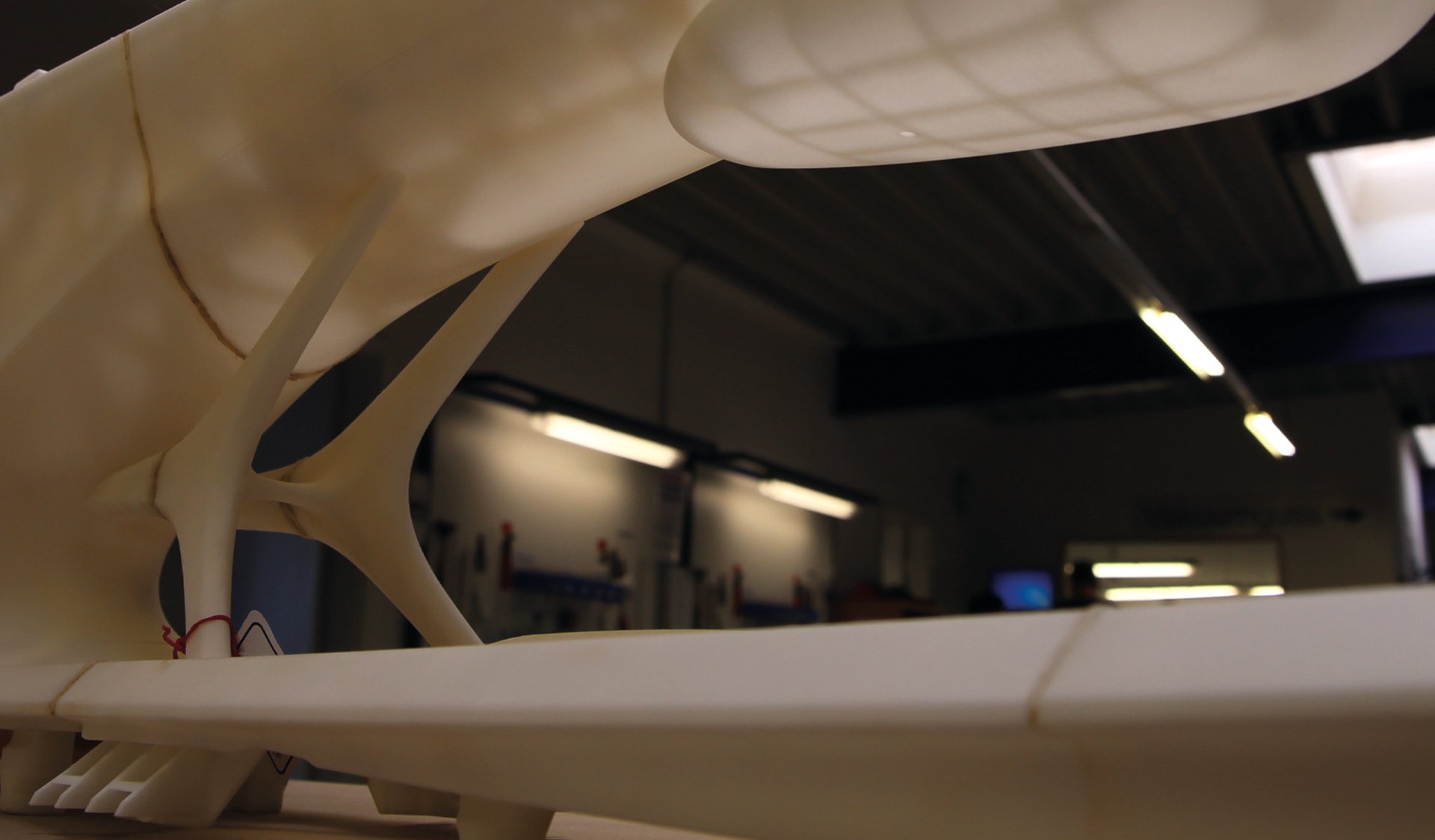
Titelthema
Mittelkonsole für ein Konzeptfahrzeug
„Nichts ist unmöglich.“ Dieses Motto von Toyota steht wie kaum ein anderes für den permanenten Fortschrittsdrang, mit dem der japanische Automobilhersteller Fahrzeuge für eine bessere Zukunft entwickelt. Das gilt besonders für das futuristisch designte Konzeptfahrzeug LQ. Es fährt autonom, 100 Prozent elektrisch und ist mit einer künstlichen Intelligenz, genannt Yui, auf Japans Straßen unterwegs. Für die Produktion einzelner Fahrzeugkomponenten im LQ setzt Toyota auf moderne Fertigungsmethoden und -verfahren. Bei der Entwicklung und Herstellung der Mittelkonsole vertrauten die Ingenieure auf die Möglichkeiten der additiven Fertigung und die Partnerschaft mit FIT. In diesem Projekt standen außergewöhnliches Design, höchste Sicherheit, beste Qualität und Leichtbau im Mittelpunkt.
LQ-Entwicklungsleiter Daisuke Ido sagt dazu: „In der Vergangenheit resultierte die Liebe zu Autos insbesondere aus der Möglichkeit, ferne Länder zu erkunden und Abenteuer zu erleben. Mit fortschrittlichen Technologien reagieren wir auf den Lebensstil unserer Kunden. Wir sind stolz darauf, mit dem LQ ein Fahrzeug offerieren zu können, das ein personalisiertes Erlebnis bietet, die individuellen Mobilitätsbedürfnisse jedes Fahrers erfüllt und eine noch stärkere Verbindung zwischen Auto und Fahrer herstellt.“
In Zusammenarbeit mit dem Designteam in Japan wurde die gesamte Geometrie der Mittelkonsole im Rahmen eines ADM-E-Projekts von FIT so gestaltet, dass die Konsole zwischen den Vordersitzen nahezu frei im Innenraum schwebt und damit den eleganten Eindruck des gesamten Interieurs perfekt unterstützt.
Ihr geringes Gewicht verdankt die Konsole der hohlen Innenkonstruktion und ihre Stabilität einem Netz innenliegender Streben, die für eine extrem robuste Struktur sorgen. Dadurch hielt die Konsole den strengen Konstruktionsrichtlinien von Toyota genauso stand, wie den notwendigen Crashtests.Im Hinblick auf Sicherheit unterliegen Fahrzeugteile im Innenraum strengen Vorgaben, auch in Bezug auf den Brandschutz. Um diese Anforderungen zu erfüllen, wurden im Rahmen eines separaten Entwicklungsprojekts (ADM-D) diverse Materialtests in der FIT-Fertigung durchgeführt. Die Eignung des schwer entflammbaren Kunststoffs PA 2241 FR als optimales Material für die Konsole wurde dadurch erfolgreich nachgewiesen. Auf die finale Designfreigabe und die Materialqualifizierung folgte die additive Serienfertigung (ADM-V). Insgesamt wurden 32 Mittelkonsolen mittels Selektivem Lasersintern (SLS beziehungsweise PBF-LB/P) hergestellt.
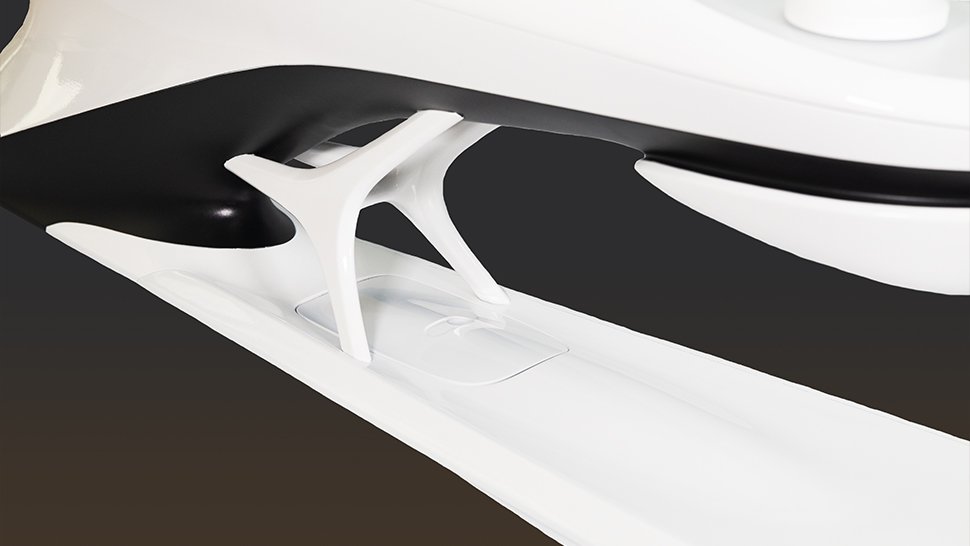
Fotos: FIT
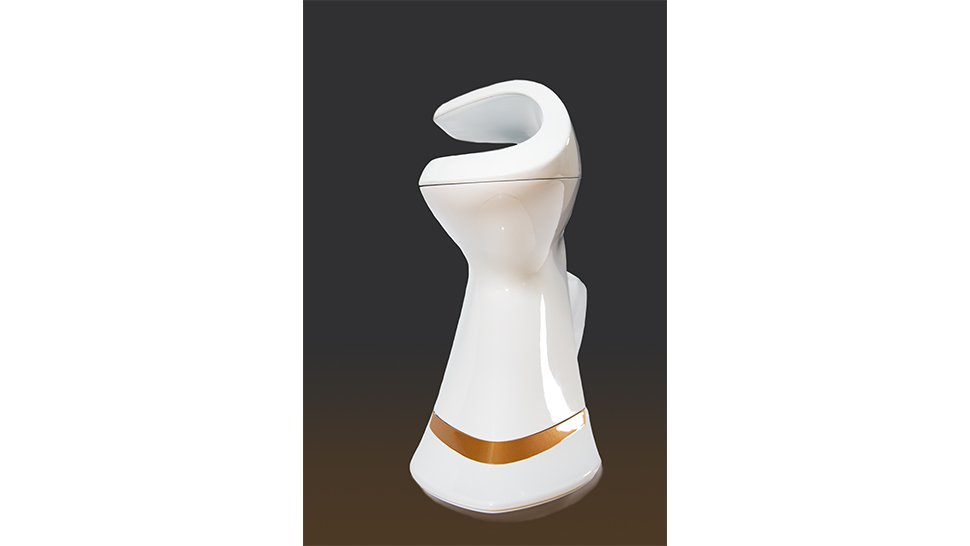
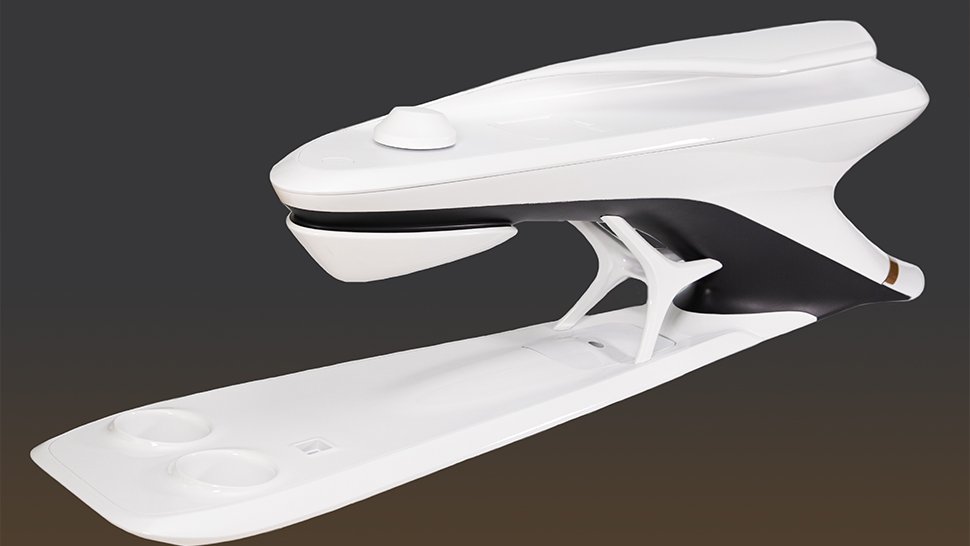
Herausragende Eigenschaften
Toyota profitiert in der Zusammenarbeit mit FIT von den Vorteilen der additiven Fertigung sowohl bei metallischen Anwendungen als auch bei Bauteilen aus Kunststoff. Durch die Neuentwicklung des Designs und die additive Serienfertigung der Mittelkonsole wurde Folgendes erreicht:
- geringes Bauteilgewicht, denn die Konsole wiegt lediglich 7,5 Kilogramm
- präzise Herstellung der Konsole, so dass sie sich in Japan problemlos im Innenraum verbauen ließ
- geringe Bauteilkomplexität trotz komplexer Bauteilgeometrie, das heißt, die Konsole wurde aus wenigen Teilen gefertigt und zusammengesetzt
- ein Bauteildesign, das sich nur dank additiver Fertigung zu vertretbaren Kosten herstellen lässt
Toyota entschied sich bei diesem Projekt, das sich insgesamt über zehn Wochen erstreckte, bewusst für das umfangreiche Leistungsangebot der FIT, denn Designentwicklung, Materialqualifikation und additive Serienfertigung aus einer Hand zu erhalten, reduzierte die Komplexität im Projekt und die Projektdauer erheblich. Die Entscheidung für die Nutzung der additiven Fertigung zur Herstellung der Konsole lag dabei nahe. Mit FIT als Partner verfolgte Toyota in diesem Projekt das Ziel, eine Mittelkonsole zu entwickeln und zu produzieren, die
- sehr leicht ist, um die Reichweite des Fahrzeuges nicht einzuschränken,
- sehr sicher ist, denn der LQ ist ein Konzeptfahrzeug mit Straßenzulassung,
- außergewöhnlich ist und durch seine Optik begeistert.
Ausgangspunkt war der erste Designentwurf der Konsole, der aufgrund seiner relativ massigen Geometrie noch zu schwer und deshalb in der Fertigung zu teuer war. An dieser Stelle übernahmen die Designexperten von FIT die weitere Entwicklung.
Design ist entscheidend
Auf Basis der Konstruktionsrichtlinie von Toyota wurden im Rahmen eines Entwicklungsprojekts mit modernsten Softwaretools verschiedene Varianten der Konsole kreiert. Am Ende fiel die Wahl auf eine Geometrie, aus deren stabilem Fundament eine nahezu frei schwebende Auflagefläche ragt, die nur von zwei filigranen Stützen getragen wird.
Das besonders Spannende an der Mittelkonsole ist ihr Innenleben, denn es handelt sich um eine sehr leichte, hohle Konstruktion. Um die erforderliche Stabilität zu gewährleisten, entwickelten die Konstruktionsprofis der FIT ein Netz aus Verstrebungen, deren Profil exakt auf die Belastungen der Konsole abgestimmt wurde. Dadurch wurde sichergestellt, dass die Mittelkonsole lediglich 7,0 Kilogramm schwer, gleichzeitig jedoch robust genug war, um die erforderlichen Sicherheitstests für die Straßenzulassung zu bestehen.
In dem Designprojekt wurde gleichzeitig die Fertigungsstrategie für den 3D-Druck definiert. Qualität und Fertigungskosten standen im Vordergrund. Aufgrund der Größe der Konsole war es nicht möglich, das Bauteil in einem Stück zu fertigen. Daher wurde die Konsole in acht Einzelteile zerlegt, die sich zusammen perfekt in einem Baujob fertigen ließen.
Damit die Brandschutzbestimmungen von Komponenten im Innenraum von Fahrzeugen erfüllt waren, stand vor der Fertigung eine Materialselektion. Im Rahmen eines Projekts wurden verschiedene Materialalternativen im Hinblick auf ihre Eignung analysiert und getestet. Dabei zeigte sich, dass PA 2241 FR das passende Material für die Herstellung der Konsole ist.
Additive Serienfertigung
Mit diesem flammhemmenden Kunststoff wurden insgesamt 32 Mittelkonsolen hergestellt, von denen 20 in Fahrzeuge verbaut und zwölf für Testzwecke bei Toyota verwendet wurden. Als Herstellverfahren für die Serienfertigung kam Selektives Lasersintern (SLS bzw. PBF-LB/P) zum Einsatz. Um die Qualität des Fertigungsprozesses zu kontrollieren, wurden pro Mittelkonsole entsprechende Prüfkörper mitgebaut, die mittels spezieller Clips in Japan in das jeweilige Fahrzeug eingebaut wurden.
Um das zu gewährleisten, kamen speziell von FIT konstruierte und mittels CNC-Fräsen gefertigte Lehren aus Oriol zum Einsatz. Ihre exakten Abmessungen wurden mittels taktiler 3D-Koordinatenmessung sichergestellt. Mit diesem Werkzeug konnte zuverlässig geprüft werden, ob alle Teile richtig dimensioniert waren und perfekt zusammenpassten. Für den finalen Zusammenbau wurden die Einzelteile verschweißt. Die Nahtstellen wurden präzise verschliffen, so dass eine perfekt glatte Oberfläche für den bei Toyota stattfindenden Lackiervorgang erzielt wurde.
In der abschließenden Qualitätssicherung wurde jede Konsole nach genauen Vorgaben mittels GOM-Scanner optisch gescannt. Die Ergebnisse wurden in einen detaillierten Prüfbericht zusammengefasst. Außerdem wurde der Einbau der elektronischen Komponenten (Touchpad, Knöpfe, Schalter) simuliert.
Dafür wurden originalgetreue Dummies mittels SLA aus Accura HPC hergestellt. Ihre Maßhaltigkeit wurde wiederum durch taktile 3D-Koordinatenmessung kontrolliert. Somit konnte sichergestellt werden, dass sich die Komponenten bei der Endmontage perfekt einpassen und die entsprechenden Spaltmaße konsequent eingehalten werden.
Kontakt
Achim Chrupala
Branchenspezialist für die Konsumgüter- und Automobilindustrie
FIT AG
Lupburg
Tel. +49 9492 9429 882
E-Mail senden