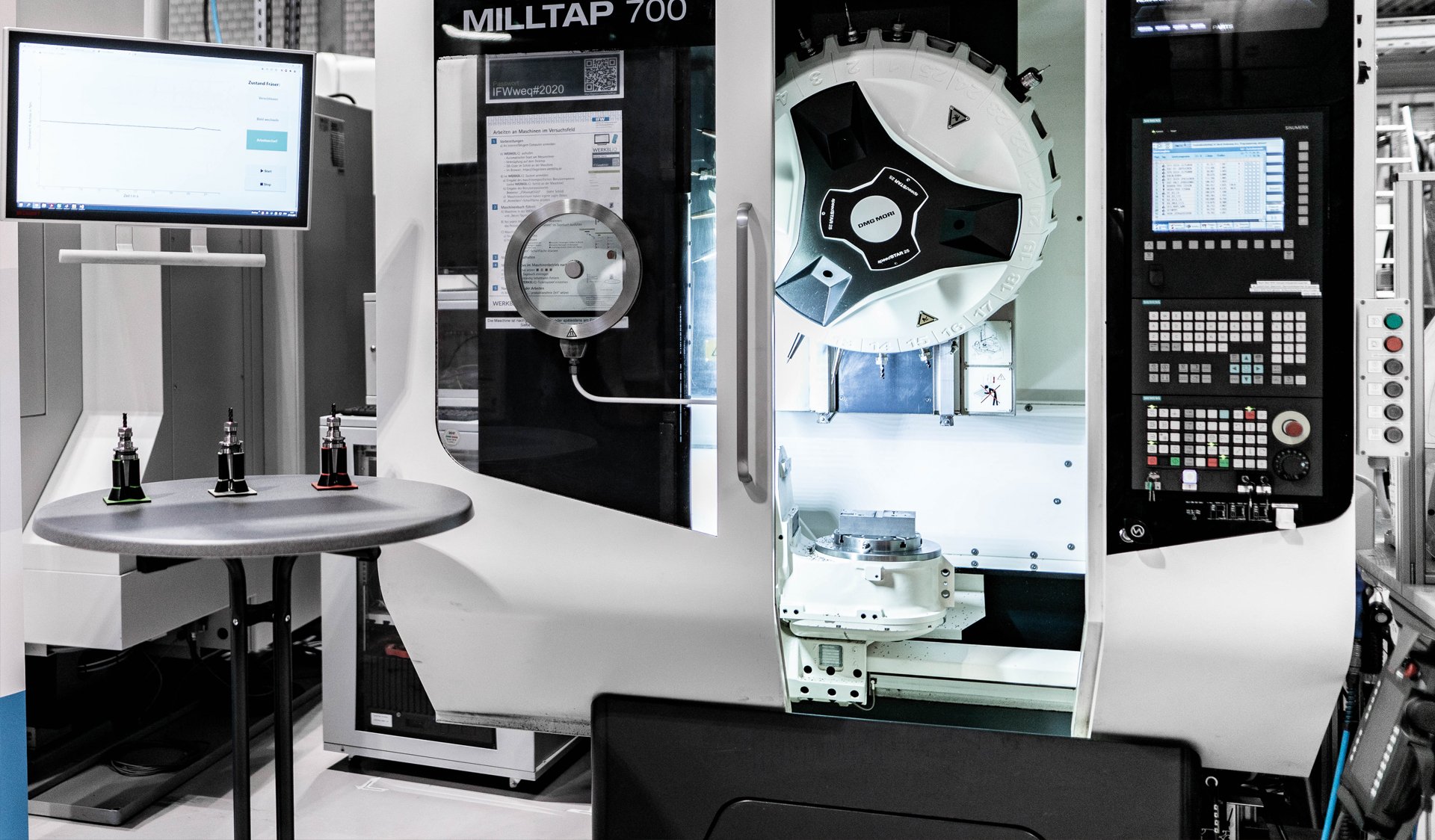
Forschung
Neuronale Netze überwachen den Verschleiß
Um trotz schwankender Standzeiten jedes Werkzeug bis zu seiner Einsatzgrenze nutzen zu können, wird der Verschleiß der Werkzeuge überwacht. Bisher ist es allerdings erforderlich, eine solche Überwachung an der überwachten Maschine selbst anzulernen. Durch eine maschinenübergreifende Nutzung von Prozessdaten kann eine solche Anlernphase entfallen. Das Institut für Fertigungstechnik und Werkzeugmaschinen (IFW) der Leibniz Universität Hannover hat dafür im Rahmen des Projektes „IIP-Ecosphere“ einen Demonstrator aufgebaut. Dabei wird die Verschleißmarkenbreite beim Fräsen durch die maschinenübergreifende Nutzung von Prozessdaten mithilfe tiefer neuronaler Netze überwacht.
Überschreiten Werkzeuge durch Verschleiß ihre Einsatzgrenze, werden Werkstückqualität und Prozesssicherheit beeinträchtigt. Um Werkzeuge rechtzeitig auszuwechseln, wird häufig ihre Einsatzdauer als Kriterium für einen Werkzeugwechsel herangezogen. Diese kann allerdings um mehr als 100 Prozent schwanken.
Aufgrund dieser Schwankungen wird in der Praxis eine sichere Obergrenze für die Standzeit festgelegt. Dadurch werden Werkzeuge vor dem Erreichen ihrer Einsatzgrenze und damit zu früh ausgewechselt. Ein erheblicher Teil der Werkzeuglebensdauer wird dadurch verschwendet.
Um präziser abzuschätzen, wann die Einsatzgrenze erreicht ist, kann der Freiflächenverschleiß eines Werkzeugs überwacht werden. Werkzeuge werden dadurch im Mittel länger genutzt, was Rüstzeiten und Werkzeugkosten reduziert.
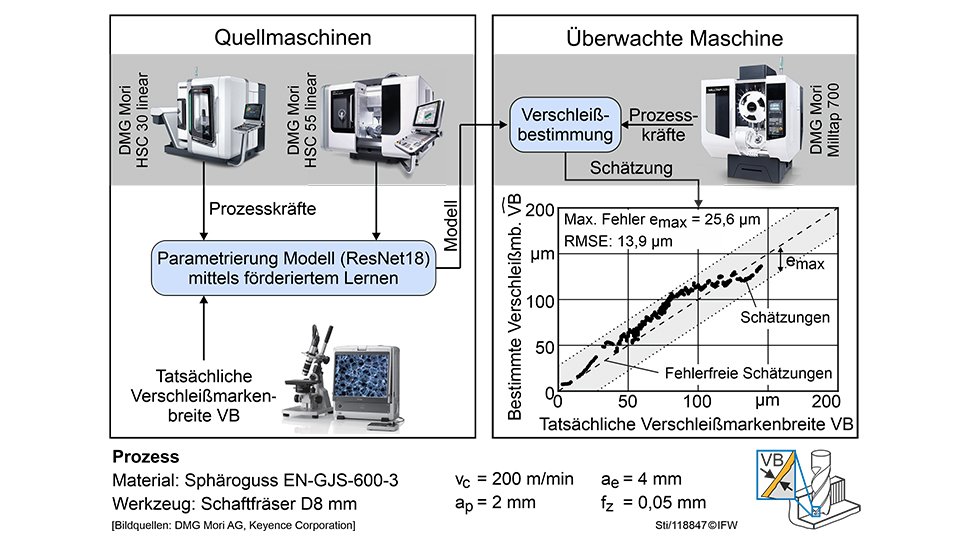
Überwachung eines Fräsers mit Prozessdaten anderer Maschinen: Im Bild (rechts unten) ist die bestimmte Verschleißmarkenbreite über die Nutzungsdauer eines Werkzeugs dargestellt. Die Diagonale markiert die fehlerfreie Bestimmung. Quelle: IFW
Eine solche Schätzung basiert häufig auf Prozesssignalen, die während der Zerspanung aufgezeichnet werden. Dabei erfolgt die Auswertung über komplexe Methoden, etwa tiefe neuronale Netze, die hohe Datenmengen für die Parametrierung erfordern. Die benötigten Datenmengen können bisher zumeist nur aus Serienprozessen gewonnen werden. Die so erzeugten Modelle sind hochspezialisiert und gelten zumeist als nicht übertragbar auf andere Werkzeuge, Werkstückwerkstoffe oder Maschinen.
In der Praxis ist deshalb für jede neue Anwendung eine lange Anlernphase erforderlich, in der keine Überwachung stattfindet. Als Teil des durch das Bundesministerium für Wirtschaft und Klimaschutz geförderten Projekts „IIP-Ecosphere“ erforscht das IFW die Überwachung von Prozessen mit Daten, die zuvor an anderen Maschinen erhoben wurden. Dafür werden Modelle für die Überwachung zwischen Maschinen übertragen.
Dadurch wird die Anlernphase an der überwachten Maschine erheblich verkürzt oder sie entfällt. Die Überwachung kleinerer Lose wird potenziell deutlich wirtschaftlicher.
Versuchsanordnung
Die Ansätze zur maschinenübergreifenden Nutzung von Prozesswissen für die Überwachung werden an einem Demonstrator aus drei Werkzeugmaschinen entwickelt. Für alle Maschinen wurden Werkstücke aus dem gleichen Werkstoff, gleiche Werkzeuge (VHM-Schaftfräser) und gleiche NC-Anweisungen genutzt.
An zwei Maschinen, den Quellmaschinen, sind aufgezeichnete Prozesssignale und der in regelmäßigen Abständen gemessene Verschleiß bekannt (Verschleißmarkenbreite VB). An den Quellmaschinen wurden insgesamt sechs neue Fräser durch Schulterfräsen ohne Kühlschmierstoff vollständig verschlissen (Einsatzgrenze bei 150 Mikrometern angenommen).
Mit den dabei aufgezeichneten 4652 multivariaten Prozesssignalverläufen wurde ein tiefes neuronales Netz (ResNet18) parametriert. Eingangsgröße des Modells sind die Verläufe der Prozesskräfte als Zeit-Frequenz-Darstellung und Ausgangsgröße ist die Verschleißmarkenbreite VB in Mikrometern.
Die Parametrierung des Modells erfolgte mithilfe des föderierten Lernens. Dabei werten alle Maschinen ihre Prozessdaten lokal aus, wodurch Daten nicht geteilt werden müssen. Lediglich Aktualisierungen der Parameter zur Modelloptimierung werden an andere Maschinen weitergegeben.
An der dritten Maschine wird das Modell anschließend genutzt, um die Verschleißmarkenbreite VB auf Basis der Prozesskräfte zu bestimmen. Eine Anlernphase an der überwachten Maschine gibt es nicht.
Übergreifendes Prozesswissen
Im Versuch wurde die Verschleißmarkenbreite über die Nutzungsdauer des Werkzeugs bestimmt. Der maximale Fehler emax liegt bei 25,6 Mikrometern (31 Prozent, bezogen auf den tatsächlichen Verschleiß bei VB = 80 Mikrometern). Oberhalb von 100 Mikrometern befindet sich der Bereich, in dem eine Verschleißbestimmung aufgrund des nahenden Standzeitendes besonders relevant ist. Dort liegt der Fehler sogar bei weniger als 13 Mikrometern (13 Prozent, bezogen auf VB = 100 Mikrometer).
Der beschriebene Demonstrator aus drei Werkzeugmaschinen zeigt, dass es möglich ist, Prozesswissen für die Überwachung von Werkzeugverschleiß beim Fräsen maschinenübergreifend zu nutzen. Die Anlernphase an der überwachten Maschine entfällt.
Als Erweiterung für das System ist die Prognose der Restlebensdauer von Werkzeugen geplant. Weiter zielt die zukünftige Entwicklung darauf ab, bei der Verschleißbestimmung gänzlich auf externe Sensorik zu verzichten, um eine Verschleißbewertung auch unter industriellen Bedingungen zu erreichen. Unternehmen, die sich für die Technik interessieren, sind eingeladen das IFW zu kontaktieren.
Kontakt
Prof. Dr.-Ing. Berend Denkena, geb. 1959, ist Leiter des Instituts für Fertigungstechnik und Werkzeugmaschinen (IFW) der Leibniz Universität Hannover. Dr.-Ing. Heinrich Klemme, geb. 1987, leitet am IFW den Bereich Maschinen und Steuerungen.
Tobias Stiehl
Wissenschaftlicher Mitarbeiter
Maschinen und Überwachung
Institut für Fertigungstechnik und Werkzeugmaschinen (IFW), Leibniz Universität Hannover
Produktionstechnisches Zentrum Hannover (PZH)
Garbsen
Tel. +49 511-762-18003
E-Mail senden