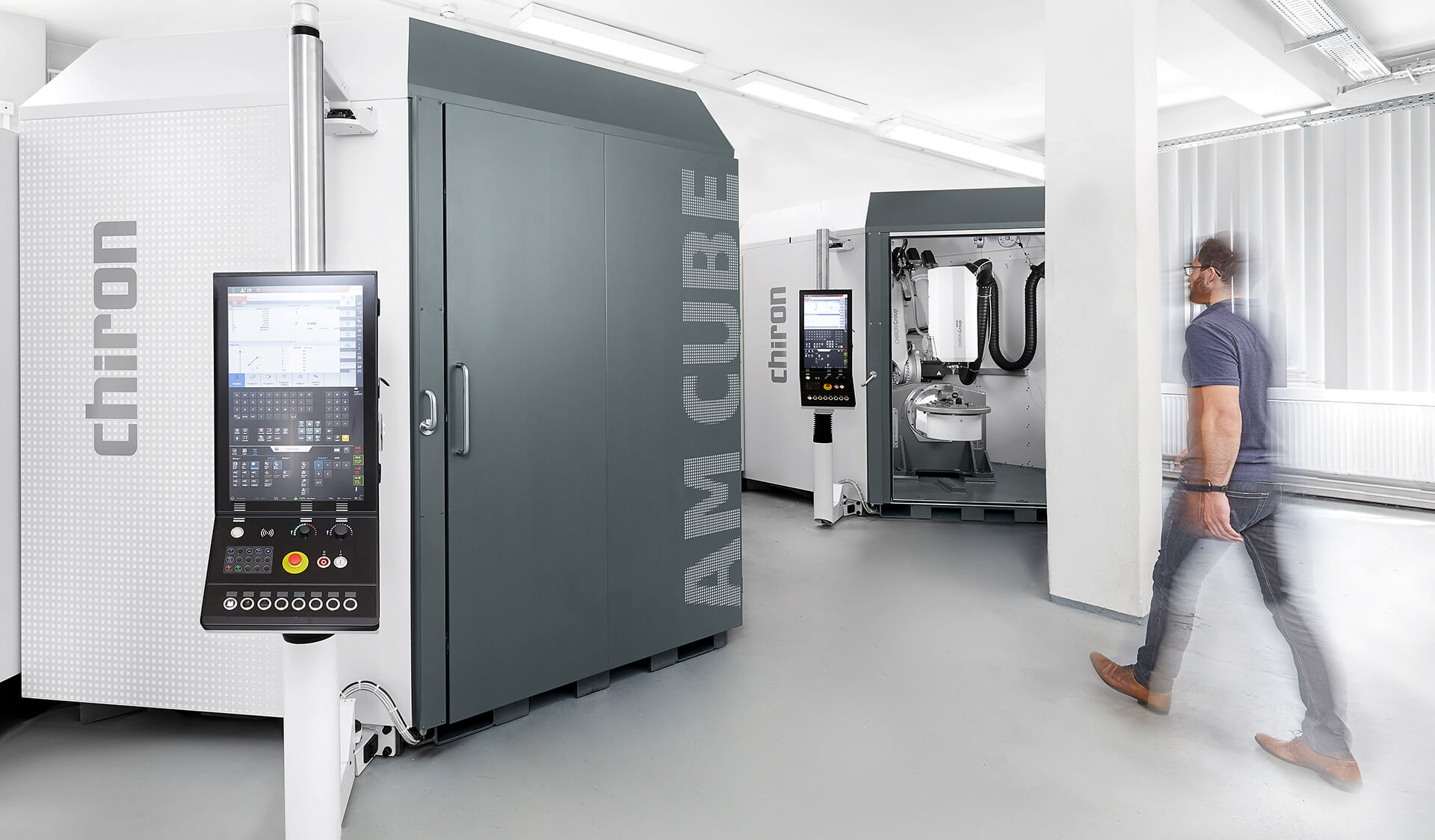
Titelthema
3D-Metalldrucker für große und komplexe Teile
Die Chiron Group hat einen 3D-Metalldrucker entwickelt: Der Spezialist für die CNC-gesteuerte, vertikale Fräs- und Drehbearbeitung ermöglicht mit dem AM Cube die Fertigung großer und komplexer Bauteile. Der 3D-Drucker eignet sich für die Beschichtung und Reparatur von Bauteilen sowie für die endkonturnahe Fertigung von Halbzeugen. Damit ergänzt der CNC-Spezialist mit Hauptsitz in Tuttlingen seine Kernkompetenzen Metallbearbeitung und Automation um die additive Fertigung.
Der Bereich Additive Manufacturing ist ein Start-up innerhalb der Unternehmensgruppe. Mit dem 3D-Metalldrucker realisiert das Unternehmen eine Anlage für die Fertigung größerer Bauteile mit langen Beschaffungszeiten und hohen Materialpreisen. Im Maschinenbau, in der Werkzeugherstellung, in der Energieerzeugung oder im Luftfahrtsektor kann diese Technologie erfolgreich eingesetzt werden.
Intuitive Bedienung
Der AM Cube ist genauso wie ein CNC-Bearbeitungszentrum an ein klassisches, kartesisches Koordinatensystem angelehnt. Bedienung und Programmierung erfolgen intuitiv. Programmiert wird die Anlage entweder mit normiertem DIN-ISO-Code oder bei komplexen Bauteilen mit einem CAD-/CAM-Software-Tool. Die Steuerung lässt sich durchgängig mit bewährten Siemens-Komponenten bewerkstelligen: von der Hardware über das Human-Machine-Interface bis zur Programmierung des Druckers. Drei Auftragsköpfe dienen zur Kombination unterschiedlicher Prozessanforderungen. Der Auftragskopf kann sogar während des laufenden Fertigungsprozesses gewechselt werden. So lässt sich mit einem Auftragskopf eine hohe Oberflächengüte, mit einem anderen ein hohes Auftragsvolumen erreichen. Durch den automatischen Kopfwechsel lassen sich diese Eigenschaften in einem Werkstück kombinieren.
Aufgrund der kleinen Stückzahlen, die mit diesem Verfahren gefertigt werden, ist eine hohe Flexibilität entscheidend. Der Drucker ist mit insgesamt drei Auftragsköpfen ausgestattet und ermöglicht zusätzlich den Wechsel des Auftragsmaterials. Draht und Pulver können innerhalb eines Fertigungsprozesses in unterschiedlichen Phasen der Produktion aufgetragen werden.
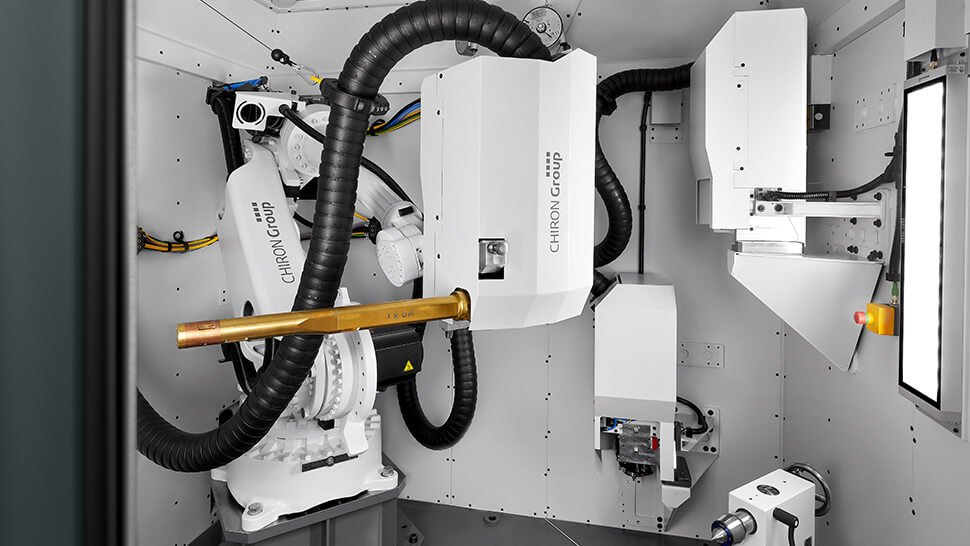
Der neue AM Cube ist wie ein CNC-Bearbeitungszentrum an das klassische, kartesische Koordinatensystem angelehnt. Fotos: Chiron
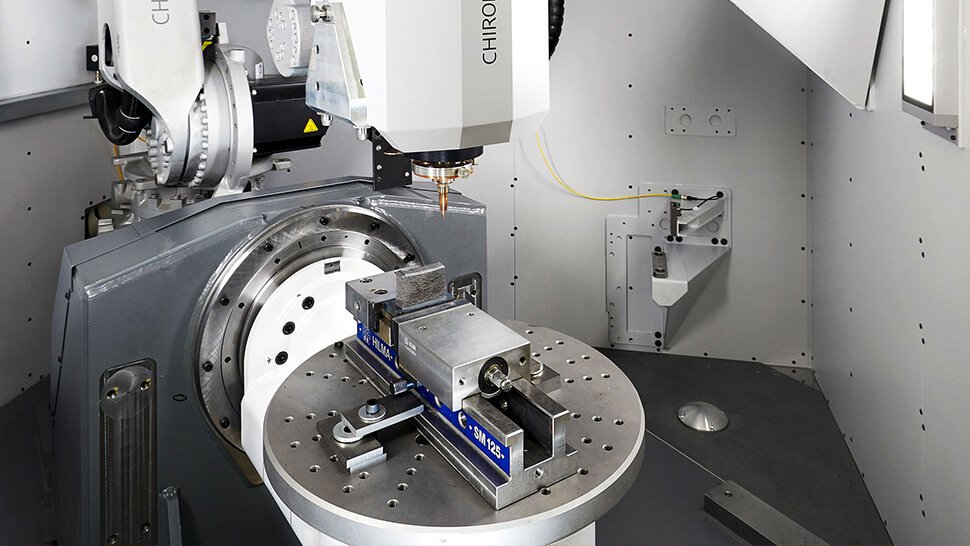
Zwei Auftragsköpfe sind bereit, einer steht in Parkposition.
Mit unterschiedlichen Rohmaterialien
Mit einer Anlage, die für zwei gängige Auftragsmaterialien – Draht und Pulver – konzipiert wurde, hat sich Chiron eine neue Technologie patentieren lassen. Beide Verfahren haben ihre Berechtigung: Während das Beschichten mit Pulver als das am meisten verbreitete innerhalb der Industrie gilt, bietet das Laserauftragschweißen mit Draht ein besseres Sicherheitshandling, zudem gibt es weniger Verlustmaterial. Draht hat nicht zuletzt den Vorteil, dass jede Art des Auftragsmaterials für die Fertigung eingesetzt werden kann.
Die Anlage ist als Plattform ausgelegt und lässt sich mit relativ geringem Aufwand von 4- auf 5-achsige Bearbeitung umrüsten. Ausgestattet mit moderner Sensorik erfüllt der Drucker alle Sicherheitsanforderungen für einen Betrieb ohne Überwachung durch den Bediener. Werden besonders reaktive Materialien wie etwa Titan bearbeitet, so kann die gesamte Anlage zur Verringerung der Oxidation mit Schutzgas geflutet werden. Das ermöglicht ein mehrstündiges Fertigen unter Schutzgasatmosphäre.
Kontakt
Axel Boi
Leiter des Additive Manufacturing
CHIRON Group
Tuttlingen
Tel. +49 7461 940-0
E-Mail senden
Anzeige
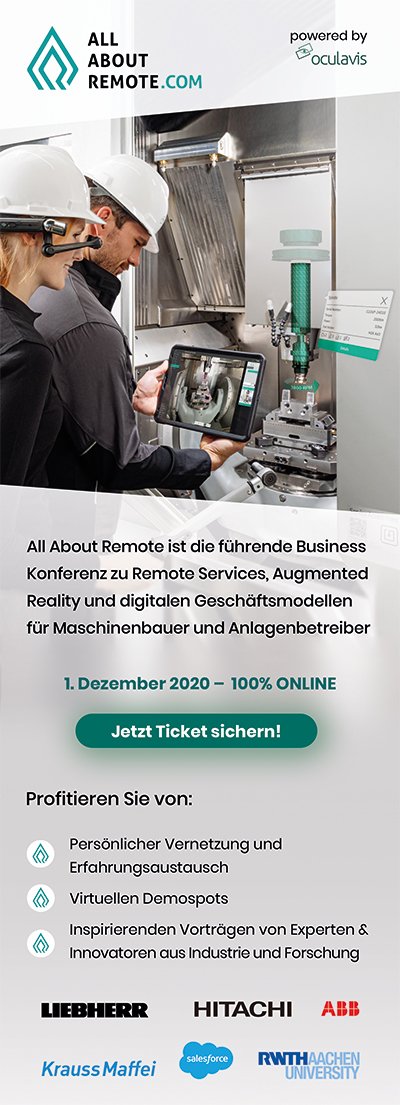