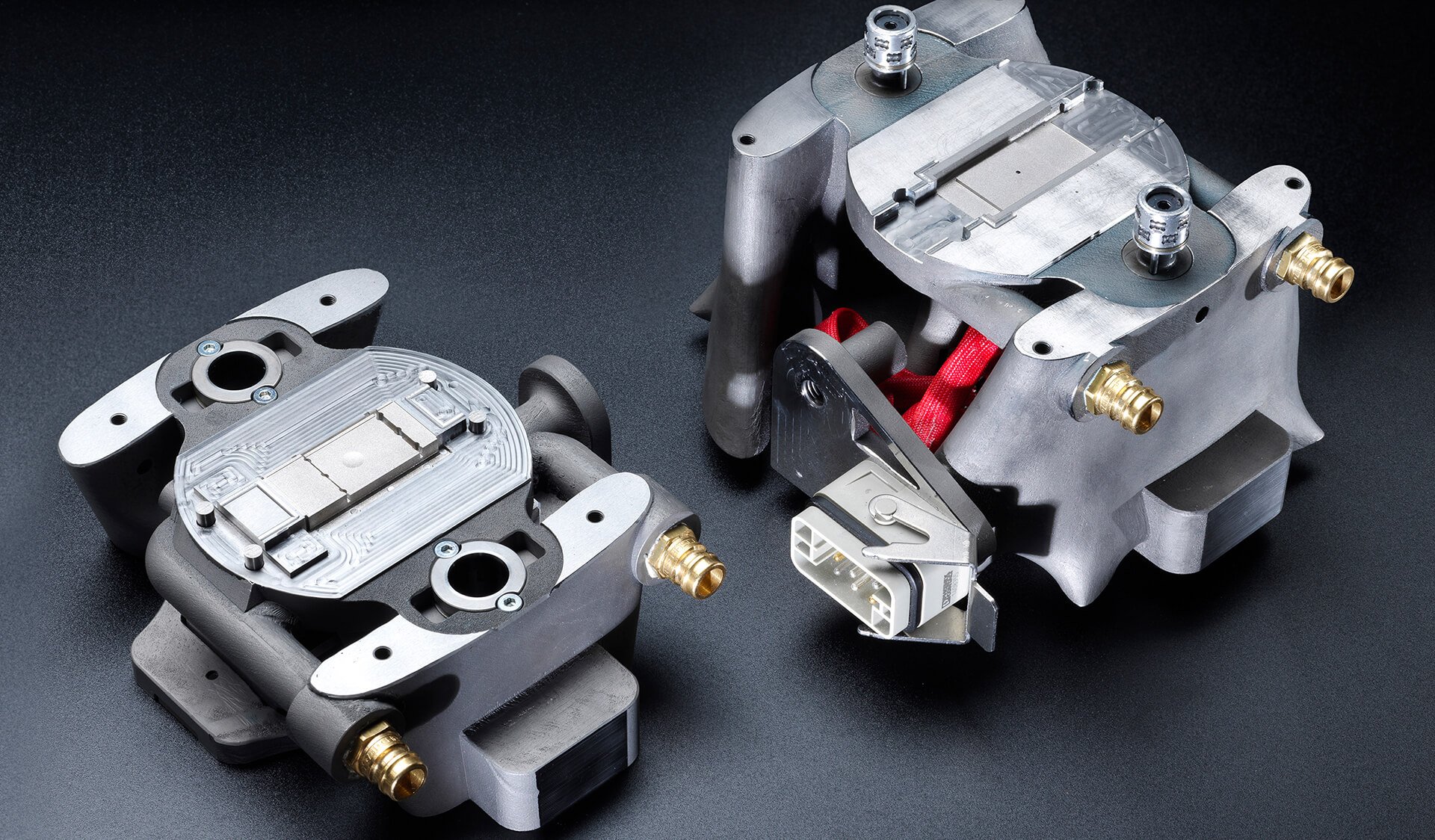
Titelthema
Erhöhung der Effizienz in puncto Gewicht und Zeit
Durch industriellen 3D-Druck können Produkte schichtweise schnell, materialsparend und individuell hergestellt werden. Bewegliche Bauteile lassen sich komplett direkt „drucken“, sodass der Prozessschritt des Zusammenfügens ganz entfallen kann. Funktionsintegration erlaubt also die Kombination mehrerer Elemente einer Baugruppe zu einem einzigen Bauteil.
Beim Spritzgießprozess führen mediendurchströmte Kühlbohrungen die Wärme der Kunststoffschmelze während des Kühlprozesses ab. Der Einsatz der additiven Fertigung ermöglicht eine Neugestaltung der Kühlkanäle. Eine oberflächennahe, frei geformte Kühlmedienführung optimiert den Abtransport der Wärme, erhöht die Abkühlraten und reduziert Zykluszeiten. Durch die additive Fertigung der Werkzeugeinsätze lässt sich die Zykluszeit der Produktion im Spritzgießprozess aufgrund einer verbesserten Werkzeug-Performance deutlich verringern.
Darüber hinaus lässt sich das Gewicht der Werkzeuge deutlich senken, um Rüstvorgänge wirtschaftlicher zu gestalten und die Werkzeuge schneller zu bewegen. Weil konventionelle Werkzeuge mitunter mehr als 30 Kilogramm wiegen, werden für ihre Auswechslung Hebezeuge benötigt. Da sich das Gewicht durch Direct Tooling typischerweise um nahezu 70 Prozent reduziert, können die Mitarbeiter die Werkzeuge manuell und mit geringerem Zeitbedarf austauschen. Protiq verbessert die Werkzeuge mittels Topologieoptimierung und Leichtbau-Design.
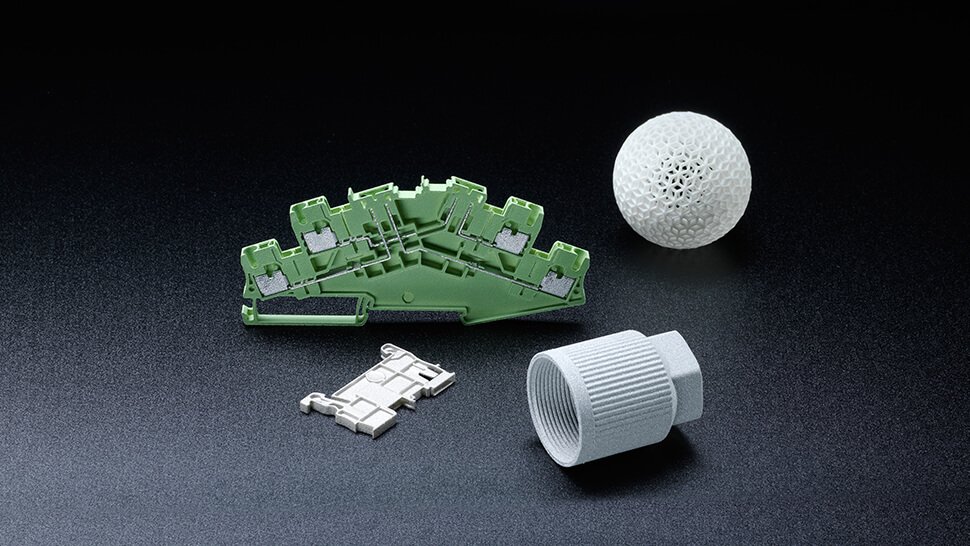
Fertigung von Funktionsprototypen sowie Muster- und Serienteilen aus technischen Kunststoffen. Fotos: Phoenix Contact
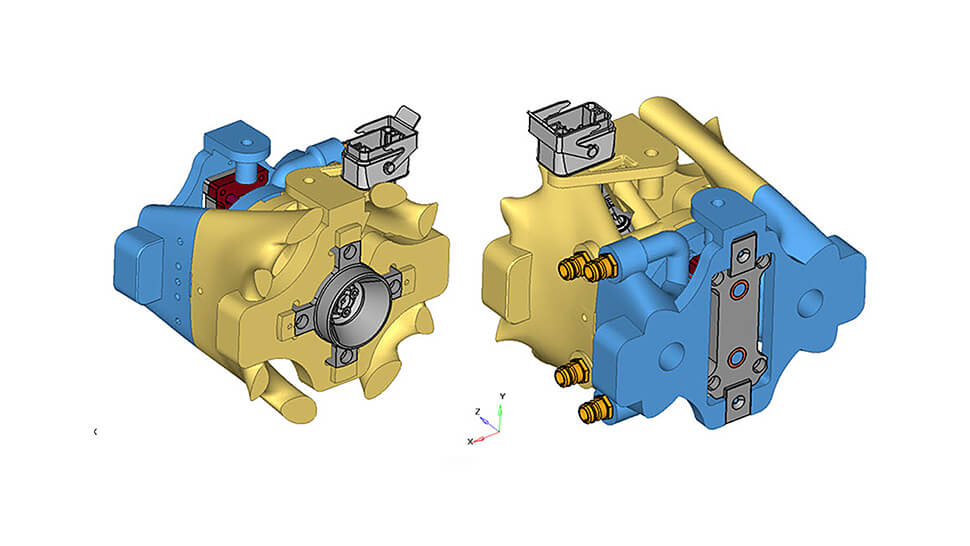
Darstellung eines topologieoptimierten Spritzgießwerkzeugs.
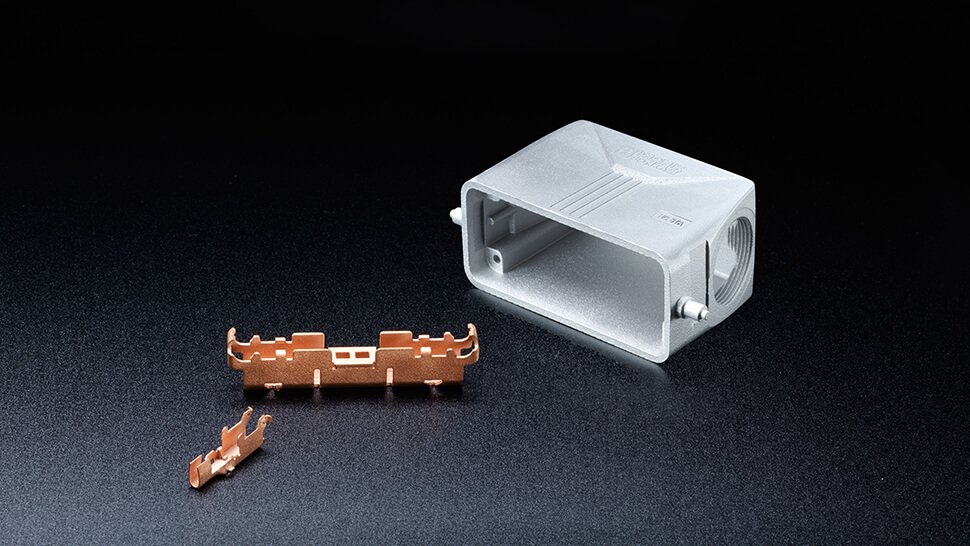
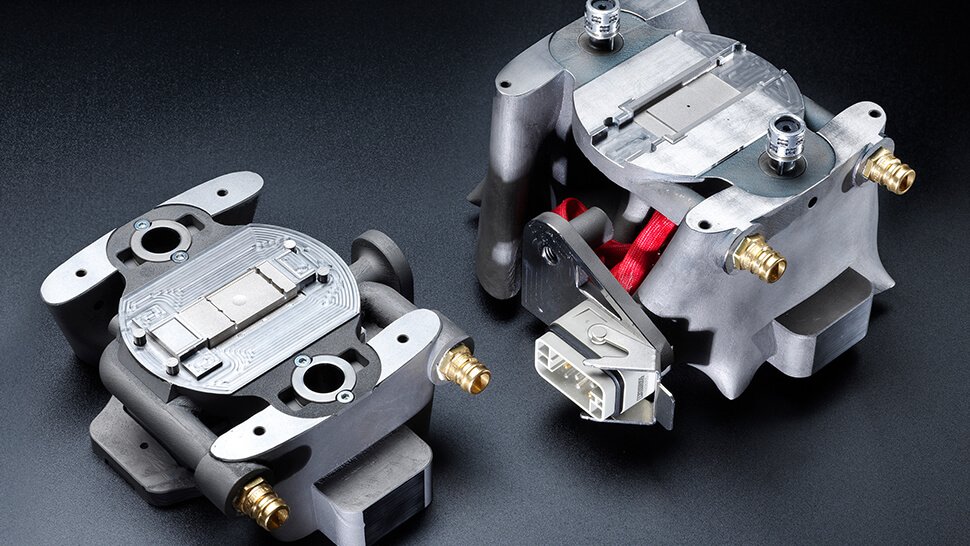
Erstellung von metallischen Bauteilen durch selektives Laserschmelzen.
Errechnung auf Basis einer Simulation
Die neue Gestaltungsfreiheit beim 3D-Drucken gestattet ein belastungsgerechtes Werkzeug-Design auf Basis einer rechnergestützten Topologieoptimierung. Durch die Finite-Elemente-Simulation lassen sich Bauteilbereiche identifizieren, die einer geringen Belastung unterliegen. Dort kann Material eingespart werden, während die Werkzeugbereiche, die einer hohen mechanischen Belastung ausgesetzt sind, eine massive Ausführung benötigen. Die aus der Topologieoptimierung resultierenden Geometrien erinnern an bionische Strukturen wie den menschlichen Knochen.
Die Werkzeuggestaltung mit einer konturnahen Kühlung und Topologieoptimierung gliedert sich in drei Teilschritte. Zur Ermittlung der Eingangsgrößen zählen die auftretenden Prozesskräfte, Schnittstellen und Anbindungspunkte zur Spritzgießmaschine sowie die maximale Werkzeuggröße. Bei der Simulation der Prozesskräfte kann Protiq auf die Expertise im Werkzeugbau von Phoenix Contact zurückgreifen.
Reverse Engineering: Mitunter benötigen Anwender ein Produkt, für das die notwendigen 3D-Daten nicht vorliegen. In diesem Fall werden die Daten mit Hilfe der Computertomographie erstellt. Die Konstrukteure prüfen das Objekt auf Umsetzbarkeit, besprechen die erforderlichen Parameter mit dem Anwender und scannen das Objekt, um es fertigen zu können.
Die sich aus dem Spritzgießen ergebenden Kräfte können einer Strömungssimulation entnommen werden. Schnittstellen, Anbindungspunkte und die maximale Werkzeuggröße leiten sich aus den Bauteilanforderungen ab. Im nächsten Schritt folgt die Integration der bauteilkonturnahen Kühlkanäle. Danach lässt sich das Leichtbau-Design aus der Topologieoptimierung durch Simulation errechnen.
Im Anschluss an das automatisiert entwickelte Leichtbau-Design geben die Konstrukteure dem Bauteil den letzten Schliff im Hinblick auf additive Fertigung. Dabei werden eine minimale Wanddicke, Stützgeometrien sowie die Produktion durch Laserstrahlschmelzen berücksichtigt.
Entwicklung eigener Anlagen und Materialien
Neben dem Direct Tooling kommt zunehmend auch das Direct Manufacturing zum Einsatz, also die direkte werkzeuglose Herstellung von Serienbauteilen. Typische Anwendungsbereiche sind die Medizintechnik sowie die Luft- und Raumfahrt. Dies liegt unter anderem daran, dass die standardmäßig im 3D-Druck verwendeten Materialien die Anforderungen der Elektronik- oder Automobilindustrie nicht erfüllen. Protiq hat eine optimierte Laser-Sinter-Anlagentechnik entwickelt, um auch Serienprodukte aus Kunststoff direkt und werkzeuglos herstellen zu können. Mit einem ebenfalls selbst konzipierten hochleitfähigen Kupfermaterial lassen sich von massiven Bauteilen bis zu Kupferkontakten mit hoher elektrischer Leitfähigkeit viele Einsatzbereiche abdecken.
Kontakt
Dr. Ralf Gärtner
Geschäftsführer Protiq GmbH Blomberg Tel. +49 5235 3-42305 E-Mail senden
Johannes Lohn
Technologiemanager Additive Fertigung Protiq GmbH Blomberg
Dr. Ralf Schlottmann
Manager Rapid Tooling Phoenix Contact GmbH & Co. KG Blomberg
Anzeige
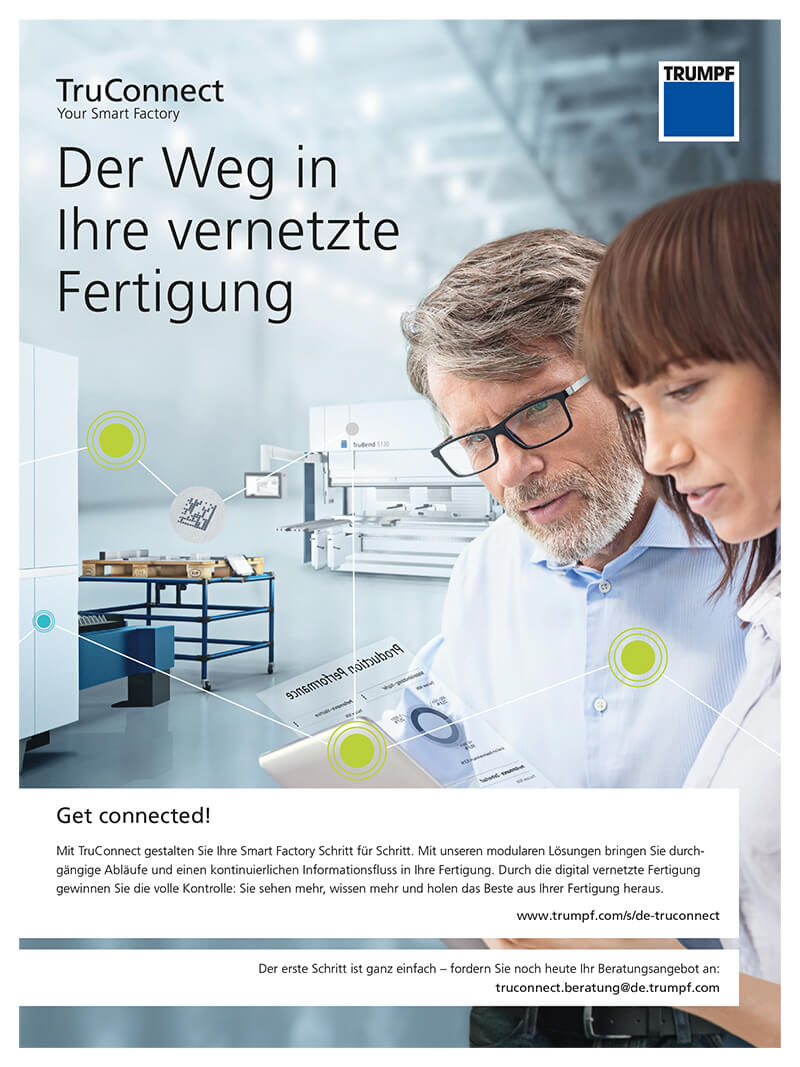