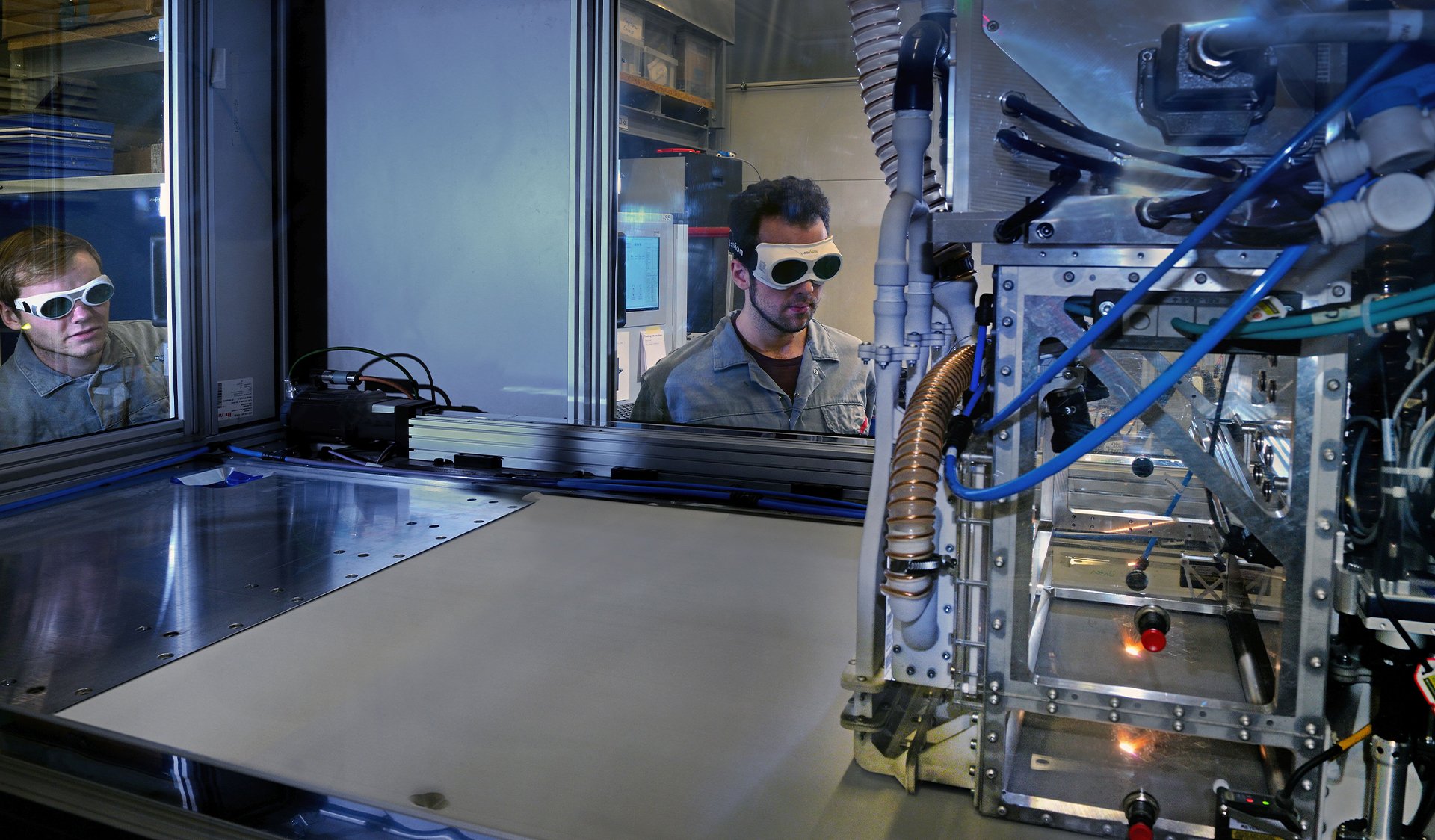
Titelthema
Ein Patent geht um die Welt
Das Jubiläum zum Basispatent Laser Powder Bed Fusion ist Anlass für einen Video-Clip. Vor 25 Jahren war die Gruppe wesentlich kleiner. Damals arbeitete lediglich ein Forscher des Fraunhofer ILT aktiv am Projekt. Im Jahr 1996 wurde das Patent zum metallischen 3D-Laser-Druck eingereicht. Ein guter Anlass für einen Rück- und Ausblick auf die Technologie. Heute zählt das Kompetenzfeld Laser Powder Bed Fusion (LPBF) am Fraunhofer ILT50 Mitarbeitende und Studierende.
Eine Drohne schwebt über dem Fraunhofer ILT und filmt die Welt. Die Mitarbeiterinnen und Mitarbeiter aus dem Bereich LPBF stehen zusammen und bilden die Ziffer 25.
Das LPBF-Verfahren bietet die Möglichkeit, komplexe Funktionsbauteile ressourceneffizient und wirtschaftlich herzustellen. Die Fertigungskosten hängen weniger von der Komplexität der Geometrie ab, sondern hauptsächlich vom Volumen des Bauteils. Das Besondere an der Idee damals war, auf anwendungsorientierte Werkstoffe wie Cobalt-Chrom-Legierungen für Dentalimplantate zu setzen und daran den Prozess anzupassen. Das LPBF-Verfahren findet heutzutage breite industrielle Anwendung beim Turbomaschinen- und Automobilbau, der Luft- und Raumfahrt sowie der Medizintechnik.
Wilhelm Meiners, Andres Gasser und Konrad Wissenbach, Erfinder des Verfahrens, sind zum Filmtermin erschienen. Sie berichten von den Anfängen: »Gestartet sind wir im Prinzip mit meiner halben Stelle«, erzählt Meiners lächelnd und schaut auf die allererste LPBF-Maschine des Fraunhofer ILT.
Konrad Wissenbach, damaliger Abteilungsleiter, erläutert: »Zunächst haben wir das Verfahren Direct Selective Laser Sintering (DSLS) getauft, was es aber nicht genau trifft. Später haben wir es Selective Laser Melting (SLM) genannt«. Er glaubte an das Verfahren und trieb zusammen mit Meiners und Gasser durch unermüdlichen Einsatz und wissenschaftliches Know-how die Technologie weiter voran.
Auf dem Transportwagen vor den Erfindern steht die erste, immer noch funktionstüchtige Maschine. Gasser erklärt: »Schicht um Schicht wird das Metallpulver mittels Rakel verteilt. In jeder Schicht verfährt der Laserstrahl entlang berechneter Bahnen. Das Metallpulver verschmilzt an definierten Stellen und das Werkstück nimmt Schicht um Schicht seine Form an«. Der Filmtermin geht seinem Ende entgegen und einige Anekdoten machen die Runde. Auch jene, von den ersten Messebesuchen mit dem damals brandneuen Verfahren. »Geradezu ausgelacht hat man uns damals. Was wollt ihr denn damit?« berichtet Gasser.
Im Jahr 2019 wird der globale Markt für additive Fertigung von Metallen einschließlich System-, Material- und Dienstleistungsumsatz auf zwei Milliarden Euro geschätzt. LPBF ist mit über 80 Prozent die dominierende Technologie auf dem Markt für die additive Fertigung mit Metallen.
Im Fokus des Fraunhofer ILT stehen gegenwärtig die Entwicklung von additiven Prozessen, innovativen Belichtungskonzepten und Maschinen sowie die Integration dieser Entwicklungen in industrielle Prozessketten. Die umfangreiche Anlagenausstattung besteht aus unterschiedlichen, kommerziellen Systemen und selbstentwickelten, hochflexiblen Laboranlagen. Gebündeltes Know-how, auch aus den Bereichen Laserstrahlquellen- und Optikentwicklung sowie Prozessbeobachtung, ermöglicht maßgeschneiderte Applikationen und Innovationen.
Verschiedene Filme laufen über den Monitor. Auch sie berichten von den Anfängen. Ein im 3D-Druck hergestelltes Hüft- und das erste Dentalimplantat werden gezeigt. Einer der ersten Use Cases lag damals in der Dentaltechnik, inzwischen ist das LPBF-Verfahren für die Fertigung der Implantate Stand der Technik.
Durch den Aufbauprozess des LPBF-Verfahrens in Schichten wird eine dreidimensionale Fertigungsaufgabe auf zwei Dimensionen reduziert. Dadurch bietet das Verfahren eine Reihe von systematischen Vorteilen im Vergleich zu konventionellen Fertigungstechniken wie dem Urformen oder der Zerspanung. Beispielweise sind komplexe Kühlkanäle zur gezielten Temperierung von Werkzeugen oder integrierte Gitterstrukturen für Leichtbauanwendungen möglich.
Yves Hagedorn, CEO der Aconity3D GmbH, Hersteller von Werkzeugmaschinen für das laserbasierte 3D-Drucken von Metallen, ist ebenfalls zum Drehtermin erschienen. Er berichtet von seinem Startup: »Ausgründen birgt immer ein Risiko. Selbst, wenn der Markt identifiziert ist und der Start gelingt. Für uns war die Unterstützung des Fraunhofer ILT sehr hilfreich und beruhigend.«
Mittels LPBF-Technologie lassen sich Prototypen in Kleinserien mit serienidentischen Werkstoffeigenschaften in kürzester Zeit herstellen. Systematischer Vorteil ist die Verkürzung von Entwicklungszeiten. Es können viele Iterationen mit geringerem Aufwand durchgeführt werden. Daraus resultiert eine verkürzte Zeit bis zur Markteinführung eines neuen Produktes.
Anders Such, Head of Additive Manufacturing bei MAN Energy Solutions, ist ebenfalls am Drehort erschienen. Er zeigt das Zusammenfassen von 13 konventionell hergestellten Bauteilen zu einem monolithisch gefertigten AM-Bauteil. Er führt die Vorteile der additiven Serienfertigung des Leitschaufel-Clusters einer Gasturbine an: »Bei der Entwicklung des Bauteils für die Serienfertigung trug besonders das Prozess-Know-how des Fraunhofer ILT zum Erfolg des Projektes bei. Es konnten wesentliche Herausforderungen wie der prozessinduzierte Verzug der Schaufelkanten, die oberflächennahe Randporosität und das Identifizieren eines geeigneten Verfahrens zur werkzeuggebundenen Nachbearbeitung der Strömungsflächen bewältigt werden.«
Zur Etablierung des LPBF als industrielles Fertigungsverfahren und zur Nutzung der dargestellten verfahrensspezifischen Vorteile in der Produktion ist eine ganzheitliche Betrachtung der gesamten Prozesskette erforderlich: Vom Bauteildesign über die Prozessführung und Anlagentechnik bis hin zur Endbearbeitung.
Die ganzheitliche Betrachtung ist auch Grundlage für ein wichtiges Zukunftsthema des Fraunhofer ILT. Hinsichtlich einer kreislauforientierten Produktion und zum Thema »ökologischer Fußabdruck« soll der LPBF-Prozess beispielgebend werden; der Fokus liegt auf dem »Life Cycle Assessment«. Eine transparente Bewertung ökologisch und nachhaltig hergestellter Produkte hilft der Industrie undkleinen sowie mittleren Unternehmen, Verantwortung für Mensch und Umwelt zu übernehmen und sich mit einem Wettbewerbsvorteil am Markt zu positionieren.
In einem weiteren Projekt werden derzeit »Smart Parts« mittels LPBF gefertigt. Dazu werden elektronische Komponenten und Sensoren während des LPBF-Verfahrens direkt ins Bauteil integriert. Der Aufbau in Schichten wird genutzt, um Sensoren innerhalb des Bauteils zu platzieren. Dadurch wird die Überwachung des Bauteilzustands und der Bauteilperformance im Einsatz und sogar die Vorhersage möglicher Schäden mittels KI ermöglicht, was Ausfälle verhindert und gleichzeitig einen präventiven Austausch kostspieliger Bauteile überflüssig macht.
20 Dissertationen und 250 Arbeiten
Das Leitungsteam im LPBF-Kompetenzfeld sortiert Dissertationen und Abschlussarbeiten auf dem Schreibtisch von Professor Constantin Häfner, Leiter des Fraunhofer ILT: »Wichtiges Element in der Arbeit unseres Instituts ist der Aufbau von Expertise. Deutlich sichtbar wird das über den Zeitraum unserer Arbeit am LPBF-Verfahren. Heute, nach 25 Jahren, forschen, arbeiten und beraten 50 Mitarbeitende mit der und für die Industrie. Ein sehr gutes Beispiel für die Realisierung unserer Mission als Fraunhofer ILT.« Dabei verweist Häfner auf die enge Zusammenarbeit mit dem Forschungscampus Digital Photonic Production (DPP), nur einen Steinwurf weit von seinem Institut entfernt.
Der Kameramann filmt Abbildungen in einer Abschlussarbeit. Sie zeigt das neue Maschinenkonzept mit dem 5-Laser-Scanner-Kopf. Ein aktuelles Stück Hightech aus dem Fraunhofer ILT. Anders als bei herkömmlichen Verfahren wird der Prozesskopf mit lokaler Schutzgasströmung über das Pulverbett bewegt. Dies ermöglicht eine Skalierung von Aufbaurate und Bauteilgröße bis zum Faktor Zehn. Die LPBF-Anlage bietet einen sehr großen, effektiv nutzbaren Bauraum von 1000 x 800 x 500 Millimetern. Eine wirtschaftliche Bearbeitung von ganzen Turbinen und Aerospace-Bauteilen rückt in greifbare Nähe.
Zum Ende des Drehtages schwebt die Kameradrohne nochmals über den Vorplatz des Fraunhofer ILT. Jetzt haben die Mitarbeiterinnen und Mitarbeiter eine andere Formation eingenommen. In Lettern steht zu lesen: LPBF.
Kontakt
Jasmin Saewe
Leiterin des Kompetenzfeldes Laser Powder Bed Fusion
Fraunhofer-Institut für Lasertechnik (ILT)
Aachen
Tel. +49 241 8906 135
E-Mail senden
Johannes Junggeburth
Kommunikation
Fraunhofer-Institut für Lasertechnik (ILT)
Aachen
Tel. +49 241 8906 171
E-Mail senden