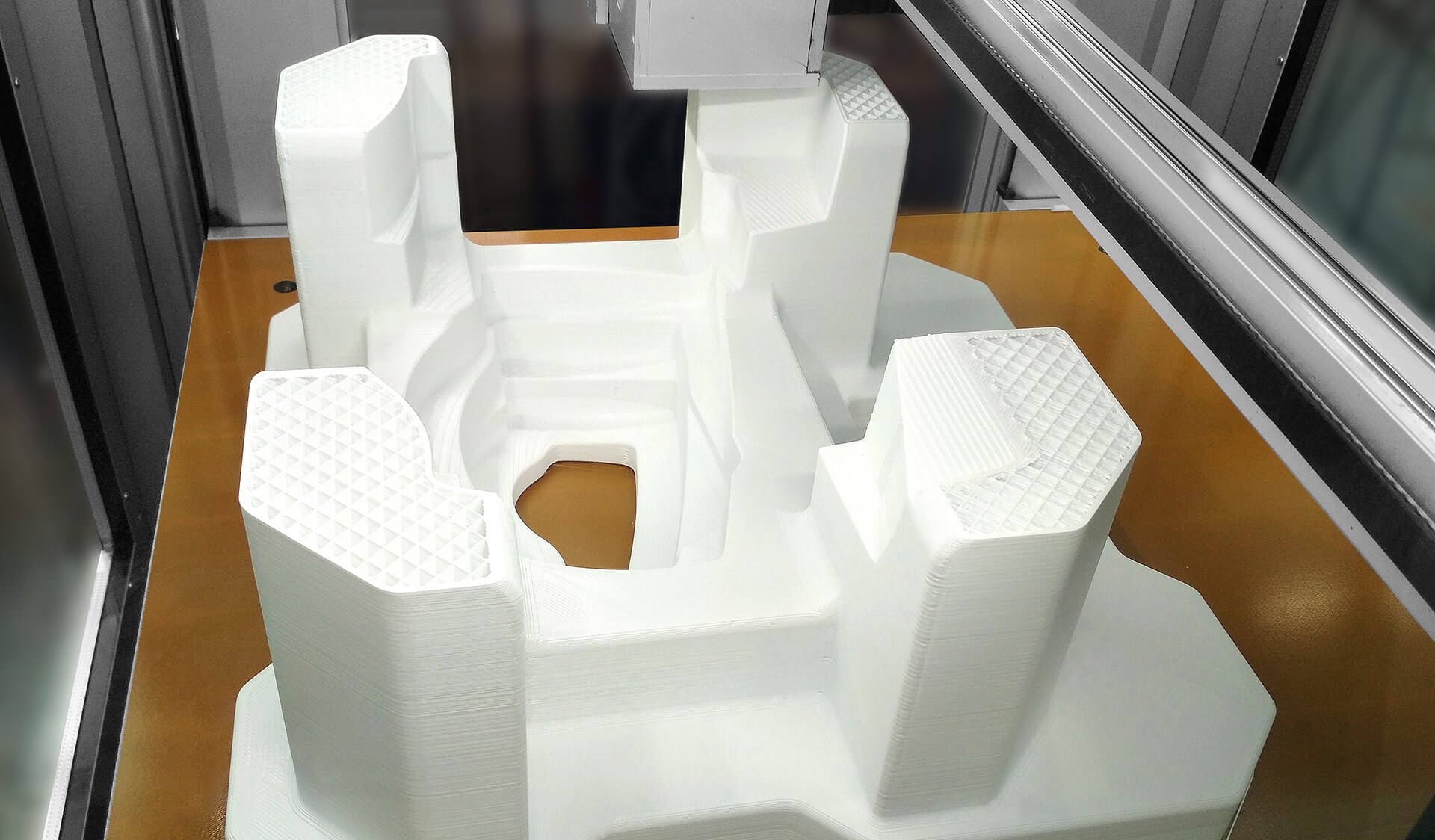
Titelthema
Selbst Einzelstücke lohnen sich
Immer dann wenn es um Bahnsteuerung mit Schrittmotoren geht, spielen die maschinenbaulichen Lösungen von Systec ihre Stärke aus. Mittlerweile hat der Mechatronikanbieter aufbauend auf den eigenen Steuerungs- und Automationsprodukten eigene, industrietaugliche 3D-Drucker-Lösungen für das FFF/FDM-Verfahren entwickelt. Bereits seit fast 40 Jahren ist die Systec GmbH bekannt für ihre Schrittmotorsteuerungen. Vor 20 Jahren startete das Unternehmen aus Münster mit der Herstellung einbaufertiger Positioniersysteme und kompletter Automationslösungen auf Basis des eigenen Produktportfolios.
Während einer Produktentwicklung kommt es immer wieder vor, dass Musterteile gefertigt, getestet, verändert und wieder neu hergestellt werden müssen. So erging es vor einigen Jahren Jochen Keuschnig, Produktentwickler bei Systec in Münster. Für ein Kunststoffgehäuse benötigte er recht große, individuell gestaltete Teile mit einer Kantenlänge von etwa 40 Zentimetern.
Die Fertigung im Spritzgussverfahren wäre in der Entwicklungsphase zu teuer gewesen. Die additive Fertigung im kostengünstigen FDM-Verfahren erschien als die effizientere Lösung. Doch Keuschnig fand zu seinem Erstaunen keinen Zulieferer. Während es FDM-3D-Drucker für kleine Teile mittlerweile beim Elektronik-Discounter gibt, ist das Angebot an skalierbaren, industrietauglichen Großraumdruckern überschaubar.
Die Systec GmbH bewegt Automation. Mit den einbaufertigen Lineareinheiten und Drehmodulen inklusive Steuerung, der Positioniersteuerungsserie, den Fertigungszellen und den innovativen Sonderanwendungen verfolgt das Unternehmen konsequent die Entwicklung von mechatronischen Systemen der Spitzenklasse. Alle Teilbereiche von Mechatronik, Maschinenbau, Elektrotechnik und Informatik werden durch Spezialisten im Haus selbst erledigt. Das Traditionsunternehmen hat seinen Sitz in Münster-Roxel. Seit 2018 gehört Systec zum niederländischen Technologieentwickler Demcon.
Systec erkannte eine Marktnische und startete an diesem Punkt die Eigenentwicklung großer Industrie-3D-Drucker. Gerade im industriellen Umfeld herrscht oft Bedarf an großen, im FDM- beziehungsweise dem ähnlichen FFF-Verfahren gedruckten Teilen – ob für Sonderlösungen, als Produktmuster, für Entwicklungsteile oder für Kleinserien. FFF/FDM-3D-Druck mit kostengünstigen und vielseitigen Filamenten wie Polyactid (PLA) oder Acrylnitril-Butadien-Styrol-Copolymere (ABS) ist eine lohnende Alternative, wenn es nicht auf große Stückzahlen und hohe Produktionsgeschwindigkeiten ankommt.
Vorhandenes Know-how genutzt
Für die Entwicklung der 3D-Drucker nutzte Systec vorhandenes Know-how. Erfahrung in der Ansteuerung von Dosiersystemen hatte man bereits bei zahlreichen Klebeanwendungen gesammelt. Beim FFF/FDM-Verfahren wird Kunststofffilament im Hotend aufgeschmolzen und durch die Druckdüse ähnlich wie Heißkleber schichtweise aufgetragen. Nach und nach entsteht ein dreidimensionales Objekt. Mit den einbaufertigen Positioniersystemen Drivesets, der Xemo-Positioniersteuerung, einem kompletten Fertigungszellenkonzept, einer NC-Softwarelösung zur Maschinenbedienung und maschinenbaulicher Erfahrung war Systec gerüstet, um die 3D-Druck-Applikation in ein industrietaugliches Anlagenkonzept zu integrieren.
„Insbesondere beim FFF/FDM-3D-Druck im industriellen Maßstab kommt es auf präzise gesteuerte Bewegung und eine hochexakte, gleichmäßige Temperaturregelung an“, weiß 3D-Druck-Berater Marcus Schwegmann zu berichten. In Kundengesprächen stellt der Systec-Mitarbeiter immer wieder fest, dass nicht der eine, komplett fertige 3D-Drucker verlangt wird. Stattdessen wünschen sich viele Kunden ein solides, flexibles Bewegungssystem mit einer beheizbaren Kabine, allen notwendigen industriellen Schnittstellen und einem passenden Bauraum.
„Oft möchten unsere Kunden die eigentliche 3D-Druck-Technologie auch selbst integrieren“, verrät Schwegmann. Geliefert werden solide, im Industriealltag voll belastbare Maschinenlösungen, die perfekt auf den Einsatz als 3D-Drucker vorbereitet sind.
So wie bei einem aktuellen Projekt: Ein Kunde suchte ein Basissystem, um einen eigenen Granulat-3D-Druckkopf zu entwickeln. Systec fertigte eine 3D-Druck-Zelle mit einem Kubikmeter Druckraum sowie der kompletten Bewegungs-, Steuerungs- und Sicherheitstechnik und bereitete sie auf die Integration des Extruders vor. Alles Weitere liegt in der Verantwortung des Kunden. „Unsere 3D-Druck-Systeme sind eine offene Plattform. Unsere Kunden haben die volle Kontrolle und den kompletten Zugriff auf alle Systemkomponenten“, hebt Systec-Niederlassungsleiter Jan Leideman hervor.
Transportlehre spart 18 Kilogramm Gewicht
Der Bedarf für kundenspezifische, großformatige 3D-Drucker ist da. Das zeigen viele der Anwendungsanfragen, die Schwegmann erreichen. Ein Kransystemhersteller benötigt für seine Intralogistik beispielsweise spezielle Transportlehren. Bislang wurden diese Teile, die nur wenige Nutzungszyklen durchlaufen, aus massiven Kunststoffblöcken gefräst. Dies verursachte viel Abfall und entsprechend hohe Materialkosten. Mit der erprobten additiven Fertigung der Transportlehren mit dem Material „Colorfab XT White“ schaffte es der Kunde, allein das Gewicht der fertigen Komponente von über 25 auf etwa 7 Kilogramm zu reduzieren.
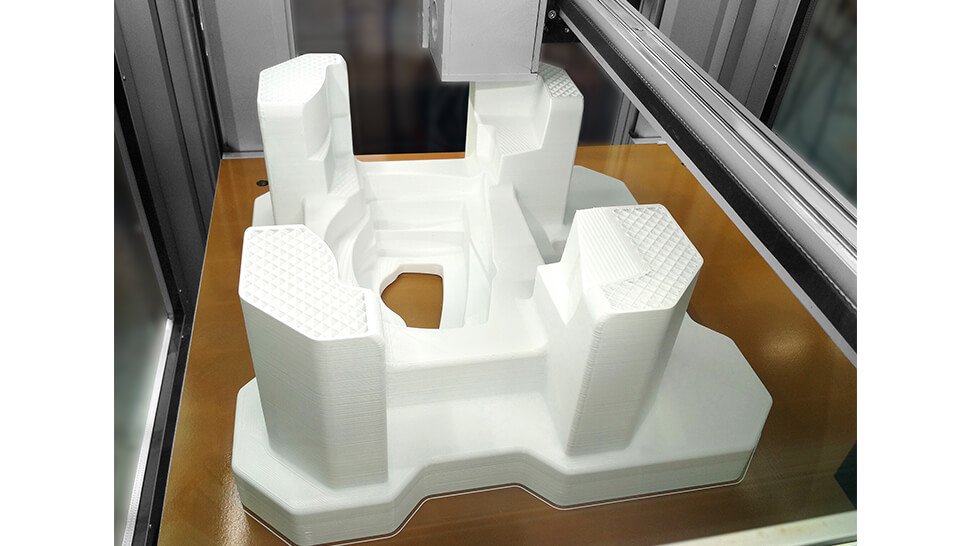
Die additive Fertigung der Transportlehre gestattet Produkteigenschaften, die mit traditionellen Produktionsmethoden wie Fräsen nicht möglich sind. Foto: Systec G 6485.1
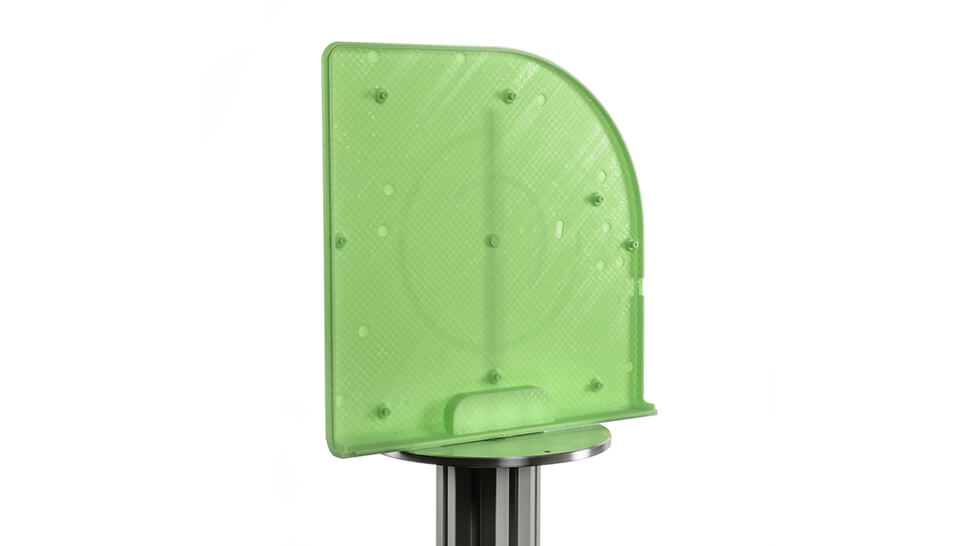
Mit dem Kunststoffgehäuseteil fing alles an. Ein passender Zulieferer war nicht zu finden. Deshalb baute Systec den FFF/FDM-3D-Drucker kurzerhand selbst. Foto: Systec
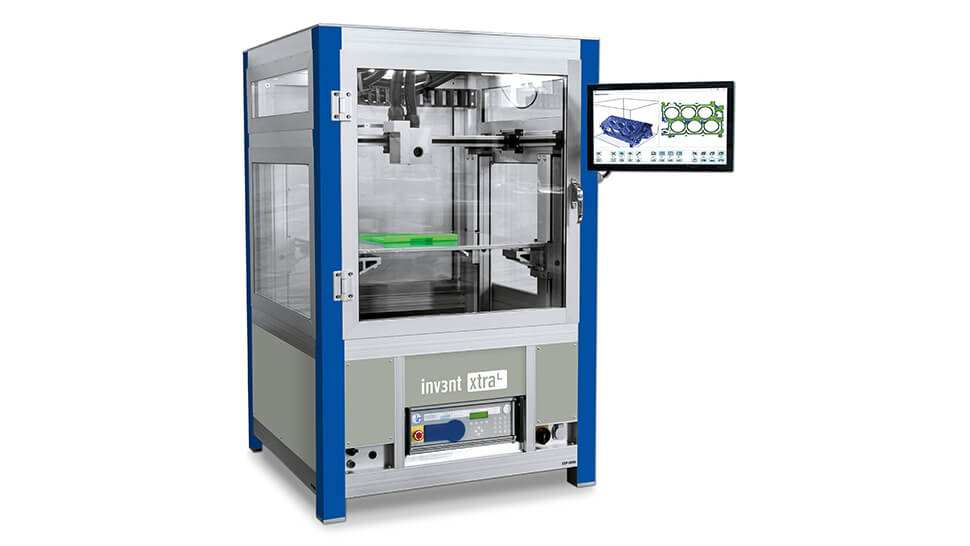
Der großformatige Industrie-3D-Drucker von Systec verfügt über einen Arbeitsraum von 625 x 625 x 625 Millimetern. Foto: Systec G 6240.3
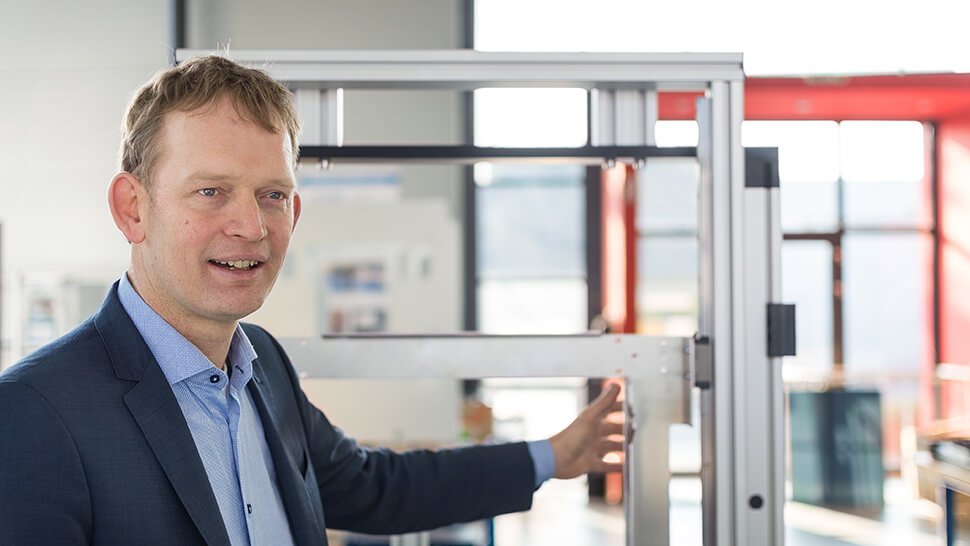
Systec-Niederlassungsleiter Jan Leideman. Foto: Systec G 6524.1

Systec-3D-Druck-Berater Marcus Schwegmann. Foto: Systec G 6531.1
Dabei dauerte ein Druck rund drei Tage. Dieser Zeitraum fiel nicht ins Gewicht, weil nur etwa zehn Teile im Jahr benötigt werden. Ein weiterer Vorteil: Mit jedem neuen Druck wurden Details verbessert. Beispielsweise erhielt die Transportlehre einen Tragegriff. Dies wäre bei gefrästen Teilen gar nicht möglich gewesen.
Ihre maschinenbauliche Kompetenz im 3D-Drucker-Segment stellt Systec gemeinsam mit dem niederländischen Technologieentwickler Demcon auch für das Euregio-Projekt „Smart Production“ zur Verfügung. Systec stellt dem Entwickler eines 3D-Druck-Kopfes für viskose Materialien eine 3D-Drucker-Basiszelle für die Integration der innovativen Technologie zur Verfügung. Ziel ist es, beispielsweise großformatige Dichtungslippen mit dem 3D-Drucker zu fertigen.
Nicht zuletzt ist die Produktion bei Systec selbst flexibler geworden, seit 3D-Drucker im Haus stehen. Selten benötigte Abdeckkappen, spezielle Umhausungen für elektrische Verdrahtungen, Musterteile und vieles mehr werden mittlerweile „schnell mal gedruckt“.
Kontakt
Ulrich Klose
Marketing Systec GmbH Münster Tel. +49 2534 8001-165 E-Mail senden
Anzeige
