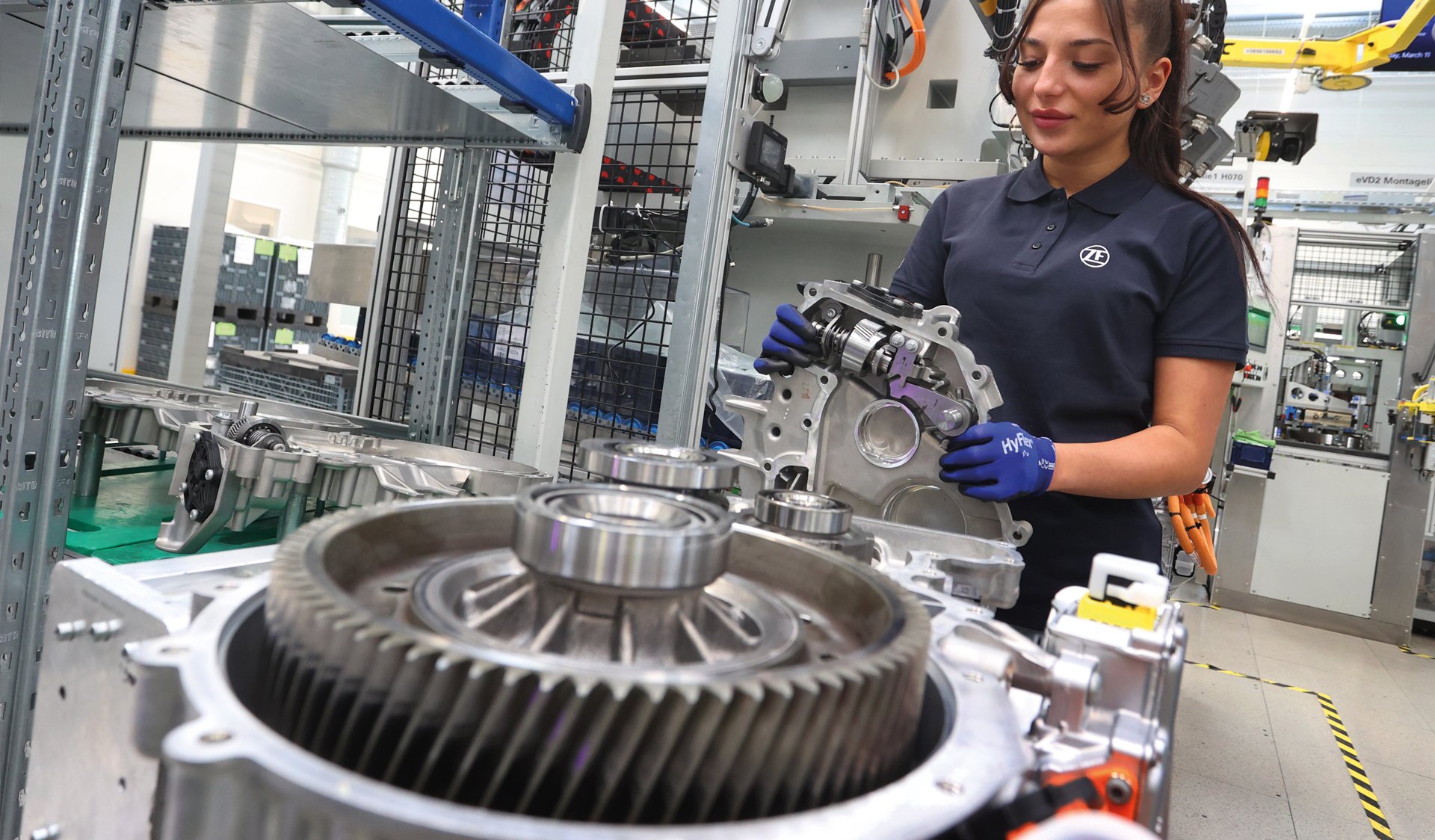
Qualitätssicherung
Mobilitätswandel verändert Messtechnik
Es war nur eine kleine Unterschrift, die in Brüssel für eine große Transformation sorgt. Der EU-Vertrag macht beim Autoantrieb aus dem Verbrenner ab 2035 eine Randerscheinung. Die Veränderung bei den Fahrzeugen bewirkt große Veränderungen in der Zerspanungstechnik, die schon wieder vor einer großen Herausforderung steht, nachdem sie erst vor kurzem die Veränderungen durch die additive Fertigung bewältigt hat. Mit der Transformation zur E-Mobilität muss sich auch die Messtechnik auf andere Aufgaben vorbereiten, um die Qualität der neuen Komponenten und feinsten Strukturen zu kontrollieren.
Der Wechsel vom Antrieb durch den Verbrenner zum Elektromotor verändert die Anforderungen an die Messtechnik massiv. Im gesamten elektrischen Antriebsstrang bieten sich große Chancen für die Messtechnikhersteller. Von der Batterie mitsamt der Wanne über den Motor bis zum Getriebe muss das Qualitätsmanagement neu ausgerichtet werden.
Die Befürchtung vieler Zerspaner ist zerstoben, dass ihre Arbeitsplätze wegfallen und beim Elektromotor weniger Teile zu bearbeiten sind. Denn gleichzeitig steigt die Zahl der verbauten Gleichteile. Die Erleichterung für die Qualitätssicherung geht einher mit einem wachsenden Druck, weil komplett alle Teile geprüft werden müssen – und zwar in den äußerst kurzen Taktzeiten der Fertigung.
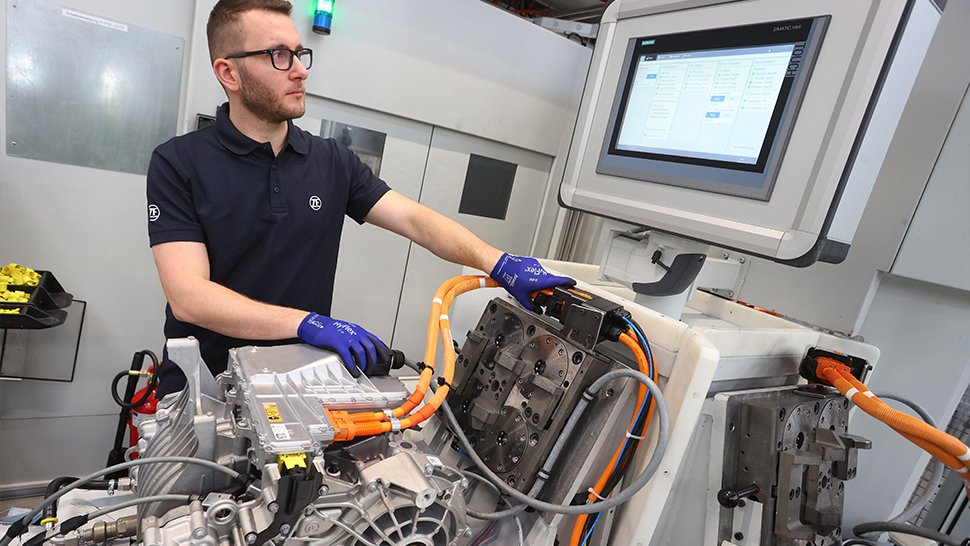
Der elektrischer Achsantrieb braucht eine End-of-Line-Prüfung. In Schweinfurt ist die Transformation in der Messtechnik zu sehen. Foto: ZF
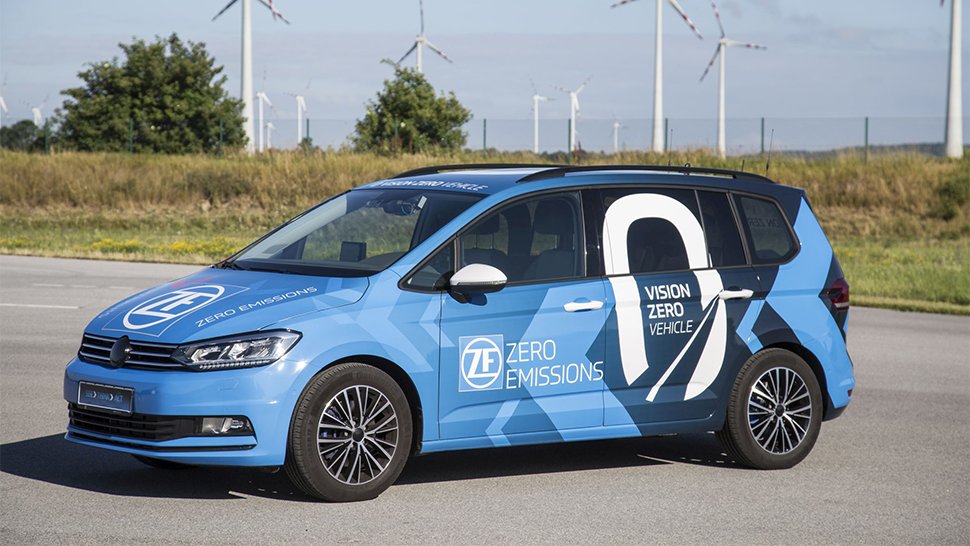
Ohne lokale Emissionen: Mit dem integrierten, 150 kW starken elektrischen Achsantrieb fährt das Vision Zero Vehicle, ohne lokale Emissionen freizusetzen. Foto: ZF
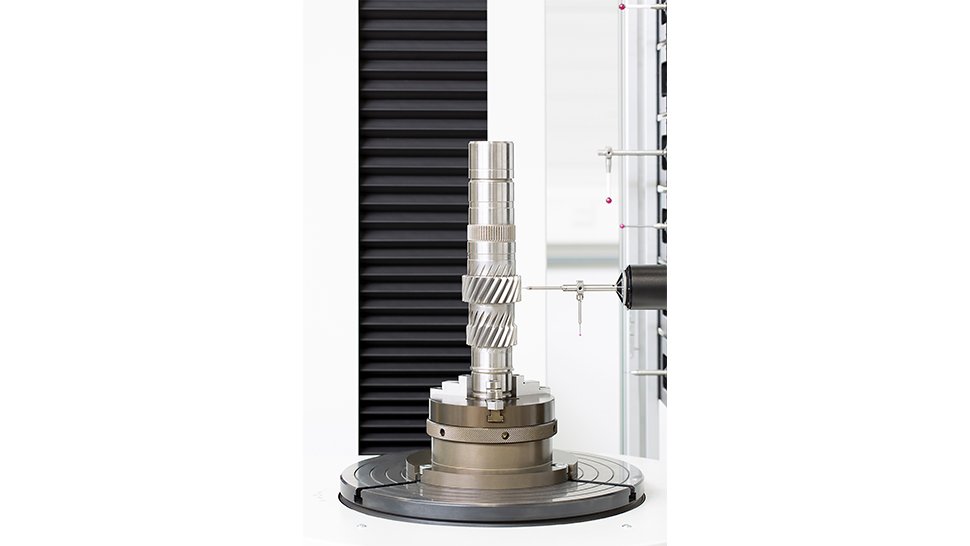
Mehr Tempo nötig
„Für Liebherr ist die Geschwindigkeit und damit die Verbesserung der Messzeiten ein wichtiger Punkt“, erläutert Matthias Bruederle von der Liebherr-Verzahntechnik. Zwar gibt es in der E-Mobilität weniger Bauteile mit Verzahnung, dafür werden die Bauteile immer kleiner. „Die Anfrage nach Welligkeitsanalysen der Oberfläche von Zahnflanken steigt“, berichtet der Produktmanager Messtechnik.
Messtechnik rückt in den Vordergrund, „um Geisterfrequenzen auszuschließen“, erklärt er – Frequenzen, die unerwünschte Geräusche erzeugen. Der erkennbare Trend zu engeren Toleranzen und zum Fokus auf sehr kleine Strukturen „bis zum Komma-My-Bereich“, wie Brüderle erzählt, „verlangt, dass wir an die physikalischen Grenzen vordringen, und es gibt immer noch Potenzial, besser zu werden.“
Störende Geräusche
Geräusche von Verzahnungen wirken bei elektrisch angetriebenen Fahrzeugen deutlich störender. Um die Ursachen von Verzahnungsgeräuschen zu verstehen, „ist noch viel Entwicklungsarbeit“ erforderlich, betont Christof Gorgels von Klingelnberg. Das Unternehmen befasst sich intensiv mit Wellen und Verzahnungen im Antriebsstrang.
Die Anforderungen für das Elektrofahrzeug führen im Vergleich zu konventionellen Fahrzeugen zu höheren Qualitäts- und Genauigkeitsanforderungen speziell bei den Verzahnungen, die künftig die größte Geräuschquelle sind. „Ursache ist die veränderte Drehmoment- und Drehzahlcharakteristik des Elektromotors“, erläutert der Vice President Innovation and Technology. Hinzu kommen steigende Geräuschempfindlichkeiten. Hier ist eine hochgenaue Messtechnik gefordert.
Durch den Wegfall des Verbrennungsmotors mit seiner Geräuschkulisse werden bei geringen und mittleren Geschwindigkeiten die Verzahnungen zur größten Geräuschquelle im Fahrzeug. Zwei Quellen kommen in Frage – die Auslegung und die Fertigung der Zahnräder.
Eine reine Betrachtung der Auslegung ist zwar eine notwendige aber keine hinreichende Bedingung für leise Verzahnungen. Bei den fertigungsbedingten Geräuschursachen sind insbesondere die sogenannten Geisterordnungen zu nennen – unerwünschte Abweichungen im Fertigungsprozess. Diese werden durch Welligkeiten auf der Zahnflanke verursacht, deren Amplitude häufig sehr klein ist, typischerweise im Sub-Mikrometer Bereich. Sie können nur mit hohem Aufwand messtechnisch direkt erfasst werden. Daher steigt bei Stirnradverzahnungen die Bedeutung der Einflankenwälzprüfung, die sich bei Kegelradantrieben etabliert hat.
„Die Genauigkeitsanforderungen an die Verzahnungen steigen, weil das Optimierungsfenster des Konstrukteurs zwischen Tragfähigkeit und Geräusch enger wird“, sagt Gorgels. Daher muss zum einen das Messmittel für die Geometrieprüfung höhere Genauigkeitsstandards erfüllen. Zum anderen ist für das Geräuschverhalten eine höhere Messfrequenz erforderlich, so dass die Einflankenwälzprüfung als qualitätssicherndes Messverfahren hinzukommt.
Hohe Spannung im Messsystem
Elektrische Antriebssysteme und Motoren für Nutzfahrzeuge und Pkw werden bereits in Serie produziert, deshalb erscheinen die Veränderungen bezüglich der Messtechnik bei ZF zunächst nicht so gravierend, auch wenn der Übergang deutlich erkennbar ist. Mit der Entwicklung von Hybridantrieb und E-Achse ist die Transformation in der Messtechnik nahezu abgeschlossen, schildert Daniel Neeser die Situation beim Automobilzulieferer aus Friedrichshafen.
„Die kurze Entwicklungszeit ist in den Vordergrund gerückt“, sagt der Gruppenleiter Prüftechnik. Baukastensysteme helfen, die bisherige Entwicklungszeit eines Fahrzeugs zu halbieren. Für jeden Entwicklungszyklus sind klare Ziele definiert, so soll der Antrieb um einige Prozentpunkte optimiert werden. Einige Prozentpunkte Steigerung bedeuten in der E-Mobilität schon einen großen Erfolg.
Während die Validierung der E-Achse inklusive E-Motor bereits üblich ist, kommt zunehmend die Leistungselektronik als zu prüfende Komponente hinzu. Hochvolttechnologie (HV) dringt in die Automobilwelt ein. Zunehmend wird die 800-Volt-Technologie mit Siliziumkarbid-Wechselrichtern genutzt. „Neben hohen Spannungen sind dadurch schnelle Schaltzyklen und deren Einflüsse zu berücksichtigen“, erläutert Johann Raab.
Der Engineering-Experte, der Prüfstände intern und extern plant und baut, führt aus, dass zu den mechanischen Kenngrößen wie Drehzahlen und Drehmomente die elektrischen Größen wie HV-Spannungen, HV-Ströme und Temperaturen betrachtet werden.
Allein die Erfassung dieser Messgrößen erfordert spezielle Qualifikationen für das Personal, was bei der Dynamik der Entwicklungsaufgaben eine gewisse Herausforderung darstellt. Für eine Wirkungsgradbestimmung müssen elektrische Kenngrößen zeitsynchron mit mechanischen Kenngrößen zusammengebracht werden, um die richtigen Schlüsse daraus zu ziehen. Die Zahl der Messkanäle hat sich durch die elektrischen Größen erhöht, um die E-Achse zu prüfen.
Weitere Herausforderungen sind die Leistungselektronik, elektromagnetische Verträglichkeit und steigende Drehzahlen, die mehr als 20.000 U/min betragen. Dafür nutzt ZF die Virtualisierung der Prüfstände: Prüfstand und Prüfling werden als digitaler Zwilling genutzt, um schneller zu sein und trotzdem hohe Standards zu gewährleisten.
Bessere Batterien
Trendveränderungen im Hinblick auf das Thema Elektromobilität zeigen sich insbesondere bei der Herstellung der Batterie. „In der Automobilbranche herrscht aktuell Aufbruchstimmung“, erklärt Michael Kuran, Key-Account Manager und Gruppenleiter Vertrieb Sensorik bei Micro-Epsilon Messtechnik. „Es wird definitiv ein neues Zeitalter eingeläutet.“
Aktuell werden alle Prozesse und Abläufe analysiert und verbessert, neue Ideen ausprobiert. Kuran sieht massive Investitionen in Forschung und Entwicklung. In ein paar Jahren wird es seiner Ansicht nach Batterien mit mehr Reichweite und kürzerer Ladezeit geben.
Messtechnik wird schon lange eingesetzt, aber derzeit werden auch neue Fertigungsverfahren etabliert. Sensoren sind in existierenden Anlagen eingebaut. „Um eine höhere Produktionsgenauigkeit und ein besseres Produkt zu produzieren werden mittelfristig und langfristig mehr und genauere Sensoren eingebaut.“
„Definitiv erhält die Messtechnik durch die Transformation in der Autoindustrie einen neuen Stellenwert“, erläutert der Messtechnikexperte. „Wir sprechen über Industrie 4.0 und künstliche Intelligenz, aber für all diese Themen werden Daten benötigt. Diese Daten werden über Sensoren und Menschen erfasst. Wenn über vollautomatische Produktionsanlagen gesprochen wird, sprechen wir immer über Sensoren sowie entsprechende Anbindung und digitale Einbindung. So werden zum Beispiel auch das Monitoring und die Rückverfolgbarkeit jeder einzelnen Zelle ermöglicht. Ohne den Einsatz modernster Sensorik ist es in der Automobilindustrie nicht möglich, neuartige Batteriezellen oder bessere Qualität zu produzieren“, betont Kuran
Ohne physische Prüfung
Einen besonderen Ansatz verfolgt das WZL in einem geplanten Forschungsprojekt. Was wäre, wenn die immer komplizierter werdenden physischen Messungen gar nicht mehr nötig werden? Das Stichwort lautet „Predictive Quality“, wie Tobias Müller erläutert. Dann wird der Produktionsprozess anhand von Informationen aus dem Prozess, beispielsweise Sensorinformationen, geprüft, um die Qualität des Produkts datenbasiert vorherzusagen. Eine weitere physische Prüfung wäre nicht notwendig.
Speziell bei der Fertigung von Batteriezellen würde der Nutzen noch vergrößert, wenn es durchgängige Informationen über die Prozesskette gäbe. So könnten Vorhersagen bereichs- oder sogar unternehmensübergreifend durchgeführt werden. „Das erscheint uns als erreichbares Ziel“, sagt Müller. Der Aufwand liegt hierbei vor allem in der Vorbereitung der Modellierung, um die vielfachen Daten in ein einheitliches Format zu bringen. Übergreifend lautet der Grundgedanke. Nicht nur reaktiv zu handeln, sondern früh eingreifen zu können, um Fehler zu vermeiden.
Kontakt
Georg Dlugosch
Chefredakteur
IndustryArena eMagazine
Oberndorf am Neckar
Tel. +49 7423 6551
E-Mail senden