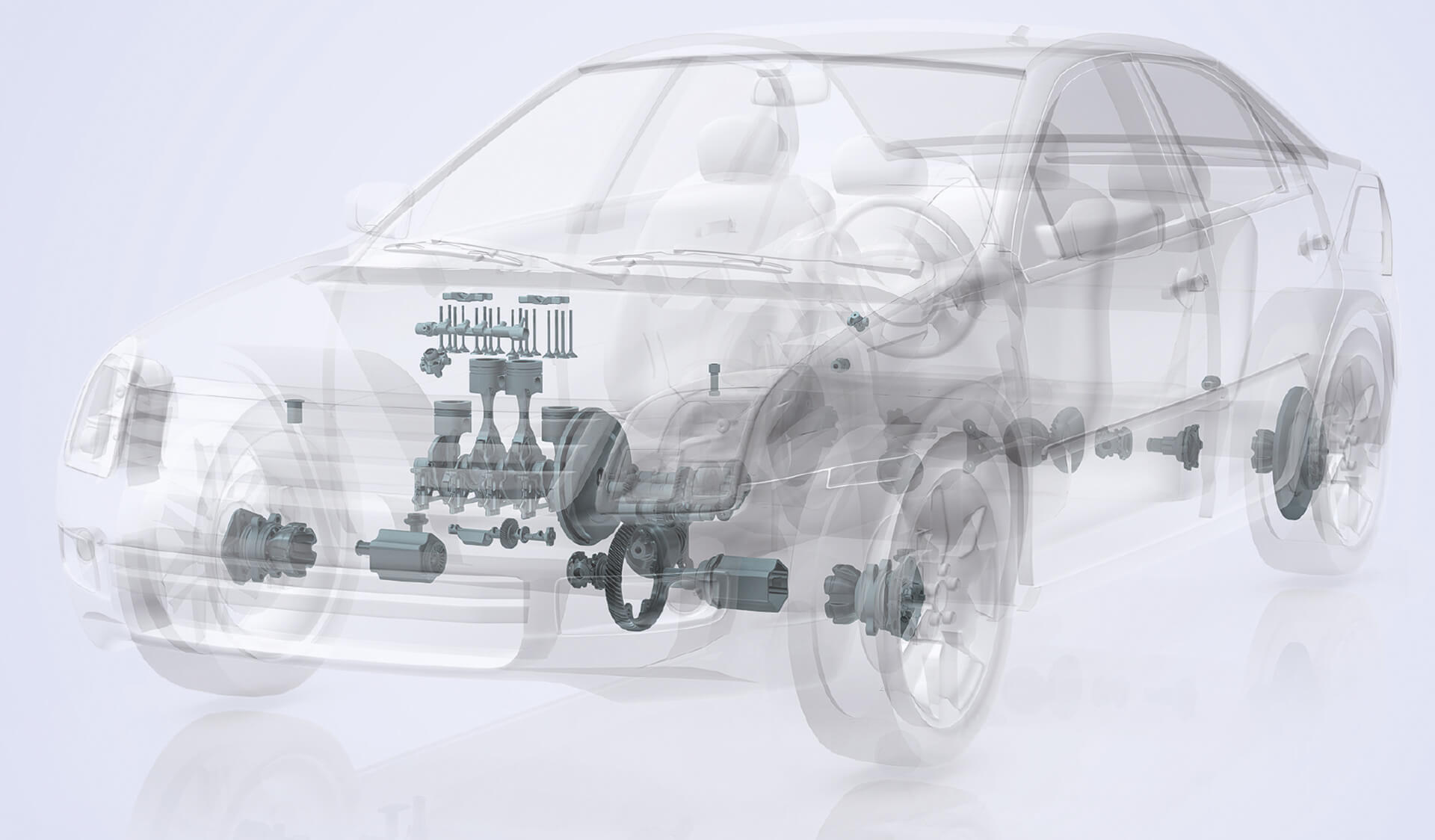
Titelthema
Der Lkw-Antriebsstrang
soll leichter werden
Wie kann das Ziel der Reduzierung von klimaschädlichem CO2-Ausstoß durch die Technologie der Massivumformung unterstützt werden? Dieser Frage gehen seit fast fünf Jahren Unternehmen der deutschen Massivumformung und der Stahlindustrie in der Initiative Massiver Leichtbau nach. Die Kombination von kreativen Ansätzen in Konstruktion und Fertigungsprozessen mit innovativen Stahlwerkstoffen ist der Megatrend des automobilen Leichtbaus. Sie steht im Fokus des Industrieverbands Massivumformung.
Gewichtseinsparungen im Fahrzeug führen zu einer Vielzahl von positiven Effekten wie Minderung des CO2- Ausstoßes, Erhöhung der Fahrdynamik, Schonung von Ressourcen. Sie haben einen positiven Einfluss auf die Fahrsicherheit. Zudem ermöglicht der Leichtbau die Kompensation des Mehrgewichts durch den vermehrten Einsatz von Komfort- und Fahrerassistenzsystemen. Das Thema Leichtbau bestimmt seit vielen Jahren die Diskussion um die Optimierung der zukünftigen Mobilität.
Die Initiative Massiver Leichtbau wurde 2013 von 15 Unternehmen der Massivumformung und neun Stahlherstellern unter der Federführung des Industrieverbands Massivumformung (IMU) und des Stahlinstituts VDEh ins Leben gerufen. In der ersten Phase wurde ein Mittelklasse-Personenkraftfahrzeug analysiert und das Leichtbaupotenzial von 42 Kilogramm für massivumgeformte Bauteile des Antriebsstrangs und des Fahrwerks identifiziert.
Aufgrund des Erfolgs bei den Kunden und in der Öffentlichkeit wurde die Kooperation 2015 mit der zweiten Phase und der Konzentration auf das Leichtbaupotenzial eines leichten Nutzfahrzeugs fortgesetzt. 17 Umformunternehmen, zehn Stahlhersteller und ein Ingenieurdienstleister untersuchten als Referenzfahrzeug ein leichtes Nutzfahrzeug mit 3,5 Tonnen Gesamtgewicht (Nutzlast inklusive). Von 2394 Kilogramm Fahrzeuggewicht entfielen 845 Kilogramm auf massivumgeformte Bauteile, die wiederum ein Einsparpotenzial in Antriebsstrang und Fahrwerk von 99 Kilogramm boten (zwölf Prozent).
Zur Analyse des Verhältnisses zwischen höheren Kosten für Hochleistungsstähle und der daraus resultierenden Gewichtseinsparung wurden Getriebeentwicklungsstudien durchgeführt. So wurden für die untersuchten Getriebe des Pkws und des leichten Nutzfahrzeugs Rechenmodelle erstellt, die über die Verringerung der Größe von Zahnrädern und Wellen aufgrund des Einsatzes höher belastbarer Stähle Einsparungen in Systemgewicht und -größe voraussagen.
Ein zusätzlicher Programmschritt berechnet die Gewichtsnebeneffekte des schrumpfenden Getriebegehäuses. Damit können neben primären Einspareffekten auch sekundäre Gewichtseinsparungen abgeschätzt werden. Zudem zeigen die Untersuchungen auch die Wettbewerbsvorteile zu konkurrierenden Fertigungsverfahren und Werkstoffen auf.
2017 startete die Initiative Massiver Leichtbau in die dritte Phase. Mit dabei sind die Kooperationspartner Industrieverband Massivumformung aus Hagen und Stahlinstitut VDEh aus Düsseldorf sowie 39 Unternehmen aus Westeuropa, Asien und den USA.
Begleitend zu den drei Phasen der Initiative untersucht seit 2015 ein Forschungsprojekt das Leichtbaupotenzial massiv umgeformter Bauteile im Pkw-Antriebsstrang. Zehn Forschungsinstitute und 50 Industrieunternehmen entlang der gesamten Prozesskette entwickeln gemeinsam leistungsfähigere Stähle, optimierte Wärmebehandlungen sowie neue Verfahren und Prozesse in der Massivumformung. Das Abschlusskolloquium mit der Präsentation der Forschungsergebnisse findet am 11. Oktober in Düsseldorf beim Stahlinstitut VDEh statt.
80 Teilnehmer aus den beteiligten Unternehmen haben bei der fka Forschungsgesellschaft Kraftfahrwesen in Aachen das Leichtbaupotenzial von Hybridfahrzeugen – dem allgemeinen Trend zur Elektrifizierung folgend – und schweren Lkws in Antriebsstrang, Fahrwerk und Getriebe untersucht.
Die Initiative will mit beanspruchungsgerechtem, gewichtsminimiertem Bauteildesign und belastungsoptimierten Werkstoffen vorhandenes Leichtbaupotential aufdecken. Zusätzlich ermöglicht die Analyse Einblicke in eine neue, zukunftsweisende Antriebstechnik. Als weitere Ergebnisse werden das Aufzeigen entsprechender Potenziale für die Unternehmen der Massivumformung, Einsatzmöglichkeiten für moderne, innovative Stähle und Stahlhersteller neuer Bauteile sein.
In dieser multilateralen Studie wurden durch die intensive internationale Zusammenarbeit von zehn Stahlherstellern, sieben Maschinenbauern für Umformanlagen, einem Werkzeughersteller und 20 Massivumformern alle Kompetenzen von der Vormaterialherstellung über die Umformung und Bearbeitung von Bauteilen gebündelt.
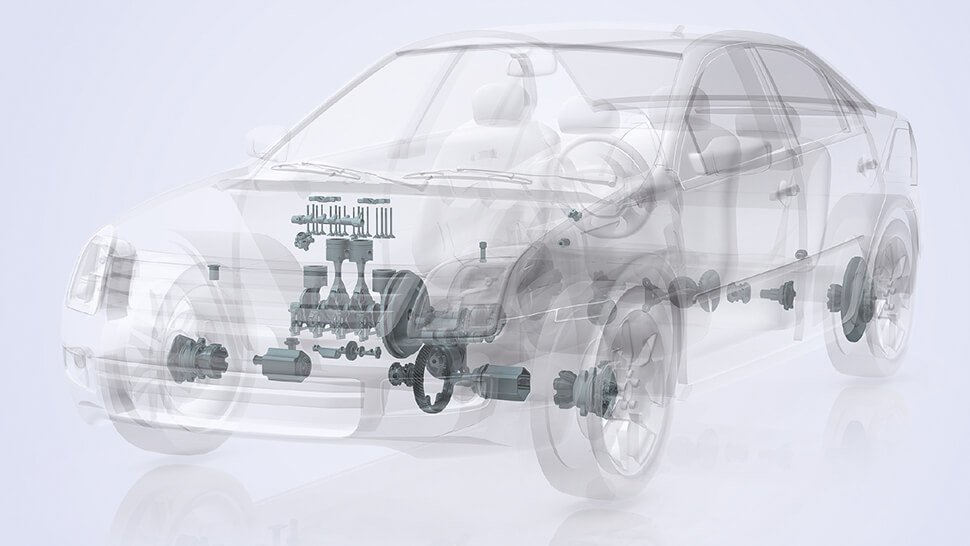
Massivumformung und Stahlindustrie tragen dazu bei, dass Gewicht, Energieverbrauch und CO2-Ausstoß für die Fahrzeugpalette vom Pkw über den Hybrid bis zum schweren Nutzfahrzeug reduziert werden. Bild: IV Massivumformung
Ferner wurde als ein weiterer Schwerpunkt nach der Analyse des Leichtbaupotenzials bei einem Pkw und einem leichten Nutzfahrzeug der Fokus auf ein schweres Nutzfahrzeug gelegt, und zwar auf ein Lkw-Getriebe sowie auf einen Lkw-Antriebsstrang mit Kardanwelle und Differenzial. Auch in dieser Phase wurden alle Leichtbau-Lösungsansätze nach Potenzial, Kosten und Umsetzungsaufwand bewertet. Ebenso wurden Getriebeentwicklungsstudien die primären und sekundären Effekte des Leichtbaus für die Getriebe des Hybrid-Fahrzeugs sowie des Lkws begleitend ermittelt.
Phase I und Phase II haben gezeigt, dass schon belastungsgerechte hochfeste Stähle auf dem Markt sind, um Getriebe leichter und effizienter auszulegen. Die Projektkooperation will in einer weiteren Studie die Frage klären, welche Maßnahmen zur Einführung von neu entwickelten höherfesten Getriebestählen beim Kunden zu ergreifen sind.
Mit diesem Gesamtpaket an Maßnahmen tragen Massivumformung und Stahlindustrie dazu bei, dass Lösungsansätze zur deutlichen Minderung des Gewichts, des Energieverbrauchs und des CO2-Ausstoßes für die gesamte Fahrzeugpalette vom Pkw bis zum schweren Nutzfahrzeug bereit stehen.
In Phase III wurden mehr als 3600 Komponenten aus Antrieb, Fahrwerk und Elektronik des Hybridfahrzeugs untersucht und insgesamt 732 Leichtbauideen entwickelt. Im Zuge der Studie wurde ein Leichtbaupotenzial für das Hybridfahrzeug von 93 Kilogramm identifiziert, dies entspricht elf Prozent der untersuchten Bauteilmasse. Im zweiten Fokus der Phase III, dem Nutzfahrzeugantriebsstrang, wurden insgesamt 460 Komponenten mit einem Gesamtgewicht von 909 Kilogramm im Design-Benchmarking betrachtet. Hiervon entfallen 290 Kilogramm auf das Getriebe und 619 Kilogramm auf die Kardanwelle sowie die Hinterachse. Mehr als 250 Ideen wurden für konstruktive sowie werkstoff- und fertigungstechnische Möglichkeiten des Leichtbaus entwickelt. Das resultierende Leichtbaupotenzial summiert sich zu insgesamt 124 Kilogramm, das entspricht 14 Prozent der analysierten Bauteilmasse.
Kontakt
Dorothea Bachmann Osenberg
Marketing Managerin
der Initiative Massiver Leichtbau
und Fachbereichsleitung Presse- und Öffentlichkeitsarbeit
im Industrieverband Massivumformung
Tel. +49 2331 958830
E-Mail senden