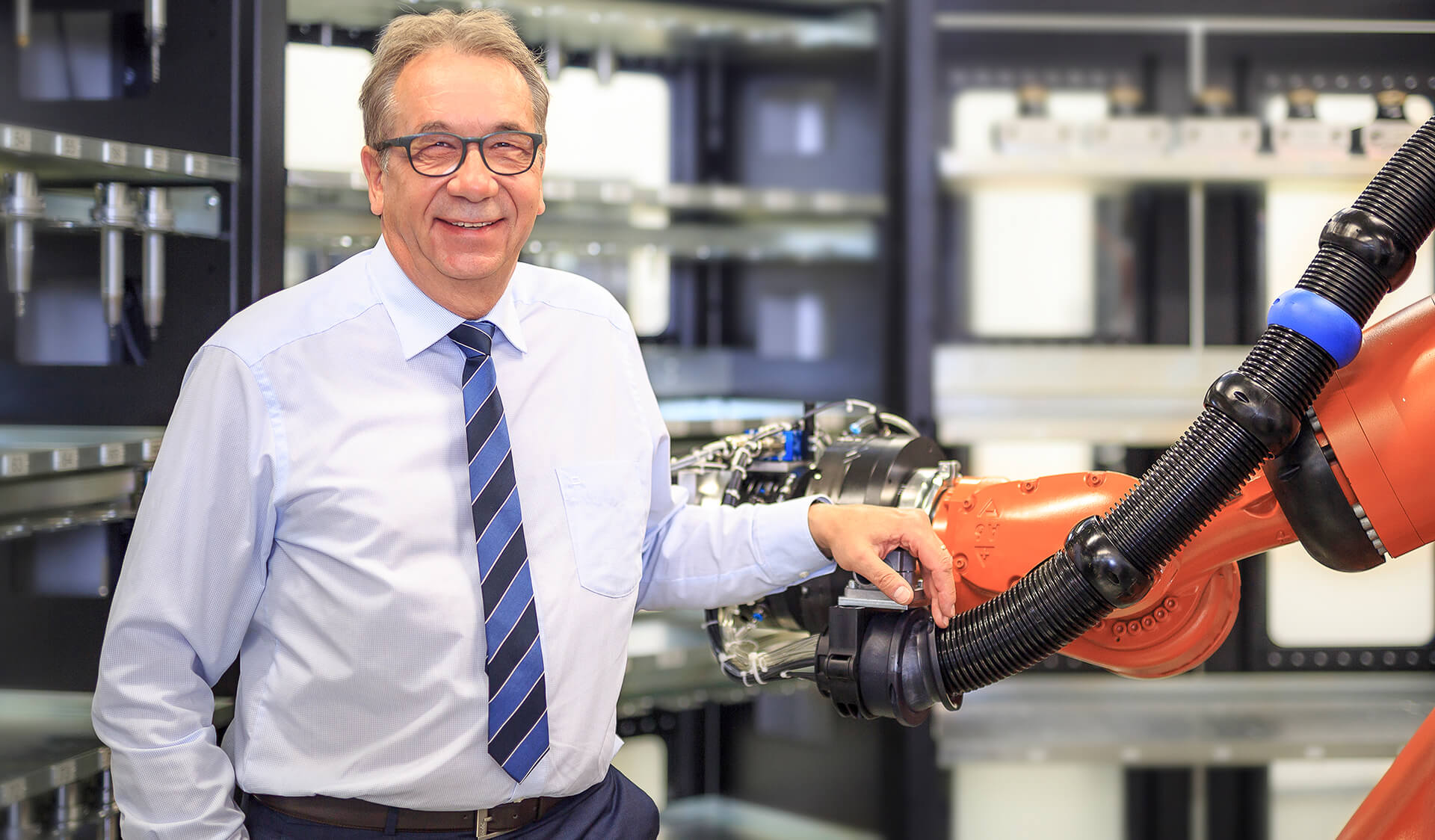
Titelinterview
Der Roboter braucht
die aktive Dämpfung
Moderne Werkstoffe erobern sich neue Einsatzbereiche, um Gewichtsreduzierung bei gleichbleibender Stabilität zu gewährleisten. Produkte in Leichtbauweise wie Flugzeuge verlangen besondere Bearbeitungsmethoden. Die Flugzeugindustrie ist auf dem Weg in die Automatisierung. Den Einsatz der Präzisionswerkzeuge bei Leichtbauwerkstoffen analysiert Mapal intensiv. Mit Uwe Weber, Bereichsleiter CoC Aerospace & Composite bei Mapal, sprach Georg Dlugosch, Chefredakteur des IndustryArena eMagazines, über die Herausforderungen beim Bohren und Fräsen mit dem Roboter.
Was sind die Herausforderungen beim Einsatz von Robotern zur Zerspanung?
Weber: Da muss man unterscheiden zwischen einem Bohrprozess und einem Fräsprozess. Der Bohrprozess für Bauteile der Luftfahrtindustrie ist Stand der Technik. Wenn es um das Fräsen geht, befinden wir uns allerdings noch in den Kinderschuhen. Man fängt gerade erst an, den Prozess zu verstehen.
Wo sehen Sie das größte Hemmnis für den Einsatz von Robotern beim CNC-Fräsen?
Weber: Das sind Steifigkeit und Regelungstechnik. Wir brauchen steifere Mechaniken und schnellere Steuerungen. Am Körper des Roboters müssten Sensoren verteilt werden, um die Belastung der einzelnen mechanischen Elemente zu erfassen. Dann könnte der elastischen Verformung des mechanischen Aufbaus und der Antriebe entgegengewirkt werden. Dazu braucht es sehr schnelle Prozessoren, die in Echtzeit die Abweichungen aktiv kompensieren. Das bedeutet, eine neue Steuerungsgeneration ist erforderlich.
Was ist das Problem bei den Steuerungen?
Weber: Die Regelung erfolgt beim Fräsen nicht schnell genug. Aufgrund der fehlenden Steifigkeit des mechanischen Systems muss die Steuerung die daraus resultierenden Abweichungen sofort ausgleichen. Das gelingt nur mit schnelleren Prozessoren sowie Sensoren, die alle Bestandteile des Gesamtsystems ständig überwachen.
Es gibt Maschinenbauunternehmen, die beim Fräsen so unzufrieden mit den Fähigkeiten der Steuerung waren, als sie den Roboter zum Einsatz im Flugzeugbau bringen wollten, dass sie die gesamten Steuerungen ausgetauscht haben. Meine Hoffnung setze ich darauf, dass auf breiter Front schnellere Prozessoren und Sensoren Einzug halten. Damit wird eine Echtzeitregelung möglich. Erst dann kann faktisch auch eine Maßnahme gegen Schwingungen getroffen werden.
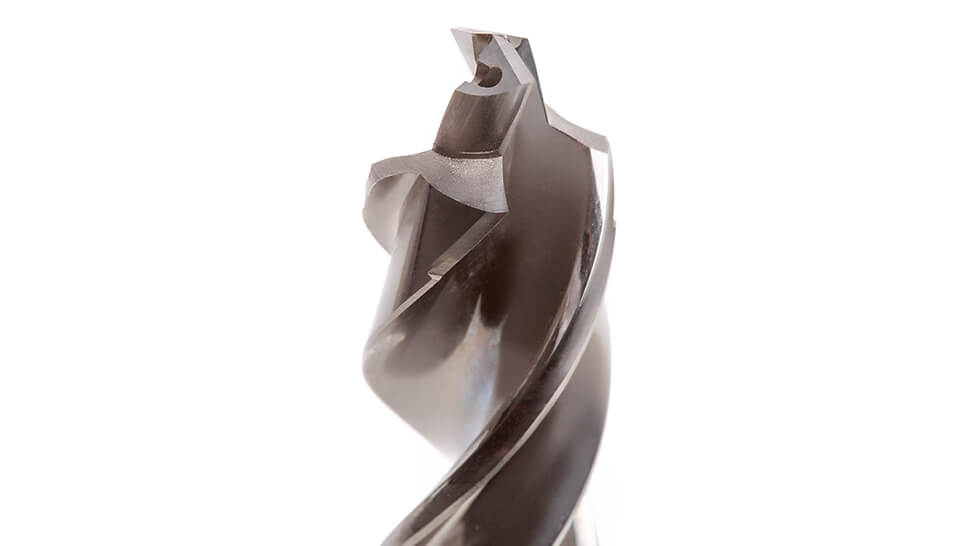
Bei der Bearbeitung mit Hilfe eines Roboters muss das Werkzeug helfen, einen sicheren Prozess zu realisieren. Eine Differenzialspitze mit unterschiedlichen Winkeln stabilisiert und vermeidet Delamination des CFK-Werkstoffs. Fotos: Mapal
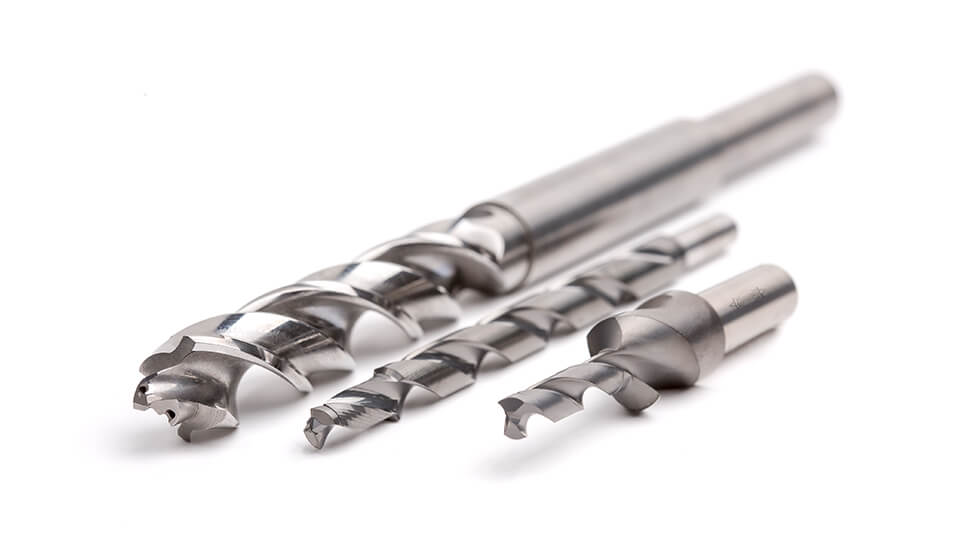
Für die Mehrlagenbearbeitung benötigt das Werkzeug unterschiedliche Features.
Was ist so entscheidend an der Echtzeitregelung?
Weber: Damit wird im Grunde der ganze Prozess geregelt. Der Roboter braucht die Echtzeitregelung, um Schwingungen schnell genug auszugleichen – sozusagen eine aktive Dämpfung. Dann erst kommen wir einen Schritt weiter, der uns in Richtung Bearbeitungsqualität weitere Chancen eröffnet. Im Augenblick ist die Bearbeitungsqualität selbst bei kleinen Fräsern eher dürftig. Für mich ist es schwierig einzuschätzen, was in den nächsten fünf Jahren passiert. Sicher ist, dass mit der aktiven Dämpfung eine Beeinflussung des gesamten mechanischen Systems und letztlich eine deutliche Verbesserung zu erzielen ist.
Werden die Werkzeuge diese Entwicklung unterstützen?
Weber: Die ersten Produkte haben wir bereits in unserem Portfolio. Dazu gehören beispielsweise intelligente Spannfutter. Diese eröffnen die Möglichkeit, Schwingungen nahe der Entstehung zu messen und zurückzumelden. Zudem arbeiten wir an Werkzeugen, die die Idee von Industrie 4.0 berücksichtigen. Die Werkzeugmaschine detektiert weitere Details, wie die sich ändernde Leistungsaufnahme der Spindel, die Rückschlüsse auf den Verschleiß des Werkzeugs sowie auf Vibrationen zulässt.
Hoffen Sie darauf, dass sich die Roboter weiterentwickeln?
Weber: Natürlich. Jede Verbesserung bedeutet im Endeffekt eine bessere Bearbeitungsqualität für unsere Kunden. Die Roboterhersteller arbeiten stetig an Verbesserungen. Üblicherweise sind, Stand heute, die meisten Roboter aus Kosten- und Gewichtsgründen nur einseitig gelagert. Beidseitig gelagerte Roboter sind da schon eine Stufe besser – sie haben eine höhere Steifigkeit und Präzision. Der erste Roboter, der die schweren Endeffektoren handhaben kann, ist seit kurzem auch auf dem Markt.
Was ist mit der Zusammenarbeit zwischen Mensch und Roboter?
Weber: Stand der Technik sind die fahrerlosen Transportsysteme, die mit mobilen Robotern zum Einsatz kommen. Dabei gibt es beispielsweise manuelle Systeme mit Fernbedienung. Zunächst wird der Roboter mit Hilfe der Fernbedienung an die richtige Position gefahren. Sobald der Roboter an seiner bestimmungsgemäßen Position angelangt ist, führt er seine Aufgabe vollautomatisch aus. Dabei nähert er sich innerhalb der Größe eines DinA4-Blatts mit Hilfe von definierten Merkmalen an der Flugzeugoberfläche an seine Position an und richtet sich auf „Best fit“ aus, um das Bohrungsprogramm und das Bauteil zueinander auszurichten. Erste Tests mit Cobots, die direkt mit Menschen interagieren, laufen im Moment bei verschiedenen Anwendern.
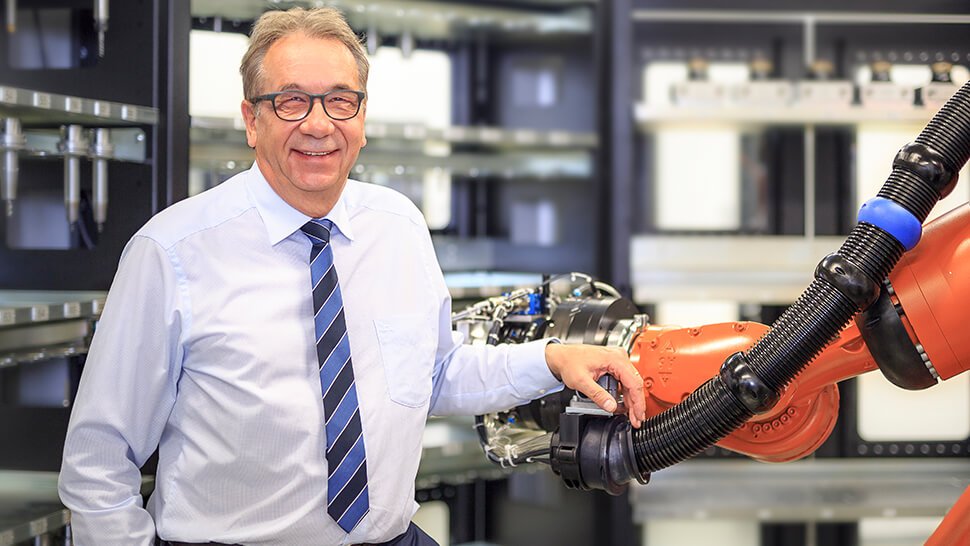
Das Bohren und Fräsen mit dem Roboter unterliegt besonderen Bedingungen, berichtet Uwe Weber, Bereichsleiter CoC Aerospace & Composite bei Mapal. Maßnahmen für eine aktive Schwingungsdämpfung bedürfen schnellerer Prozessoren, um eine Echtzeitregelung zu ermöglichen. Foto: Mapal
Was ist die Rolle des Werkzeugs bei der Bohrbearbeitung mit Hilfe eines Roboters?
Weber: Generell ist es unter anderem die Aufgabe des Werkzeugs, den Prozess weiter zu stabilisieren. Zwar besitzen die bereits erwähnten, neu entwickelten Schwerlastroboter für die Montage in der Flugzeugindustrie eine deutlich erhöhte Steifigkeit durch spielfreie Spindeln und Antriebe. Trotzdem muss das Werkzeug dabei helfen, einen sicheren Prozess zu realisieren. Dafür ist eine Betrachtung des Gesamtsystems notwendig. Meist werden beim Bohren mehrere Lagen unterschiedlicher Werkstoffe bearbeitet, was immer einen Kompromiss bei der Schneidengeometrie erfordert. Kohlefaserverstärkter Kunststoff (CFK), ein sehr abrasives Material, ist vielfach im Einsatz. Dafür muss das Werkzeug sehr verschleißfest ausgeführt sein.
Um einen stabilen Prozess zu erreichen, haben wir unsere Bohrer für diese Bearbeitung mit einer Pilot- und Differenzialspitze ausgestattet. Das heißt, die Spitze des Bohrers hat unterschiedliche Winkel. Ein kleiner Winkel im Zentrum stabilisiert den Rundlauf beim Bohrungseintritt. Der große Winkel im Außenbereich vermeidet Delamination an der Austrittstelle von CFK. Bei Materialkombinationen aus Aluminium und CFK findet die beschriebene Bohrerspitze sehr erfolgreich Anwendung. An den Führungsfasen unserer Bohrwerkzeuge ist ein kleiner Absatz zu spüren. Diese Zusatzschneide, wir nennen sie „MicroReamer“, minimiert die Durchmessertoleranz in den verschiedenen Materiallagen. Der Bohrer verschlankt sich nach hinten etwas. Durch die Verjüngung hat er Spiel in der Bohrung und klemmt nicht ein.
Besondere Bohranwendungen sind Bohrungen für Nieten mit konischem Kopf, die bei der Montage der Außenhaut zur Anwendung kommen. Die Bohrer für diese Aufgabe haben einen am Schaft integrierten Kegelsenker. Wenn die Schneide des Kegelsenkers zum Einsatz kommt, um den Sitz der Nieten vorzubereiten, dann wirkt auf ihn eine seitliche Kraft, die zur Auslenkung führen kann. Dagegen wirkt ein zylindrischer Anteil am Bohrer unterhalb des Kegelsenkers, der Führung gibt.
Wie entwickelt man ein solches Werkzeug?
Weber: Dazu haben wir unser gesammeltes Know-how genutzt. Das haben wir über Testreihen unter verschiedenen Bedingungen vervollkommnet. Unser Ansatz basiert auf dem Prozessverständnis. Dazu nutzen wir den direkten Kontakt und die Nähe zu unseren Kunden und Partnern, den Flugzeugherstellern wie auch den Roboterherstellern.
Wie weit ist die Entwicklung für die Composite-Bearbeitung mit einem Roboter gediehen?
Weber: Auch hier muss man zwischen Bohren und Fräsen unterscheiden. Für das Bohren haben wir bereits die entsprechenden Schneidengeometrien und beherrschen die Prozesse. Unterschiedliche Schneidengeometrien, wie bereits erwähnt, helfen einer Delamination am Ein- und Austritt entgegenzuwirken. Auch der Vorschub ist so angepasst, dass kein übermäßiger Druck auf die CFK-Lagen am Austritt ausgeübt wird. Zum Fräsen von Composite-Materialien mit Robotern gibt es Stand heute keine wirklich prozesssichereren Lösungen.
Wobei eignet sich der Roboter noch?
Weber: Die Automobilindustrie nutzt zunehmend Leichtbauwerkstoffe wie CFK oder Glasfaser. Daraus werden Karosserieteile oder auch Frontend- und Backend-Bauteile gefertigt. Diese werden zum Beispiel besäumt und gebohrt.
Kontakt
Uwe Weber
Bereichsleiter CoC Aerospace & Composite Mapal Präzisionswerkzeuge Dr. Kress KG Aalen Tel. +49 7361 585-0 E-Mail senden
Patricia Hubert
Corporate Communications Mapal Präzisionswerkzeuge Dr. Kress KG Aalen Tel. +49 73 61 585-0 E-Mail senden