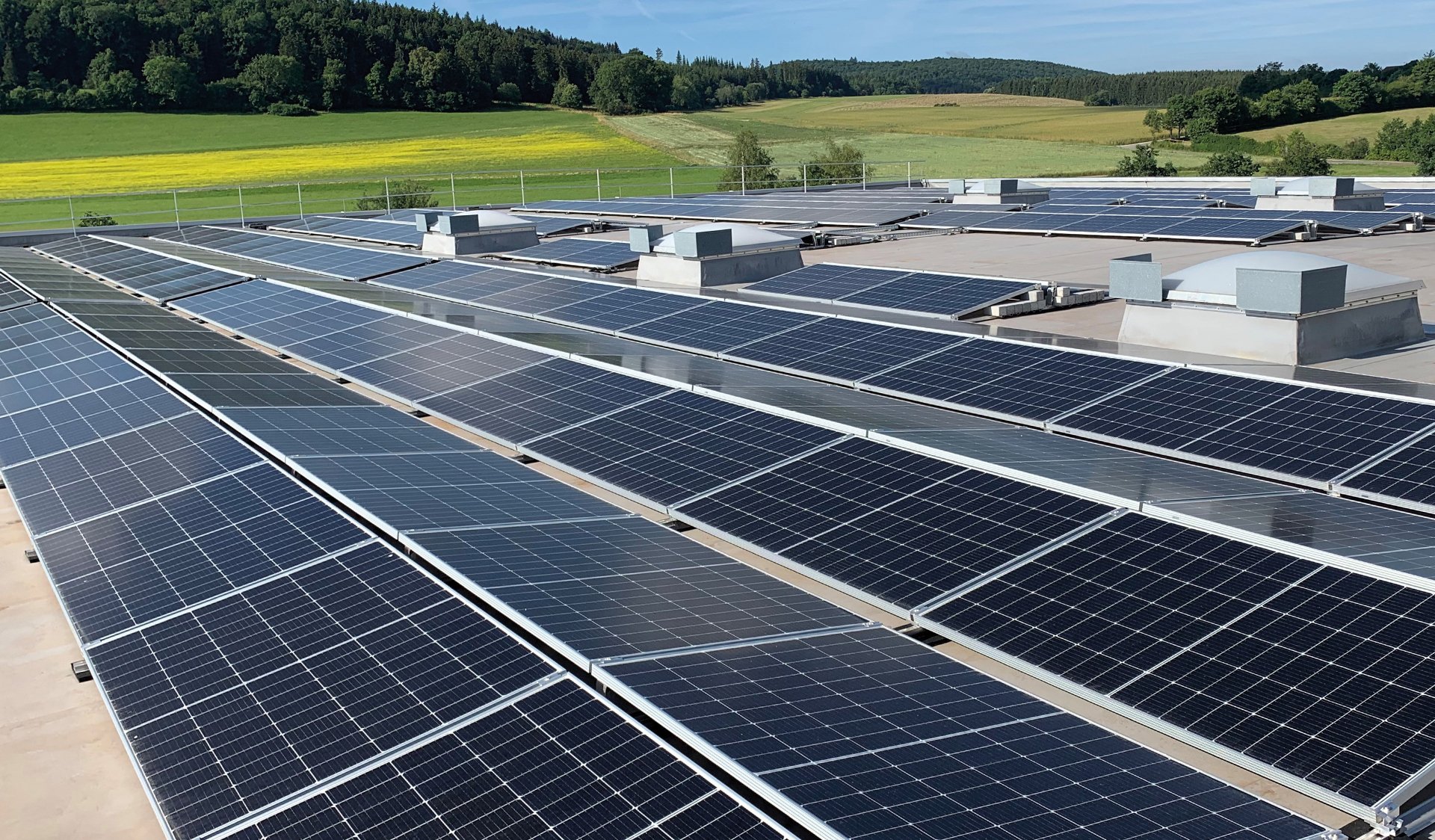
Titelinterview
Der Rohstoff kommt vor allem vom Recycling
Wer nach einem Vorzeigeunternehmen in Betracht auf den schonenden Umgang mit Ressourcen sucht, findet es mit Sicherheit im Südwesten Deutschlands, der Hochburg der Werkzeugbranche. In Tübingen hat sich die Walter AG mit einem ehrgeizigen Programm einen Namen gemacht, lange bevor die gegenwärtigen Krisen mit ihren Zwängen den Handlungsspielraum eingeschränkt hätten. In Bezug auf nachhaltiges Wirtschaften ist Walter besonders aktiv. Treiber dieser Entwicklung ist Gerhard Schüßler, Direktor für das Qualitäts- und Risikomanagement.
Die aktuellen Zeiten scheinen besonders herausfordernd zu sein. Brüche in den Lieferketten, Mangel an Ressourcen, explodierende Preise – welche Herausforderung stellt sich für sie im Moment am größten da?
Schüßler: Natürlich machen wir uns zu diesen Themen Gedanken. Zum Beispiel das Thema Gas. Wir verwenden es nicht direkt in unseren Prozessen, sondern nur zum Heizen und zur Energiegewinnung. Wir haben vor sechs Jahren ein Blockheizkraftwerk in unserem Werk in Tübingen eingebaut. Damit heizen wir im Winter mit Gas und im Sommer erzeugen wir Strom. Die Abwärme nutzen wir über eine adiabate Kühlung für die Klimatisierung. In einem unserer Werke wird Gas zur Lufttrocknung verwendet. Der Kostenfaktor spielt für uns eine wichtige Rolle. Wir haben keine langfristigen Verträge, sondern kaufen an der Energiebörse Gas zu aktuellen Preisen ein. Da haben wir eine Steigerung von 138 Prozent derzeit.
Auch andere Materialien spielen in unseren Überlegungen eine große Rolle. Bei der Herstellung von Hartmetall wird beispielsweise ein Kobaltanteil verwendet. Auch da hat sich eine Verteuerung ergeben. Der Preis liegt fast beim sechsfachen Wert im Vergleich zur Zeit vor der Pandemie. Die Ausrichtung an der Elektromobilität und der Herstellung der Batterien hat dazu beigetragen.
Wie reagieren Sie, um genügend Rohstoff zu erhalten?
Schüßler: Eine unserer Herausforderungen ist, so viel wie möglich von dem verkauften Vollhartmetall wieder zurückzukaufen und dem Recycling zuzuführen. Das übernimmt unser Tochterunternehmen in Österreich. Dort werden die Werkzeuge in ihre Bestandteile wie Kobalt und Wolframcarbid zerlegt. Alle Bestandteile werden fein separiert und können nach dem Recyclingprozess im Prinzip wie Rohmaterial verwendet werden. Bei diesen Anstrengungen weiten wir unsere Bemühungen auf Länder aus, in denen wir noch nicht so aktiv waren, um möglichst viel Material in den Prozess zurückzuführen.
Der Kreislauf der Materialien unterstützt also auch das Unternehmen?
Schüßler: Das Thema Kreislaufwirtschaft hat für uns eine enorme Bedeutung. Allein schon durch die Gesetzgebung sind wir in Deutschland verpflichtet, mindestens 90 Prozent wieder in den Kreislauf zu führen. Das Ziel erreichen wir auch an den deutschen Standorten. Sowohl Deponie wie auch Verbrennung werden so wenig wie möglich genutzt.
Gibt es dann überhaupt noch Abfall?
Schüßler: Der anfallende Abfall, überwiegend aus der Herstellung der Werkzeuge, wird seit Jahren nach den Mindestanforderungen des Kreislaufwirtschaftsgesetzes getrennt gesammelt und ist leicht rückläufig. Die Getrenntsammlungsquote liegt über 96 Prozent. Ein großer Faktor bei unserer Abfallverwertung ist Aluminiumoxid. Das wird in einem Prozess verwendet, um beim Hartmetall beispielsweise Kanten zu verrunden. In einigen Ländern gibt es Wiederverwendungsmöglichkeiten wie im Straßenbau. Bei uns in Deutschland fallen insgesamt jährlich etwa 60 Tonnen als Abfall an, die wir jetzt mit unserem Entsorger wieder in den Kreislauf bringen.
Welche Materialien fehlen?
Schüßler: Wir haben seit einem Dreivierteljahr Versorgungsengpässe bei der Belieferung mit HSS, also High-Speed Steel. Auch dieser Stahl hat einen gewissen Kobaltanteil. Er findet Anwendung für Gewindewerkzeuge und Bohrer. Die meisten HSS-Rohlinge, mehr als 50 Prozent, kommen aus China. Da machen uns die unterbrochenen Lieferketten Schwierigkeiten. Teils müssen wir auf andere Lieferanten umsteigen, teilweise müssen wir auch erheblich mehr als bei den Stammlieferanten bezahlen, aber wir halten unsere Fertigung in Betrieb, weil die Nachfrage nach den Produkten weiterhin auf einem hohen Niveau liegt. Im Zuge der Pandemie und des Ukraine-Kriegs hatten wir eigentlich mit einem stärkeren Einbruch gerechnet.
Wie reagiert Ihre Abteilung, das Qualitäts- und Risikomanagement, auf diese Situation?
Schüßler: Wir sind in Verbindung mit den Verantwortlichen im Einkauf, wenn es um die Beschaffung der Materialien geht, und auch bei Themen wie Strom und Gas. Ich habe die Verantwortung für das Thema Sustainability. Im Bereich der CO2-Emissionen spricht man von drei Kategorien. Scope 1 ist der Bereich der direkt freigesetzten klimaschädlichen Gase, also was verbrauchen wir an Benzin, Diesel, Gas. Scope 2 umfasst die indirekte Freisetzung durch Energielieferanten, also Strom. Scope 3 sind die vor- und nachgelagerten Bereiche. Was kaufen wir zu und wie viel Energie oder CO2 steckt da drin – vom Bleistift oder Radiergummi bis zur Werkzeugmaschine. Nachgelagert sind auch die notwendigen Transporte in die Läger und zu unseren Kunden. Bereits seit 2012 erfassen wir Scope-1- und Scope-2-Daten. Das haben wir in diesem Jahr auf Scope 3 erweitert.
Scope 1 und 2 erfassen wir in allen Niederlassungen weltweit. An allen 34 Standorten werden zum Beispiel die Verbräuche der Dienstfahrzeuge erfasst. Auf dieser Basis rechnen wir die Reduzierungen. In den letzten 3 Jahren haben wir die Steuerungen und die Konfigurationen unserer Druckluftstationen auf den neuesten Stand gebracht. Heizung und Klimatisierung wurden an vielen Standorten erneuert. An unseren eigenen Standorten werden nach Möglichkeit Solarzellen auf den Dächern montiert. In Münsingen ging jetzt ein großes Solarfeld in Betrieb. In Tübingen wird noch eine Solaranlage montiert. Wo es möglich ist, soll eigene Energie erzeugt werden.
Neben der Energie steht auch die Problematik mit der Verwendung von Kunststoff im Blick. Welche Verpackung nutzt das Unternehmen?
Schüßler: Auch beim Abfallmanagement sind wir sehr aktiv. In diesem Quartal haben wir die Umstellung in der Verpackung auf recyceltes Material erreicht. Jetzt werden alle Produktverpackungen auf Verpackungen aus Recycling-Material hergestellt und sind damit wiederverwendungsfähig. Plastik war allerdings bisher deutlich günstiger. Vor vier Jahren war das Recycling-Material etwa viermal so teuer wie das direkt generierte Rohmaterial aus Erdöl. Auch werden wir zukünftig keine Luftpolsterfolien aus Kunststoff mehr verwenden, sondern auf Papierverpackungen mit Wabenstruktur zum Schutz der Werkzeuge einführen. Außerdem sind wir beim Füllmaterial auf zerknülltes Papier umgestiegen und müssen jetzt mit den Kunden das Problem lösen, dass das Abfallvolumen gestiegen ist.
Ist das als nachhaltig zu betrachten?
Schüßler: Aus unserer Sicht ist es nachhaltig, weil wir kein Plastik mehr verwenden und auf das Bleaching verzichten, das heißt, wir verwenden nur noch braunes, recyceltes Papier. Die Prozesse sind sehr viel umweltschonender in der Herstellung.
Die Beschwerden der Kunden haben Sie gerade angesprochen. Wer darf die Diskussionen führen?
Schüßler: Die Kommunikation zum Thema Verpackungen führen unsere Kollegen im Verkauf. Die Kommunikation zur Nachhaltigkeit gehört aber zu meinem Bereich. Ich stehe mit vielen Kunden persönlich im Austausch über die Maßnahmen. Wenn wir CO2-Neutralität erreichen wollen, dann müssen wir auch unsere Lieferanten einbinden. Auch unsere Kunden fordern starke Einsparungen. Je weniger unsere Produkte an CO2-Fußabdruck liefern, umso geringer ist auch die Bilanz des Kunden in der vorgelagerten Lieferkette. Beispielsweise hat sekundäres Material im Vollhartmetall einen viel niedrigeren CO2-Koeffizienten als neuwertiges Material. Das gilt auch für Verpackungen oder Stähle.
Wie hoch ist der Anteil?
Schüßler: Wir liegen bei den Werkzeugkörpern aus Stahl bei einem Recycling-Anteil von 95 bis 98 Prozent. Es gibt nur sehr kleine Beimischungen, um die benötigte Spezifikation des Stahls zu bekommen. Bei Vollhartmetall liegen wir aktuell bei 75 Prozent und bei High-Speed Steel zwischen 84 und 88 Prozent. Damit sind wir bereits weit vorne. Die Umstellung bei der Verpackung war ein weiterer großer Schritt für uns. Ein weiterer wichtiger Faktor ist der Transport. Wir liefern an vier zentrale Lagerorte im US-Staat Kentucky, in Holland, in Singapur und Shanghai. Standardwerkzeuge werden innerhalb von 24 Stunden ausgeliefert, das ist dem Kunden zugesichert. In den meisten Fällen lässt sich das nur mithilfe des Flugzeugs realisieren. Damit steigt der CO2-Fußabdruck stark. Der Umstieg auf Schiff oder Schiene hätte neben einer viel längeren Lieferzeit, sehr viel höhere Lagerbestände zur Folge; und damit eine große Kapitalbindung. Beim Recycling nutzten wir grundsätzlich nur das Schiff oder die Schiene zum Transport.
Wie sieht die Nachhaltigkeitsstrategie aus?
Schüßler: Unsere Strategie zur Nachhaltigkeit gliedert sich in vier Teile. Circularity, Climate, Zero Harm to People und Compliance. Vieles ist schon in der deutschen Gesetzgebung enthalten, bei vielen Vorgaben haben wir in Deutschland eine Vorreiterrolle. Die Walter AG ist dabei in vielen Bereichen gut gerüstet. An allen Standorten führen wir ein so genanntes Compliance-Haus. Darin sind die wichtigsten Regularien lokal, regional und weltweit berücksichtigt. Die Regularien werden jährlich in einem Assessment geprüft und aktualisiert.
Wie bewerten Sie die Sorgfaltspflicht in der Lieferkette?
Schüßler: Die Sorgfaltspflicht in der Lieferkette ist für uns ein wichtiges Thema. Die Vorgaben sind bei uns schon sehr gut abgesichert. Beispielsweise gibt es seit 2008 das Gesetz zu Konfliktmineralien. Davon ist Vollhartmetall mit Wolframcarbid ebenso wie Tantal betroffen. Zinn und Gold gehören auch dazu. Wir prüfen in der Lieferkette, ob diese Mineralien zum Beispiel über Kinderarbeit, Versklavung oder aus dem Kongo kommen, weil dort der Verdacht besteht, paramilitärische Truppen mit den Erlösen zu unterstützen. In diesem Bereich haben wir eine Nachvollziehbarkeit von 99 Prozent. Dabei hilft uns auch der hohe Wert an recyceltem Material, weil damit die sauberste Verwendung besteht. Generell verlangen wir, dass alle unsere Lieferanten einen Code of Conduct bestätigen, bevor wir eine kontinuierliche Belieferung unterzeichnen.
Wie sieht Ihr Zeitplan für die nächsten Ziele aus?
Schüßler: Bei den oben genannten Bausteinen unserer Nachhaltigkeitsstrategie haben wir uns Ziele für das Jahr 2030 gesetzt. Wir gehen zudem davon aus, dass wir zwischen 2040 und 2045 das Ziel der Klimaneutralität erreichen. Grundsätzlich muss man dabei berücksichtigen, dass es sich um eine stetige Entwicklung handelt. Wir hoffen auf viele Innovationen, um diesen Weg zu verfolgen.
Welche Innovationen gibt es aktuell bei Walter?
Schüßler: Vor einem halben Jahr haben wir die Beschichtung Tiger tec Gold neu entwickelt. Wir haben eine sehr hohe New Sales Ratio. Sie liegt bei über 25 Prozent, also ein Viertel der Produkte sind jünger als fünf Jahre. Wenn ein Produkt erneuert wird, dann ist die Zielvorgabe 30 bis 40 Prozent Leistungsverbesserung. Bei der neuen Tiger·tec-Gold-Schneidstoffgeneration für Dreh-Anwendungen haben wir sogar 50 Prozent mehr Standzeit geschafft.
Was ist der Kunde bereit, für Nachhaltigkeit zu bezahlen?
Schüßler: Eine Preissteigerung wird sich nicht vermeiden lassen, allein aufgrund der Verteuerung der Energie. Aktuell sehen wir, dass die Kunden in Deutschland sehr sensibel auf das Thema Nachhaltigkeit reagieren. Bei diesem Thema sind die skandinavischen Länder immer vorne mit dabei, und auch in Großbritannien wird es weiterhin verfolgt. Dort werden trotz Brexit noch viele EU-Gesetze hochgehalten. Aus unserer Sicht ist der Einklang mit der EU weiterhin hoch. Generell muss ich sagen, dass die Kunden solche Aktivitäten erwarten, auch wenn sie nicht unbedingt bereit sind, mehr dafür zu bezahlen. Deshalb ist die Kommunikation ein sehr wichtiger Faktor geworden und auch die Mitarbeiter, die einen sehr hohen Anteil zum Gelingen beitragen, müssen mitgenommen werden.
Kontakt
Gerhard Schüßler
Director Quality & Risk Management/Data Privacy Officer
Walter AG
Tübingen
Tel. +49 7071 701-0
E-Mail senden
Das Interview führte Georg Dlugosch, Chefredakteur des IndustryArena eMagazines.