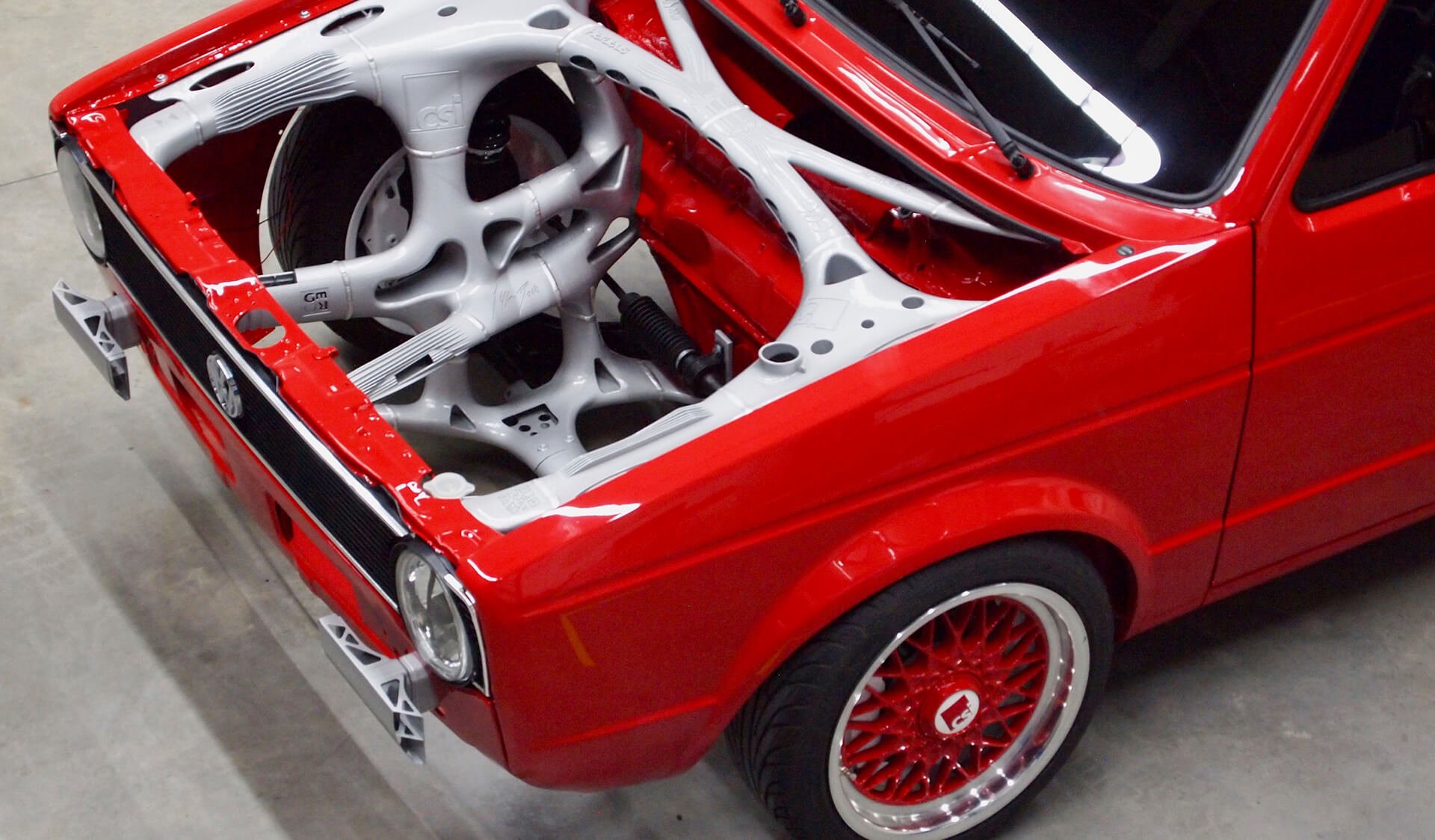
Titelthema
VW Caddy erhält neuen Vorderwagen
Der industrielle 3D-Druck, auch als additive Fertigung oder Additive Manufacturing (AM) bezeichnet, wird in naher Zukunft ein fester Bestandteil der Serienfertigung sein. Die Unternehmen Altair, Apworks, CSI Entwicklungstechnik, EOS, Gerg und Heraeus zeigen am Beispiel der Vorderwagenstruktur eines alten VW Caddy das Potenzial des industriellen 3D-Drucks für die Automobilindustrie.
Die Struktur ist besonders leicht und gleichzeitig stabil und verfügt über ein hohes Maß an Funktionsintegration. In dem gemeinsamen Entwicklungsprojekt mit dem Namen 3i-PRINT haben die Unternehmen alle Schritte der Prozesskette abgedeckt: von Design, Auslegung, Berechnung und Konstruktion bis hin zu Bau und Nachbearbeitung der Baugruppe. Die Umsetzung von der Idee bis zum fertig umgebauten Fahrzeug erfolgte innerhalb von neun Monaten.
Mehrwert additiver Fertigung für Automobilbranche im Fokus
Schon heutzutage findet die Technologie Einsatz in zahlreichen Industrien. Die beständige Weiterentwicklung der Produktions- und Konstruktionstechniken mit der additiven Fertigung wird die Technologie kostengünstiger und schneller machen.
Damit wirtschaftliche Lösungen gefunden und ein echter Mehrwert erzeugt werden können, müssen die Betrachtungen hinsichtlich additiver Fertigung für den Automobilbau weit über die Bereiche Strukturmechanik und Leichtbau hinausgehen. So sind die Möglichkeit zur Funktionsintegration – die Realisierung möglichst vieler technischer Funktionen mit möglichst wenigen Bauteilen – und der damit verbundene Mehrwert ein wesentlicher Vorteil, der den Einsatz von 3D-Druck für die Automobilindustrie auch aus wirtschaftlicher Sicht attraktiv macht. Das Projekt 3i-PRINT möchte mit dem Caddy-Konzept aufzeigen, was technologisch in Zukunft möglich ist.
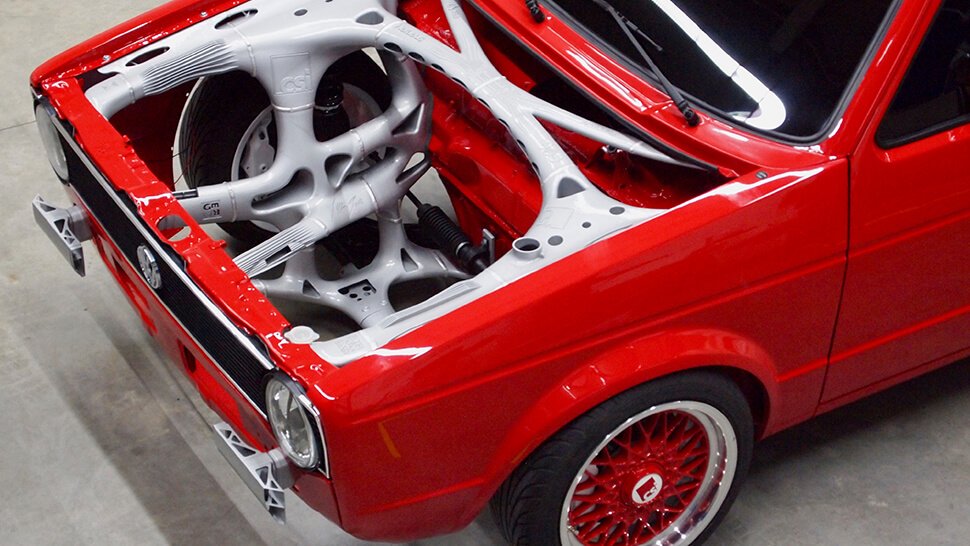
Das Partnerprojekt 3i-PRINT zeigt am Beispiel der Vorderwagenstruktur eines alten VW Caddy, was mit industriellem 3D-Druck möglich ist. Fotos: CSI Entwicklungstechnik
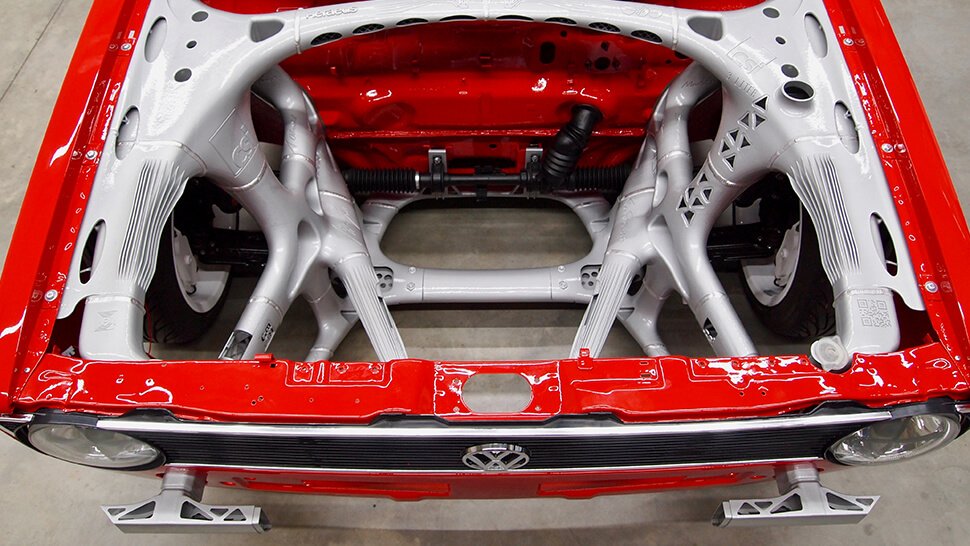
Die Struktur des überarbeiteten Autos ist besonders leicht und gleichzeitig stabil. Sie verfügt über ein hohes Maß an Funktionsintegration.
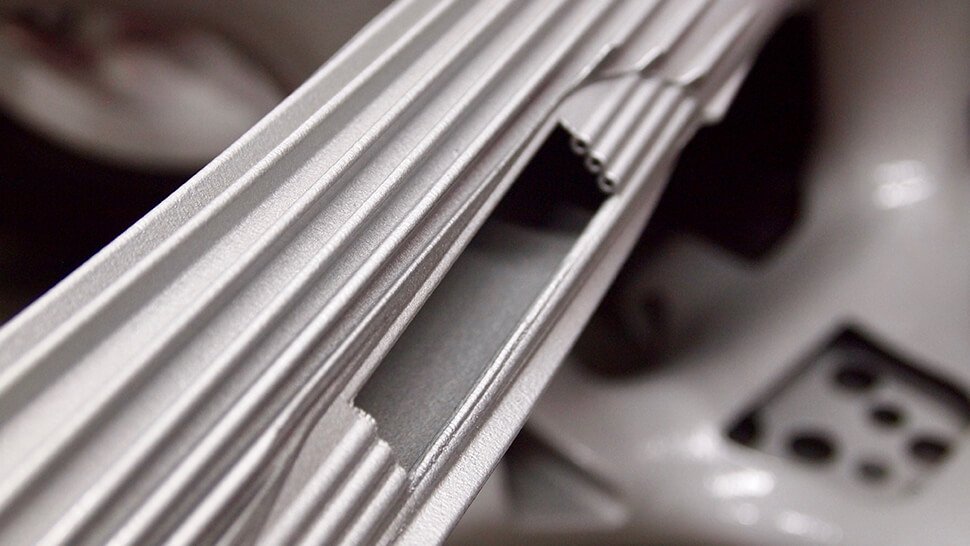
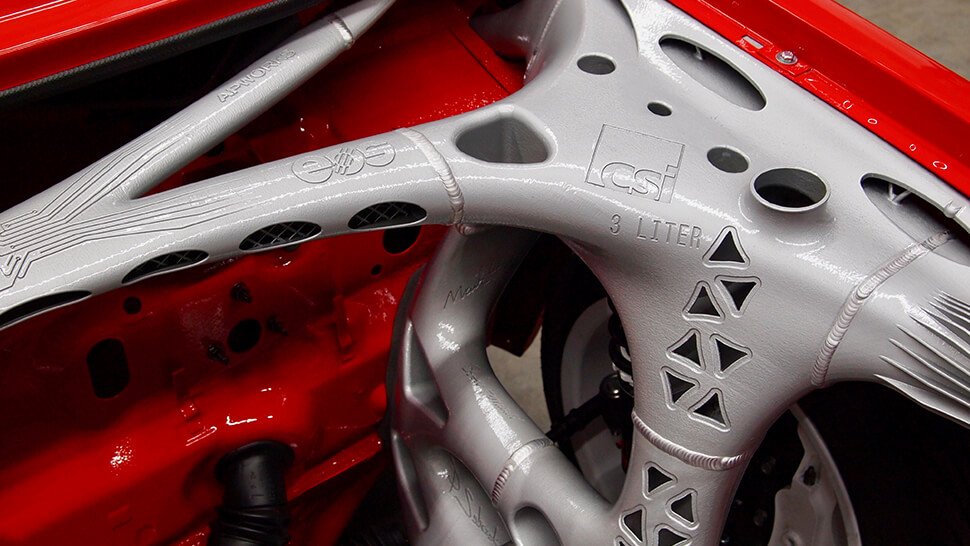
Organisches Design für lasttragende Strukturen
Vor dem Hintergrund der Elektrifizierung im Automobilbereich waren das Wärmemanagement sowie die Bauraum- und Gewichtsreduzierung entscheidende Punkte für die Konstruktion eines innovativen Vorderbaus. Zudem galt es, die strukturellen Anforderungen bezüglich Fahrzeugsicherheit, Leistung und Komfort zu erfüllen.
Entsprechend verfügt der additiv gefertigte Vorderwagen über lasttragende Strukturen mit Details zur aktiven und passiven Kühlung – beispielsweise in Form eines geleiteten Luftstroms für die Kühlung von Batterien und Bremsen. Darüber hinaus wurden Funktionen aus dem Wärmemanagement, der passiven Sicherheit, der Flüssigkeitsspeicherung und andere Funktionen in das organische, lastgetriebene Design des Frontmoduls integriert. So ist der Wischwasserbehälter im Zuge der Topologie-Optimierung direkt in die Vorderwagenstruktur integriert.
Mit diesen Zielen vor Augen begannen die Experten der Firmen CSI Entwicklungstechnik mit Design, Berechnung und Konstruktion der Vorderwagenstruktur. Das Unternehmen entwickelt für Hersteller und Zulieferer der Automobilbranche hochwertige Module im Karosserie-, Interieur- und Exterieur-Bereich. Gerg ist Anbieter innovativer Lösungen im Bereich Prototypen und Kleinserien für die Automobil- und Luftfahrtindustrie und übernahm im Zug des Projektes den Rahmenbau aus den additiv gefertigten Einzelbauteilen. Bei Auslegung, Berechnung, Simulation und Konstruktion kamen die Software-Lösungen von Altair zum Einsatz, das als Unternehmen die breite Anwendung von Simulationstechnologie entwickelt und unterstützt.
Nach erfolgreicher Simulation und Konstruktion des Konzepts erfolgte die finale Auslegung der Bauteile auf den 3D-Druck durch die Apworks, die ihr Knowhow zur Druckvorbereitung beisteuerte und die additive Fertigung der Strukturelemente umsetzte. Als hundertprozentige Tochter von Airbus ist das Unternehmen mit modernen Fertigungsprozessen vertraut. Für den Bau des Vorderwagens setzte Apworks auf ein System von EOS. Für die Produktion der Bauteile lieferte und qualifizierte der Metallpulverspezialist Heraeus die von Apworks entwickelte technisch hochfeste Aluminium-Legierung Scalmalloy.
Forum für innovative Prototypenkonzepte
Das 3i-PRINT-Projekt fungiert als agile Engineering-Plattform für Forschung und Entwicklung, auf der innovative Prototypenkonzepte präsentiert werden können. Das Konzept baut auf dem Einsatz neuer Entwicklungswerkzeuge und -methoden auf, darunter industrieller 3D-Druck. Stefan Herrmann aus dem Bereich Leichtbau im Team Rohkarosserie, CSI Entwicklungstechnik, erklärt: „Die Struktur und der Kontrast zwischen alt und neu zeigen eindrucksvoll, welches Potenzial der industrielle 3D-Druck und ein hoher Grad an Funktionsintegration gerade auch für die Automobilindustrie bieten.“ Nicht nur das Ergebnis, auch den agilen und zeiteffizienten Weg von der Idee bis zum fertig umgebauten Fahrzeug innerhalb von nur neun Monaten, hob er als erstaunlich hervor.
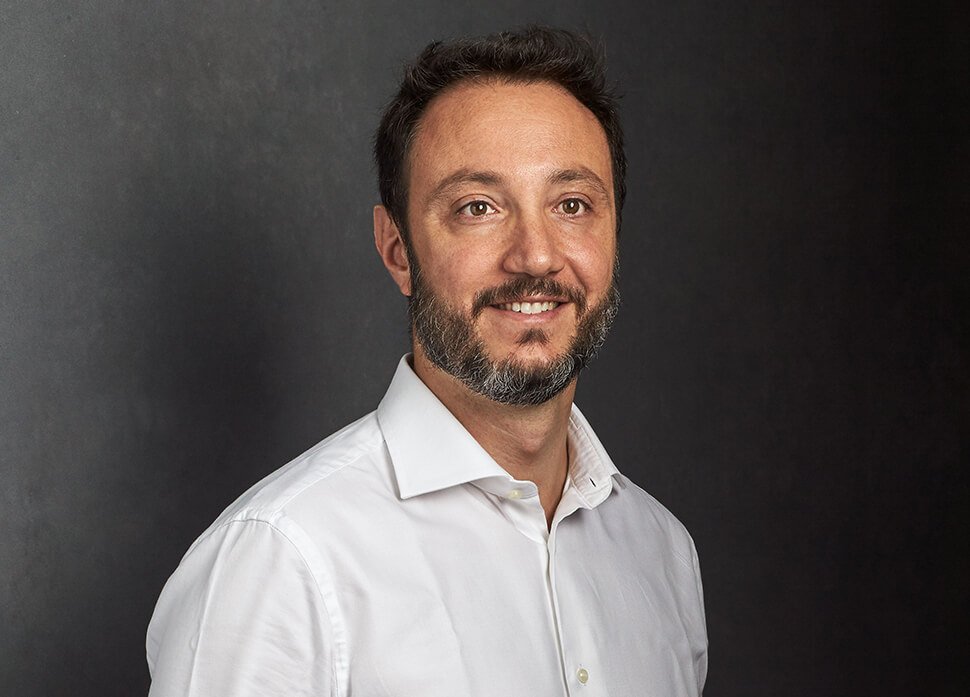
„Additives Design muss noch ankommen“
Die Altair Engineering GmbH entwickelt Software, die Konstrukteure mithilfe von numerischen Methoden und künstlicher Intelligenz zum optimalen Design für additiv gefertigte Bauteile führt. Im Interview erklärt Geschäftsführer Dr. Pietro Cervellera, wo aus seiner Sicht die Vorteile und schwachen Stellen in der additiven Fertigung liegen.
Welchen Teil der Wertschöpfungskette decken Sie in der additiven Fertigung ab?
Cervellera: Im Additive Manufacturing ist die Konstruktion der zentrale Part. Dank der Schichtbauweise lassen sich komplexe Geometrien realisieren – Gitterstrukturen, bionische Designs, Integration von Leitungen in Bauteile. Doch die Komplexität ist so hoch, dass Konstrukteure die optimale Performance kaum intuitiv entwickeln können. Hier setzen wir an. Unsere Software unterstützt sie dabei, die Designfreiheit zu nutzen. Additive Fertigung zahlt sich in den meisten Fällen nur dann aus, wenn diese Freiheiten genutzt werden. Der Mehrwert liegt in der Konstruktion. Doch wer sagt mir, wo ich eine stabilisierende Gitterstruktur, eine zusätzliche Strebe oder dickere Wand brauche und wo nicht? Im simulationsgestützten Designprozess finde ich diese Antworten.
Was sind aus Ihrer Sicht die wichtigsten Argumente für die additive Fertigung?
Cervellera: In additiven Verfahren lassen sich Bauteile mit minimiertem Gewicht und Materialeinsatz realisieren, die höhere Lasten aufnehmen, verbesserte Eigenfrequenzen und Steifigkeiten aufweisen. Oft sinkt der Montage- und Wartungsaufwand, da sich bisherige Baugruppen in einem Stück fertigen lassen. Indem Kanäle oder Halterungen ins Bauteil verlegt werden, wird die Reinigung einfacher, sinkt der Bauraum oder wird in temperatursensiblen Prozessen konturnahes Kühlen oder Heizen möglich. Zudem lässt sich eine Ersatzteilversorgung on-demand realisieren, und auch nach dem Produktionsstart können Komponenten jederzeit verbessert werden. Es besteht von den Kosten her außerdem kein Unterschied, ob man ein hoch komplexes bionisches Bauteil oder einen simplen Entwurf ausdruckt. Im Zweifel ist sogar der komplexe Entwurf günstiger, weil Material eingespart wird. Und das sind längst nicht alle Vorteile.
Welchen Beitrag kann Software leisten, um das volle Potenzial der additiven Fertigung zu heben?
Cervellera: Intuitive Konstruktion auf Basis etablierter Regelwerke stößt an Grenzen. Die Bauteile werden schlicht zu komplex. Unsere Verfahren suchen numerisch das optimale Design und spielen binnen Sekunden eine enorme Fülle an Möglichkeiten durch. Die Verfahren sind im Automobilbau und in der Luft- und Raumfahrt Stand der Technik. Und im Maschinenbau fassen sie aufgrund des steigenden Wettbewerbsdrucks mittlerweile immer besser Fuß. Das liegt auch daran, dass die Bedienung unserer Software keine besondere numerische Expertise erfordert. Software hat also die Aufgabe, Entwicklern die Komplexität abzunehmen – und sie dabei durch einen iterativen Optimierungsprozess zu führen. Dazu zählt auch die Optimierung der Stützstrukturen für den Fertigungsprozess.
Wo sehen Sie in Ihrem Bereich der Prozesskette Optimierungspotenzial?
Cervellera: Es bedarf vor allem eines grundsätzlichen Umdenkens. Additive Manufacturing ist nur vordergründig eine Fertigungsrevolution. Tatsächlich beginnt diese Revolution in der Entwicklungsmethodik. Additives Design muss in den Köpfen der Konstrukteure und auch in den traditionellen Firmenstrukturen ankommen. Die Technologien auf der Soft- und Hardwareseite sind da. Jetzt müssen wir als Menschen lernen, sie optimal zu nutzen.
Weitere Informationen unter am.vdma.org
Kontakt
Martin Grebner
EOS GmbH Electro Optical Systems München Tel. +49 89 893 36-2264 E-Mail senden