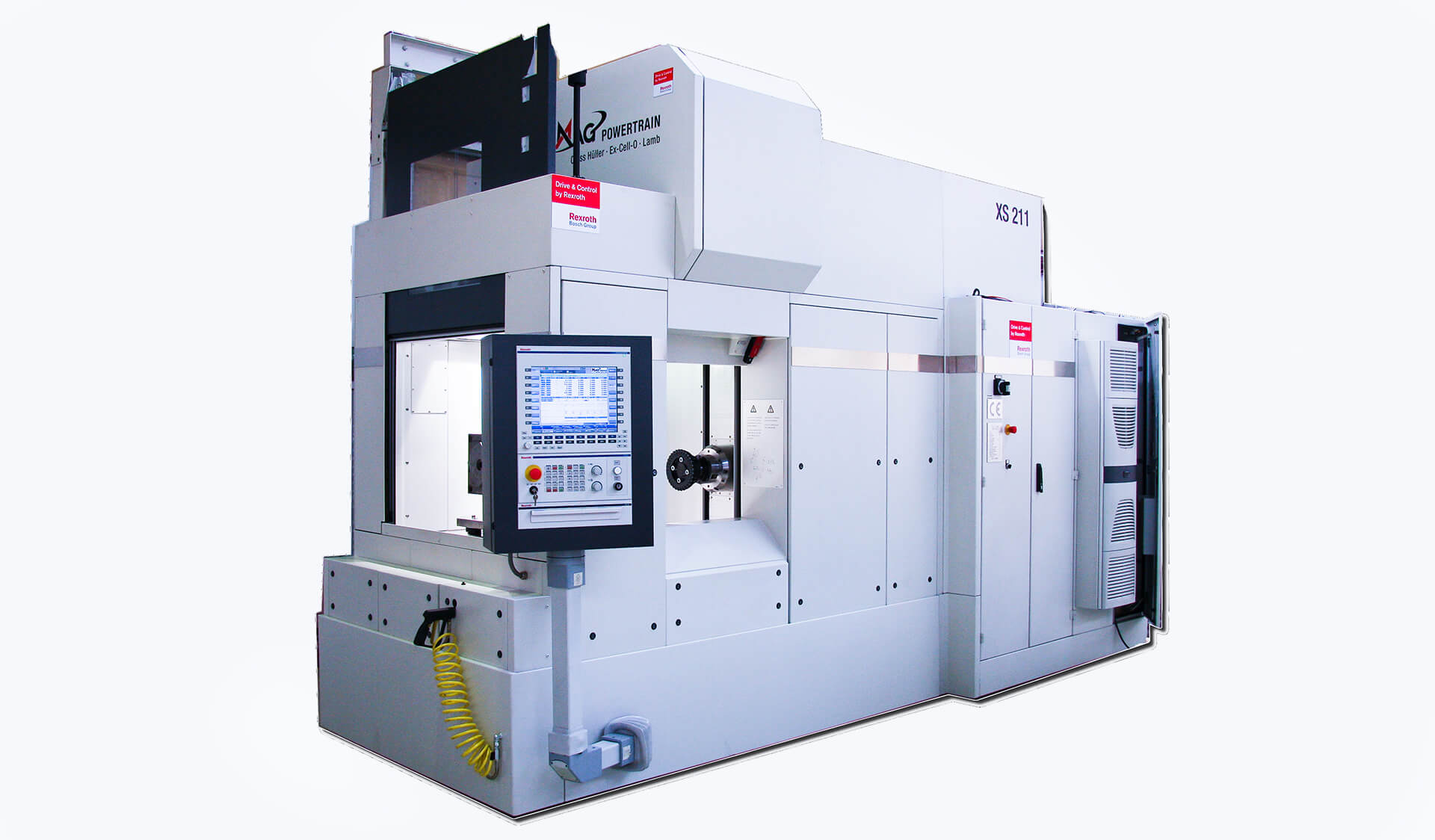
Titelthema
Werkzeugmaschine
mit Spareffekt
Ausgehend von einer Untergliederung der Werkzeugmaschine in einzelne Funktionsmodule oder Verbrauchsgruppen sind unterschiedliche Konfigurationen zur Verbesserung des Energieverbrauchs einer Werkzeugmaschine möglich. Im Rahmen eines vom Bundeswirtschaftsministerium geförderten Projekts wurden sie an einem Demonstrator umgesetzt. Mit dieser Methode lässt sich anhand der Konfigurationsalternativen und der Bearbeitungsaufgabe die energieoptimale Maschine konfigurieren.
Für die Etablierung einer solchen Methode sind Standards und Richtlinien zwischen den Maschinenherstellern sowie den Lieferanten der Komponenten oder Funktionsmodule zu definieren, so dass eine geeignete Kennliniendatenbank für die praktische Anwendung geschaffen wird. Die Methode ist sowohl bei der Neuentwicklung als auch beim Retrofitting bestehender Anlagen anwendbar. Das wachsende Bewusstsein für umweltgerechte Produkte und deren Herstellung sowie Kostensteigerungen für Energie führt zu einer wachsenden Nachfrage nach Energieeffizienzlösungen in der industriellen Produktion. Da energiesparende Produkte häufig mit Mehrkosten bei den Investitionen verbunden sind, liegt die Schwierigkeit für Hersteller und Betreiber von Produktionsmaschinen darin sowohl energieeffiziente als auch wirtschaftlich sinnvolle Lösungen auszuwählen. Am Beispiel eines Bearbeitungszentrums werden Möglichkeiten zur energieeffizienten Konfiguration von Werkzeugmaschinen aufgezeigt. Zudem wird eine Methodik vorgestellt, die den Energieverbrauch der Konfigurationsalternativen abschätzt. Im Forschungsprojekt MAXIEM ist eine Energieverbrauchsanalyse von Werkzeugmaschinenkomponenten durchgeführt worden. Sie bildet die Basis für eine Bewertung verschiedener Energieeffizienzmaßnahmen. Um die ermittelten Potenziale wirtschaftlich zu nutzen, muss bereits in der Projektierungsphase einer Werkzeugmaschine eine effiziente Konfiguration gewählt werden.
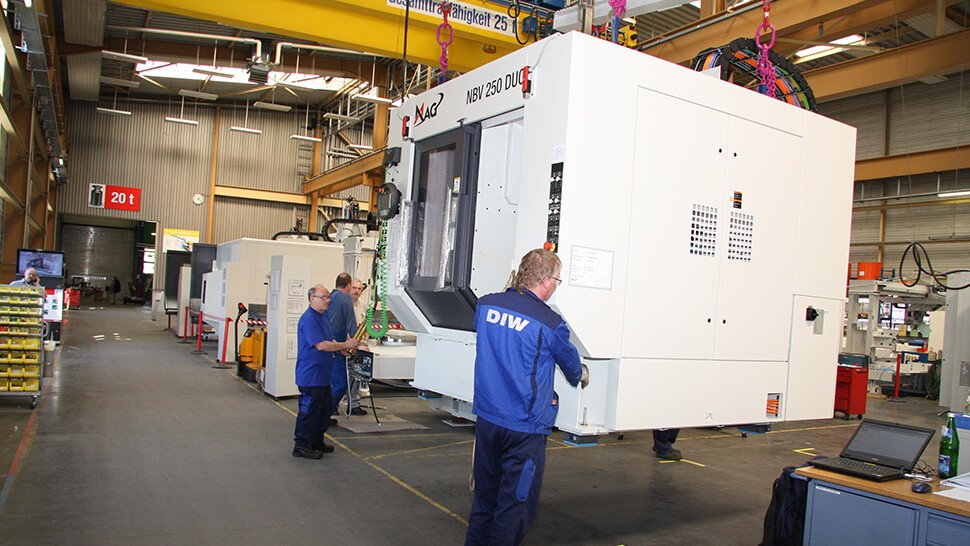
Foto: Dlugosch
Gemeinsam mit den Industriepartnern wurde eine Methodik entwickelt, die es dem Maschinenhersteller erlaubt den Energieverbrauch verschiedener Konfigurationsalternativen zu ermitteln, basierend auf einem anwenderspezifischen Nutzungsprofil. Die Methodik ergänzt die von den Maschinenherstellern durchgeführten Zeitstudien, in denen einzelne Bearbeitungsschritte und die zugehörigen Maschinenzustände sowie Zerspanungsparameter definiert werden. Um die für den Energieverbrauch optimale Konfiguration der Werkzeugmaschine zu finden, ist eine geeignete Untergliederung der Werkzeugmaschine vorgenommen worden. Für die funktionalen Einheiten ist der Begriff Verbrauchsgruppe eingeführt worden. Darunter werden Komponenten verstanden, die im System zusammenarbeiten und an der Ausführung bestimmter Funktionen beteiligt sind. Die Methodik wurde an einem Demonstrator umgesetzt.
Die Analyse des Energieverbrauchs der einzelnen Funktionsmodule hat zu den Kühlschmierstoffanlagen, zur Maschinenkühlung und zur Hydraulik als energieintensivste Module geführt.
Konfigurationsalternativen
Das Hydraulikaggregat, das nach dem Konzept des Speicherladebetriebs arbeitet, besteht aus einer Innenzahnradpumpe mit einem netzbetriebenen Asynchronmotor als Antrieb. Fällt der Druck im Speicher unter 115 bar, so wird die Pumpe über ein Ventil vom drucklosen Umlauf in den Förderbetrieb geschaltet. Bei Erreichen von 120 bar wird die Pumpe über ein Ventil vom System getrennt, und sie arbeitet dann im drucklosen Umlauf. Im Maschinenzustand Grundlast wird die Pumpe alle 27 Sekunden zur Deckung von systembedingten Leckageverlusten in den Schieber- beziehungsweise Druckregelventilen für kurze Zeit zugeschaltet. Durch den Einsatz von Sitzventilen anstelle der Schieberventile kann die Leckage soweit reduziert werden, dass die Pumpe erst nach mehr als sieben Minuten wieder in den Förderbetrieb geht.
Durch den drucklosen Umlauf und die Leckage wird eine große Wärmemenge in das Öl eingetragen, so dass zusätzlich Energie für den Rückkühler aufgebracht werden muss, um das Öl zu kühlen. Der drucklose Umlauf wird vermieden, indem durch einen größeren Speicher sowie eine Vergrößerung der Hysterese auch im Lastbetrieb die Zuschalthäufigkeit der Pumpe herabgesetzt wird. Der Pumpenantrieb kann abgeschaltet werden, ohne die zulässige Einschalthäufigkeit des antreibenden Asynchronmotors zu überschreiten. Auf diese Weise wird der Wärmeeintrag in den Ölkreislauf reduziert und der Rückkühler entlastet. Für die Rückkühler wurden nur Konfigurationsalternativen verglichen, die in der Lage sind, bei der Temperaturregelung eine Hysterese von plusminus 0,5 Kelvin einzuhalten. Ein taktender Betrieb ist dann in der Regel aufgrund von Restriktionen der Tankgröße nicht mehr möglich, da sich die häufigen Schaltvorgänge negativ auf die Lebensdauer des Verdichters auswirken. Die Temperaturregelung mittels Heißgas-Bypass stellt den Stand der Technik dar. Der Verdichter ist dabei als Dauerläufer ausgeführt, das heißt, er verrichtet kontinuierlich maximale Arbeit.
Im Teillastbetrieb öffnet das Bypass-Ventil und spritzt das verdichtete, heiße Kältemittel am Verflüssiger vorbei direkt vor dem Verdampfer ein. Die überschüssige Kühlleistung wird somit aktiv vernichtet, so dass im Teillastbereich ein sehr geringer Energieeffizienz vorliegt. Eine Möglichkeit die Kühlleistung an den aktuellen Bedarf anzupassen, stellen Digital-Scroll-Verdichter dar. Bei diesem Funktionsprinzip läuft der Verdichter dauerhaft mit konstanter Drehzahl. Über ein Magnetventil und die mechanische Trennung der Verdichterspiralen kann die Kompression variiert werden. Dadurch lässt sich mithilfe einer pulsweitenmodulierten Ansteuerung eine Leistungsregelung von zehn bis 100 Prozent verwirklichen.
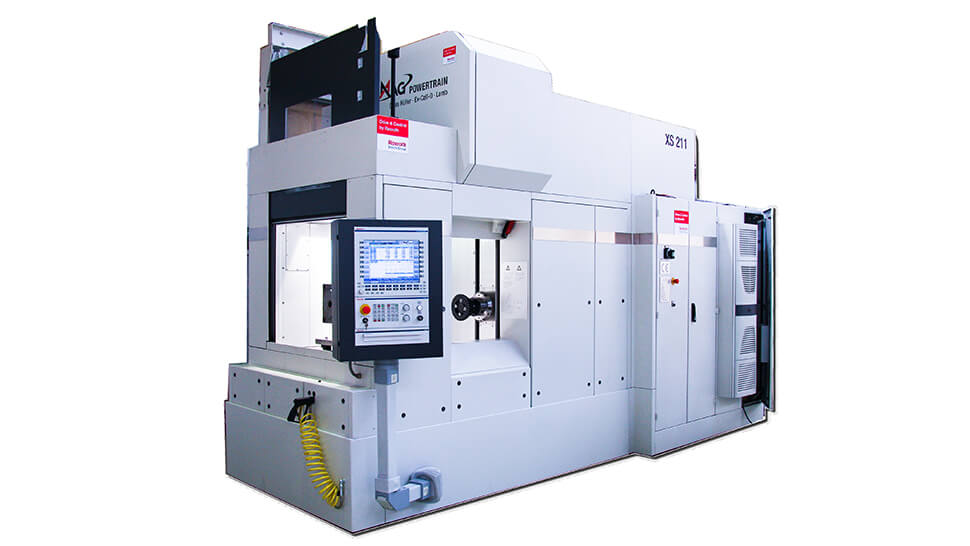
Foto: PTW
Abhängig von der maximalen Kühlleistung und dem Lastzustand der Maschine werden so im Teillastbetrieb bis zu 30 Prozent Energie einsparen. Eine weitere Variante, die Kühlleistung bei Teillast an den aktuellen Bedarf anzupassen, besteht darin, die Drehzahl des Kompressors durch einen Frequenzumrichter zu regeln. Solche invertergeregelten Kompressoren liefern im Verbund mit drehzahlgeregelten Verflüssiger-Lüftern und elektronischen Expansionsventilen durch Anpassung der Motordrehzahl immer nur so viel Kühlleistung, wie gerade gefordert ist. Sind die Restriktionen hinsichtlich der Tankgröße nicht gegeben, und ein ausreichend großes Tankvolumen kann installiert werden, bietet die Kaltwasserbeimischung ebenfalls großes Potenzial für eine effiziente Temperierung mit getaktetem Verdichterbetrieb. Der große Tank dient bei diesem Prinzip als Kaltwasserspeicher. Innerhalb des Speichers befindet sich ein abgegrenzter Bereich aus dem das Kühlwasser entnommen wird. In diesem Bereich wird über Regelventile das warme Wasser des Rücklaufs mit dem Kaltwasser aus dem umgebenden Tank so gemischt, dass die Solltemperatur erreicht wird. Im Teillastbetrieb wird ein Teil des Rücklaufs unter Beimischung von Tankwasser über den Verdampfer geleitet und gekühlt, ehe er wieder in den Tank beziehungsweise Mischungsbereich geleitet wird. Auf diese Weise wird im Teillastbereich das im Tank befindliche Wasser bis auf ein festgelegtes Temperaturniveau abgekühlt, so dass Kompressor und Lüfter abgeschaltet werden. Bis zum Erreichen der oberen Grenze der Temperaturhysterese wird die Vorlauftemperatur nur durch Beimischung von Kaltwasser aus dem Speicher geregelt.
Je nach Ausgangstemperatur im Tank und Last nach dem Einschalten der Anlage muss zunächst Energie aufgebracht werden, um das Tankvolumen unter das gewünschte Vorlauftemperaturniveau zu kühlen, dadurch kann das Einregeln auf die Vorlauftemperatur etwas länger dauern als bei den voran vorgestellten Systemen. Ebenso muss auch ohne externe Last beachtet werden, dass Verluste durch einen Wärmeaustausch mit der Umgebung auftreten können.
Die Hauptverbraucher des KSS-Systems des Demonstrators sind die vier eingesetzten Pumpen. Im Niederdruckteil (KSS-ND) versorgt eine Pumpe Bettspülung und Arbeitsraumdusche, während eine zweite den Zulauf zum Hochdruckteil (KSS-HD) realisiert. Die Hochdruckpumpe stellt die innere Kühlmittelzufuhr durch die Spindel sicher. Die vierte Pumpe ist eine niveaugesteuerte Hebepumpe, um den KSS zurück in den Tank zu fördern.
Sobald die Freigabe für den KSS durch die Steuerung erfolgt, laufen alle Pumpen an. Solange keine Anforderung per Steuerungsaufruf für KSS-HD erfolgt befindet sich die Pumpe im drucklosen Umlauf. Ebenso wird über ein Druckregelventil je nach Anlagenkennlinie des innengekühlten Werkzeugs der zu viel geförderte Volumenstrom in den Tank zurückgeleitet. Eine drehzahlgeregelte Pumpe stellt eine deutlich effizientere Alternative dar, da diese sich in ihrer Leistungsaufnahme dem geforderten Druck und dem sich einstellenden Volumenstrom anpasst.
Die KSS-HD-Anlage beeinflusst auch den Niederdruckteil, der den Zulauf für die Hochdruckseite gewährleistet. Bereits eine optimale Auslegung von Konstantpumpen ermöglicht eine deutliche Verbrauchsreduktion. Eine weitere Steigerung durch drehzahlgeregelte Systeme ist den höheren Investitionskosten gegenüberzustellen. Die optimale Konfiguration für die Demonstratormaschine konnte durch Substitution der zwei ungeregelten ND-Pumpen durch eine drehzahlgeregelte Pumpe erreicht werden.
Ermittlung der Lastprofile
Die Grundlage zur Auswahl geeigneter Konfigurationsalternativen ist die Analyse der späteren Nutzung. Sowohl Nutzungszeiten und Betriebszustände der Werkzeugmaschine selbst als auch die hierdurch induzierten Nutzungszeiten und Betriebszustände der einzelnen Verbrauchsgruppen sind in die Berechnung einzubeziehen. Die im Rahmen des Projekts Maxiem entwickelte Methode zielt darauf ab, dem Maschinenhersteller während der Projektierung von Werkzeugmaschinen für die Großserienproduktion ein Hilfsmittel an die Hand zu geben, um den Energieverbrauch verschiedener Konfigurationsalternativen abzuschätzen. Drei Phasen können unterschieden werden.
In Phase 1 werden verschiedene Informationen im Rahmen eines Lastenheftes abgefragt. Da der konkrete Nutzen von Energieeffizienzmaßnahmen neben der Art der Nutzung vor allem von der Nutzungsdauer determiniert wird, müssen die voraussichtliche Betriebsmittelnutzungszeit, das heißt, die Betriebszustände der Werkzeugmaschine und deren zeitliche Verteilung abgeschätzt werden. In Anlehnung an VDI 3423 wird nach
- Belegungszeit und
- nicht geplanter Zeit
unterschieden.
Die Belegungszeit teilt sich auf in
- Nutzungszeit der Maschine,
- organisatorische Ausfallzeit,
- Zeitanteile für Rüsten, Einrichten und Werkzeugwechsel sowie
- Pausen.
Unter Nutzungszeit werden Zeiten verstanden, in denen eine Maschine ohne technische oder organisatorische Störungen im Rahmen der geplanten Taktzeiten Werkstücke bearbeitet. Für organisatorische Ausfallzeiten und Pausen sowie in der nicht geplanten Zeit werden vom Anwender verschiedene Anlagenzustände, zum Beispiel verschiedene Stand-by-Modi, definiert, in die eine Maschine versetzt werden soll, um nach einer vordefinierten Zeit wieder betriebsbereit zu sein. Zusätzlich werden in Phase 1 Informationen zur Produktionsinfrastruktur und -Umgebung abgefragt. Hierbei ist zu klären, welche Medien zentral bereitgestellt werden können und welche Kostensätze hierfür anzusetzen sind. Abschließend werden im Lastenheft Informationen über die Methode zur Berechnung der Wirtschaftlichkeit einzelner Effizienzmaßnahmen abgefragt.
Das Ergebnis von Phase 2 ist eine Abschätzung des zu erwartenden Energieverbrauchs einzelner Konfigurationsalternativen basierend auf den Informationen aus dem Lastenheft. Zunächst stellt der Maschinenanwender dem Maschinenhersteller weitere Informationen über das zu fertigende Werkstück zur Verfügung. In der Automobilindustrie ist es üblich, dass ein Roh- und Fertigteil an den Maschinenhersteller übergeben wird, sowie eine Taktzeit definiert wird. Auf Basis dieser Informationen führt der Maschinenhersteller eine Zeitstudie durch.
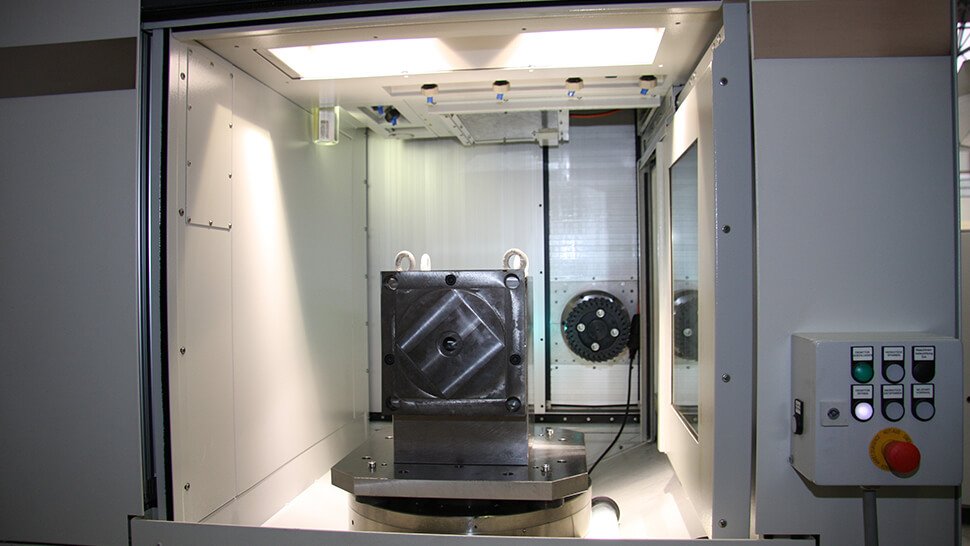
Foto: PTW
Dieser Arbeitsschritt wurde im Rahmen des Projekts Maxiem als Ansatzpunkt für Energieverbrauchsberechnungen identifiziert. Das Ziel der Zeitstudie ist eine Dekomposition eines Bearbeitungstakts in die Bearbeitungsschritte. Damit werden in der Phase der Maschinenprojektierung die Anteile für Haupt- und Nebenzeiten bewertet. Diese bestehende Methodik wurde genutzt, um Energieverbrauchsberechnungen durchzuführen. Basierend auf den Angaben zu Bearbeitungsparametern, Verfahrbewegungen, Werkzeugwechseln und Betriebsmodi der beteiligten Verbrauchgruppen, kann der jeweilige Lastverlauf abgeleitet werden. Mithilfe einer Kennliniendatenbank zu den vorhandenen Alternativen, in welcher der Energiebedarf verschiedener Lastpunkte hinterlegt ist, wird der Energiebedarf der einzelnen energiebetriebenen Aggregate in den verschiedenen Betriebsmodi prognostiziert.
In Phase 3 stellt der Produktionsmittelhersteller abschließend die Konfigurationsalternativen gegenüber. Hierzu nutzt er die in Phase 1 erhaltenen Daten zu der geplanten Nutzung der Werkzeugmaschine. Zusätzlich fließen die in Phase 2 erworbenen Erkenntnisse über den erwarteten Energiebedarf während der Nutzungszeit, sowie in den sonstigen vordefinierten Betriebszuständen der Werkzeugmaschine in die Berechnung mit ein. Abschließend kann der Werkzeugmaschinenhersteller dem –Anwender die verfügbaren Energieeffizienzoptionen, den Nutzen und die voraussichtliche Amortisation der verschiedenen Effizienzmaßnahmen darstellen.
Spezifische Ermittlung des Energiebedarfs
Soll beispielsweise der notwendige Energieeinsatz für ein dezentrales Rückkühlaggregat bestimmt werden, muss zunächst die Verlustleistung in den einzelnen zu kühlenden Komponenten abgeschätzt werden. Der Verlauf der Verlustleistungen dient als Eingangsparameter zur Energiebedarfsermittlung im Rückkühlaggregat. Werden Hauptspindelantrieb und Hydrauliköl aktiv gekühlt, ist zunächst deren Lastprofil über einen Bearbeitungstakt zu ermitteln. Dieses ergibt sich für den Hauptspindelantrieb aus vier Bestandteilen:
- Grundlast des Hauptspindelantriebs
- Leistung im Spindelleerlauf bei Bearbeitungsdrehzahl
- Energiebedarf zum Beschleunigen und Abbremsen der Spindel auf, beziehungsweise von der Bearbeitungsdrehzahl
- Betriebslast durch Zerspanungsprozesskräfte.
Durch Messungen oder vorhandene Kennlinien können (1) bis (3) ermittelt werden, wobei (1) und (2) zur Ermittlung des Energiebedarfs mit der jeweiligen Bearbeitungsdauer der einzelnen Prozessschritte zu multiplizieren sind. Die Betriebslast kann mithilfe geeigneter Zerspankraftmodelle ausreichend genau abgeschätzt werden. Die Verlustleistung kann abschließend durch eine geeignete Wahl des Wirkungsgradfaktors (je nach System bei etwa 0,8) des Hauptspindelantriebs ermittelt werden.
Zur Bemessung der Verlustleistung des Hydrauliksystems wird der Gesamtenergiebedarf der Hydraulikpumpe angesetzt, die in den Betriebszuständen
- druckloser Umlauf und
- Nachladen
betrieben wird. Die Leistungsaufnahme kann anhand vorhandener Kennlinien der Motor-Pumpeneinheit im Nachladebetrieb und im drucklosen Umlauf unter Zuhilfenahme der Kennlinie des Ventils abgeschätzt werden. Mit Informationen über die Leckage und Steuerölvolumenstrom der hydraulischen Komponenten sowie der Gesamtzykluszeit wird der Gesamtenergiebedarf der Hydraulikeinheit bestimmt.
Der Verlauf der erforderlichen Kälteleistung des Rückkühlaggregats kann anschließend aus den jeweiligen Berechnungen ermittelt werden. Die parallel an dem Demonstrator durchgeführten Messergebnisse haben gezeigt, dass die getroffenen Annahmen geeignet sind, den tatsächlichen Verbrauch aller Komponenten zu ermitteln.
Kontakt
Martin Beck
Wissenschaftlicher Mitarbeiter
Institut für Produktionsmanagement, Technologie und Werkzeugmaschinen (PTW)
Technische Universität Darmstadt
Tel. +49 615116-6619
E-Mail senden
Prof. Dr.-Ing. Eberhard Abele
Leiter
Institut für Produktionsmanagement, Technologie und Werkzeugmaschinen (PTW)
Technische Universität Darmstadt
Tilo Sielaff
Wissenschaftlicher Mitarbeiter
Institut für Produktionsmanagement, Technologie und Werkzeugmaschinen (PTW)
Technische Universität Darmstadt