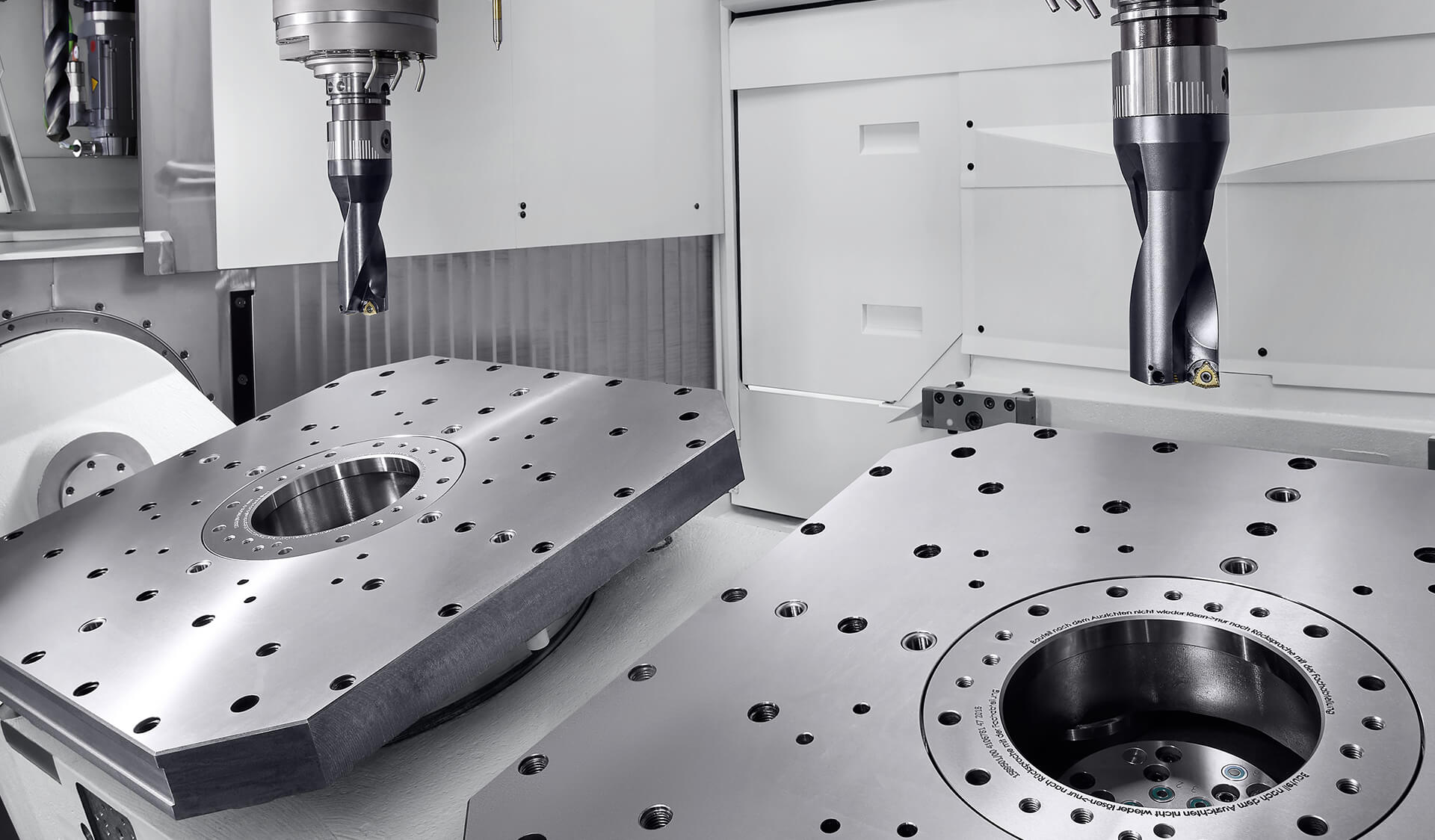
Produktion
Lösungen nach Maß
für den neuen Antrieb
Reiner Fräsprozess, kombinierte Fräs-Drehapplikation oder Drehmaschinenlösung: Für die Produktion von Komponenten für Elektro- und Hybridmotoren werden unterschiedliche Technologien benötigt. Die Chiron-Group ist in der Lage, die für jede Art der Anforderung passende Maschine zur Elektromobilität herzustellen. Mit den Bearbeitungszentren neuer Baureihen ist die Unternehmensgruppe in diesem Zukunftsmarkt stark vertreten.
Speziell für die Elektromobilität bietet die Unternehmensgruppe eine Bandbreite an Lösungen und Technologien: Von Chiron kommt die Komplettbearbeitung von Batteriegehäusen und die Bearbeitung extrudierter Profile. Scherer hat sich auf die hochproduktive Drehbearbeitung für die Produktion von Elektromotoren und Differenzialgehäusen spezialisiert. Stama verfolgt Ansätze für die integrierte Fräs-/Drehbearbeitung von Antriebsstrangkomponenten.
Durch die Diversifikation innerhalb der Unternehmensgruppe können unterschiedliche, maßgeschneiderte Fertigungslösungen realisiert werden. So sind beispielsweise für die Produktion von Gehäusen für Elektromotoren – je nach gewünschter Ausbringung, Flexibilitätsanforderung und Präferenz – ein Fräsprozess, eine Fräs-Drehapplikation oder eine Drehmaschinenlösung erforderlich. Für alle drei Konzepte sind spezielle Komplettsysteme, also inklusive Spannvorrichtung, zugehörigen Werkzeugen, integriertem Prozess und Automation, möglich. Die Einbindung zusätzlicher Gewerke wie Entgraten, Schweißen, Montieren und Prüfen, lässt sich auf einfache Weise realisieren.
Bewährte Baureihen
Im Automotive-Sektor sind neben vollelektrischen Antrieben auch Hybridantriebe auf der Überholspur. Verbrennungsmotoren werden mit elektrischen Antriebseinheiten kombiniert oder soweit elektrifiziert, dass Nebenaggregate bedarfsgerecht und unabhängig vom Motor betrieben werden können.
Ein Beispiel ist der elektrische Kältemittelverdichter, dessen Hauptkomponente, der Scroll, auf der doppelspindligen DZ 08 S five axis precision+ von Chiron mit höchster Genauigkeit und Wirtschaftlichkeit gefertigt wird. Bei diesem hochpräzise gefertigten Bauteil sind die Stärken des Maschinenkonzept mit vertikal angeordneten Motorspindeln und Linearantrieben entscheidend, da nur damit die geforderten Genauigkeiten prozesssicher gefertigt werden können.
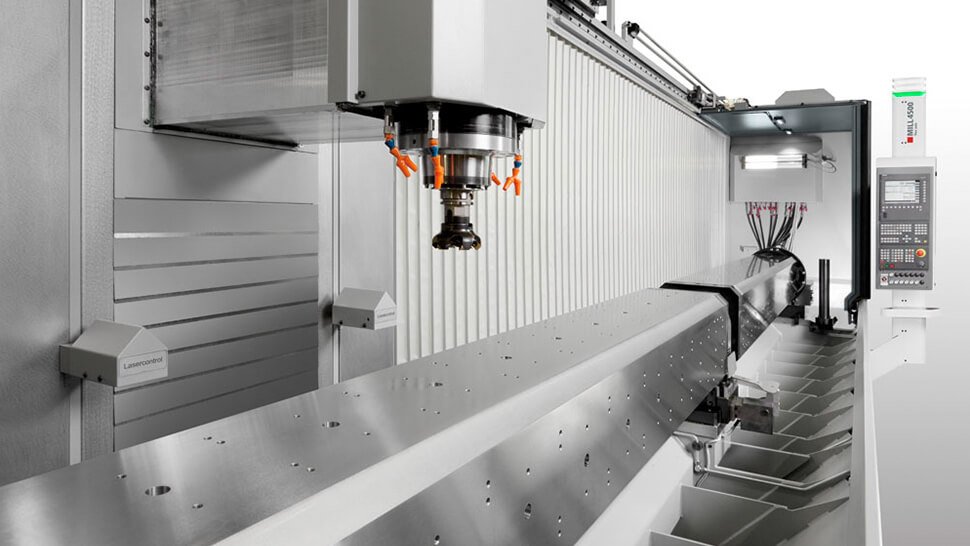
Bei der Fertigung von Fahrwerks- und Strukturbauteilen aus Aluminium werden flexible Bearbeitungszentren wie die MILL-Baureihe benötigt. Federbeindome oder der Batteriekasten eines vollelektrischen Fahrzeugs gehören zu den gefragten Bauteilen. Fotos: Chiron
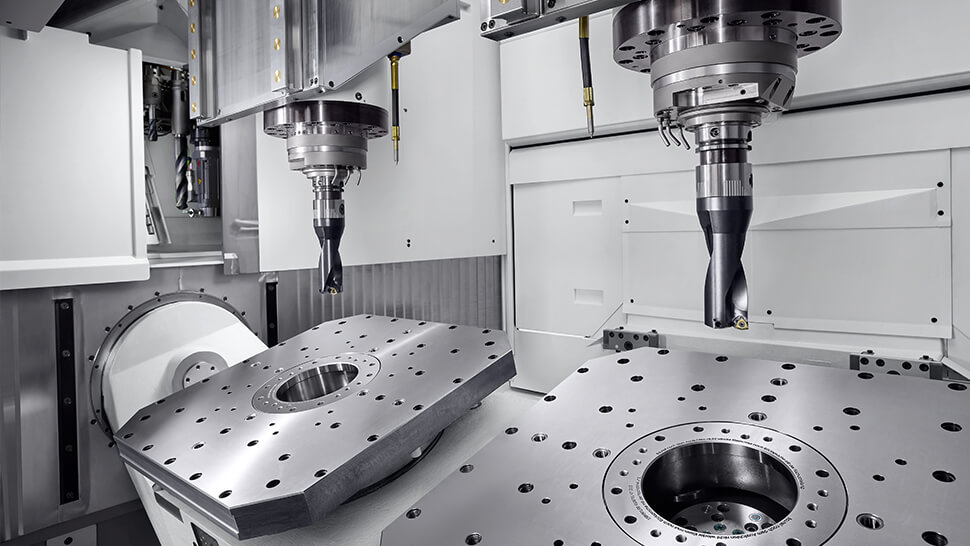
Hochpräzise Bauteile lassen sich mit der DZ 25 von Chiron fertigen. Das Maschinenkonzept mit vertikal angeordneten Motorspindeln und Linearantrieben liefert die geforderten Genauigkeiten prozesssicher.
Aufgrund des zunehmenden Gewichtsproblems aktueller und künftiger Fahrzeuge durch die Kombination von Elektro- und Verbrennungsmotor ist davon auszugehen, dass der Bedarf an Fahrwerks- und Strukturbauteilen aus Aluminium anhalten oder sogar steigen wird. Bei der Fertigung dieser Komponenten ist die Chiron Group bereits seit Jahren beispielsweise mit besonders flexiblen Bearbeitungszentren beteiligt. Mit den Langbettmaschinen der MILL-Baureihe ist es möglich, vom Federbeindom bis zum Batteriekasten eines vollelektrischen Fahrzeugs sämtliche Strukturbauteile wirtschaftlich zu fertigen.
Auch mit der Baureihe 25 können komplexe, großvolumige Strukturbauteile hochproduktiv bearbeitet werden. Die Maschinen legen eine Kombination aus Produktivität, Genauigkeit und Flexibilität an den Tag. Der Spindelabstand von 800 Millimetern prädestiniert die DZ 25 P five axis für das doppelspindlige Bearbeiten von Aluminiumstrukturbauteilen. Für ein Plus an Präzision sorgen die voneinander unabhängig in X- und Z-Richtung verfahrbaren Spindeln. Im Zug der Produktoffensive steht auch die Baureihe 28 mit einem Spindelabstand von 1200 Millimetern in den Startlöchern. Auch diese bieten die Voraussetzungen für die Herstellung von großvolumigen Fahrwerks- und Strukturbauteilen.
Fokus auf die Automobilindustrie
Den Grundstein der 2018 gestarteten Produktoffensive legte eine völlig neue Maschinenplattform. Der Vorteil für die Automobilindustrie: Sämtliche Bearbeitungszentren auf dieser Plattform sind konkrete Antworten auf die aktuellen Anforderungen der Branche.
Die DZ 22 W five axis verspricht insbesondere auch bei sehr großen Werkstücken eine hohe Präzision. Kurze Taktzeiten werden durch die hohe Achsbeschleunigung, kurze Span-zu-Span-Zeiten sowie schnelle Eilgänge erreicht. Für ein Steigerung der Produktivität sorgt die integrierte Werkstückwechseleinrichtung, durch die Roh- und Fertigteile hauptzeitparallel be- und entladen werden können. Sie ist für die Komplettbearbeitung von großen Bauteilen aus Stahl- und Aluminium wie Elektromotoren, Getriebegehäuse oder Fahrwerkskomponenten geeignet.
Kontakt
Kristoffer Siegmann
Head of Global Account Management AutomotiveCHIRON Werke GmbH & Co. KG
Tuttlingen
Tel. +49 7461 940-0
E-Mail senden