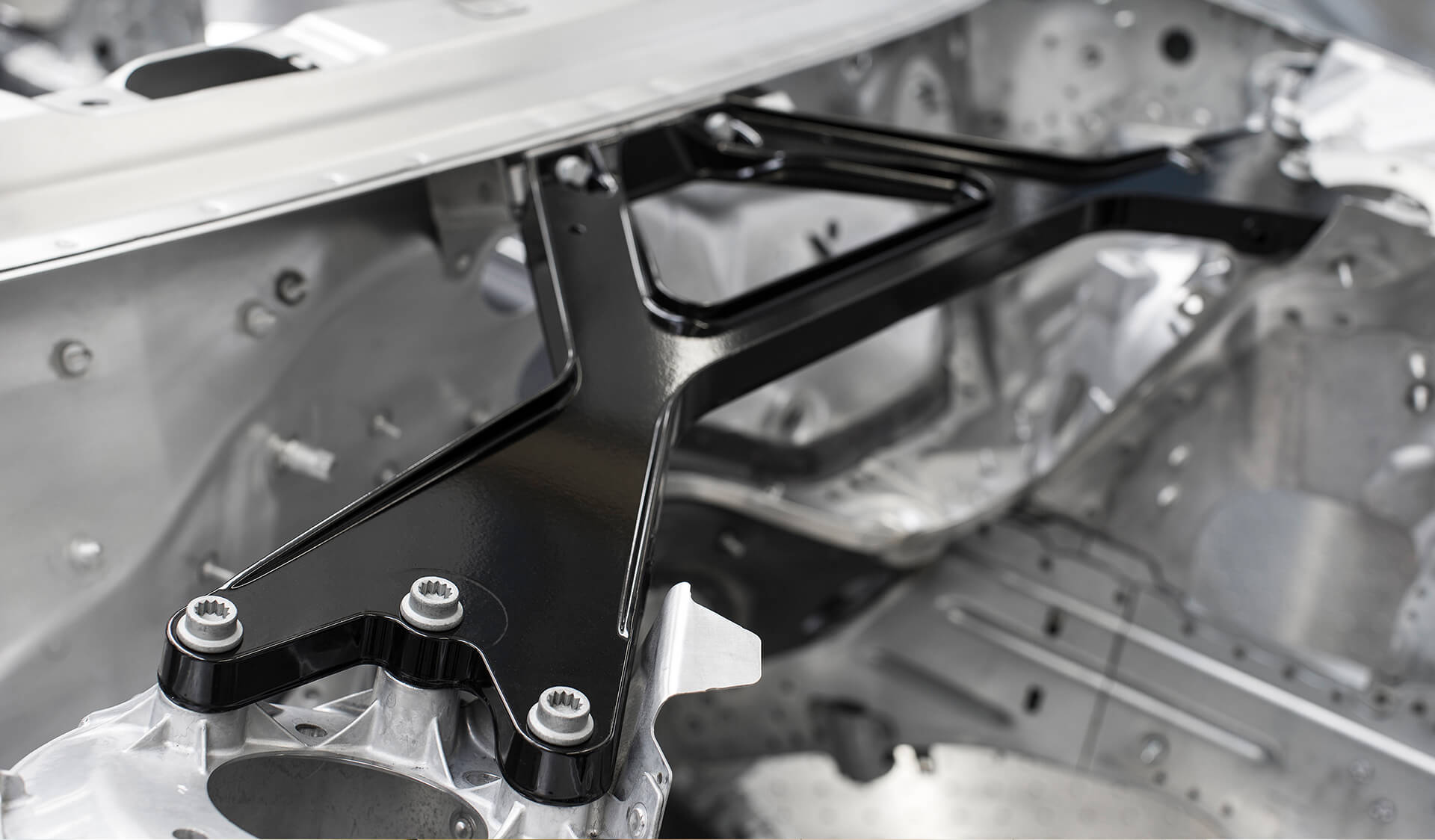
Produktion
Leichte Herausforderung
Magnesium ist ein Leichtgewicht unter den Metallen. Darin ist sich die Ingenieurswelt einig. Doch geht es um dessen Korrosionsschutz, herrscht oftmals das Vorurteil, Magnesium sei schwer zu händeln. Stimmt nicht, sagen die Oberflächenspezialisten der Benseler-Firmengruppe. Sie setzen sich schon lange mit den charakteristischen Besonderheiten von Leichtmetallen auseinander und beherrschen deren Korrosionsschutz. Das zeigt ein aktuelles Projekt: die Domstrebe des neuen Audi A8.
Neben Aluminium und Kohlefaserstoffen gehört Magnesium zu den Materialien, mit denen Leichtbaukonzepte in der Automobilindustrie umgesetzt werden, etwa um die Fahrdynamik zu optimieren oder Gewicht einzusparen. „In weiten Kreisen herrscht jedoch noch immer das Vorurteil, dass Magnesium hinsichtlich des Korrosionsschutzes nicht beherrschbar ist“, diese Erfahrung hat Uwe Büchle, Leiter Vertrieb der Benseler Beschichtungen GmbH & Co. KG, gemacht.
„Korrosionsschutz ist auch bei Magnesium dauerhaft und verlässlich machbar“, betont Büchle. Benseler hat sich bereits vor Jahrzehnten auf den Korrosionsschutz von Leichtbaumetallen spezialisiert. „Inzwischen können wir tatsächlich schon von Fahrzeuggenerationen sprechen, für die wir Leichtbaukomponenten korrosionssicher beschichtet haben“, stellt der Vertriebsleiter fest.
Nicht zuletzt aus diesem Grund setzt die Stihl Magnesium Druckguss, ein Unternehmen der Andreas Stihl AG & Co. KG, neben eigenem Know-how auf die Unterstützung von Benseler. Der Produzent fertigt im Auftrag der Audi AG die Domstrebe für den künftigen A8. Das Magnesiumbauteil wird im Warmkammerdruckgussverfahren hergestellt.
Der Mix macht’s
In der aktuellen Generation des A8 setzt der Fahrzeughersteller in der tragenden Karosseriestruktur erstmals auf einen Mix aus vier Materialien: In dem sogenannten Audi Space Frame sind Aluminiumteile, warmumgeformte Stahlkomponenten, kohlenstofffaserverstärkter Kunststoff (CFK) und Magnesium für die Domstrebe verbaut. Das Ziel des automobilen Leichtbaus: geringes Gewicht und hohe Steifigkeit für mehr Komfort, Effizienz, Fahrdynamik und Sicherheit.
Die Magnesiumdomstrebe sitzt im Motorraum und ist dort an den beiden Federbeindomen sowie an der Stirnwand verschraubt. Sie ist ein Garant für die hohe Torsionssteifigkeit der Karosserie und hilft bei einem Frontalaufprall, die auftretenden Kräfte auf drei Lastebenen im Vorderwagen zu verteilen.
Der Vorteil des Leichtbaumaterials Magnesium: Im Vergleich zum Vorgängermodell aus Aluminium reduziert es das Gewicht der Domstrebe um 28 Prozent. Die Herausforderung ist, diese Druckgusskomponente ein Fahrzeugleben lang sicher vor Korrosion zu schützen, denn Magnesium verhält sich im Zusammenbau mit anderen Metallen unter Umwelteinflüssen anders als Stahl.
Maßgeschneiderter Schutz
Das Kundenprojekt ist bei der Benseler-Firmengruppe 2018 angelaufen. Die Magnesiumdruckgussteile erhalten am Standort Kornwestheim einen auf ihre Anforderungen passgenau abgestimmten Rundumkorrosionsschutz in nahezu Schwarz-Hochglanz. „Das Ziel ist ein qualitativ hochwertiger, dauerhaft zuverlässiger Schutz, bei dem die Verbaubarkeit der Komponenten sichergestellt ist“, erklärt Vertriebsleiter Büchle.
Um Leichtmetalle wirkungsvoll gegen Umwelteinflüsse zu schützen, greifen die Oberflächenspezialisten auf eine Multimetall-Vorbehandlung in drei Phasen zurück: Entfettung, Abtragen der Entfettungslösung (Dekapierung) und chromfreie Konversion. Eingehende Analysen und enge Prozessgrenzen stellen sicher, dass jede Phase optimal auf die Legierung der Magnesiumteile angepasst ist, um den empfindlichen Werkstoff nicht anzugreifen.
Bei der Entfettung wird, ähnlich wie bei Stahl, ein alkalisches Medium eingesetzt. Im Tauchbecken muss dafür eine Balance zwischen Reinigung und Schonung gefunden werden, um Rückstände aus Vorprozessen sicher zu entfernen, ohne das Bauteil selbst zu schädigen. Ausschlaggebend sind Konzentration, Temperatur und Verweildauer im Becken.
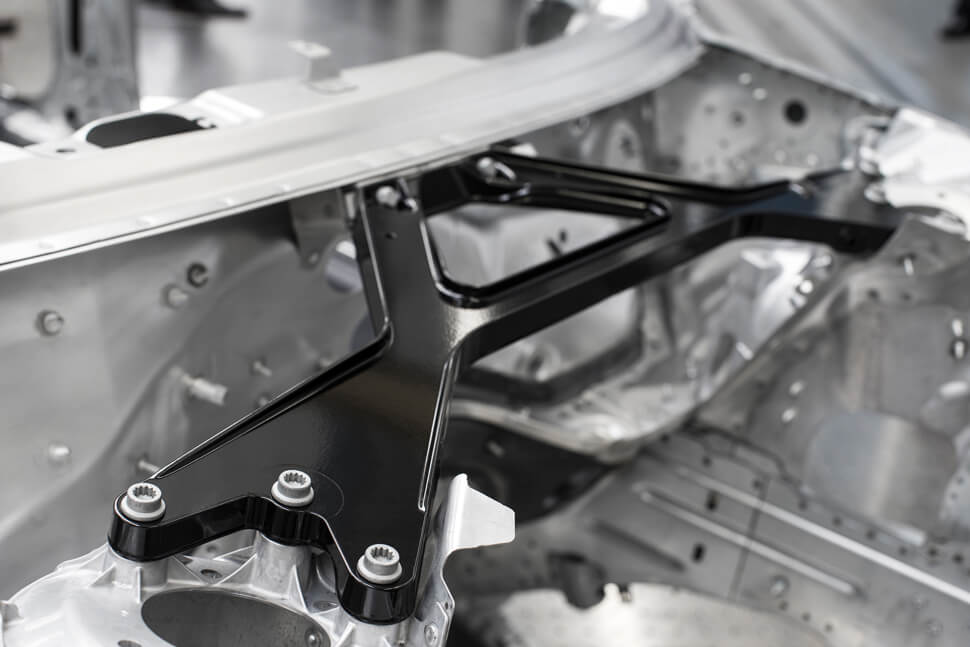
Die Domstrebe dient der Versteifung der Karosserie. Der Mix aus vier Materialien soll für geringes Gewicht und hohe Steifigkeit sorgen. In dem Audi Space Frame sind Aluminiumteile, warmumgeformte Stahlkomponenten, kohlenstofffaserverstärkter Kunststoff und Magnesium verbaut. Foto: Kati Ebner/Audi
Bei der anschließenden Entfernung des alkalischen Mediums sind – abhängig von der Legierung des Magnesiums – verschiedene Säuren im Einsatz. Mit der chromfreien Konversion schließt Benseler die Vorbehandlung der Magnesiumteile ab. Eine komplexe Verbindung verschiedener Elemente wie Titan, Mangan und Zirkon hinterlässt dabei eine dünne Schicht im Nanometer-Bereich auf dem Leichtmetall, die unter anderem als Haftvermittler für die folgende Beschichtung dient.
Die anschließende kathodische Tauchlackierung (KTL) auf Epoxidbasis, die so auch zur Behandlung von Stahl angewandt wird, realisiert Schichtdicken zwischen 15 und 25 Mikormetern. Das umweltfreundliche Verfahren – als Lösungsmittel wird zu über 99 Prozent demineralisiertes Wasser eingesetzt – dient zusammen mit der Multimetallvorbehandlung als optimale Vorbereitung und Grundierung für die spätere Pulverlackierung.
Um die erforderlichen Toleranzen zu erreichen, müssen an den Bauteilen Bohrungen oder Gewinde mit speziellen Klebepunkten oder Stopfen abgedeckt werden. Nach der Maskierung wird das elektrostatisch aufgeladene Pulver auf die grundierten Bauteile appliziert, wo es sich beim anschließenden Einbrennprozess vernetzt.
Die daraus resultierende Beschichtung erfüllt hohe Ansprüche an Chemikalien- und Wetterbeständigkeit und zeichnet sich durch Härte und Kratzfestigkeit aus. Bei der Qualitätsprüfung zeigt sich das beispielsweise durch eine Salzsprühnebelbeständigkeit von mehr als 720 Stunden und eine Ritzunterwanderung von weniger als einem Millimeter nach zehn Runden zyklischem Korrosionswechseltest. „Ein Beleg dafür, dass Magnesium ebenso wirksam vor äußerlichen Einflüssen geschützt werden kann, wie man es von Stahl kennt“, lautet das Fazit von Büchle. Im Anschluss an die Pulverbeschichtung werden die Magnesiumbauteile demaskiert, kommissioniert und nach erfolgreicher Endkontrolle an den Kunden ausgeliefert.
Kontakt
Martina Hönekopp
Senior Consultant
Sympra GmbH (GPRA)
Stuttgart
Tel. +49 711 947670
E-Mail senden
Anzeige
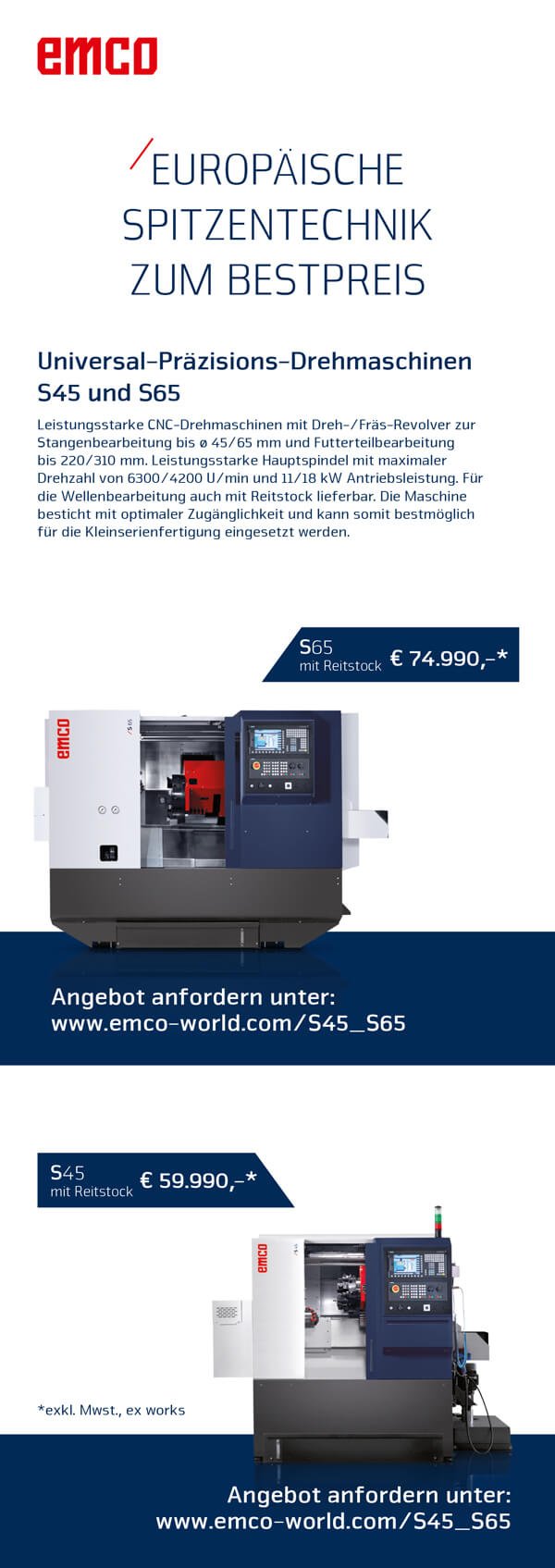