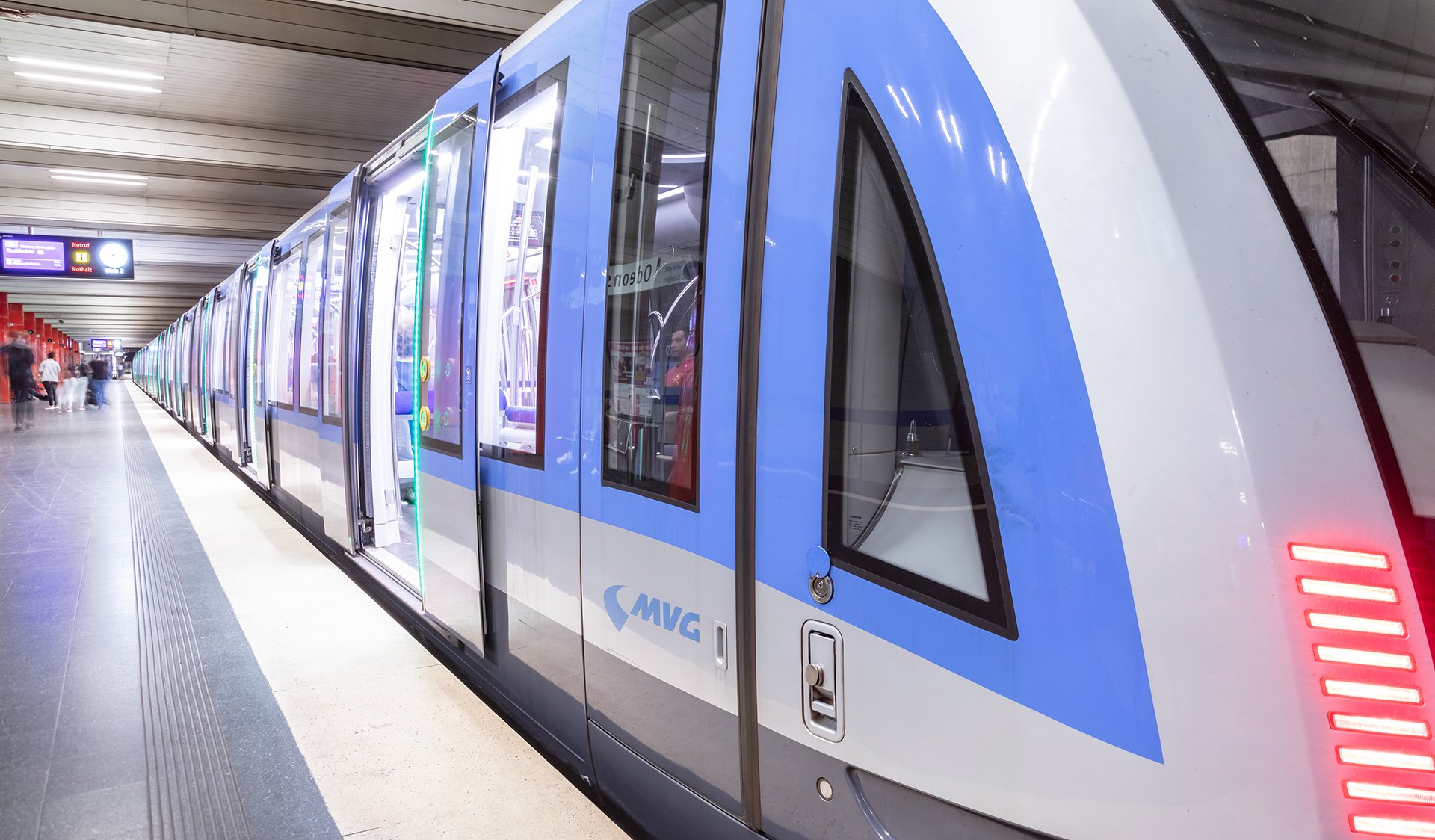
Management
Durchlaufzeit im Griff mit digitaler Terminierung
„Unsere Prozesse sind so agil, da kann nicht Tage im Voraus terminiert werden!“, erklärt Bernhard Binder, der langjährige Leiter des Bereiches Oberflächenbehandlung und heutiger Technologieexperte. Gleichzeitig betont er auch, dass die Terminierung der Fertigungsaufträge eine der wichtigsten Aktionen im gesamten Produktionsplanungsprozess ist. Ausgehend von der Projektplanung werden Kundenaufträge, Planaufträge und schließlich Fertigungsaufträge im Enterprise-Resource-Planning-System (ERP) generiert. Auf Basis dieser Planung werden Materialabrufe und Personalressourcen festgelegt und angestoßen. Mit Datencleaning, Rückmeldungen in Echtzeit und vernetzten Planungsebenen werden spontane Eingriffe in die Fertigungsabläufe im Siemens-Mobility-Werk Wien überflüssig.
Maßgebend für den Terminierungsprozess sind meist die Daten im ERP-System. Dort werden die Warenströme ausgelöst und gesteuert. Die Qualität der Daten im ERP-System sind der Schlüssel zum Erfolg für eine kalkulierbare Durchlaufzeit und letztendlich damit auch zur Erfüllung der zugesagten Liefertermine.
Bestellungen auslösen ist das Eine – die bestätigten Liefertermine einpflegen der nächste Schritt. Dieser Schritt ist elementar, um vor dem Start eines Fertigungsauftrages die Verfügbarkeit der Materialien zum Einsatzzeitpunkt sicherstellen zu können. Wird ein Fertigungsauftrag auch ohne Verfügbarkeitsprüfung gestartet, kommt es unweigerlich zu „Ad hoc“-Umterminierungen im Auftragserfüllungsprozess und damit zu Verzögerungen in der Auslieferung zum Kunden, so Patrick Solea im Werk Wien.
Modelle zu den Datenverarbeitungsebenen sind zu erweitern
Diese Digitalisierungslücke in der Auftragsabwicklung wird meist durch Ad-hoc-Aktionen manuell auf der Meisterebene überbrückt. Gerade um diese Aktionen zu minimieren, haben die Abteilung Digital-Manufacturing-Technologies (DMT) bei Siemens in München und das lokale Digitalisierungsteam im Siemens-Mobility-Werk Wien das Projekt „Integrierte Digitale Terminierung“ gestartet.
Zentraler Punkt in diesem Projekt ist die direkte Vernetzung der unterschiedlichen Planungsebenen mit der Auftragserfüllungsebene in der Fabrik. Dabei ist Ebene 0 die Produkt-Daten-Management-Ebene (PDM), wo alle Entwicklungsdaten einschließlich der Stückliste verwaltet werden. In Ebene 1 – der ERP-Ebene findet die Auftragseinplanung statt, inklusive des Einkaufs und des Lagerwesen. Neu ist die Ebene 2 – die Terminierungsebene. Ab der Ebene 3 beginnt der Fabrikbereich (Shopfloor).
Digitale Identifikation der Produkte in der Wertschöpfungskette
Dabei ist es die Aufgabe der Forscher in München in der Abteilung DMT, ein Konzept zu entwickeln, das es ermöglicht, die bestehenden Prozesse im Projektplanungstool und im ERP so mit der Fabrikebene zu integrieren, dass die „Real Time Reaction“ in der Fabrik unmittelbar auf die Auftragseinplanung und Terminierung wirkt. Das lokale Digital Factory Team in Wien um Siegfried Idinger hat indes die Aufgabe diese Ideen mit den lokalen Erfahrungen zu ergänzen, direkt vor Ort umzusetzen und zu validieren. Die Identifikation der Seriennummer des zu bearbeitenden Wagenkastens ist dabei der erste Prozessschritt.
Für Oliver Lohse und Michael Meyer-Hentschel vom DMT-Team ist der Detaillierungsgrad der Arbeitsvorgänge im ERP-Arbeitsplan ein elementarer Baustein für eine möglichst lückenlose Terminierung der Fertigungsaufträge. Demnach müssen alle terminierungsrelevanten Arbeitsvorgänge im Arbeitsplan enthalten sein, um eine Durchlauflenkung realisieren zu können.
Patrick Solea und Peter Smolik aus dem Team Digital Factory Wien haben daraufhin einen Musterarbeitsplan mit dem Planungsexperten Christian Giller so überarbeitet, dass er die echte Abwicklung im Werk widerspiegelt. Ein wesentlicher Punkt für die Terminierung ist auch die Rückmeldung der Verrichtungen in Echtzeit – das heißt, wirklich unmittelbar nach der Erledigung, um so die Abweichungen vom Planungszustand schnellstmöglich zu erkennen und entgegenwirken zu können.
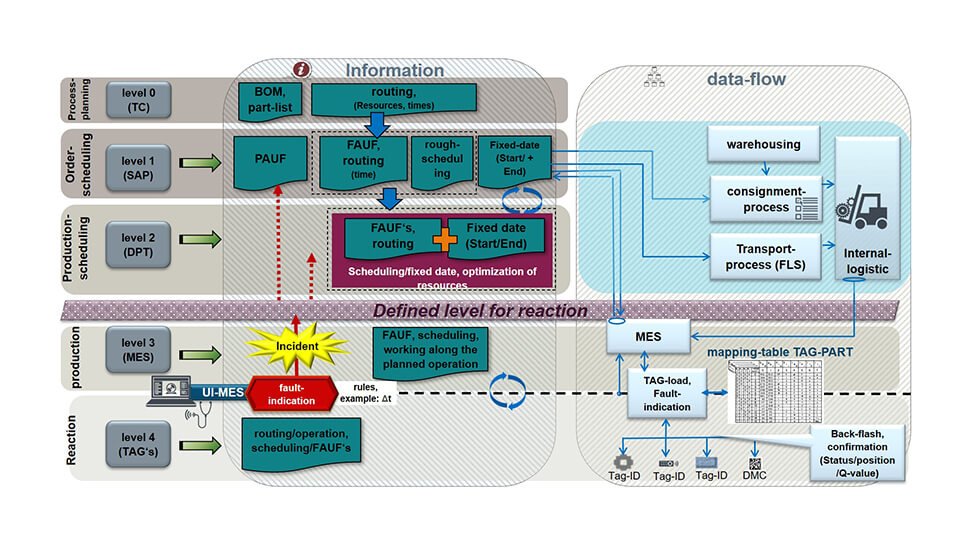
Datenverarbeitungsebenen (Level 0 bis Level 4) zur Prozess- und Auftragsplanung inklusive der Terminierung und Abwicklung in der Fabrik. Bilder: Siemens
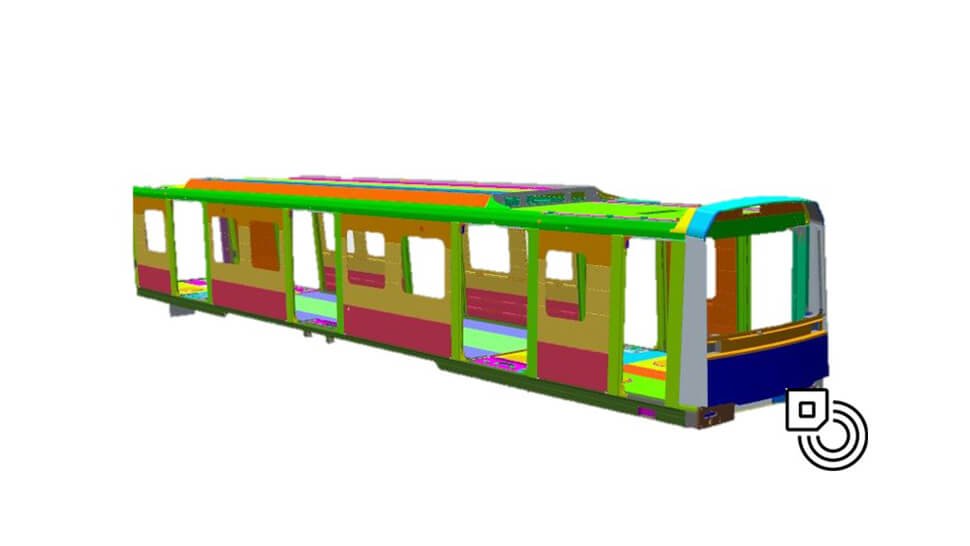
Das Produkt (hier ein Wagenkasten) wird mittels der Seriennummer anhand eines DMC oder RFID identifiziert.
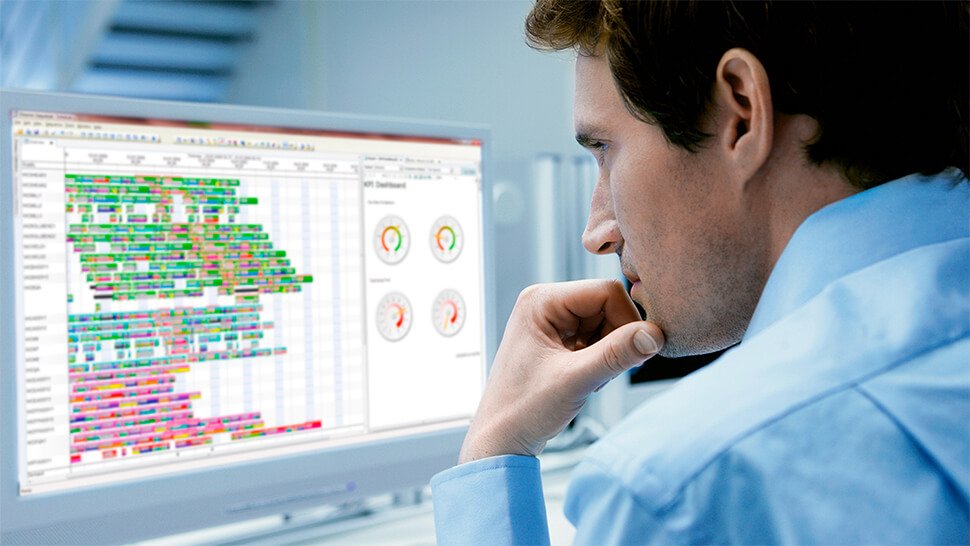
Die Advanced-Planning-and-Scheduling-Software Preactor wird in die bestehenden IT-Lösungen integriert.
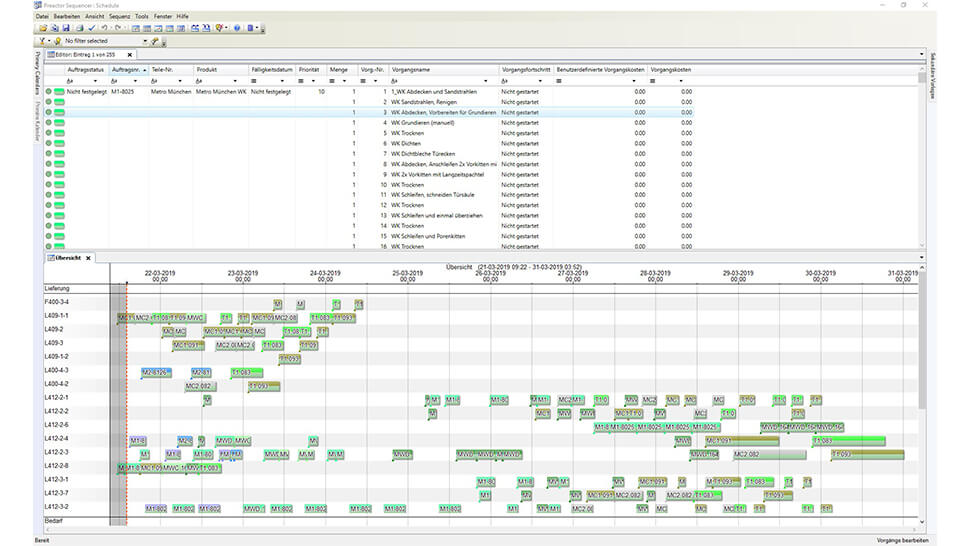
Für eine digitale Terminierung werden Arbeitsplan und Terminierung mit der Kabinenbelegung verknüpft.
Digitale Terminierung mit Unterstützung von Advanced Planning and Scheduling
In der Konzeptentwicklung erwies sich die Einführung der neuen Ebene „Digitale Produktions-Terminierung“ (DPT) als sinnvoll und notwendig. Die Siemens-Advanced-Planning-and-Scheduling-Software Preactor bietet die Möglichkeit einer exakten digitalen Terminierung. Um dieses Software-Tool sinnvoll betreiben zu können, bedarf es mehrerer Voraussetzungen. Die Lagerdaten müssen vollständig und aktuell sein, die Zeiten im Arbeitsplan müssen stimmen, die Rückmeldungen aus dem Produktionsprozess müssen verlässlich sein und alle notwendigen Ressourcen (Fertigungshilfsmittel und vor allem Personal) müssen planbar sein.
Für Smolik ist es „das Logischste der Welt“, dass die Daten verlässlich und wahr sein müssen – in vielen Fällen sind sie jedoch veraltet, fehlerhaft oder nicht vorhanden – das heißt für den Datenkonsumenten ungenießbar. Die Daten sind in manchen Fällen mehr „Abraum“ als „Rohstoff“, so Michael Meyer-Hentschel. Das heiß im IDT-Projekt ist erst mal ein Datencleaning notwendig, um Vertrauen auf der Anwenderseite zu gewinnen.
Das Terminierungstool Preactor ist so mit dem ERP- und dem Personalplanungstool vernetzt, dass ihm alle terminierungsrelevanten Daten zur Verfügung stehen. Als Ergebnis der Aktivitäten im Pilotbereich „Oberfläche“ können alle zur Verfügung stehenden Bearbeitungskabinen optimal terminiert werden – Änderungen oder Störungen werden in Realtime zurückgemeldet und zyklisch in der Terminierung berücksichtigt.
Smolik und Solea bereiten die Softwarelösung Preactor für den Produktivbetrieb vor und überarbeiten zusammen mit der Arbeitsvorbereitung die Arbeitspläne nach dem Muster und verteilen die Lösung über alle Arbeitsplätze im Bereich „Oberfläche“. Das DMT-Team in München beschäftigt sich im nächsten Schritt mit einer weiteren Integration zur Durchlauflenkung der Wagenkästen für die 32 Arbeitsschritte innerhalb dieser Abteilung. Die Herausforderung besteht dabei weniger in der Übernahme der rückgemeldeten Daten als in der Abstimmung dieser Daten mit den Prozess- und Chemiezeiten in dieser Abteilung.
Eine Vielzahl von Regeln muss berücksichtigt werden, wenn die Wagenkästen ihren Durchlauf durch die Abteilung machen. Die Rezeptur ist nicht nur abhängig von den Trockenzeiten der einzelnen Lackschichten, sondern auch von Regelabnahmeteminen mit der Qualitätssicherung und dem jeweiligen Kunden.
Laut Lohse ist ein weiterer Schritt in Richtung Digitalisierung die Entwicklung eines Tools zum Störungsmanagement. Dieses neue Tool verwendet Methoden der künstlichen Intelligenz (KI). Sie ermöglichen, Probleme im Prozessablauf optimal auszugleichen. Das DMT-Team in München arbeitet an KI-Lösungen, die nicht nur maschinenbedingte Störungen berücksichtigen. Die KI berücksichtigt zur Terminierung der Arbeitsschritte auch Unterbrechungen, die von der Verfügbarkeit von qualifiziertem Personal oder den klimatischen Beeinflussungen (zum Beispiel auf die Luftfeuchtigkeit) ausgelöst werden.
Das Konzept der „integrierten digitalen Terminierung“ in der Abteilung Oberfläche stellt einen „Footprint“ für andere Bereiche wie den Rohbau dar, so Abteilungsleiter Siegfried Idinger, den es nun weiter zu verfolgen gilt.
Titelbild: Andreas Messner/Metro München, Siemens
Kontakt
Dr.-Ing. Peter Robl
Corporate Technology
Research in Energy and Electronics
Digital Manufacturing Technologies
Siemens AG
München
Tel. +49 1522 3150978
E-Mail senden
Anzeige
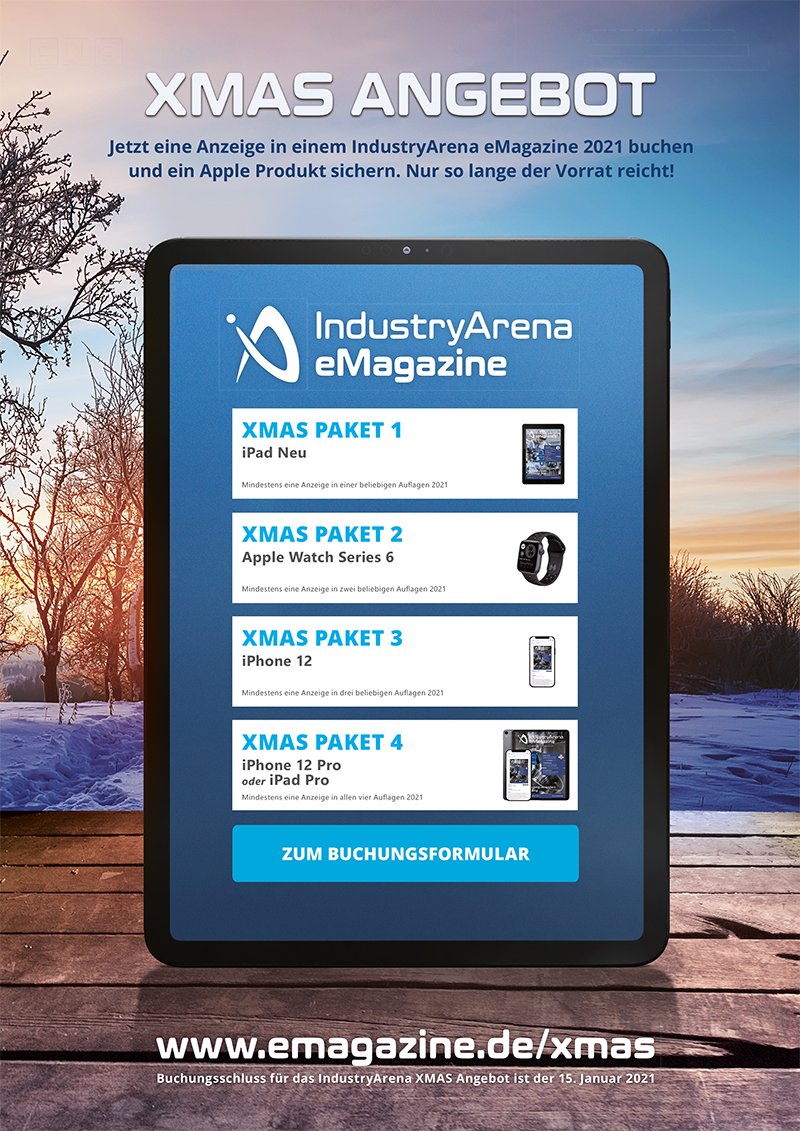