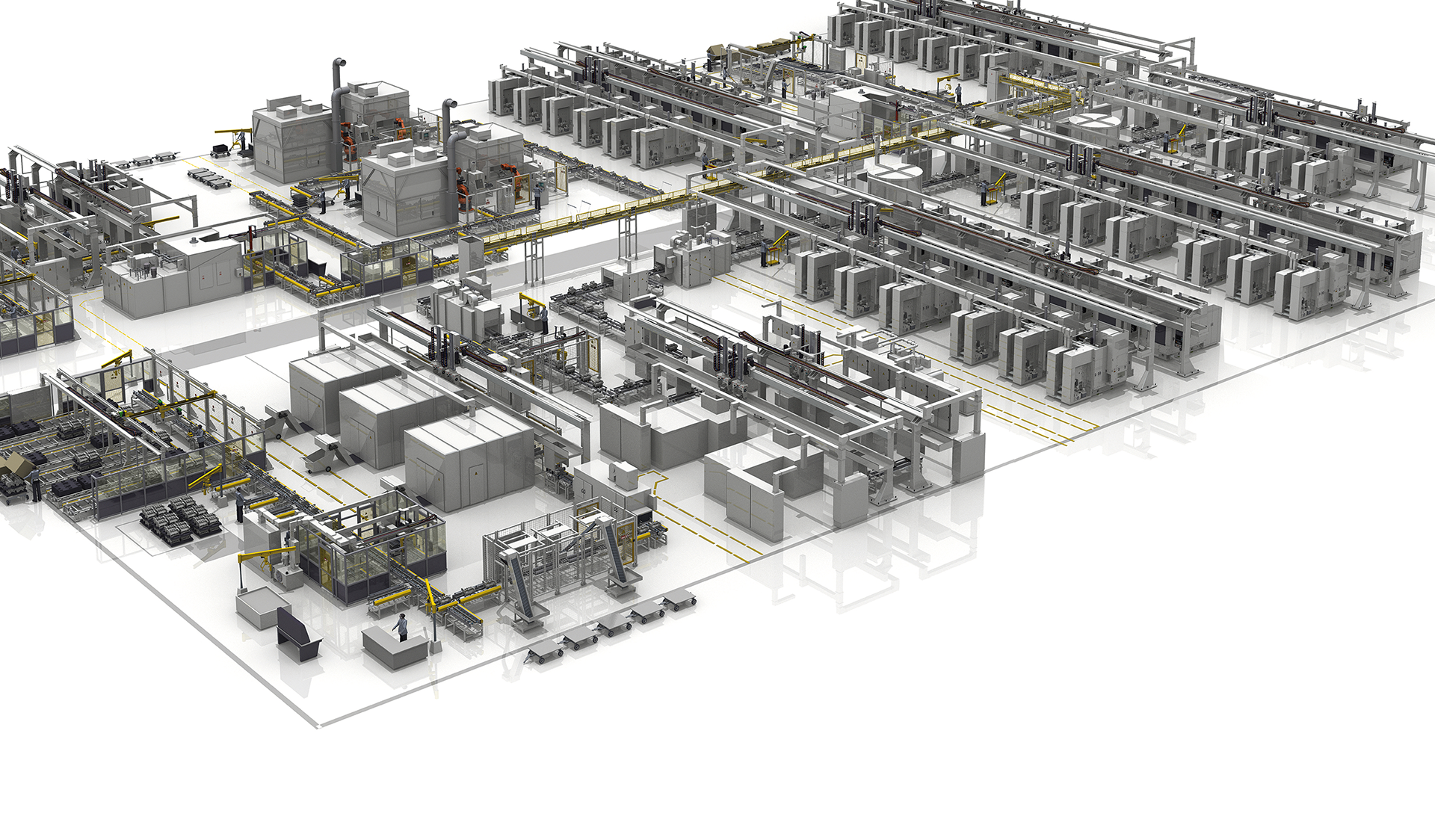
Titelthema
CNC-Bearbeitung für die Elektromobilität
Letztlich stellen die Produktionsanlagen für Komponenten des elektrischen Antriebsstrangs keinen Quantensprung im Vergleich zu modernen agilen Fertigungssystemen dar. Neu hingegen ist die Art der Planung und Umsetzung unter Nutzung der verfügbaren Digitalisierungsmethoden für das spezifische Technologiewissen. Der disruptive Prozess muss von beiden Seiten gemeistert werden: Der Fahrzeughersteller muss akzeptieren, dass eine weitere Kernkomponente möglicherweise vom Zulieferer kommt und der Anlagenhersteller muss das Verschwinden vieler Motor- und Getriebebauteile verkraften und sich vermehrt auf die Kunden aus der Zuliefererbranche einstellen, heißt es bei der FFG-Gruppe zur Transformation des Fahrzeugantriebs.
Die Herausforderung bei der Produktionsplanung für den Fahrzeugmarkt war noch nie schwieriger aufgrund der unklaren Parameter aus Markt und Politik. Die Mehrzahl der Automobilhersteller wird sich nicht auf eine Technologie festlegen können. Das Produktionsvolumen von Fahrzeugen mit Verbrennungsmotoren (singulär oder im Hybridantrieb eingebunden) ist in den kommenden Jahren noch so hoch, dass ein kompletter Ausstieg aus der Technologie für die meisten Hersteller unmöglich erscheint. Auf der anderen Seite steigen die Produktionszahlen des elektrischen Antriebs langsam.
Es gibt sogar strategische Überlegungen, ob der elektrische Antrieb zukünftig eine Kernkompetenz des Fahrzeugherstellers bleiben wird. Kann man nicht bereits jetzt schon am Entwicklungsvorsprung von Tesla eine Antwort auf diese Fragestellung finden? Die erheblichen Entwicklungsaufwendungen der Fahrzeughersteller für attraktive Produktangebote in jedem Fahrzeugsegment beeinflussten die Zielsetzung bei der Produktionsplanung. Wiederverwendung oder Rekonfiguration sind vielfach die aktuellen Aufgabenstellungen.
Mehr Honen statt Schleifen
Laut einer Analyse des VDMA schrumpft die Wertschöpfung bei der Fertigung eines Elektrofahrzeugs um zwei Drittel gegenüber einem Fahrzeug mit Verbrennungsmotor. Elektromotor, Inverter sowie das Getriebe werden oft in ein gemeinsames Gehäuse eingebaut. Deshalb erfordern die Konstruktionen im Vergleich zum Zylinderkurbelgehäuse (900 Sekunden Gesamtbearbeitung) mit mehr als 1000 Sekunden Gesamtbearbeitung vergleichbare Anlagenkonzepte. Der klassische Elektroantrieb besteht aus dem Statorgehäuse mit angegossenem vorderem Lagerschild, einem separaten Getriebegehäuse und einem ebenso separaten Invertergehäuse. Das Lagerschild wird über einen Passungsdurchmesser an der Außenseite des Lagerschildes auf das Getriebegehäuse aufgesteckt und verschraubt. Bei dieser Konzeption müssen Lagersitz und Außendurchmesser in einer Aufspannung und von einer Seite bearbeitet werden, um die erforderlichen Toleranzen einzuhalten.
In dieser Aufspannung werden Lagerbohrung, Außendurchmesser und Statorblechaufnahme üblicherweise in Folge bearbeitet. Dadurch soll ein möglichst kleiner Luftspalt zwischen Stator und Rotor erzielt werden. Die Spaltbreite zwischen den Bauteilen entscheidet über den magnetischen Widerstand, die Höhe des induzierten Stroms (Asynchronmaschinen) und damit über den Wirkungsgrad des Motors.
Aus vielen Gründen, beispielweise der Toleranzkette der Bauteile, beträgt der Luftspalt nur 0,5 bis 0,6 Millimeter. Ein weiterer signifikanter Unterschied zu den klassischen Verbrennungsmotoren liegt in der Motordrehzahl von mehr als 10.000 Umdrehungen pro Minute. Beide Merkmale – gesteckte Antriebswelle und hohe Drehzahl – sind für das Geräuschverhalten des Antriebsstrangs verantwortlich. Neben den engen Positionstoleranzen der Getriebelagerstellen kommen die erforderlichen Oberflächenqualitäten der Getrieberadverzahnung für eine optimale Laufruhe des Antriebsstranges hinzu. Deshalb wird die Oberfläche nicht geschliffen, sondern gehont.
Für die Bearbeitung der sensiblen dünnwandigen Bauteile wird vorzugsweise eine Direktspannung in der Vorrichtung (alternative Adapterplatte) und eine Mehrfachaufspannung (Vor- und Fertigbearbeitung) empfohlen. Bei der Schruppbearbeitung ist grundsätzlich in Richtung der Werkstückauflage zu bearbeiten. Der großflächige Spanabtrag am Innendurchmesser des Statorgehäuses setzt Spannungen frei, die sich auf die Geometrie auswirken. Daher wird ein erneutes Spannen vor der Fertigbearbeitung erforderlich. Optimal wäre eine Feinbearbeitung des Innendurchmessers (Butterfly-Werkzeug) ohne Gleitleisten zur Vermeidung von Brandflecken.
Auf Elektroantrieb gerüstet
Die ein- und zweispindeligen CNC-Hochleistungsmaschinen der Baureihe Specht bieten für jedes kubische Bauteil des Elektroantriebes, des Energiespeichers und des Fahrwerks die Bearbeitungsmöglichkeit. Im Vergleich zu den klassischen Kugel-Rollspindel-Achsantrieben kann mit Lineartrieben die Produktivität zwischen acht und zwölf Prozent verbessert werden. Die Maschinen sind für die Nassbearbeitung sowie für die Trockenbearbeitung mit Minimalmengen-Schmierung konzipiert. Mit einer Fünf-Achs-CNC-Maschine sind auch die Voraussetzungen für die Prozess- und Werkstückflexibilität geschaffen. Beim Einsatz von Adapterplatten können auch sehr unterschiedliche Bauteile in einer Maschine ohne Umrüsten, also für Losgröße 1, gespannt und bearbeitet werden.
Kontakt
Dr. Manfred Berger
Executive Vice President Sales and Marketing
MAG IAS GmbH
Eislingen
Tel. +49 7161 805-4900
E-Mail senden