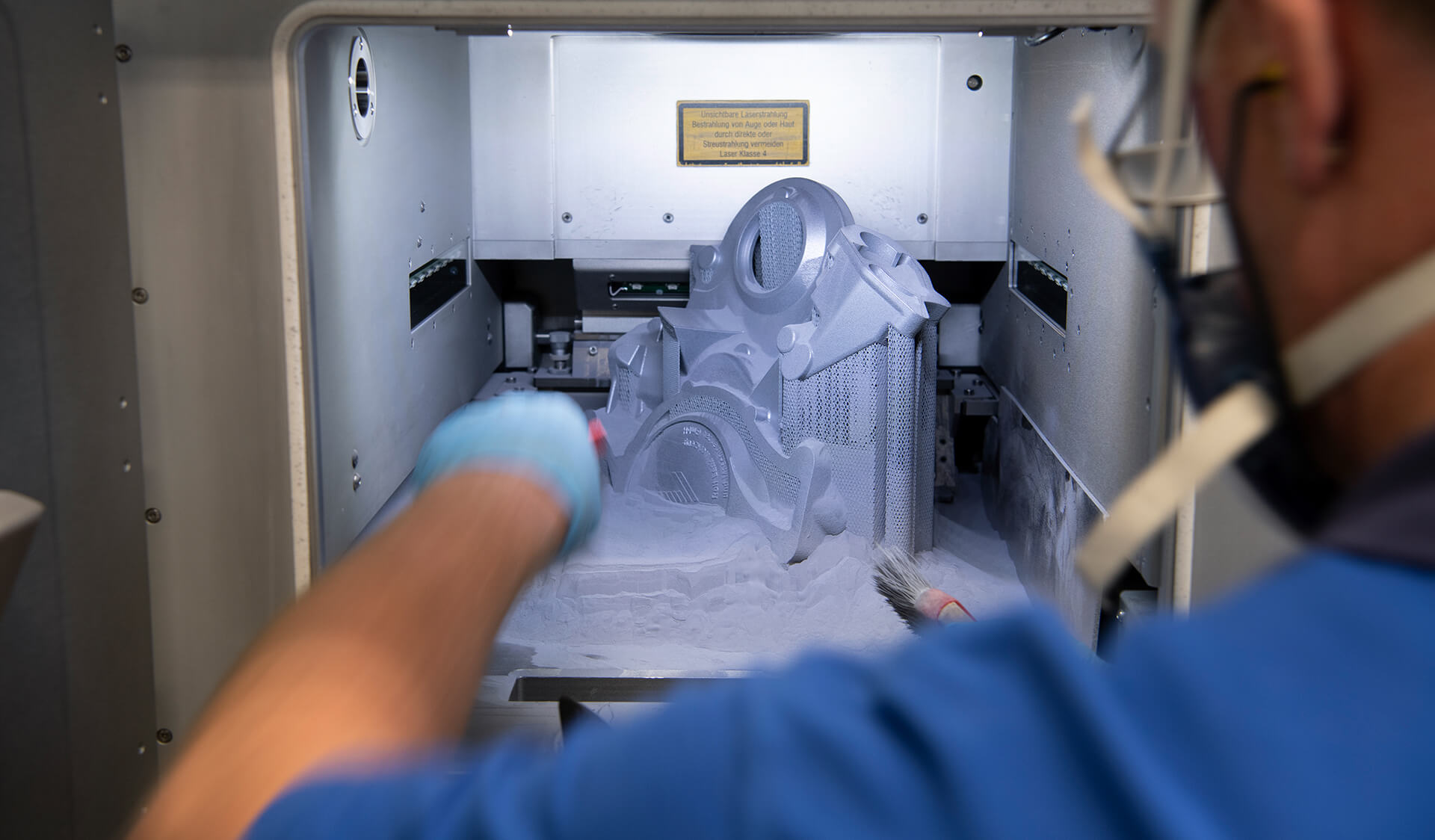
Titelthema
Optische Messtechnik sorgt für Qualität
In vielen Schritten des 3D-Druckprozesses unterstützen die Messsysteme von GOM die Qualitätssicherung. Je nach Anforderungen des Unternehmens und der Reife der Druckprozesse können verschiedene Systeme für die unterschiedlichen Ziele eingesetzt werden. Dabei sind die Systeme in der Lage, mit den Anforderungen des Unternehmens zu wachsen. Die optische Messdatenerfassung bietet gegenüber der herkömmlichen Messtechnik auch bei komplexen Geometrien entscheidende Vorteile. Konkret lassen sich zum Beispiel Abweichungen bei Freiformflächen viel schneller erkennen.
Weitere Vorteile beim Einsatz optischer Messtechnik sind weniger Iterationen, geringerer Ausschuss und eine höhere Qualität der Bauteile. Die spürbare Zeitersparnis bei der Messung und Datenverarbeitung führt letztlich zu enormen Kosteneinsparungen und damit zu einem zuverlässigen und ausgereiften Produktionsprozess.
Die Vorteile von 3D-Druckteilen liegen auf der Hand: Sie sind oft komplex, hochgradig individuell und verfügen über Freiformflächen. Die größte Herausforderung bei funktionalen Druckteilen ist allerdings, den Endverbraucher von der Verlässlichkeit der Teile zu überzeugen. Darüber hinaus müssen die Funktionalitäten exakt den Anforderungen in Bezug auf Maßhaltigkeit, Zugfestigkeit, Härte, Verschleißfestigkeit oder Hitzebeständigkeit entsprechen. Der Einsatz optischer Messtechnik zur Funktionsprüfung, Prozessüberwachung und Qualitätskontrolle bietet daher insbesondere für 3D-Druckteile immense Vorteile.
Praxisbeispiel Steuergehäusedeckel
Für eine bessere Qualitätssicherung und Reverse Engineering nutzt die Rolf Lenk Werkzeug- und Maschinenbau GmbH optische Messtechnik von GOM. In den additiven Fertigungsprozessen setzen die Mitarbeiter von Rolf Lenk einen ATOS 3D-Scanner ein. Um einen verschlissenen Originalsteuergehäusedeckel eines 1967er Cadillac Eldorado zu ersetzen, sollte eine funktionsfähige Bauteilkopie angefertigt werden.
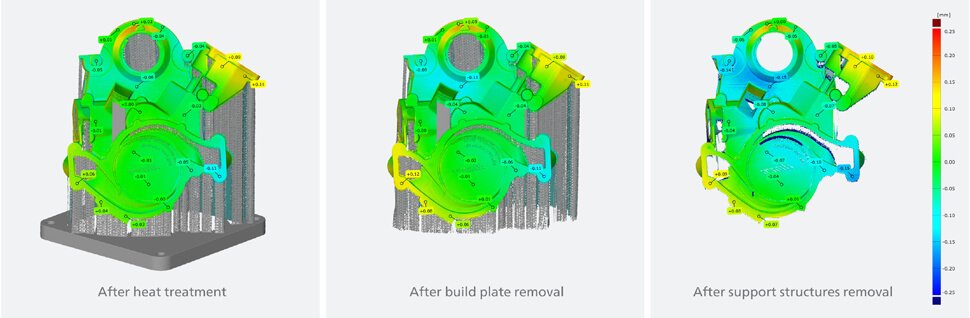
Drei Schritte zum fertigen Bauteil mit additiver Fertigung. Foto: GOM
Mithilfe des 3D-Scanners vermaßen die Mitarbeiter das Originalteil hochpräzise und erstellten ein CAD davon, das sie entsprechend ausbesserten. Im anschließenden Herstellungsprozess konnten die Mitarbeiter auf Basis dieses CAD jede geometrische Abweichung identifizieren und korrigieren.
Prozess der additiven Fertigung
Das Unternehmen Rolf Lenk setzt optische Messtechnik nicht nur zur Qualitätsprüfung am Ende, sondern während des gesamten Prozesses ein. Dies führt zu einer besseren Überwachung und damit zu schnelleren Reaktionszeiten bei auftretenden Fehlern. Gleichzeitig ermöglicht es ein tieferes Verständnis der einzelnen Prozessschritte. Sogar vor der eigentlichen Fertigung ist die optische Messtechnik schon im Einsatz.
Vor dem Druck: 3D-Testing
In der Automobilindustrie ist Titan aufgrund seiner hervorragenden mechanischen Eigenschaften sowie seiner Wärme- und Korrosionsbeständigkeit das aus technischer Sicht bevorzugte Material für die Herstellung von Funktionsteilen. Allerdings hat Titan einen großen Nachteil: den Preis. Daher untersuchen Wissenschaftler alternativ Aluminiumlegierungen.
Wenn deren mechanische Eigenschaften mit denen von Titan übereinstimmen, könnte dies zu enormen Kosteneinsparungen führen. Aluminiumlegierungen erlauben nicht nur höhere Produktionsgeschwindigkeiten, sondern sind leichter, ermöglichen eine schnellere Nachbearbeitung und können besser maschinell bearbeitet werden.
Aramis, das 3D-Testing-System von GOM, ist optimal für die Materialforschung geeignet. Die Analyse von Zug-, Druck- oder Biegeversuchen beispielsweise gibt Aufschluss über die Materialeigenschaften. Darüber hinaus kann das System das Verhalten von Bauteilen unter Last analysieren. Diese Ergebnisse bilden die Grundlage für Produkthaltbarkeit, Geometrielayout, zuverlässige numerische Simulationen und deren Validierung.
Neue Materialien zu entwickeln und bekannte zu verbessern, ist ein notwendiger Schritt, um die hohen Stückzahlen in der Automobilindustrie bewältigen zu können. Die statische und dynamische Bauteilprüfung ist dabei in der additiven Fertigung das richtige Instrument. Mit ihrer Hilfe können sowohl präzise vollflächige Daten erzeugt werden, als auch vollständige Materialanalysen: von gewöhnlichen Dehnungen bis hin zu spezifischen Rissen und Strukturen.
3D-Modell
Sobald sich der Anwender für ein zu seinen Anforderungen passendes 3D-Druckverfahren und -material entschieden hat, wird ein 3D-Modell benötigt. ATOS 3D-Scanner von GOM erzeugen eine 3D-Punktwolke, die direkt an den Drucker gesendet werden kann. Aufgrund ihrer hohen Detailtiefe und Genauigkeit der Daten kann sie als Grundlage für die Weiterentwicklung des 3D-Modells dienen.
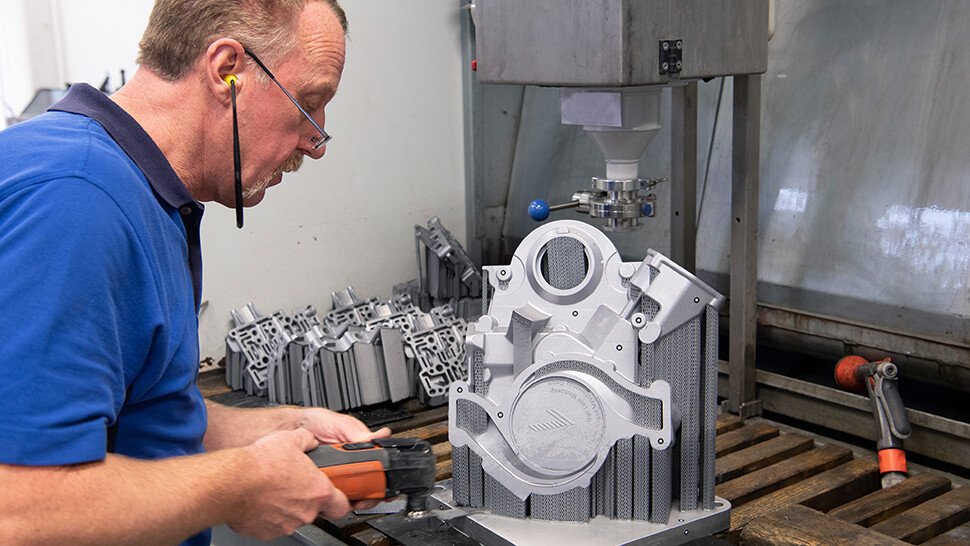
Das fertige Bauteil aus dem 3D-Drucker wird von der Bodenplatte gelöst. Fotos: GOM
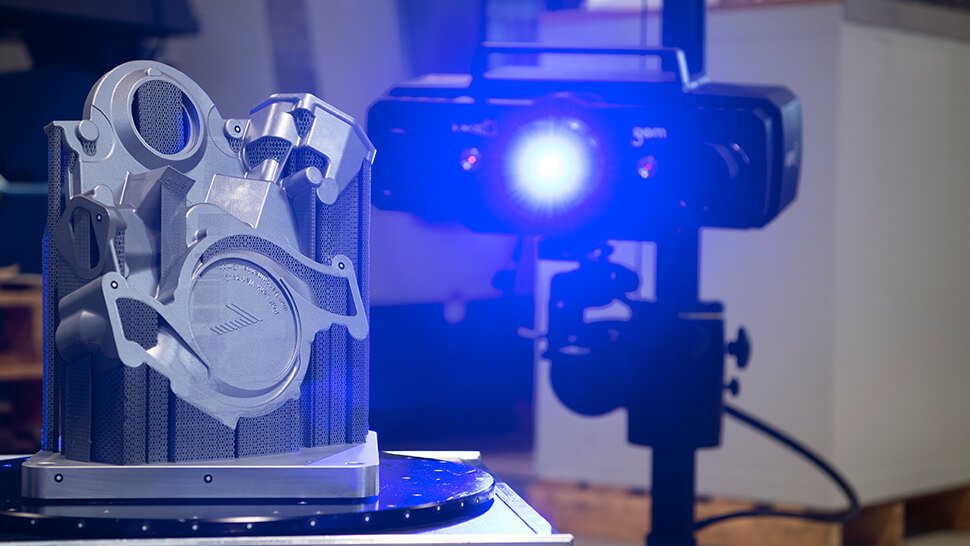
Optische Messtechnik ist der Schlüssel zum ausgereiften 3D-Druckverfahren.
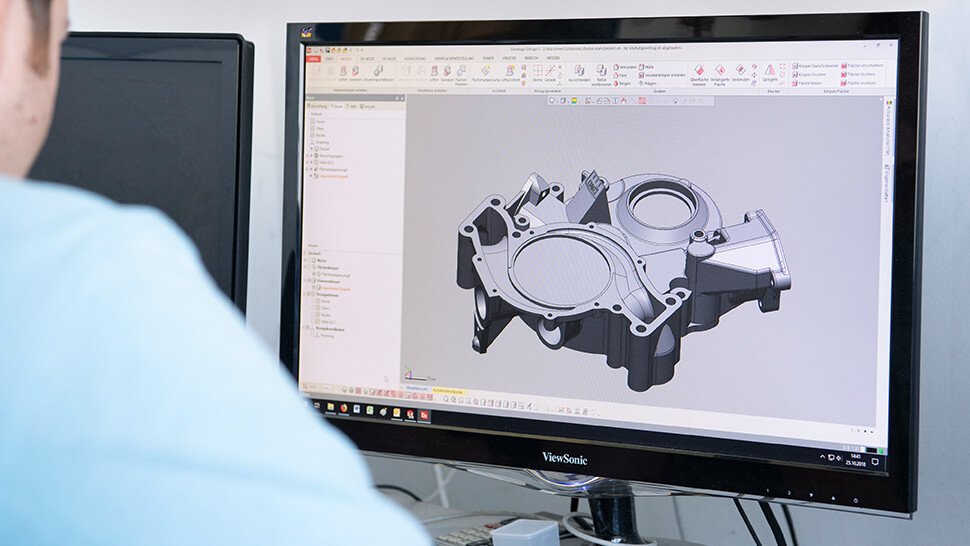
Reverse Engineering: mit Hilfe optischer Messtechnik erhält ein Cadillac Eldorado einen neuen Steuergehäusedeckel.
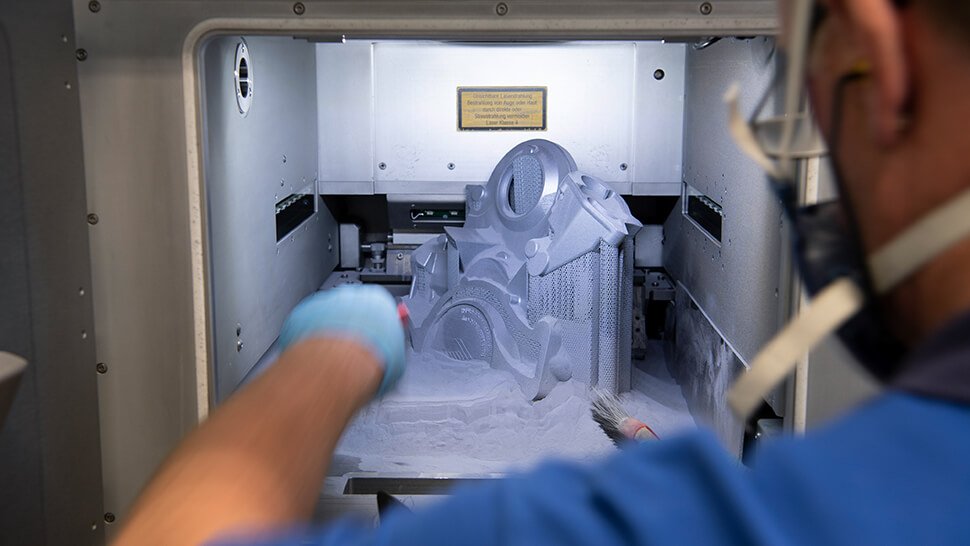
Mit optischer Messtechnik als Unterstützung ist eine funktionsfähige Bauteilkopie angefertigt worden.
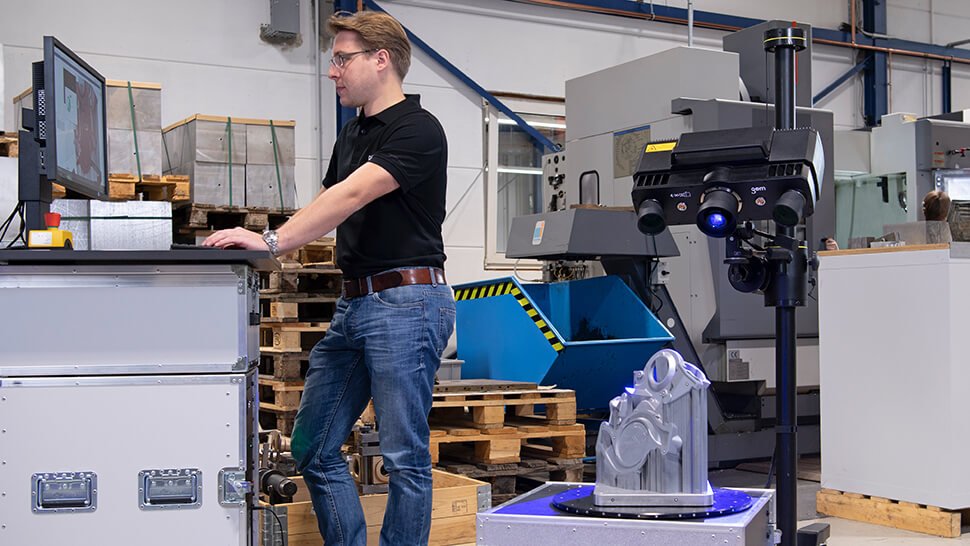
Vor dem Entfernen von der Bodenplatte wird das Bauteil auf Maßhaltigkeit geprüft.
Bei Rolf Lenk wurde der defekte Originaldeckel gescannt, um ihn via Reverse Engineering als neues Bauteil in einer CAD-Software zu hinterlegen. Reverse Engineering im CAD kann zeitaufwändig sein, aber die sauberen und hochpräzisen Daten der Scans vereinfachen diesen Prozess im Vergleich mit anderen Methoden oder Scansystemen deutlich.
Die Software GOM Inspect, die sowohl mit den ATOS-Sensoren als auch Messsystemen anderer Hersteller verwendet werden kann, verfügt über Netzbearbeitungsfunktionen, die die STL-Datei aus dem CAD sogar ohne Reverse Engineering druckfähig machen kann. Das entstandene Netz kann mit der Funktion „Löcher füllen“ lückenlos geschlossen werden. Mit nur wenigen Klicks lassen sich dann Bauteilgeometrie wie Wandstärke oder Winkel messen.
Nach dem Druck: Spannungen reduzieren
Die gängigste Methode zur Verringerung von Spannungen beim 3D-Metalldruck ist die Wärmebehandlung vor der Abnahme des Bauteils von der Grundplatte. Innere Spannungen können dazu führen, dass sich das Bauteil verformt, schrumpft oder wellt. Daher ist das Ziel, diese so gut wie möglich zu minimieren. Mit den ATOS-Sensoren kann jeder einzelne Prozessschritt während des Fertigungsprozesses festgehalten werden. Dadurch wird sofort sichtbar, wie und wann sich ein Bauteil verformt.
Die optischen Messungen des Steuergehäusedeckels vor und nach der Wärmebehandlung, nach Entfernung des Bauteils von der Grundplatte und nach Entfernung der Supportstrukturen führte zu interessanten Erkenntnissen. Die Oberflächenvergleiche zeigen, dass sich das Bauteil nach der Wärmebehandlung durch die Dehnung der Streben der Supports leicht wellte. Nach dem Entfernen der Montageplatte verformte sich das Bauteil aufgrund der Rückfederung. Weitere Verformungen kamen aufgrund der Spannung nach dem Entfernen der Supportstrukturen hinzu.
Dieses Tracken der Bauteilverformung aufgrund von Eigenspannungen liefert Informationen, die direkt in den Produktionsprozess einfließen und wertvolle Rückmeldungen über Konstruktion oder Ausrichtung der Bauteile geben.
Nachbearbeitung: Veränderungen beachten
Sowohl die Oberflächenveredelung als auch die Nachbearbeitung eines Bauteils, können seine Maße beeinflussen. Diese Veränderungen lassen sich ebenfalls mithilfe optischer Messtechnik darstellen. Ob eine Bearbeitung überhaupt erforderlich ist, kann durch eine Oberflächendefektdarstellung des Bauteils in der Software Inspect genau geprüft werden.
Wenn eine Nachbearbeitung nötig ist, kann das Spannen eines frei geformten 3D-Druckteils in einer CNC-Maschine und das Festlegen des Nullpunkts eine Herausforderung darstellen. Darüber hinaus ist es oft sehr zeitaufwändig und ungenau. Durch das Messen des Bauteils im gespannten Zustand kann die Festlegung der Nullpunkte und die Ausrichtung in Inspect vorgenommen und an die CNC-Fräsmaschine übermittelt werden.
Fertiges Bauteil
Für die finalen Prüfungen, beispielsweise zur Maßhaltigkeit der erzeugten Bauteile, werden Scanner genutzt. Die flächenhafte Messung des Druckteils ermöglicht dem Anwender, prozessbedingte Einflüsse zu erkennen und entsprechende Gegenmaßnahmen wie Vorkehrungen gegen die zu erwartende Verformung zu treffen.
Wenn es darum geht, größere Chargen zu messen, empfiehlt sich der Einsatz von automatisierten Lösungen, wie den ScanBox-Systemen. Um auch innenliegende Geometrien oder Lufteinschlüsse darstellen zu können, erweiterte GOM sein Portfolio um einen Computertomografen (CT).
Das ARAMIS-System kann mehr, als nur die Eigenschaften des gewählten Druckmaterials bereits vor dem Drucken zu analysieren. Um sicherzustellen, dass das 3D-Druckteil in Bezug auf die Funktionalität seiner Alternative aus Metallguss ebenbürtig ist, lassen sich damit auch Bauteilprüfungen durchführen.
Fazit
Die optische Messdatenerfassung bietet gegenüber der herkömmlichen Messtechnik auch bei komplexen Geometrien entscheidende Vorteile. Konkret lassen sich etwaige Abweichungen bei Freiformflächen viel schneller erkennen.
Weitere Vorteile beim Einsatz optischer Messtechnik sind die geringere Zahl von Iterationen, weniger Ausschuss und eine höhere Qualität der Bauteile. Die spürbare Zeitersparnis bei der Messung und Datenverarbeitung führt letztlich zu enormen Kosteneinsparungen und damit zu einem zuverlässigen und ausgereiften Produktionsprozess.
Kontakt
Melissa Claessens
Marketing & Communication
GOM Metrology
Leuven, Belgien
Tel. +49 531 390 29-0
E-Mail senden