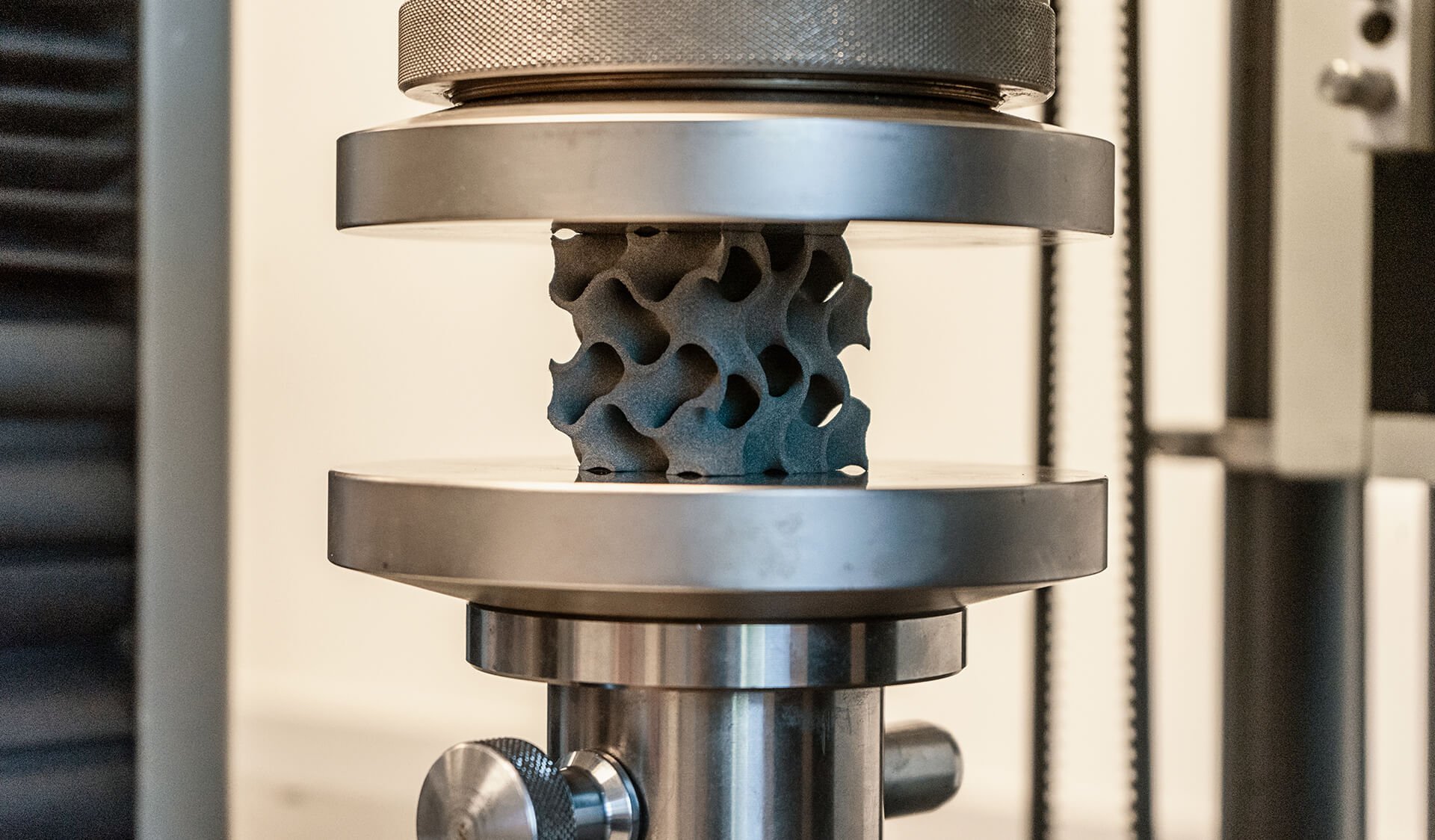
Titelthema
Heiß auf die Raumfahrt
Im Hybrid Materials Laboratory an der University of Applied Sciences and Arts of Southern Switzerland (SUPSI) werden neue Verbundwerkstoffe entwickelt. Neben einer Vielzahl an Produktions- und Analysegeräten setzen die Tessiner Forscher auch ein Sintratec Kit ein, um außergewöhnliche Strukturen zu erzeugen.
Bei künftigen Space Shuttles wird vermehrt auf die Wiederverwendbarkeit von Komponenten geachtet. Professor Alberto Ortona, Leiter des Hybrid Materials Laboratory am Institute for Mechanical Engineering and Materials Technology (MEMTi) an der University of Applied Sciences and Arts of Southern Switzerland (SUPSI), sagt: „Eine Weltraumfähre tritt von einem niedrigen Erdorbit mit einer Geschwindigkeit von 30.000 Stundenkilometern in die Atmosphäre ein. Das Vehikel wird dann durch die Luftreibung abgebremst, wodurch sich deren Oberfläche extrem erhitzt.“ Damit die Struktur beim Wiedereintritt nicht verbrennt, werden spezielle Hybridmaterialien eingesetzt – wie Strukturbauteile aus leistungsfähigen Keramikverbindungen, die über längere Zeit extremen Bedingungen, höchsten Temperaturen und Thermoschocks standhalten. Solche Komponenten müssen nicht mehr nach jeder Expedition ausgetauscht werden.
Gasgekühlte Sandwichstrukturen
An solchen keramischen Hybridmaterialien für Extrembedingungen forscht Ortona’s Team. Für das EU-Forschungsprojekt THOR entwickelte sein Institut zum Beispiel komplexe Sandwichstrukturen aus gasgekühlten Keramikverbundwerkstoffen. Dadurch wird das thermische Verhalten von Strukturkomponenten künftiger Weltraumfähren mittels eines Thermal Protection Systems kontrolliert.
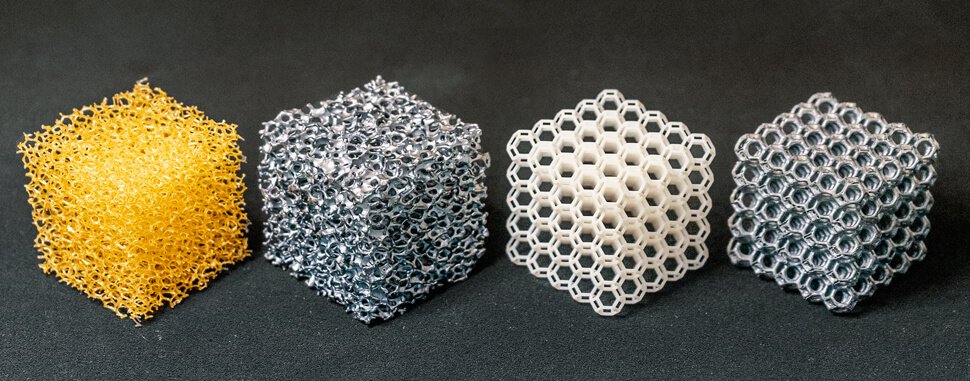
Entwicklungsprozess zellularer Keramik für den Leichtbau (von links): Natürlicher Schaumwürfel mit heterogener Zufallsstruktur, das mit einer keramischen Paste beschichtete Schaum-Template, 3D-gedrucktes Sakral-Template mit exakt strukturierter Geometrie und das mit einer keramischen Paste beschichtete Sakral-Template. Foto: Sintratec
Der Forschungsfokus der Hochschule liegt beim Engineering spezieller Materialkombinationen, worunter auch Kombinationen mit Luft – also poröse Werkstoffe – verstanden werden. Dazu gehören moderne Strukturbauteile, durch die Gase oder Flüssigkeiten geleitet werden und die in Wärmetauschern, Heizungsbrennern, Solaranlagen, Katalysatoren oder in Wasserfiltrationssystemen eingebaut werden.
Komplexes Polymer-Design
Für thermisch belastbare Komponenten eignen sich insbesondere sogenannte Ceramic Matrix Composites (CMC). Solche sowohl stabilen als auch leichten Gyroid-Architekturen vertreten aufgrund ihrer exzellenten mechanischen Eigenschaften eine eigene Anwendungsklasse unter den leistungsfähigen Komponenten. Deren Herstellung ist oft nur mit additiven Fertigungsverfahren realisierbar.
Im Hybrid Materials Laboratory werden seit 15 Jahren 3D-Drucker genutzt. Das bis anhin am häufigsten eingesetzte Stereolithografieverfahren (SLA) kommt nun gerade bei komplexen Designs wie Gyroiden an seine Grenzen. Auch die Herstellung poröser Polymere ist damit nicht möglich. Um sich dieser Schwachpunkte zu entledigen, schaute man sich am Institute for Mechanical Engineering and Materials Technology Hybrid Materials Laboratory (MEMTi) nach anderen 3D-Druck-Verfahren um und kam auf das selektive Lasersintern (SLS).
Poröse Strukturen
Für ein wegweisendes Projekt setzte Simone Vitullo, Forschungsassistent am MEMTi, das Sintratec-Kit täglich ein. Während dreier Monate untersuchte er die mechanischen Eigenschaften und Porösitäten von 3D-gedruckten Gitterstrukturen mit dem Ziel, möglichst poröse Geometrien – ohne hohen Festigkeitsverlust – zu erhalten. „Um die Geometrie, das Gewicht und die Dichte der Gyroide zu optimieren, veränderte ich systematisch die Sintertemperatur, die Lasergeschwindigkeit und die Schichtdicke“, erklärt der Assistent. Dabei setzte er die Teile mechanischen Kompressions- und Torsionstests aus. Die Zusammenhänge zwischen Druckparametern und den Charakteristika der 3D-gedruckten Teile dienen nun der weiterführenden Materialforschung am Institut.
Thermisch beanspruchte Gitterstrukturen müssen nicht nur stabil und leicht sein, sondern auch funktionale Eigenschaften aufweisen. Bis dahin verliefen die Abgasströme in Katalysatoren, ob im Auto oder in der Industrieanlage, in etwa linear. Doch die Siebwirkung ist effizienter, wenn Emissionsgase mit möglichst viel Substratoberfläche in Berührung gelangen. Die Lösung dafür sind innovative Geometrien, die den Abgasstrom verwirbeln.
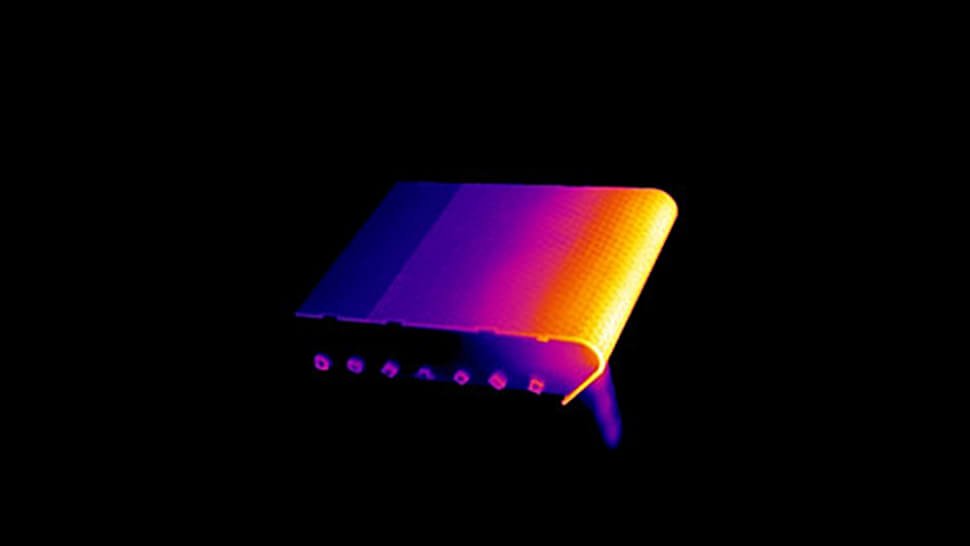
Thermischer Schutzschild: Test eines exponierten Rumpfteils in einem Plasmawindtunnel. Foto: Deutsches Zentrum für Luft- und Raumfahrt)
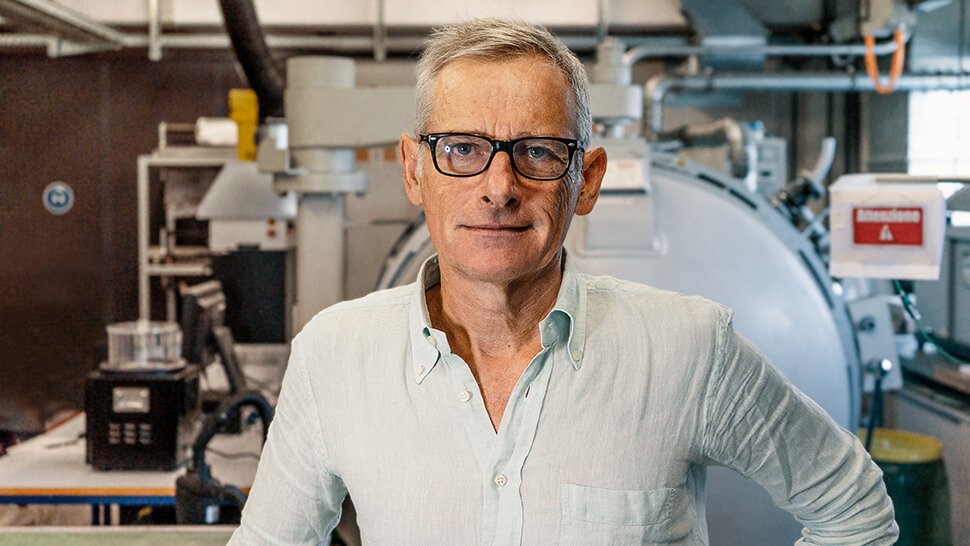
Professor Alberto Ortona, Leiter des Hybrid Materials Laboratory am Institute for Mechanical Engineering and Materials Technology (MEMTi) an der SUPSI, erwartet, mehr von den Möglichkeiten additiver Technologien zu profitieren. Foto: Sintratec
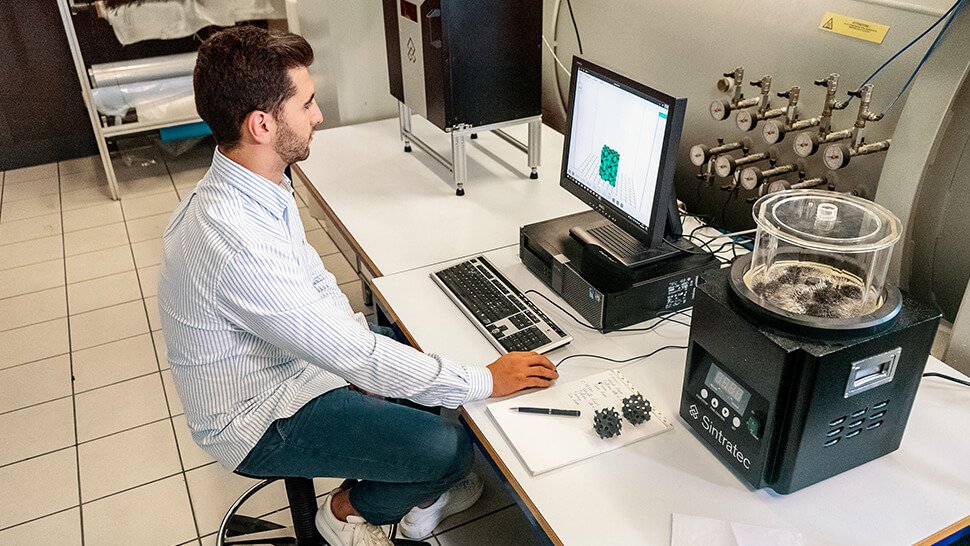
Simone Vitullo, wissenschaftlicher Assistent, forscht an hybriden Materialien. Foto: Sintratec
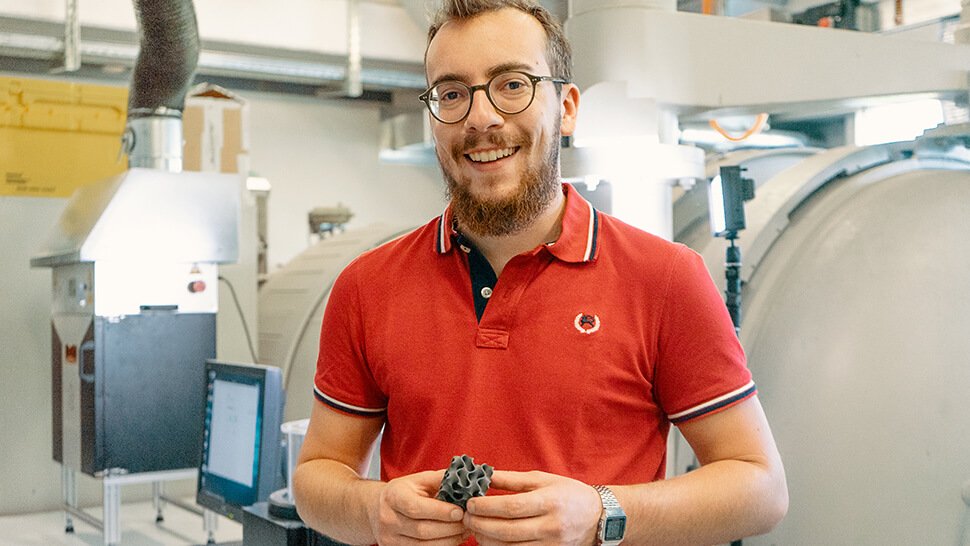
Oscar Santoliquido, Forschungsassistent, setzt auf die SLS-Technologie, um komplexe Gitterstrukturen einfach und schnell herzustellen. Foto: Sintratec
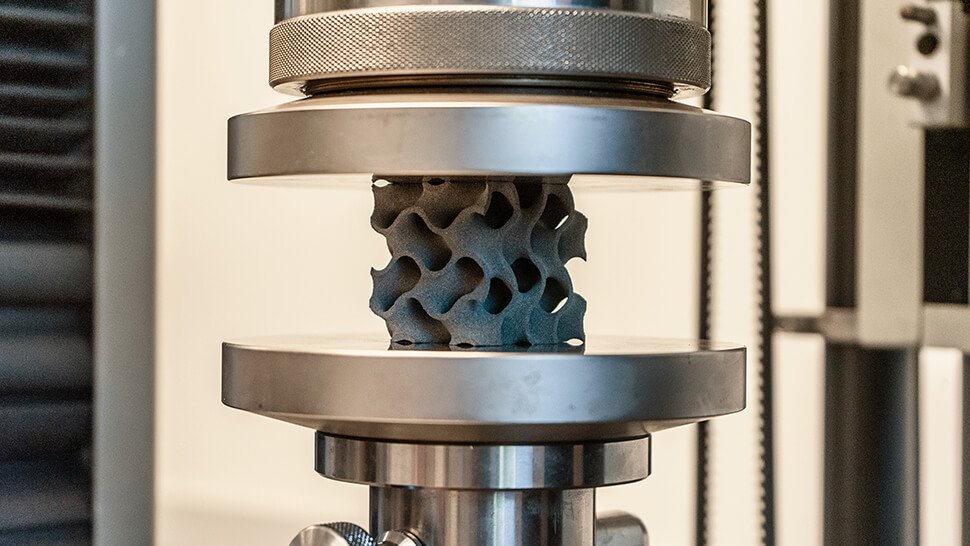
Mechanischer Festigkeitstest eines würfelförmigen Gyroid-Musters mit einer Seitenlänge von 40 Millimetern: Trotz leichter Struktur hat das Objekt aus Sintratec PA12 eine Kompressionslast von fünf Kilonewton ausgehalten. Foto: Sintratec
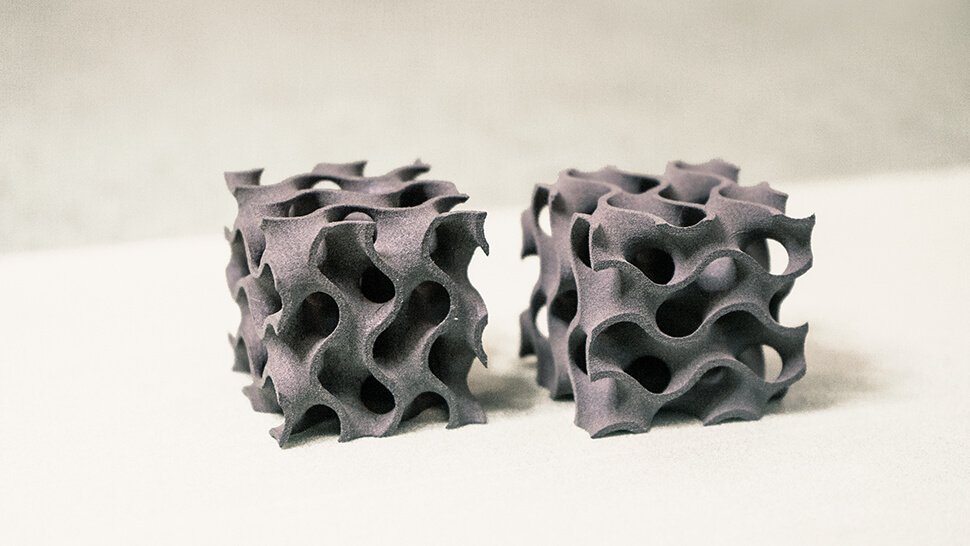
Katalysatorsubstrate, die den Abgasstrom verwirbeln: Die beiden gleich großen, aber mit unterschiedlichen Parametern 3D-gedruckten Gitterstrukturteile weisen unterschiedliche mechanische Eigenschaften und Porösitäten auf. Foto: Sintratec
Sakrale Templates
Besonderes Augenmerk legt das MEMTi außerdem auf das Engineering von keramischen Verbundwerkstoffen, die mittels Strukturvorlagen aus Sintratec PA12 realisiert werden. Ortona erläutert: „Solche Strukturvorlagen nennen wir sakrale Templates.“ Der Ausdruck erklärt den raffinierten Herstellungsprozess: Das via SLS 3D-gedruckte Polymer-Template wird mit einer keramischen Paste beschichtet, worauf das Polymer bei der darauf folgenden Wärmebehandlung verbrennt. Dabei entsteht eine hohle, ultraleichte und hochstabile Keramikstruktur. Diese werden nun durch das Schweizer Unternehmen Engicer SA industriell hergestellt.
Oscar Santoliquido, Forschungsassistent am MEMTi, ergänzt: „Dank der offenen Parameter des Sintratec-Kit konnten wir die 3D-gedruckten Objekte mit den besten Eigenschaften definieren, die erforderlich sind, um die Keramikbeschichtung optimal auf das Template aufzubringen. Die SLS-Technologie erlaubt uns, komplexe Gitterstrukturen einfach und schnell herzustellen.“
Der Impulsgeber
In Zukunft sollen die komplexen Keramikstrukturen direkt additiv gefertigt werden. „Je weiter sich die additiven Technologien professionalisieren, umso mehr werden wir von deren Möglichkeiten profitieren“, resümiert Ortona. Dass der 3D-Druck zu neuen Engineering-Paradigmen verhilft, ist im Bereich der keramischen Verbundwerkstoffe offensichtlich.
Kontakt
Luca Meister
Freier Fachjournalist
Zürich
E-Mail senden
Gabor Koppanyi
Head of Marketing and Sales
Sintratec AG
Brugg (Schweiz)
Tel. +41 56 552 00 22
E-Mail senden
Anzeige
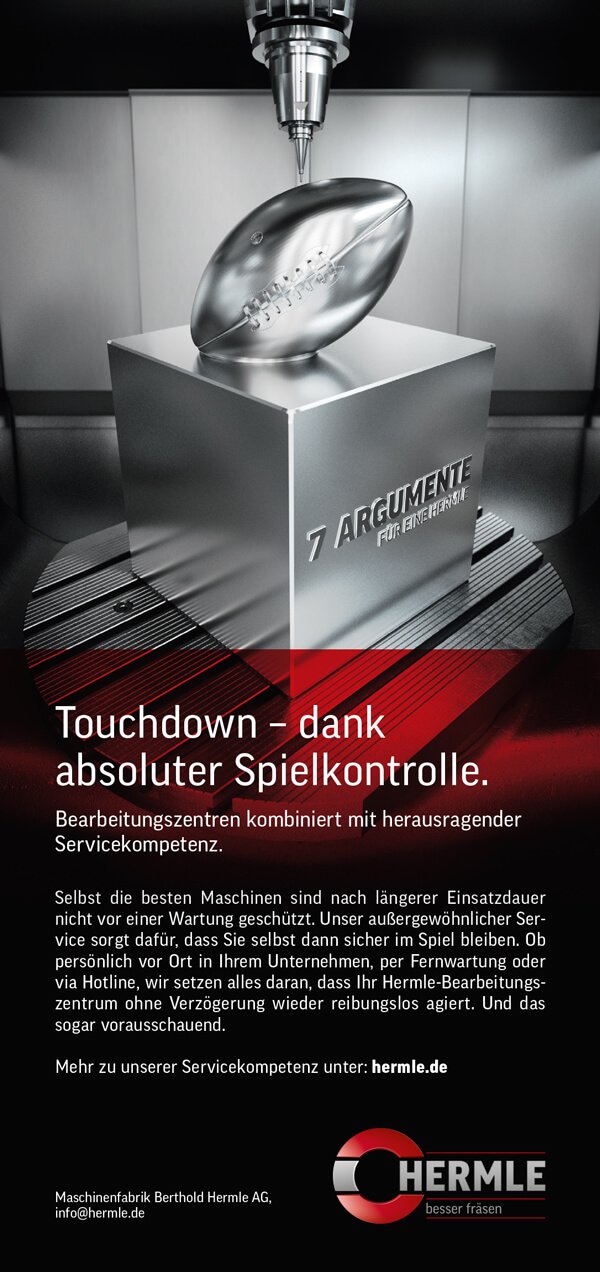