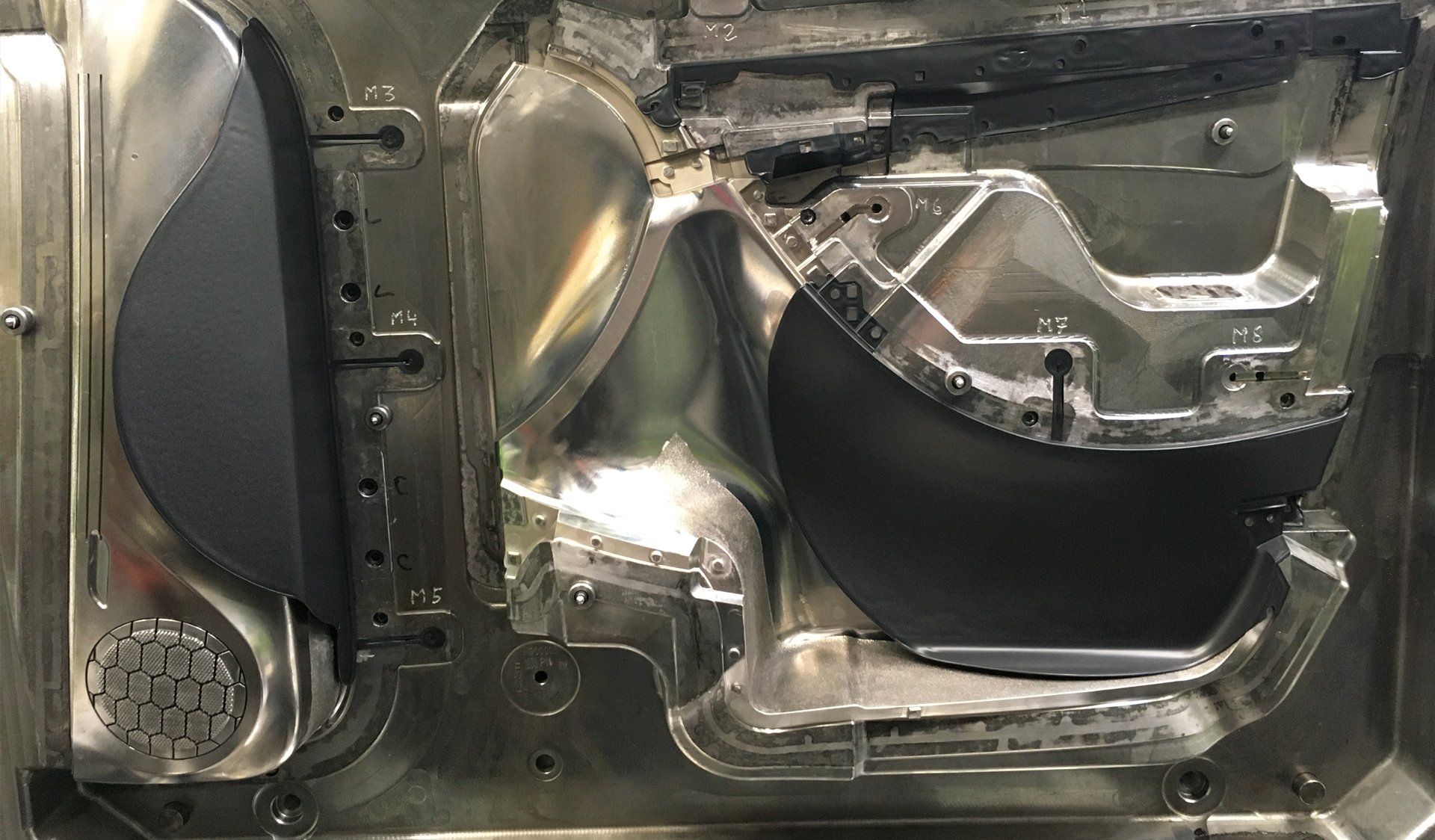
Titelthema
Simulation mit der realen Welt vereint
Die Datenschnittstelle „sim link“ von Engel, dem österreichischen Hersteller von Spritzgießmaschinen, tritt an, die Simulation und den realen Prozess zu verknüpfen, um den Kunststoffverarbeiter über den gesamten Produktlebenszyklus – von der Produktentwicklung und Werkzeugkonstruktion bis zur laufenden Produktion –besser unterstützen zu können. Die Herstellung von Automobilkomponenten im Familienwerkzeug macht deutlich, wie die Schnittstelle das Abmustern von Spritzgießwerkzeugen und die Optimierung von Spritzgießprozessen beschleunigt und die Produktivität steigert.
Bereits vor der Werkzeugkonstruktion für ein neu entwickeltes Spritzgießprodukt wird eine Fülle an Informationen generiert. Mittels Strömungssimulation werden zum Beispiel mögliche Anspritzpunkte eruiert, Füllverhalten der Kavitäten überprüft, Randbedingungen für den zukünftigen Spritzgießprozess eingestellt und die Werkzeugkühlung optimiert.
Sind die Ergebnisse der Simulation zufriedenstellend, kann die Werkzeugfertigung beginnen. Es folgen die Erstbemusterung, die Optimierung der Maschineneinstellungen und schließlich die Serienproduktion. Häufig fällt jedoch beim Bemustern auf, dass an den Kavitäten nachgearbeitet werden muss, um die gewünschte Produktqualität zu erreichen. Das kann die Projektkosten erheblich erhöhen und die Time-to-Market des neuen Produkts verlängern.
Mögliche Ursachen für den Zusatzaufwand sind, dass viele in der Simulation ermittelten Prozessparameter nicht in den Produktionsprozess übernommen werden oder zum Beispiel die ausgewählte Spritzgießmaschine den Volumenstrom aus der Simulation in Realität nicht übernehmen kann. Doch warum ist dies so? Das Hauptproblem ist, dass die Werte aus der Simulation zum Teil aufwendig umgerechnet werden müssen und die Maschinengrenzen in der Simulation nicht überwacht werden. Umgekehrt erhält der Simulationstechniker kaum Feedback, wie gut der mit dem Werkzeug mitgelieferte Einstelldatensatz beziehungsweise die Qualität der Simulation war.
Mit „sim link“ tritt Engel an, diese Datenbarriere zu durchbrechen. Die Datenschnittstelle macht es möglich, die im Vorfeld der Werkzeugfertigung in der Simulation gewonnenen Erkenntnisse und Parameter als Ersteinstellvorschlag direkt in die Steuerung der Spritzgießmaschine zu übertragen und umgekehrt die realen Prozessdaten zurück in die Simulation zu überführen. Ziel ist es, die Qualität der Simulation sukzessive zu verbessern. Simulationstechniker und Produktionstechniker können auf diese Weise das Wissen und die Ergebnisse des jeweils anderen nutzen und voneinander lernen.
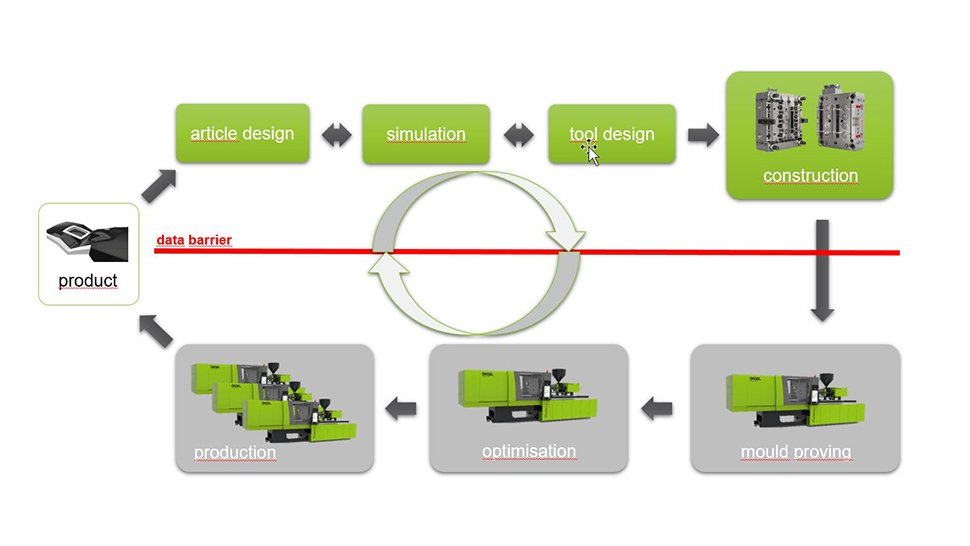
Die Schnittstelle für den Datenaustausch zwischen Simulationsprogramm und Spritzgießmaschine vereinfacht die Zusammenarbeit zwischen den Simulationsexperten und den Prozesstechnikern. Die Datenbarriere wird überwunden. Foto: Engel
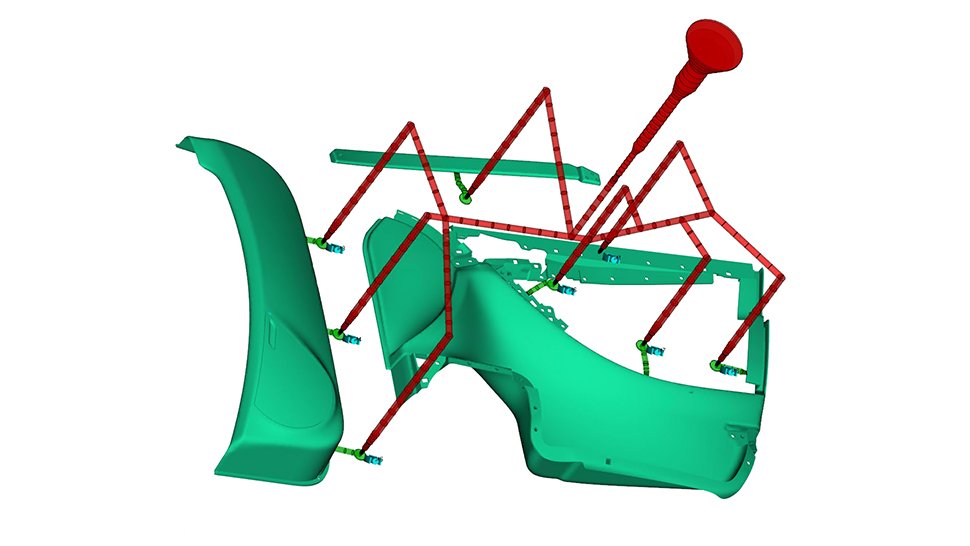
Das Simulationsmodell wurde im Programm Moldflow von Autodesk aufgebaut.
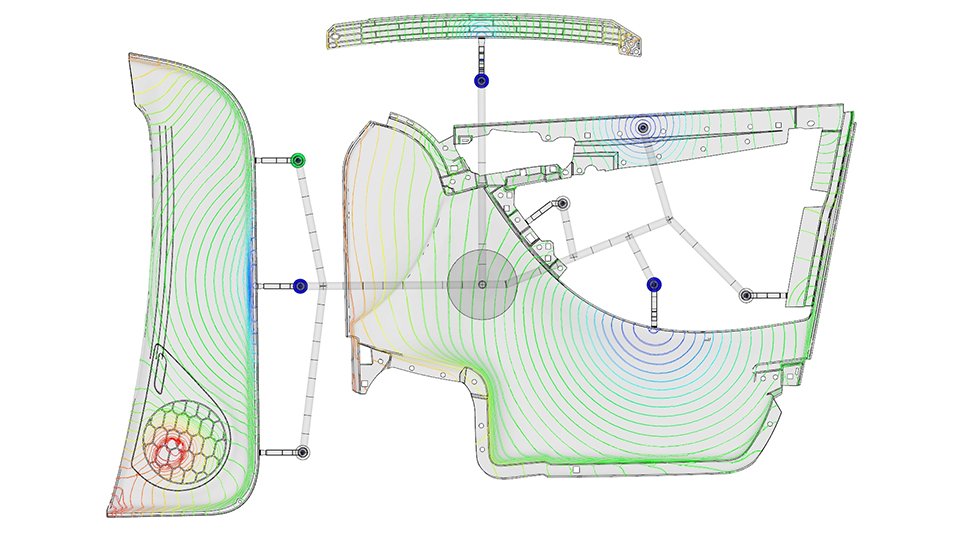
Die simulierte Fließfrontgeschwindigkeit stimmt mit den tatsächlichen Einspritzparametern überein.
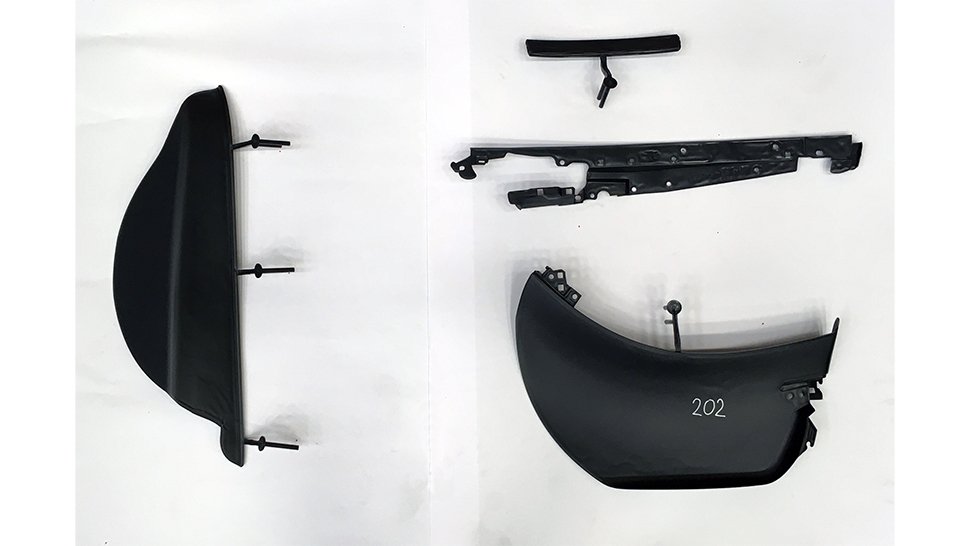
Simulation versus Realität: Bei allen Nadelverschlussdüsen wurde in der Simulation darauf geachtet, dass sich die Fließfronten der jeweiligen Kavität und der zu öffnenden Nadelverschlussdüse am Anschnitt treffen, um Bindenähte zu vermeiden.
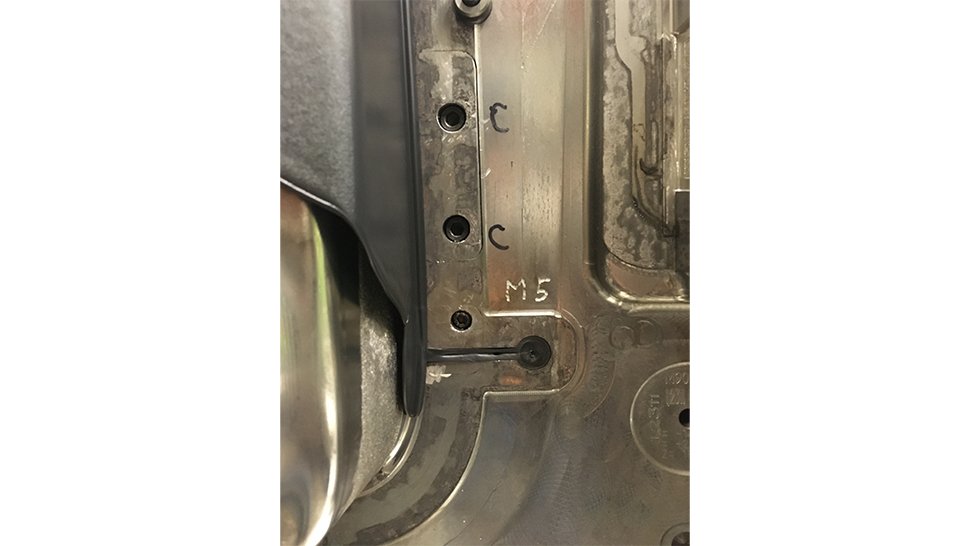
Simulation versus Realität: Bei allen Nadelverschlussdüsen wurde in der Simulation darauf geachtet, dass sich die Fließfronten der jeweiligen Kavität und der zu öffnenden Nadelverschlussdüse am Anschnitt treffen, um Bindenähte zu vermeiden.
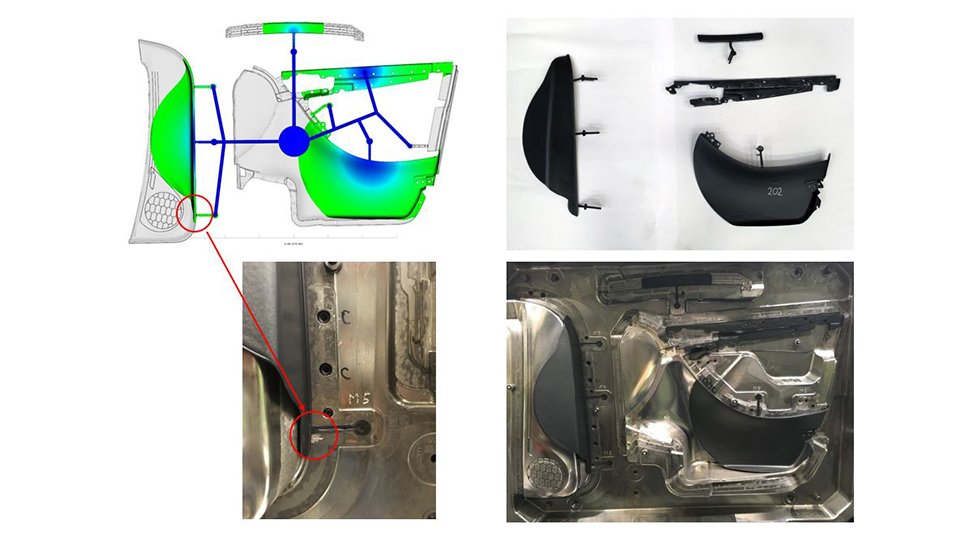
Simulation versus Realität: Bei allen Nadelverschlussdüsen wurde in der Simulation darauf geachtet, dass sich die Fließfronten der jeweiligen Kavität und der zu öffnenden Nadelverschlussdüse am Anschnitt treffen, um Bindenähte zu vermeiden.
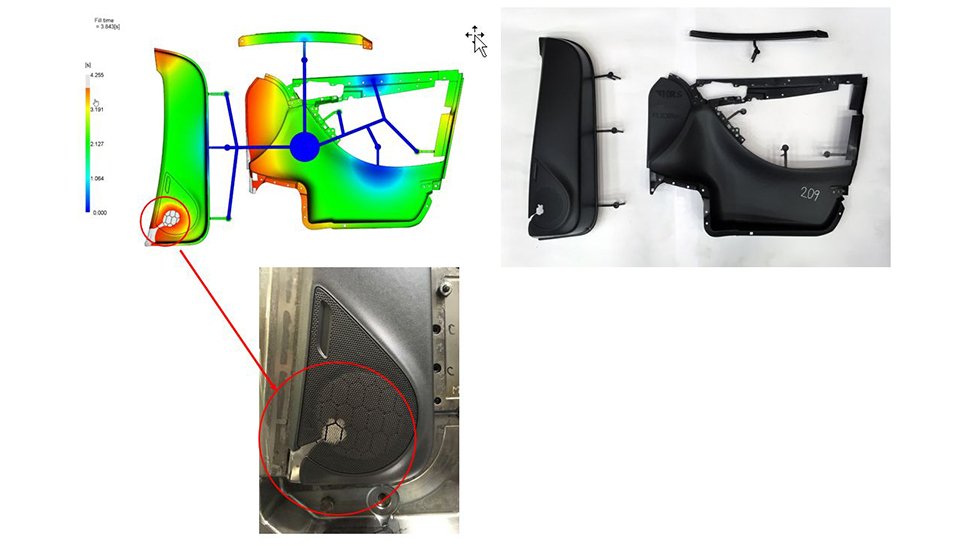
Momentaufnahme zum Zeitpunkt des Umschaltens von der geschwindigkeitsgeregelten Einspritzphase in die druckgeregelte Nachdruckphase: Auch hier lässt sich eine sehr gute Übereinstimmung zwischen Simulation und realer Produktion feststellen.
Realitätsnahe Simulation
Die Genauigkeit der Simulation hängt stark von der Modellierung und der Qualität der Materialdaten ab. Es handelt sich um ein „Müll-rein-Müll-raus“-System. Je realitätsnaher simuliert wird, desto besser sind die Ergebnisse und der Nutzen der Simulation. „sim link“ dient gleichermaßen als Postprozessor (Export von Ersteinstellungen für die Spritzgießmaschine) und Präprozessor (Import von Produktionsdaten).
Ziel ist es, für das jeweilige Spritzgießprodukt einen Ersteinstellvorschlag aus der Simulation zu generieren und die Qualität der Simulation mittels Feedbacks aus der Produktion kontinuierlich zu verbessern. Hierfür ist die Schnittstelle mit drei Funktionen ausgerüstet: Modifikation, Export und Import.
Die Funktion „Modifikation“ passt das Simulationsprofil auf die reale Dynamik der ausgewählten Maschine an und verbessert damit die Simulationsqualität deutlich. Damit können sowohl Maschinendynamik wie auch Maschinengrenzen bereits in der Simulation berücksichtigt werden und die Qualität deutlich verbessern. Mithilfe der Modifikation lässt sich abschätzen, ob das Produkt auch wirklich auf der gewählten Spritzgießmaschine produziert werden kann.
Die Funktion „Export“ erstellt aus der Simulation automatisch einen Teiledatensatz und überträgt diesen direkt an die Steuerung der Engel-Spritzgießmaschine. Dabei werden die Simulationseinstellungen so umgerechnet, dass sie von der Steuerung richtig interpretiert werden können. Auf diese Weise kann der Verarbeiter seine Einstellungen aus der Simulation mittels Knopfdrucks auf die Maschine übertragen und damit effizienter in die Produktion starten.
Die Funktion „Import“ überträgt reale Parameter und Messsignale aus der Produktionsmaschine zurück in das Simulationsprogramm und rechnet diese automatisch für die Simulation um. Mit diesem Feedback kann der Simulationstechniker die Qualität seiner Simulation überprüfen, Druckkurven vergleichen und weitere Expertise aufbauen.
In der aktuellen Version arbeitet „sim link“ mit zwei Simulationstools, mit Moldflow von Autodesk und mit Cadmould von Simcon. Die Datenschnittstelle ist für Engel Spritzgießmaschinen mit CC200- und CC300-Steuerung kompatibel und benötigt keine zusätzliche Soft- oder Hardware.
Datensicherheit hat Priorität
Im Engel-Kundenportal e-connect werden automatisch alle im Maschinenpark vorhanden Spritzgießmaschinen angezeigt, die mit „sim link“ arbeiten können. Generierte Teiledatensätze und Messungen lassen sich im „sim link data store“ einfach verwalten und abrufen.
Der Datensicherheit galt bei der Entwicklung der Schnittstelle das Hauptaugenmerk. Sensible Daten, wie CAD-Files oder Informationen über komplette Simulationsprojekte, verbleiben in den lokalen Systemen des Anwenders und werden nicht in die Engel-Systeme übertragen. Sie sind für die Benutzung von „sim link“ nicht erforderlich. Es werden jeweils nur die notwendigen Parameter und Einstellungen über die Schnittstelle transferiert, wobei der Anwender jederzeit die volle Transparenz über den Datenverkehr hat.
Der Datenaustausch zwischen Simulationsprogramm und e-connect erfolgt über einen lokalen Client, das „sim-link-Interface“. Nach der Modifikation oder dem Import von Produktionsdaten werden die Daten mit zusätzlichen Metainformationen versehen. Es wird dokumentiert, woher die Daten stammen und welche Randbedingungen wie Maschinentyp oder Schneckendurchmesser für die jeweilige Aktion geherrscht haben.
Nachbesserungen vermeiden
Gemeinsam mit den Partnerunternehmen Oerlikon HRSflow und Borealis hat Engel „sim link“ in der Praxis umfangreich getestet. Es wurde ein Familienwerkzeug mit drei Kavitäten und einer Heißkanalkaskade mit insgesamt acht servoelektrisch gesteuerten Düsen in Produktion genommen. Bei den Teilen handelte es sich um die Innenverkleidung einer Autotür, eine Kartentasche und ein Versteifungselement. Die Teile sollen aus Polypropylen mit sieben Prozent Mineralfüllung produziert werden.
Die Einstellungen für die Produktion der Teile sollten mittels Simulation bestimmt und optimiert werden. Bei der Optimierung standen eine konstante Fließfrontgeschwindigkeit über alle drei Kavitäten sowie die optimalen Schaltzeitpunkte der servoelektrischen Düsen des Heißkanals im Fokus. Neben dem Familienwerkzeug stellte das Abstimmen der Kaskadierung der Heißkanaldüsen auf die Fließfrontposition die größte Herausforderung dar.
Das Simulationsmodell wurde in Moldfow von Autodesk aufgebaut. Es umfasste die Kavitäten, das gesamte Heißkanalvolumen, die servoelektrischen Nadelverschlussdüsen sowie die Maschinendüse inklusive eines Teils des Schneckenvorraums. Ebenso wurde die Werkzeugkühlung mitmodelliert und simuliert.
Es wurde zunächst eine maschinenunabhängige Simulation unter Verwendung eines relativen Einspritzprofils durchgeführt. Hier erfolgte die Definition der Einspritzgeschwindigkeit als prozentualer Volumenstrom über den Füllgrad der Kavität. Dadurch ist die Schmelzfrontgeschwindigkeit an der Stelle X in der Kavität unabhängig von der Kompression im System.
Es sollte über den gesamten Füllprozess eine konstante Fließfrontgeschwindigkeit erreicht werden. Die Schaltzeitpunkte für die einzelnen Heißkanaldüsen wurden anhand der Fließfrontposition im Füllvorgang definiert. Es war vorgegeben, dass sich die Fließfront in der Kavität mit der Fließfront aus der Düse am jeweiligen Anschnitt trifft. Dies ist mit der initialen maschinenunabhängigen Simulation einfach möglich. Die Öffnungszeitpunkte der einzelnen Düsen sind somit vollständig voneinander und ebenso von der Kompression im System entkoppelt. Es konnte gezeigt werden, dass durch die Wahl einer maschinenunabhängigen Simulation auch ein komplexes System sehr schnell und mit wenigen Iterationen optimiert werden kann.
Kontinuierlich optimieren
In der maschinenunabhängigen Simulation wurden alle initialen Einstellungen ermittelt und diese mittels der „sim-link“-Funktion Modifikation für die gewählte Spritzgießmaschine angepasst. Die so erhaltenen maschinenabhängigen Einstellungen wurden erneut simuliert, um den Prozess auf Basis der Produktionsmaschine weiter optimieren zu können.
Da das Ergebnis mit den nun maschinenabhängigen und somit realitätsnahen Parametern sehr zufriedenstellend war, wurde für die Bemusterung mit der Funktion Export ein Ersteinstelldatensatz generiert und in die Steuerung der Produktionsmaschine übertragen.
Die Nadelöffnungseinstellungen wurden auf Basis der in der Simulation gewonnenen Werte in der HRS-FLEXflow-Steuerung manuell eingestellt.
Beim Anfahren der Spritzgießmaschine wurde der reale Umschaltpunkt nachträglich analog zur Simulation eingestellt. „sim link“ exportiert einen sicheren Wert, der bei Parameterungenauigkeiten in den Materialdaten oder Zylindertemperaturen keinesfalls zu einem Überspritzen der Kavitäten führen kann. Es waren keine weiteren Optimierungsschritte notwendig, um die Teile in der gewünschten Qualität zu produzieren.
Für Folgeprojekte lernen
Um dem Simulationstechniker ein Feedback hinsichtlich der Verwendbarkeit der in der Simulation ermittelten Einstellparameter zu geben, wurden die im realen Prozess verwendeten Teiledaten und Messergebnisse aus der Maschine wieder zurück in das Simulationsprogramm übertragen. Da „sim link“ die Ist-Daten aus der Produktion automatisiert aufbereitet und einspielt, kann der Simulationstechniker sofort mit der Nachsimulation starten.
„sim link“ ist ein vielseitiges Tool, das die Expertise des Simulationstechnikers direkt in die Produktion übermittelt. Bereits im Vorfeld des Serienstarts kann überprüft werden, ob die für die Produktion vorgesehene Spritzgießmaschine auch tatsächlich für das Produkt geeignet ist. Durch die Modifikation von Simulationsparametern entsprechend der gewählten Spritzgießmaschine können komplexere Einspritzprofile verwendet und die Zykluszeit realitätsnah abgeschätzt werden. Das Feedback aus der Produktion hilft, die Qualität der Simulation zu erhöhen.
Kontakt
Alfred Angerer
Entwicklungsingenieur im Bereich smart production
ENGEL AUSTRIA GmbH
Schwertberg
Österreich
Tel. +43 50 620 0
E-Mail senden