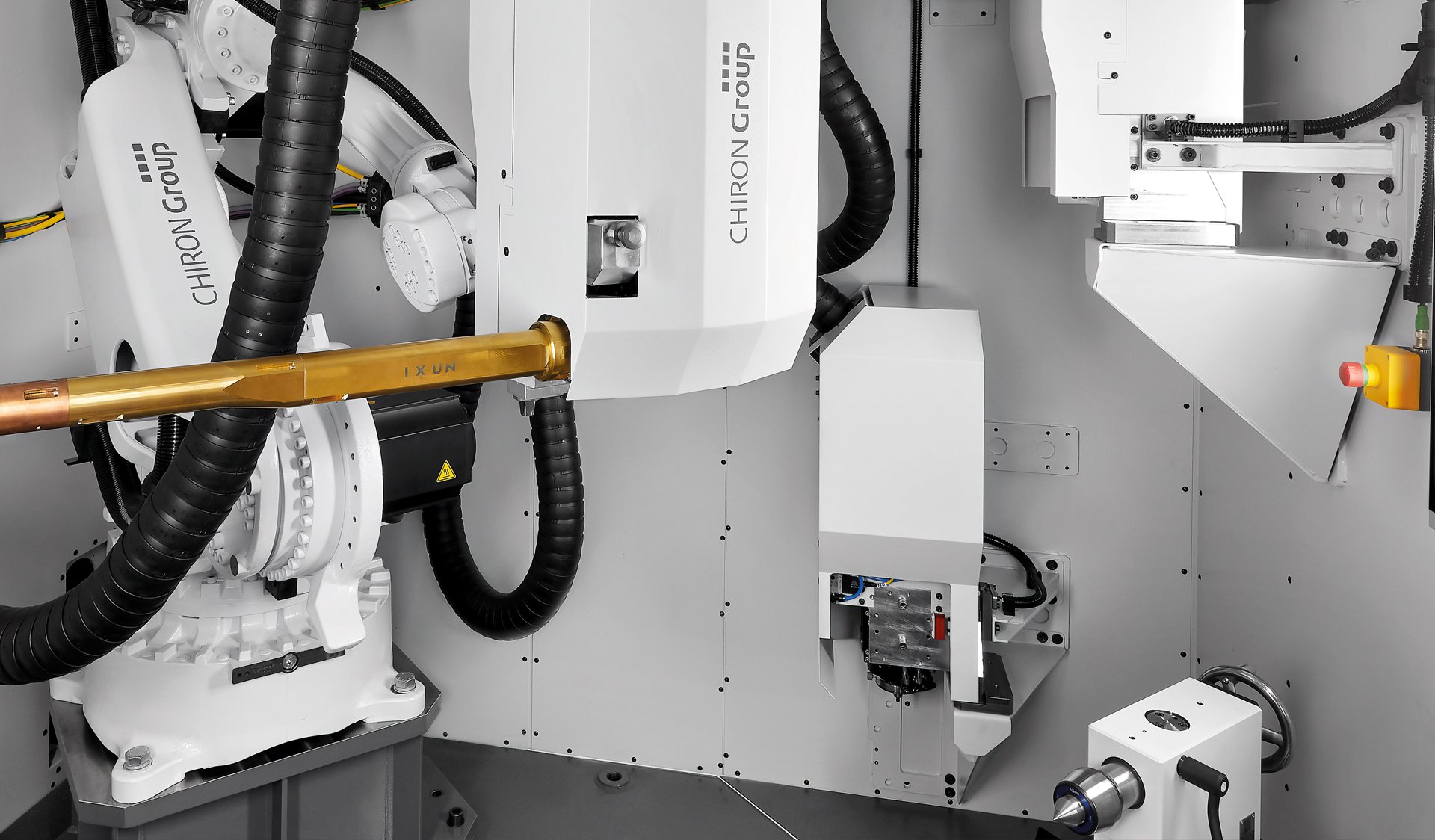
Titelthema
3D-Druck ist wettbewerbsfähig
Mit hohen Erwartungen gestartet, aber auf dem Boden der Tatsachen gelandet: Diese Erfahrung haben Unternehmen mit dem Einstieg in die additive Fertigung gemacht. Die großen Hoffnungen sind vorbei und die Entwicklung am Markt ist deutlich langsamer als die anfänglichen Erwartungen, erläutert Axel Boi, Leiter Additive Manufacturing (AM) bei der Chiron Group, im Interview mit dem IndustryArena eMagazine. Die Zielmärkte Beschichtung oder Reparatur für den Formenbau treten inzwischen deutlich sichtbarer hervor. Das Gespräch führte Chefredakteur Georg Dlugosch.
Wie entwickelt sich der Markt für additive Fertigung?
Boi: Natürlich sind wir vor drei Jahren mit hohen Erwartungen in diese Technologie eingestiegen, weil wir gesehen haben, dass Wachstumszahlen zwischen 20 und 30 Prozent erwartet wurden. Ich schätze, dieser Hype ist definitiv vorbei. Wir sind in der Realität angekommen. Ich denke, man kann heute sagen, dass die Marktentwicklung deutlich langsamer ist als das, was wir erwartet haben. Es ist für alle Teilnehmer im AM-Markt schwierig, den richtig passenden Anwendungsfall zu finden. Wenn wir funktionsgetriebene Argumentationen haben, dann setzt sich das schnell um. Die Ansicht, ich kann aus dem klassisch gefertigten Bauteil einfach per Copy and Paste eines per 3D drucken, ist falsch, und wenn man Leuten diesen Zahn zieht, dann verliert man 70 bis 80 Prozent der Interessenten. Wir haben inzwischen unsere Zielmärkte deutlich besser geschärft – das sind Beschichtung und Reparatur mit Fokus auf den Formenbau.
Wie hart war die Landung?
Boi: Die Antwort in konkreten Zahlen auszudrücken, ist sehr schwierig. Zum einen ist der Markt an sich noch extrem klein. Zudem ist der Start bei Null gewesen. Deshalb sind konkrete Zahlen irreführend. – Die Landung war jedenfalls hart.
Stichwort funktionsgetrieben, was kann man darunter verstehen?
Boi: Wenn man es schafft, in ein 3D-gedrucktes Bauteil neue Funktionen zu integrieren, dann ist die klassische Kostendiskussion deutlich weniger intensiv zu bewerten. Wenn wir Funktionen reinbringen, dann ist die Herausforderung häufig mit neuen Werkstoffen verknüpft oder einer Kombination von exotischen Materialien. Dann befindet man sich auch am Anfang der gesamten Zulassungs- und Validierungsschleife. Das macht den Prozess länger, als man es bei klassischen Werkzeugmaschinen gewohnt ist.
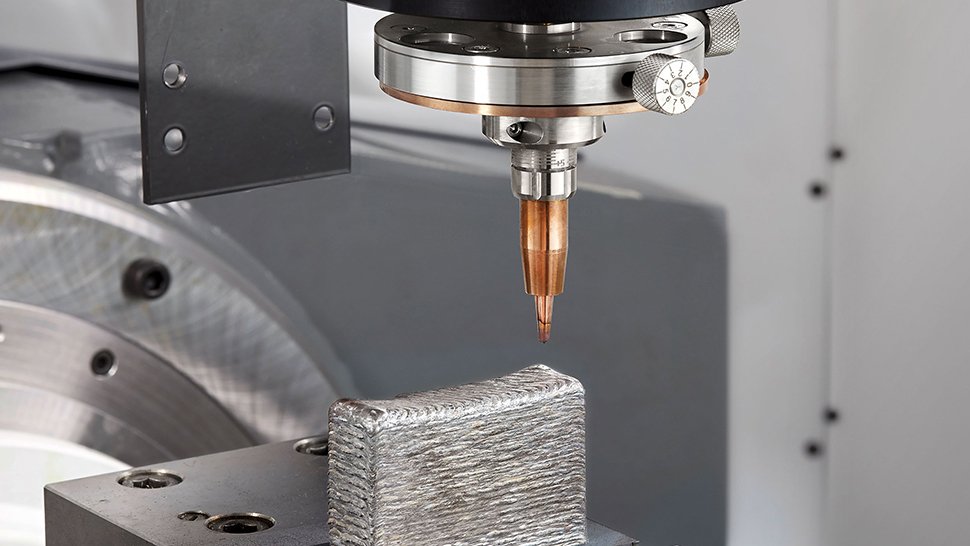
Fotos: Chiron
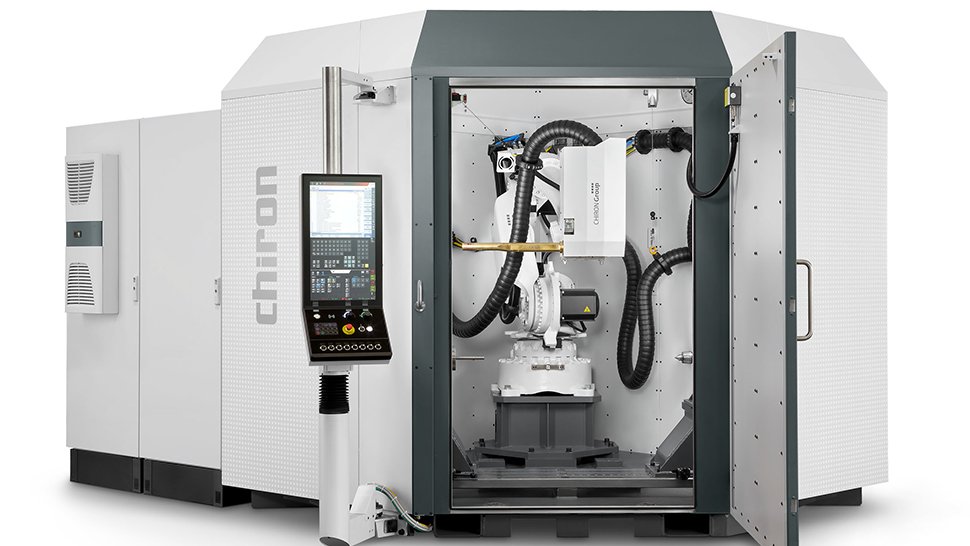
Fotos: Chiron
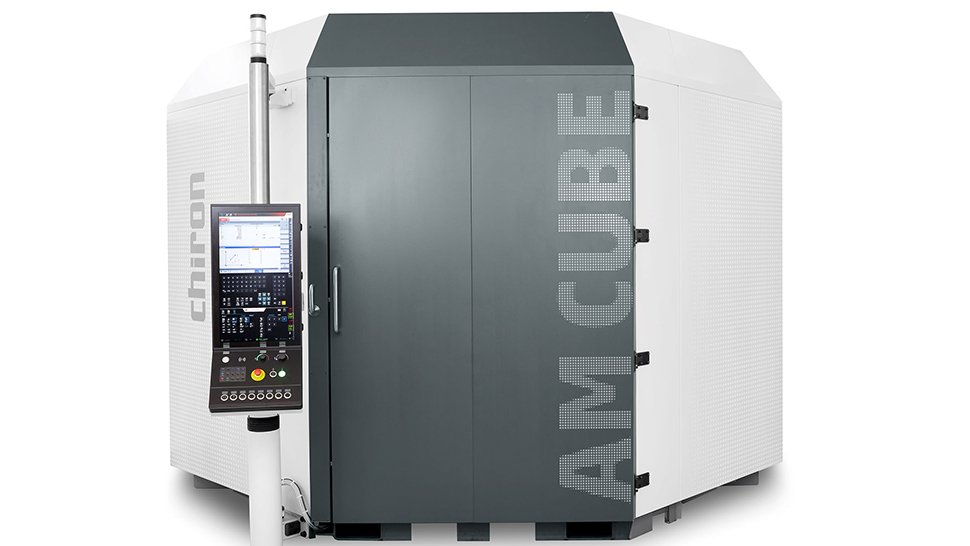
Fotos: Chiron
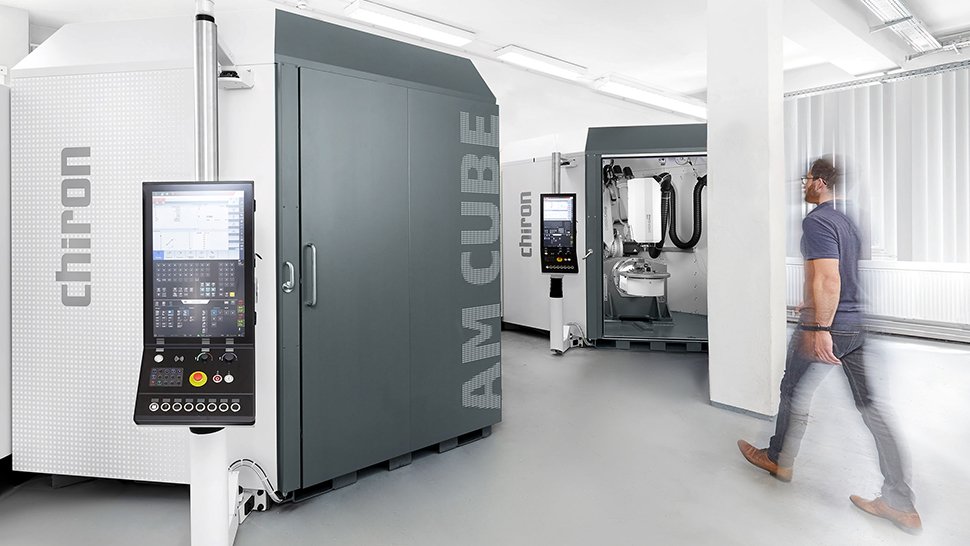
Fotos: Chiron
Wenn zusätzliche Funktionen integriert werden, dann ist die Kostenseite leichter zu befriedigen?
Boi: Es gibt eine Herausforderung, die wir mit unserem Produkt haben. Im Pulverbettverfahren sind wir im Design-Freiheitsgrad besser aufgestellt als beim klassischen Laser-Auftragsschweißen. Dieser Prozess ist schneller, aber grob. Die Bereitstellung von Kühlkanälen ist dann sehr eingeschränkt. Auch die Geometrien sind eingeschränkt. Da gehen wir eher gegen das klassische Gussteil an, das einzeln gefertigt wird. Im Sandguss können wir ein Halbzeug schneller herstellen, aber die Funktionsintegration ist untergeordnet.
Wo liegen die Chancen des Laser-Auftragsschweißens?
Boi: Ich schätze, dass wir die Geometrien besser als beim manuellen Auftragsschweißen darstellen können. Zudem hat die Anlage keine menschlichen Schwächen und braucht keine Pause. Wir können die Parameter, um das Ergebnis zu beurteilen, während des Prozesses kontinuierlich abfragen und verfolgen. So können wir erkennen, ob der Prozess in den gewünschten Toleranzfeldern gelaufen ist. Das gibt einen Vorteil in Bezug auf die Qualität der Schweißung. Zudem arbeiten wir insbesondere beim Reparaturschweißen mit geringeren Aufmaßen. Normalerweise wird ein Sicherheitsaufschlag berücksichtigt, um die Schwankungen der manuellen Bearbeitung auszugleichen. Das Entfernen des überschüssigen Materials ist hingegen bei geringerem Aufmaß deutlich leichter. Das lässt sich auch quantifizieren. Beim Formenbau hat man bei üblichen Reparaturen Aufmaße zwischen drei und sechs Millimetern. Mit der additiven Fertigung genügt ein Millimeter. Das wirkt sich auf die Kosten aus.
Gibt sich die Qualitätssicherung mit reiner Dokumentation zufrieden?
Boi: Wir haben zwei Punkte. Über die Regelung haben wir die Möglichkeit, die Ist-Temperatur im Schmelzbad zu verfolgen. Ein Beispiel. Die Schmelztemperatur ist fix, bei Wasser liegt sie um null Grad. In der Spanne bis zum Sieden habe ich flüssiges Wasser verfügbar. Beim Schmelzprozess habe ich eine ähnliche Situation. Der Schmelzpunkt ist definiert, und das Material fängt an zu verdampfen. Dazwischen habe ich bei Metall eine Spanne von mehreren hundert Grad. Von der Höhe der Temperatur hängt auch die Abkühlsituation ab. Wir haben eine Möglichkeit, dass wir die Temperatur während des Schmelzprozesses in der Schmelze messen können. Dafür wurde ein Pyrometer integriert. Dieses Messgerät nimmt die Temperatur auf, und damit regeln wir die Laserleistung nach. Dadurch können wir innerhalb der Toleranz bleiben. Das ist ein Vorteil, den man in den klassischen Prozessen nicht abbilden kann. Beim Schweißen nehmen wir auch kontinuierlich 30 Parameter während des Schweißens auf. Der Bediener hat die Möglichkeit, gewisse Parameter aufzunehmen und mit Toleranzfeldern wie Vorschubgeschwindigkeit zu belegen. Wenn es zur Überschreitung der Grenzen kommt, gibt es ein Signal. In der Analyse können die anderen Parameter in dieser Situation zur Betrachtung hinzugezogen werden.
Wird diese Funktion genutzt?
Boi: Es ist interessant. Am Anfang musste man die Leute quasi zwingen, dass sie dieses Werkzeug akzeptieren. Aber jetzt erkennen sie die Vorteile. So haben wir ein einfaches Mittel, um den Schweißprozess Stück für Stück ein bisschen besser zu verstehen. Das einfach zu bedienende Software-Tool hilft uns gewaltig. Zum Schluss kann das Ergebnis in einem Protokoll festgehalten werden. Das können wir bei den manuellen Arbeiten nicht.
Wie lange wird es noch dauern, bis der gesamte Prozess im Blick ist?
Boi: Das ist immer abhängig von den Nutzern. Wenn man will, bekommt man den Prozess relativ rasch in den Griff. Derzeit ist es leider so, dass man einen Zerspanungsprozess auf einem Bearbeitungszentrum hat und die Prozesse vergleicht. Das lässt sich in der additiven Fertigung nicht so einfach vergleichen.
Wie sieht es im Formenbau aus?
Boi: Die 3D-Fertigung auf der einen und der manuelle Prozess auf der anderen Seite. Wenn ich nur beide Prozesse vergleiche, dann ist der manuelle Prozess viel schneller. Man bedeckt die Stelle mit einer dicken Schweißnaht. Aber wenn das Thema Qualität ins Spiel kommt, kann ich es über die Standzeit beurteilen. Beim Thema Materialeinsatz handelt es sich um ein größeres Volumen mit teurem Material. Beim Stichwort Nachbearbeitung geht ein geringes Aufmaß mit schneller Bearbeitung einher, während ein hohes Aufmaß länger dauert und die Werkzeugabnutzung eine Rolle bei den Kosten spielt. Dadurch sieht man schon, bei der Einzelbetrachtung des reinen Auftragsschweißens verliert die additive Fertigung deutlich. Wenn man allerdings alle Schritte betrachtet, dann ergibt es unter dem Strich ein positives Bild für die additive Fertigung. Bei einem fairen Vergleich ist der 3D-Druck also wettbewerbsfähig.
Wie sieht es bei den Nachbearbeitungsprozessen aus?
Boi: Als wir vor drei Jahren starteten, haben wir uns die AM-Cell vorgenommen. Wir hatten drei Projekte, darunter eines, 3D-gedruckte Teile fertigzustellen. Gemeinsam mit zwei Industriepartnern haben wir einen Blick auf die Fertigung in fünf Jahren geworfen. Diesen Fertigungsablauf haben wir in eine automatisierte Anlage gegossen. Drucken, entpulvern, Druck messen, auf dem Bearbeitungszentrum bearbeiten, Trennen von der Planscheibe, Fertigbearbeitung, Qualitätssicherung und ausschleusen. Dabei haben wir festgestellt, dass die Nachbearbeitungsaufgaben von Bauteil zu Bauteil sehr unterschiedlich sind – mit oder ohne thermische Behandlung, mehr drehen oder mehr fräsen. Dafür eine universelle automatisierte Anlage zu entwickeln, war unmöglich. 3D-Druck ist heute eine Technologie, die bei Einzelteilen und Kleinserien ihre Vorteile hat. In der Großserie sind wir noch nicht. Insofern tut sich jeder Automatisierungsprozess schwer, eine Vielzahl von unterschiedlichen Bauteilen zu handhaben. In unserem Fall haben wir eine Bauteilfamilie, Schneidwerkzeug mit Fräsern, aber die Prozesse sind in der Breite noch nicht in der Stückzahl angekommen, dass sich eine automatisierte Nachbearbeitung lohnt.
Wie werden sich Markt und Technik Ihrer Einschätzung nach in den nächsten fünf Jahren entwickeln?
Boi: Ich bin unentschieden. Wenn das Binder Jetting in einfacherer Technologie funktioniert, dann wird das ein Sprung sein. Daran wird schon länger gearbeitet, aber es gibt kein industrietaugliches Ergebnis. Wenn es funktioniert, wird es in Serie gehen. Kleine Bauteile, rotationssymmetrische Bauteile. Bisher ist der Erfolg nicht sichtbar. In den jetzt eingesetzten 3D-gedruckten Techniken erwarte ich ein kontinuierliches Wachstum, weil sich Schritt für Schritt die Anwendungsfälle herauskristallisieren. Der Markt wächst. Im Bereich der akademischen Ausbildung ist das Thema ebenfalls erkannt worden. Dadurch kommt Nachwuchs in die Unternehmen. Das wird den Markteintritt für die Technologie vereinfachen. Die Produkte werden leistungsfähiger. Technologisch wird es außer dem Binder Jetting eher kleine Fortschritte geben. Neue Materialien werden entwickelt und validiert. Alle Zeichen stehen auf Wachstum, aber wir starten von ganz weit unten. Der Anteil von 3D-Druck zu klassisch gefertigten Teilen liegt eher bei 1 zu 1000. Das Marktvolumen der Werkzeugmaschinen liegt bei 70 Milliarden Euro, davon ein Drittel Zerspanung. Der Markt für 3D-Drucker beträgt eine Milliarde Euro. Der Taktzeitunterschied zwischen einem 3D-gedruckten und einem zerspanten Bauteil liegt etwa bei 20. Damit können lange nicht so viele Teile produziert werden. Das heißt, wir haben einen sehr geringen Anteil am Kuchen. Wir bedienen Sonderfälle, Einzelanforderungen, aber wir haben ein größeres Wachstum.
Was erhofft sich das AM-Team des Start-ups bei Chiron?
Boi: Wir haben ein Produkt am Start mit Verkaufsfreigabe für den AM-Cube. Die Feldtesterprobung ist abgeschlossen. Pulverdraht-Laser-Auftragsschweißen. Zweites Produkt zum Beschichten von Bremsscheiben ist in der Entwicklung – AM-Coating. Mit diesen beiden Produkten hoffe ich, dass ich mein Start-up signifikant vergrößern kann.
Kontakt
Axel Boi
Leiter Additive Manufacturing
Chiron Group
Kontakt
Christina Meßmer
Marketing
CHIRON Group SE
Tuttlingen
Tel. +49 7461 940 3712
E-Mail senden