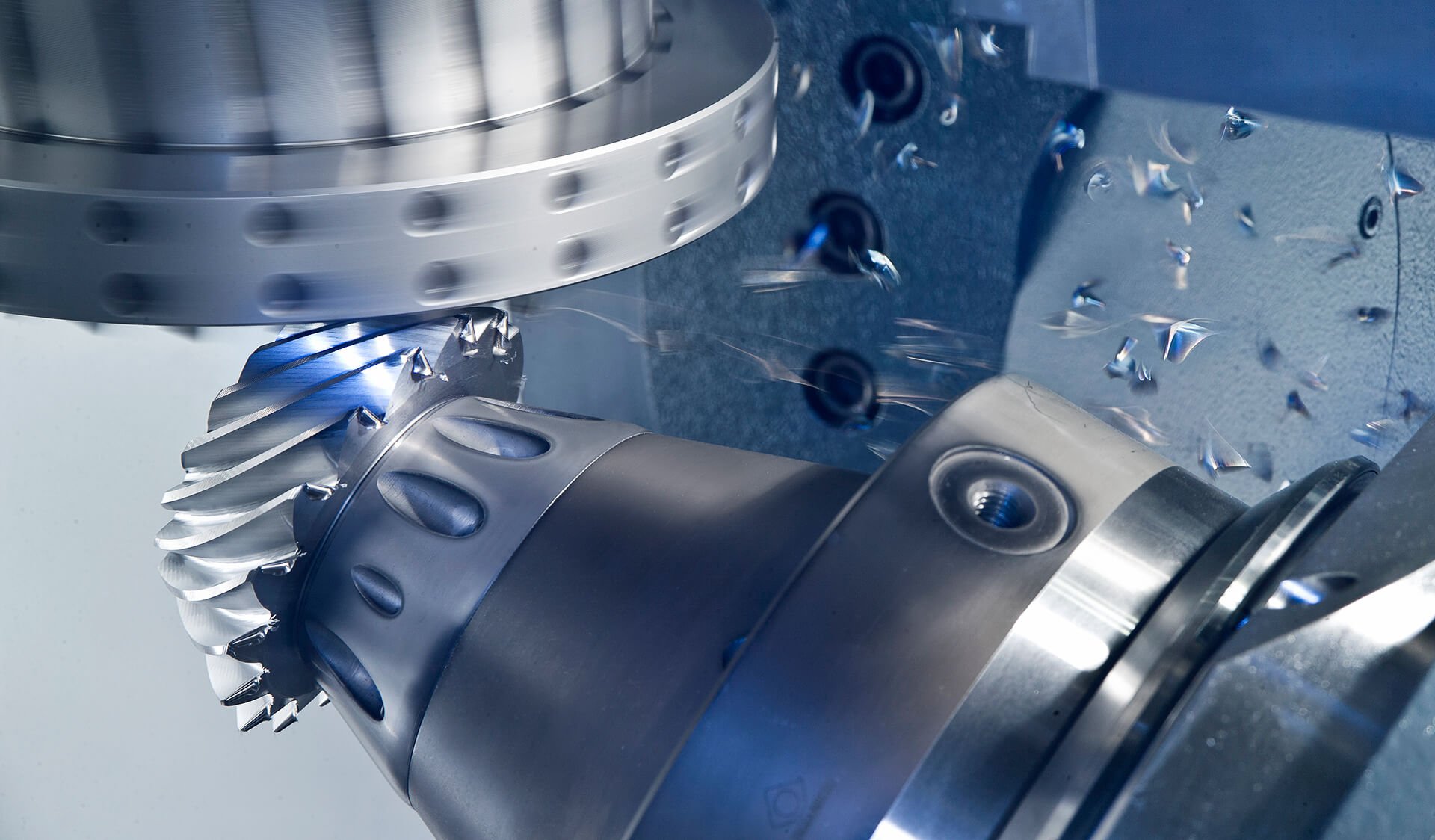
Produktion
Das digitale Abbild des Zahnrads
ist Geburtsurkunde mit Stammbaum
Obwohl der Schweizer Leonhard Euler schon 1760 mit der Evolvente für ein Zahnprofil die Grundlagen für leistungsfähige Getriebe schuf, brauchte es noch ein Vierteljahrtausend bis sich das, was der geniale und erblindete Mathematiker in seiner Gedankenwelt sah, als durchgängige, digitale Lösung in der Welt der Zahnräder durchsetzen konnte. Trotzdem ist selbst für Kenner des Maschinenbaus eine Verzahnmaschine immer noch eine Besonderheit, und mancher fragt sich, warum dies trotz Industrie 4.0 immer noch so ist. Den Kerngedanken von Industrie 4.0 hat Klingelnberg auf die Zahnradfertigung angewandt und ein cyber-physisches System geschaffen, das entlang der gesamten Wertschöpfungskette digitale Abbilder des Zahnrades beisteuert. Dadurch wird die Einführung objektiver Quality Gates erst ermöglicht.
Bei der spanenden Fertigung von Werkstücken ist ein CAD-CAM-Prozess Stand der Technik. Das Werkstück wird als 3D-Modell beschrieben, in dem nachfolgenden CAM-Prozess werden Werkzeuge ausgewählt und NC-Dateien erzeugt, die auf der Bearbeitungsmaschine das digital beschriebene Werkstück real herstellen. Dieses Prinzip ist bei Verzahnmaschinen nicht anwendbar, weil das Zahnrad nicht als 3D-Modell beschrieben wird.
Von der Mathematik
zur digitalen Zahnradfertigung
Basierend auf der Theorie von Evolventen und anderen Kurven wird ein Zahnrad immer durch die Geometrie der Werkzeugschneide und durch eine Relativbewegung zwischen diesem Werkzeug und dem herzustellenden Zahnrad beschrieben. Auch wenn es mittlerweile 5-achsige Bearbeitungsprinzipien gibt, mit denen Zahnräder hergestellt werden können, ist diese spezielle Zahnradbeschreibung stets die Grundlage und damit die Ursache für die Besonderheit der Spezies Verzahnmaschine. Die Industrie-4.0-Lösung, die auf 3D-Modellen und dem CAD-CAM Prozess beruht, lässt sich hier nicht so einfach anwenden.
Klingelnberg hat ein cyber-physisches System geschaffen, das entlang der Wertschöpfungskette digitale Abbilder des Zahnrades beisteuert. Die Wertschöpfungskette eines Kegelradsatzes beginnt mit dem Engineering der Verzahnung, zu dem auch die Werkstoffspezifikation gehört. Zu Beginn wird die Verzahnung optimiert, um die geforderte Spezifikation in einem gegebenen Umfeld durch Lager, Getriebegehäuse und Betriebsbedingungen zu erfüllen.

Leonhard Euler schuf die Grundlagen für leistungsfähige Getriebe. Foto: Klingelnberg
Im Ergebnis entsteht ein digitaler Zwilling des Zahnrades, der nicht nur alle seine geometrischen Informationen enthält: Wegen der Besonderheit der Beschreibung eines Zahnrades liegen auch alle Informationen zum Werkzeug sowie die Beschreibung der Herstellbewegung einer virtuellen Verzahnmaschine sowohl für die Weich- als auch für die Hartbearbeitung vor. Diese Daten kommen automatisch aus dem Klingelnberg-Programmsystem KIMoS. Sie bilden das digitale Rückgrat aller Fertigungsschritte. So wurde eine horizontale Integration aller am Prozess beteiligten Maschinen und Programmsysteme realisiert, bei der die zentrale Datenbank die digitalen Abbilder und geometriebestimmenden technologischen Parameter für jeden Schritt der Herstellung enthält.
Was ist nun der Nutzen dieses cyber-physischen Systems? Weil es zu jedem Fertigungsschritt ein digitales Abbild gibt, können Quality-Gates im Prozess eingeführt werden, in denen die für den aktuellen Fertigungsschritt gegebene Geometrie geprüft wird. So lassen sich alle Fertigungsabweichungen an der richtigen Stelle in der Prozesskette erfassen und korrigieren. Die dadurch erreichte Transparenz des Fertigungsprozesses spart einerseits Kosten und ist andererseits Voraussetzung für jede Art von Rückverfolgung (Traceability). Der digitale Zwilling ist eben nicht nur ein Abbild des fertigen Bauteils, er ist auch quasi Geburtsurkunde mit Stammbaum.
Ein weiterer entscheidender Vorteil ist die Korrektur von Fertigungs- oder Montageabweichungen. Das Verzahnungsfräsen bei Kegelrädern wird mit Messerköpfen durchgeführt, die mit Hartmetall-Stabmessern als Schneiden ausgestattet sind. Diese speziell geschliffenen und beschichteten Schneiden müssen sehr präzise im Messerkopf montiert werden. Hier taten sich in der Vergangenheit zwei Fehlerquellen auf: die Form der Stabmesser-Schneide und die Genauigkeit der Stabmesser-Montage. Früher wurden die Auswirkungen eines ungenauen Messerkopfes auf die Zahnform vom Maschinenbediener minimiert, indem er Know-how-basierend die Einstellwerte der Verzahnmaschine veränderte.
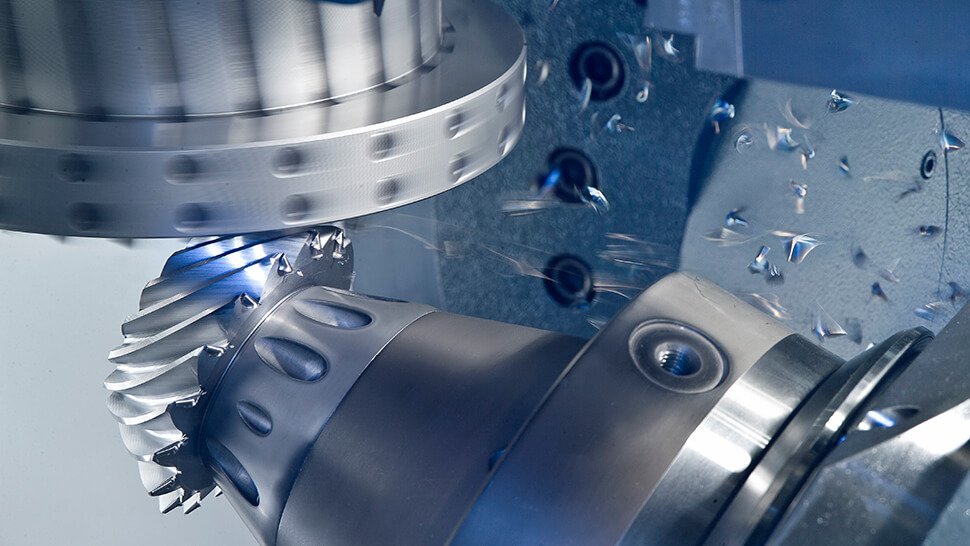
Foto: Klingelnberg
Das cyber-physische System ist die digitale Basis für perfekt geschliffene Messer und hochpräzise eingestellte Messerköpfe. Die Geometrie der Stabmesser liegt als fertiges Messprogramm für eine Klingelnberg-Messmaschine in der Bauteildatenbank vor. Die gemessene Fertigungsabweichung wird von einem Korrekturprogramm verarbeitet und als Modifikation der Einstellwerte der Stabmesser-Schleifmaschine in der Bauteildatenbank abgelegt. Mit einem Nachschliff der Stabmesser erhält man eine perfekte Schneidengeometrie.
Für die Montage der Stabmesser im Messerkopf hat sich das CS200-Einstellgerät bewährt. Mit den Informationen aus dem digitalen Abbild des Messerkopfes werden die Stabmesser mikrometergenau automatisch positioniert. Nach dem Anziehen der Klemmschrauben wird die radiale und Position der Schneide vermessen, protokolliert und in der Datenbank abgelegt.
Die automatische Verbindung der Fertigungsmaschinen mit der Messtechnik, die so genannte Closed-Loop-Fertigung, bringt neben erheblichen Kosteneinsparungen auch einen Quantensprung in der Qualität mit sich. Closed-Loop-Module sind in der Abbildung der Wertschöpfungskette als kleine Kreise dargestellt. Solche Module in der Prozesskette gibt es für das Stabmesser-Schleifen, für das Verzahnungsfräsen und für das Verzahnungsschleifen. Selbst Härteverzüge können mit dem Closed-Loop-Ansatz zur Minimierung des Schleifaufmaßes weitgehend kompensiert werden. Mit zum Funktionsumfang des cyber-physischen Systems gehören auch Bearbeitungsschritte wie das Thema Entgraten. Der Entgratvorgang auf der Fräsmaschine wird genauso behandelt, wie das Verzahnungsfräsen: Das Werkzeug und die Maschinenbewegung werden durch das System vorgegeben und in der Datenbank abgelegt.
Was zunächst den Eindruck eines komplexen Gebildes erwecken mag, hat sich in der Praxis seit Jahren als leicht zu bedienendes System erwiesen. Neben der maximalen Transparenz in der Fertigung hat man die Garantie, die Verzahnung exakt produziert zu haben, wie sie ausgelegt wurde. Und das ist die Basis für ein immer besser werdendes Engineering.
Kontakt
Dr. Hartmuth Müller
Leiter Technologie und Innovation
Klingelnberg GmbH
Hückeswagen
Tel. +49 2192 81 568
E-Mail senden