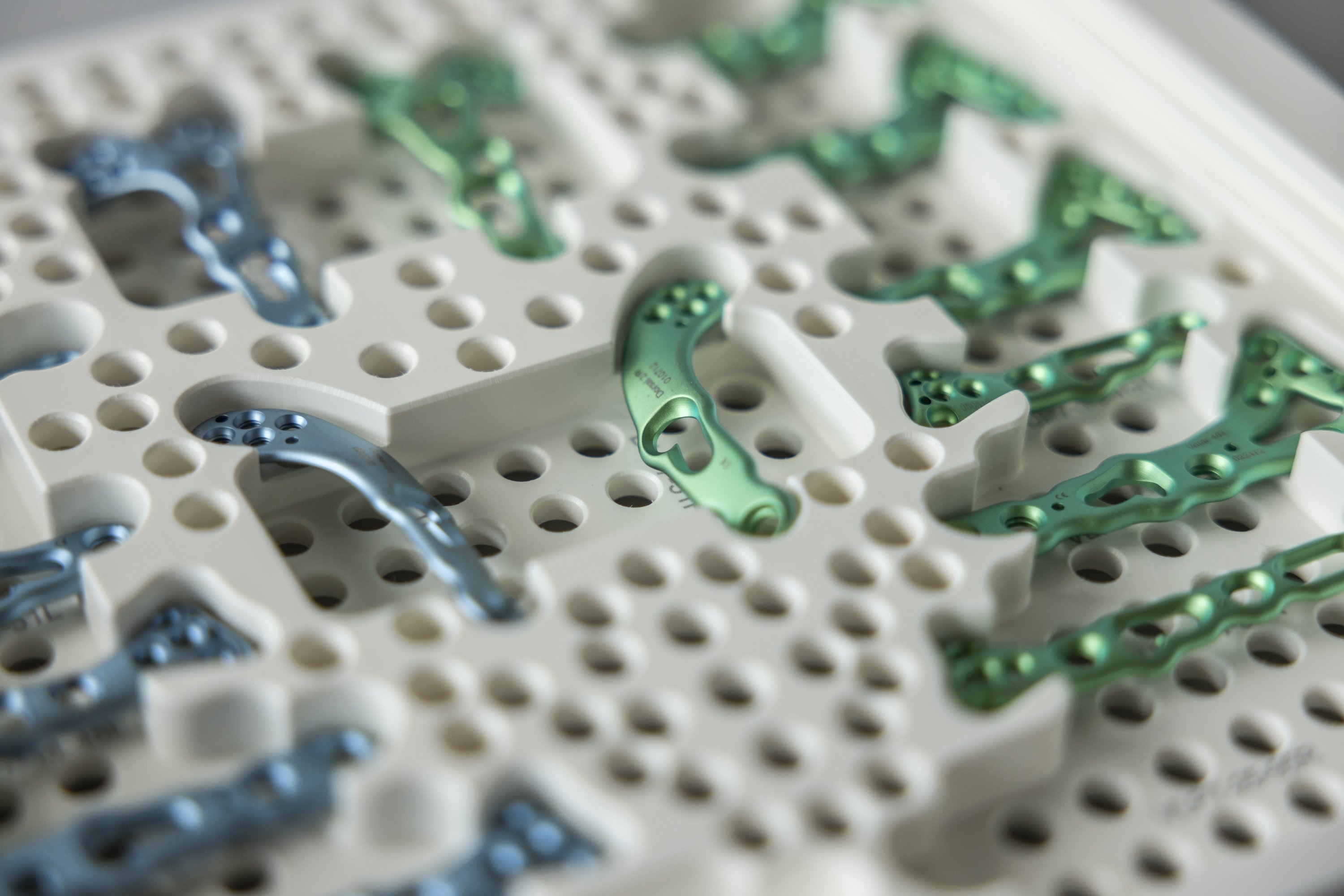
Automatisierung
Zeitbrecher für Knochenheiler
Medizintechniker nehmen es ganz genau. Um orthopädische Implantate fristgerecht in höchster Qualität liefern zu können, setzt hg medical auf knapp zwei Dutzend 5-Achs-Bearbeitungszentren von Hermle. Bei der jüngsten Investition entschied sich der Lohnfertiger erstmals für eine Roboterautomation – und profitiert in mehrfacher Hinsicht.
Florian Lukats sieht schon an den Auftragsbüchern, wann Winter ist. Er leitet die Fräserei bei hg medical in Raisting, einer Gemeinde am südlichen Ende des Ammersees. Der Lohnfertiger hat sich auf die besonderen Bedürfnisse der Medizinbranche spezialisiert. Im Winter steigt die Nachfrage nach den Produkten, die dort im Dreischichtbetrieb entstehen: orthopädische Implantate zur Osteosynthese. Die kleinen Platten – oft aus Titan, manchmal aus Edelstahl – überbrücken Frakturen und ermöglichen so ein natürliches Zusammenwachsen des Knochens in kürzerer Zeit.
Das Unternehmen begann 2007 mit zwei Fräsautomaten, zwei Drehmaschinen und zwei Mitarbeitern. Heute sind allein in Raisting etwa 190 Personen beschäftigt. Das 2015 gegründete Zweitwerk in den USA zählt mittlerweile rund 40 Angestellte. Die maschinelle Ausstattung ist ebenfalls gewachsen: „Wir haben 19 Bearbeitungszentren von Hermle in Deutschland und vier in den USA, weitere fünf sind in Raisting geplant. Zusätzlich bauen wir gerade in den USA unser drittes Werk auf, das von der Kapazitätsgröße her identisch zu diesem sein soll“, erläutert Lukats.
Der starke Bezug zu den Vereinigten Staaten ist historisch bedingt: hg medical ist aus dem europäischen Vertriebszentrum eines amerikanischen Anbieters orthopädischer Hilfsmittel und Schuhe entstanden. „Bis heute sind 90 Prozent unserer Kunden in den USA zuhause“, ergänzt Lukats.
Wer so erfolgreich wächst, dem wird es schnell zu eng. Das ist auch am oberbayerischen Standort sichtbar. Zunächst fanden Dreherei, Fräserei und Analyse in einem Gebäude Platz, wo auch der komplette Second Process stattfand: von der Oberflächenbehandlung über die Qualitätskontrolle bis hin zur Verpackung. Als es zu eng wurde, baute das Unternehmen direkt nebenan und verlagerte die Fräserei. Weiteres Wachstum erforderte eine dritte Halle. „Dadurch ist dieser Standort sehr verschachtelt“, begründet Lukats. „Und wir sind noch lange nicht am Ende des Ausbaus. Nur hier in Raisting haben wir keine Kapazitäten mehr. Darum geht es jetzt in die USA.“
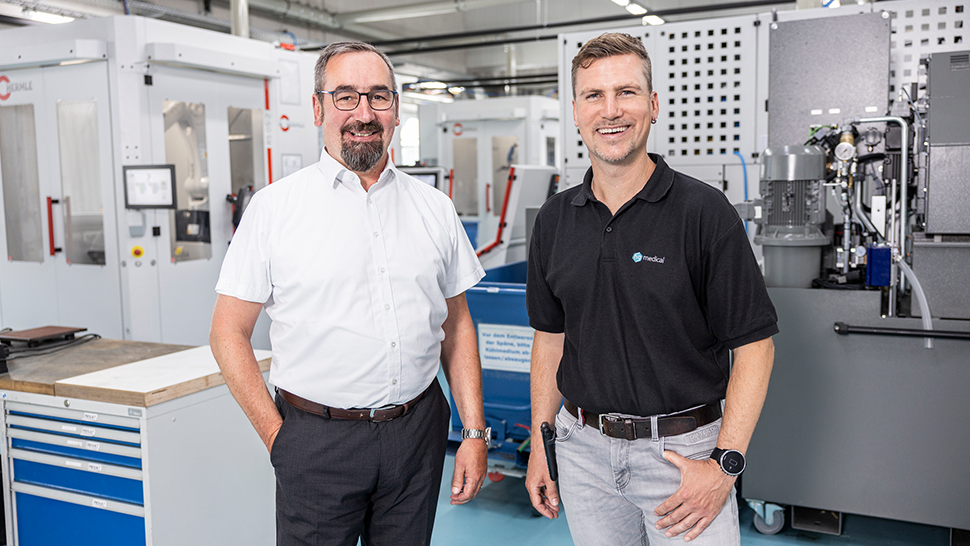
Stefan Bux (links) von der HPV Hermle Vertriebs GmbH und Florian Lukats (rechts) von der hg medical GmbH.
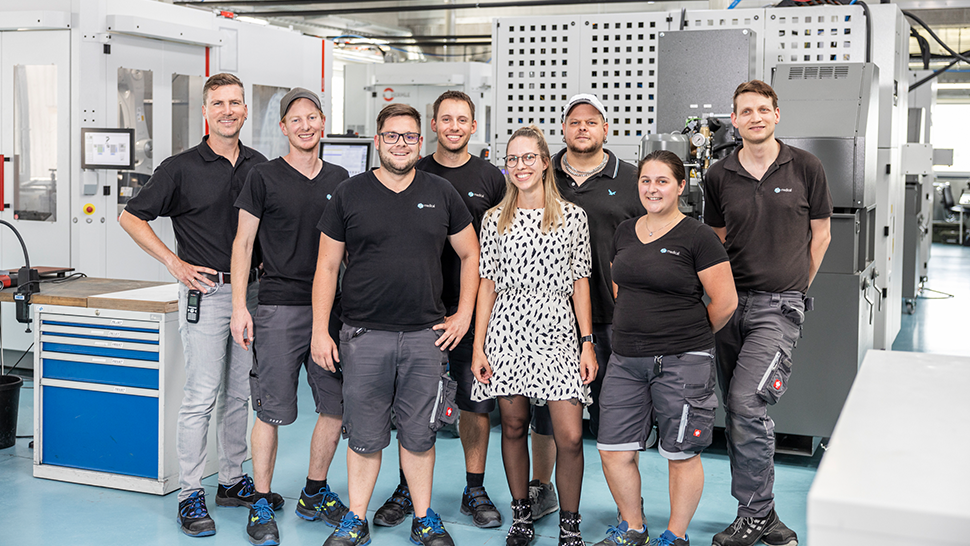
Fräser-Team der hg medical: (von links) Florian Lukats, Stefan Hannweber, Max Schade, Manuel Moritz, Andrea Huber, Basti Müller, Lisa Leiß und Franz Settele.
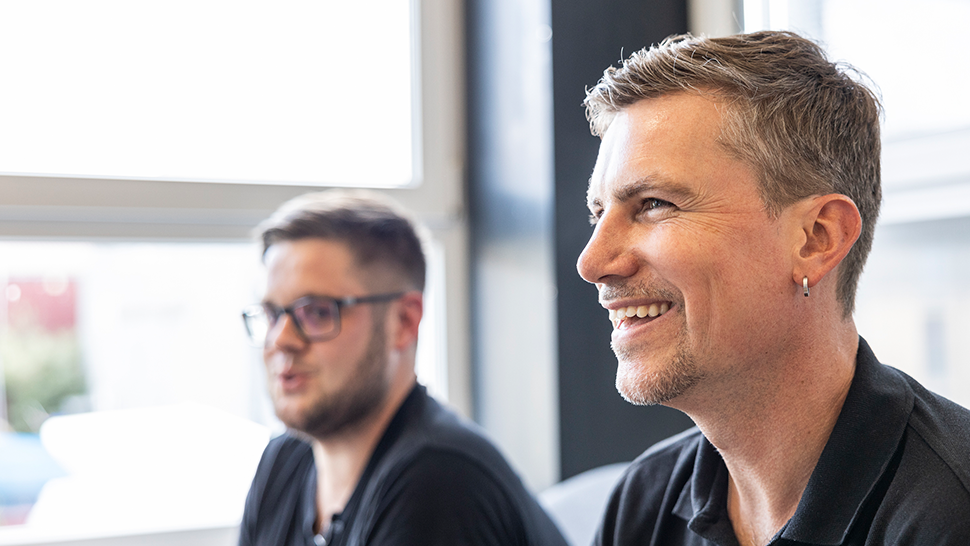
Abteilungsleiter Florian Lukats (rechts) mit CNC-Fräser Max Schade.
Damit es keinen Schaden anrichtet
Für den Anspruch an die Teile des Lohnfertigers spielt der Standort der Kunden keine Rolle – die zulassenden Behörden wie die Food and Drug Administration (FDA) sind überall streng. Toleranzen, Oberflächengüte und die allgemeine Qualität müssen stets auf oberstem Niveau sein.
„Das fängt bei der optischen Qualität an, geht über die Maßhaltigkeit bis hin zur Dokumentation“ erklärt Lukats. Es ist zudem wichtig, dass das Kühlmittel passt und die Fette, Öle und Schmierstoffe von den Arzneimittelbehörden freigegeben sind. Nach dem ganzen Verarbeitungsprozess dürfen keine Rückstände mehr auf dem Implantat vorhanden sein, die den menschlichen Körper schädigen könnten. „Bei den Bearbeitungstoleranzen bewegen wir uns innerhalb von wenigen hundertstel Millimetern“, greift Lukats eine Anforderung auf, die hg medical letztlich zu Hermle geführt hat.
„Hermle liefert die Qualität, Präzision und Genauigkeit, die wir brauchen. Besonders bei der Fünf-Achs-Simultanbearbeitung der freigeformten Implantate“, begründet Lukats die starke Präsenz dieser Maschinen am Hauptsitz. Sie füllen eine komplette Halle, tragen alle eine eigene Nummer zur eindeutigen Identifikation, stehen geordnet, aber nicht sortiert. Das hat mit der Dokumentationspflicht und dem organischen Wachstum zu tun: Jedes 5-Achs–Bearbeitungszentrum ist zertifiziert, weswegen das Unternehmen die interne Maschinenbezeichnungen nicht ändern kann. Ein Umstellen ist aufgrund der engen Platzverhältnisse auch nicht mehr möglich.
Erste Roboter im Einsatz
Seit Anfang 2023 stehen vier weitere Bearbeitungszentren vom Typ C 12 U RS 05 in der Fräshalle. Bisher automatisierte hg medical alle Maschinen mit dem IH-Handlingsystem. Bei den vier neuen Anlagen greifen erstmals Roboter zu. Sie legen Rohteile in den Spannstock, spannen das Halbfertigteil um und entnehmen das fertig gefräste Implantat.
An den anderen Anlagen versorgt jeweils ein Werkstückwechsler die Fräszentren mit vorgespanntem Material und ermöglicht so den personenlosen Automatikbetrieb. „Wir haben viele Kleinserien. Der Investitionsplan für die RS 05-Anlagen stand, nachdem ein Kunde deutlich größere Stückzahlen seiner Produkte bestellte. Wir wollten schneller werden und den personellen Aufwand verringern“, berichtet Lukats. Wie? Indem die robotergestützten Fräszentren einen Arbeitsschritt übernehmen, der bis dato nur manuell möglich war.
„Bisher frästen wir die Implantate in einer Aufspannung. Dabei bleiben zwei Support-Stäbchen stehen, die wir herausbrechen und deren Reste manuell verschleifen müssen“, erläutert Lukats. Damit die C 12 U den kleinen Überstand wegfräsen kann, braucht es eine zweite Spannung und einen Greifer, der das Bauteil umsetzt.
Das Besondere: Um dabei äußerst präzise zu arbeiten, ist die Aufnahme das Negativ der Knochenplatte. „Nach dem ersten Fräsvorgang nimmt der Greifer das halbfertige Implantat und legt es in die Negativmatrize ein. Positionsbohrungen sichern die exakte Lage, so dass die Maschine die Oberfläche ebenso genau bearbeiten kann wie in der ersten Spannung.“ So kommt die Platte nach 19 bis 25 Minuten fertig heraus und ist frei für die Oberflächenbehandlung und Qualitätsprüfung.
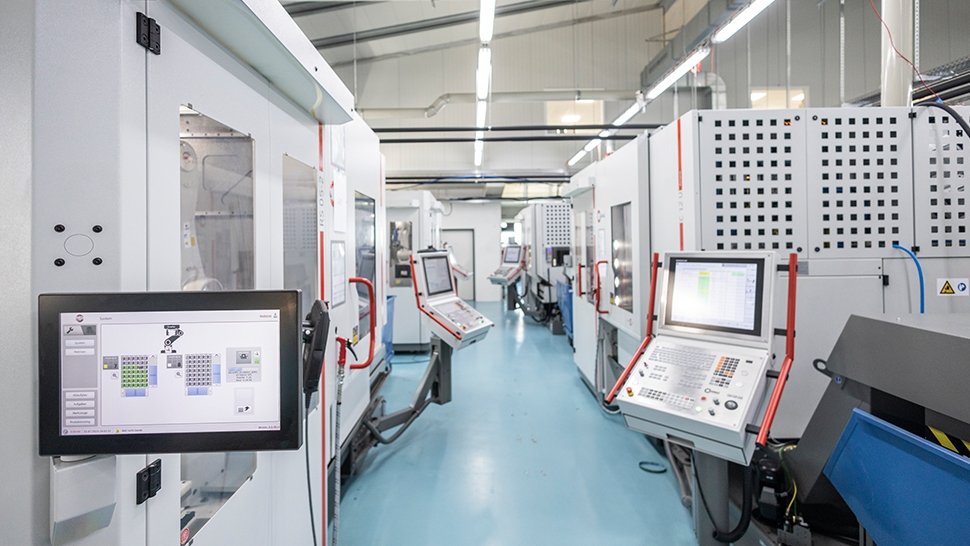
Eine Halle voller Hermle-Maschinen: hg medical vertraut auf die Präzision und den schnellen Service, den der Gosheimer Maschinenbauer verspricht.
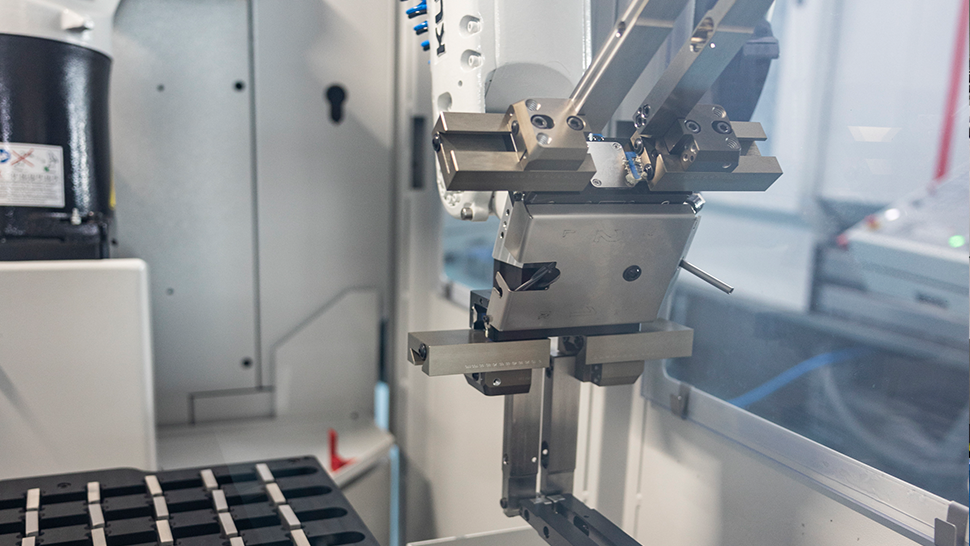
Der Greifer des Roboters ist komplett aus Edelstahl – Aluminium würde die medizinischen Implantate kontaminieren.
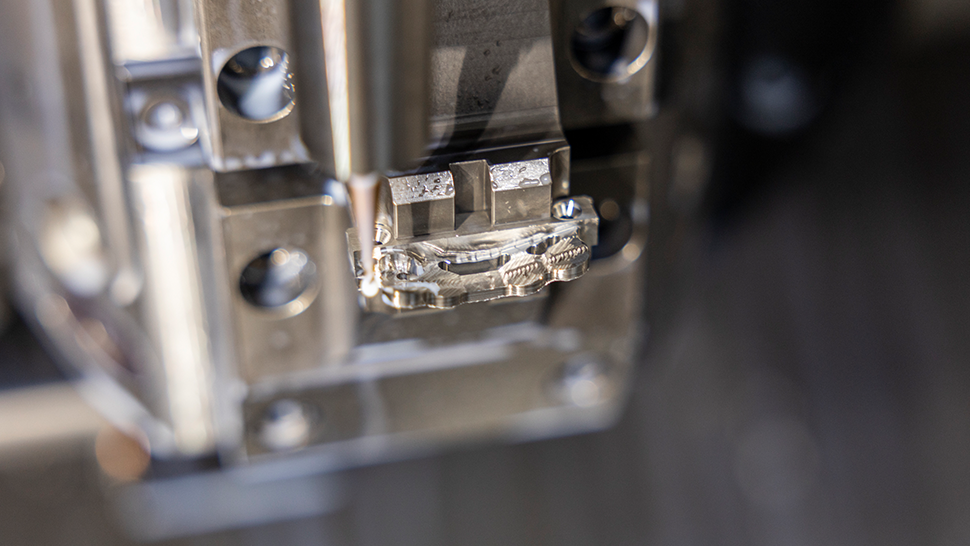
Dank Roboter kann hg medical die Implantate in einem Durchgang komplett fräsen.
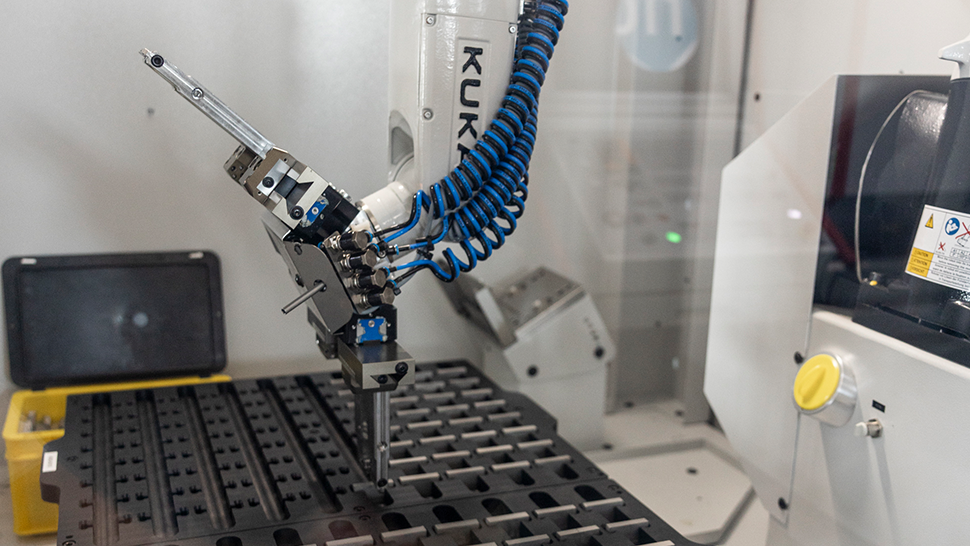
Die Matrizen bevorraten genügen Rohmaterial, damit die C 12 U übers Wochenende beschäftigt ist.
Dreifacher Gewinn
„Wir haben hohe Erwartungen an die Roboterautomation: Sie sollte Zeit und Aufwand einsparen, bei gleichbleibender oder sogar besserer Qualität. Das hat Hermle umgesetzt“, lobt Lukats. hg medical spart sich das manuelle Verschleifen, das zudem immer ein Risiko für Fehler barg. Das Unternehmen optimiert dazu noch die Vorarbeit: Statt die Rohlinge vorzuprägen und in die Schraubstöcke zu spannen, wie es die andere Automation erfordert, schiebt der Bedienende einfach eine Matrize mit den Titan- oder Edelstahlplatten in die Roboterzelle.
Abgesehen davon punkten die Hermle-Roboter auch noch auf eine ganz andere Art, wie Lukats abschließend erwähnt: „Moderne Hightech-Maschinen begeistern die Leute. Die neue Technologie ist ein Motivationsschub für unsere Mitarbeitenden und beflügelt unser Wachstum.“
Titelfoto: Orthopädische Implantate halten Knochenfragmente zusammen und beschleunigen die Heilung der Fraktur.
Kontakt
Udo Hipp
Leiter Marketing
Maschinenfabrik Berthold HERMLE AG
Gosheim
Tel. +49 7426 95-6238
E-Mail senden