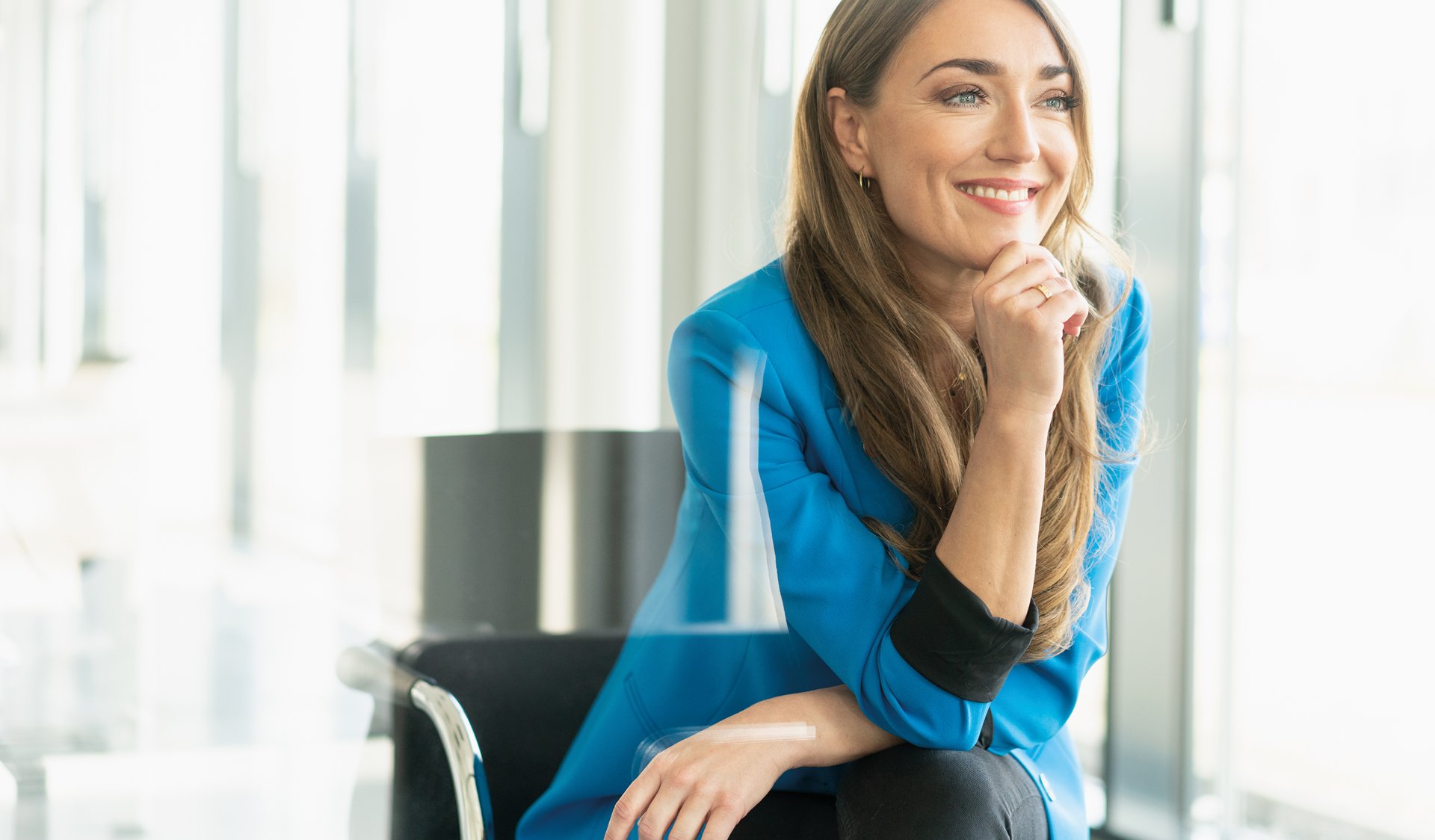
Software
Corona war ein Booster für Digitalisierung
Unternehmen sind auf dem Weg in das digitale Zeitalter. Dabei müssen sie zunächst lernen, die über sie hereinbrechende Datenflut zu beherrschen. Das Manufacturing Execution System (MES) leistet als Brücke zwischen den strategischen und operativen Systemen wertvolle Dienste. Wo steht der deutsche Maschinenbau in Bezug auf die Digitalisierung? Das MES entwickelt sich zum Schlüssel für Industrie 4.0, berichtet Katharina Van Meenen-Röhrig im Interview mit dem IndustryArena eMagazine. Sie leitet gemeinsam mit Dr. Ignace Van Meenen, Chief Executive Officer, die GFOS Group in Essen.
Wo steht der deutsche Maschinenbau in Bezug auf die Digitalisierung der industriellen Produktion?
Van Meenen-Röhrig: Ich muss schmunzeln bei der Frage, weil ich sie 2017 tatsächlich noch anders beantwortet habe. Ich war damals Teilnehmerin bei einer großen Studie. Wir haben uns genau mit dieser Frage beschäftigt. Damals war die psychologische Komponente, das Mindset, noch ein ganz wesentliches Thema. Wir haben festgestellt, es gibt noch psychologische Restriktionen, den Maschinenbau für übergeordneten Datentransfer zu öffnen. Ich glaube jedoch, dass wir heute ein großes Stück weiter sind. Wir haben in Deutschland sicherlich viele Technologien entwickelt, allerdings muss man sagen, dass wir uns im globalen Kontext und mit vielen Wettbewerbsländern auseinandersetzen müssen, die teils noch deutlich schneller sind als wir.
Die Komplexität steigt und verlangt mehr Flexibilität. Wie sieht die Antwort der Industrie aus?
Van Meenen-Röhrig: Wir haben aktuell die große Herausforderung durch die steigende Komplexität. Wir sehen einen Wandel im Absatz- und Beschaffungsmarkt. Wir haben zudem das Thema der explodierenden Energiepreise. Ich arbeite auch in verschiedenen Fachgremien, in denen es ein Riesenthema ist. Ein Problem sind auch politische und gesetzliche Restriktionen, der Fachkräftemangel oder der Eintritt neuer Wettbewerber. All solche Dinge sind mit einer erheblichen Komplexitätssteigerung verbunden. Es ist natürlich eine große Herausforderung, die notwendige Flexibilität auch in der Industrie abzubilden. Ein wichtiges Stichwort an dieser Stelle ist das Thema Interoperabilität. Das bedeutet, dass man verschiedene Systeme miteinander vernetzt, dass man das Thema Automatisierung über Schnittstellen vorantreibt oder agile Produktionsmethoden implementiert. Ich glaube, dass wir schnell dahin kommen müssen, handlungsfähig zu sein und uns auf unterschiedliche Rahmenbedingungen einstellen können.
Was ist das größte Hindernis für die schnelle Umsetzung von Industrie 4.0?
Van Meenen-Röhrig: Auf diese Frage höre ich unterschiedliche Antworten. Meine persönliche Meinung ist, dass wir mit OPC UA eine Standardschnittstelle geschaffen haben, die eine Grundvoraussetzung gerade für die deutsche Industrie darstellt, aber wir müssen uns jetzt für übergeordneten Datentransfer über die Ländergrenzen hinaus vernetzen. Da muss sicherlich noch an internationalen Standards gearbeitet werden. Das größte Hindernis für Industrie 4.0 ist schwierig herauszuheben, aber es war tatsächlich auch damals genau diese Frage ein Thema in der Studie. Ich glaube, dass der übergeordnete Datentransfer nach wie vor ein ganz großes Hindernis für die Umsetzung von Industrie 4.0 ist – und das Mindset dazu. Also wirklich die eigenen Unternehmensgrenzen zu überschreiten, weil große Sorgen wegen Datenklau oder Datensicherheit dahinterstehen, die auch ihre Berechtigung haben. Die Produktionsdaten für den übergeordneten Datentransfer freizugeben, das ist bis heute eines der größten Hindernisse überhaupt. Sicherlich gibt es auch die Sorge vor hohen Kosten und fehlende technologische Kompetenz.
Kann mit Hilfe der Digitalisierung die Kollaboration verbessert werden?
Van Meenen-Röhrig: Das fragen Sie natürlich jemanden, der vollumfänglich auf Digitalisierung setzt. Ich glaube, dass die Digitalisierung ein ganz wichtiger Bestandteil von Kollaboration ist, alleine wenn wir das Thema Interoperabilität nochmal aufgreifen, also von unterschiedlichen Anlagen, Maschinen und Systemen. Natürlich auch die virtuelle Zusammenarbeit. Die Vernetzung von Lieferketten oder ganzen Wertschöpfungsketten funktioniert nur innerhalb der Digitalisierung. Dadurch wurde eine massive Kollaboration zwischen verschiedenen Wertschöpfungssystemen geschaffen. Ohne Digitalisierung können wir in der heutigen Zeit gar keine Kollaboration mehr generieren.
Welche erlernten Erfahrungen nimmt die Industrie aus der Corona-Zeit mit?
Van Meenen-Röhrig: Das schließt sich nahtlos an die Corona-Pandemie an. Coivd19 war ein riesiger Digitalisierungsbooster. Wir hatten völlig veränderte Rahmenbedingungen. Absatzmärkte und Lieferketten sind zusammengebrochen. Ich vermute, dass wir ohne Digitalisierung noch deutlich schlechter weggekommen wären. Diejenigen mit vielen digitalen und autonomen Prozessen waren handlungsfähig geblieben in der Zeit, wo eben keine Menschen nebeneinander in der Produktion stehen durften.
Es sieht so aus, als müssten oft zunächst einmal die Prozesse geklärt und definiert werden. Ist das eine der Hürden für die Einführung des MES?
Van Meenen-Röhrig: Ich glaube, dass es ein Schlüssel zu Industrie 4.0 ist. Wir müssen uns vorstellen, dass ein MES-System im Prinzip die Daten aus der Produktion erst einmal sammelt, aufbereitet und zur Verfügung stellt. Das heißt MES ist eine Schnittstelle zu anderen Systemen und damit auch zu einem übergeordneten Datentransfer. Das ist die Grundvoraussetzung, wenn man an eine horizontale oder vertikale Vernetzung in der Produktion denkt. Meines Erachtens ist Industrie 4.0 ohne ein MES-System aus heutiger Sicht nicht möglich. Das MES-System ist folglich ein wichtiger Baustein von Industrie 4.0.
Geht es also wieder einmal um das berühmte Software-Phänomen Mist-rein-Mist-raus?
Van Meenen-Röhrig: Es ist eine Grundvoraussetzung für die Einführung von MES, die Prozesse zu klären. Wenn man sich vergegenwärtigt, dass ein MES dazu verwendet wird, die Produktion und die Produktionsdaten in Echtzeit zu überwachen und zu steuern, dann bedeutet es, dass nicht nur die Prozesse, sondern auch beispielsweise die Stammdaten erst mal einwandfrei sein müssen, damit eben auch die richtigen Daten aufbereitet werden. Allein das ist häufig schon eine Herausforderung, das kann ich aus Erfahrung sagen. Das MES erfordert auch die detaillierte Kenntnis der Produktionsprozesse, damit das System die richtigen Daten zur richtigen Zeit sammelt und bereitstellt, um eine Optimierung der Produktion zu erreichen. Es stellt also sicher, dass alle Abteilungen und Mitarbeiter das gleiche Verständnis für den Produktionsablauf haben. Es ermöglicht eine standardisierte Überwachung und Optimierung der Prozesse. Es erleichtert die Datenerfassung. Deswegen ist es meistens noch keine Hilfe, sondern tatsächlich eine Grundvoraussetzung.
Wie fügt sich MES am besten in das Produktionsmanagement ein?
Van Meenen-Röhrig: Ich sehe MES als Brücke zwischen den strategischen und operativen Systemen, da sie sicherstellt, dass die Daten in Echtzeit aktualisiert werden, genau sind und eine effektive Überwachung sowie Steuerung der Prozesse im Fertigungsbereich ermöglicht. MES ist im Prinzip die Middleware, die als Bindeglied oder Verbindungsstück verstanden werden kann.
Für die Arbeit mit Business Intelligence und Kennzahlen ist die Kenntnis von Betriebsdaten und Maschinendaten die Voraussetzung. Wie lässt sich Transparenz in der Produktion herstellen?
Van Meenen-Röhrig: Ganz sicher durch MES-Lösungen. Die als Datensammler fungieren und erst mal die Daten standardisiert und bedarfsgerecht aufbereiten. Ein MES kann eingesetzt werden, um Daten zu sammeln, zu analysieren und dann eben ganz wichtige Einblicke zu geben, also eben Transparenz in den Produktionsprozess zu bringen. Das kann dazu beitragen, die Prozesseffizienz und Qualität zu verbessern, Kosten zu optimieren und bessere Entscheidungen zu treffen. Ein Thema für die Transparenz ist die Echtzeitdatenaufbereitung. Man arbeitet nicht mehr mit Daten aus der Vergangenheit, sondern man hat Echtzeitdaten. Das ist ein wichtiger Schritt, um die notwendige Transparenz in die Produktion zu bekommen.
Wie weit ist die Entwicklung des integrierten Produktionsmanagements gediehen?
Van Meenen-Röhrig: Wir sehen immer wieder, dass die Integration eine Herausforderung ist, weil es zum Teil eben nicht so ist, dass die Dinge gut vernetzt sind oder so transparent ineinandergreifen, wie es eigentlich notwendig ist. Da gibt es sehr fortschrittliche Unternehmen, in denen die Technologien bereits über Schnittstellen eingesetzt werden, aber das ist noch nicht überall der Standard. Wir versuchen natürlich, dies gerade mit den MES-Systemen zu erreichen, aber es ist wichtig, dass die Schnittstellen gut funktionieren und dass auch die Denkweise innerhalb der Produktionsmitarbeiter davon geprägt ist.
Ist das MES der Schlüssel zu Industrie 4.0?
Van Meenen-Röhrig: Die Anpassung an die ständig wechselnden Bedingungen ist ein äußerst wichtiges Thema. Wir haben stark veränderte Markt- und Rahmenbedingungen. Ich schätze, ein ganz wichtiger Schlüssel für die nächsten fünf Jahre ist, dass man stärker auf das Thema Modularität setzt. Das bedeutet, sich an die unterschiedlichen Bedarfe über Modularität anzupassen. Anstatt ein monolithisches System einzuführen, setzen wir auf ein sehr stark modular aufgebautes System, das mit dem Unternehmen, in dem es implementiert wird, wächst und sich an die Rahmenbedingungen anpasst. Das Thema Skalierung wird stark von unseren Kunden nachgefragt. Modularität und Parametrierbarkeit werden die Entwicklung prägen.
Kontakt
Katharina Van Meenen-Röhrig
Chief Executive Officer
GFOS Group
Dr. Kerstin Kipper
Corporate Communications
GFOS mbH - Gesellschaft für Organisationsberatung
und Softwareentwicklung mbH
Essen
Tel. +49 201 61 300 750
E-Mail senden