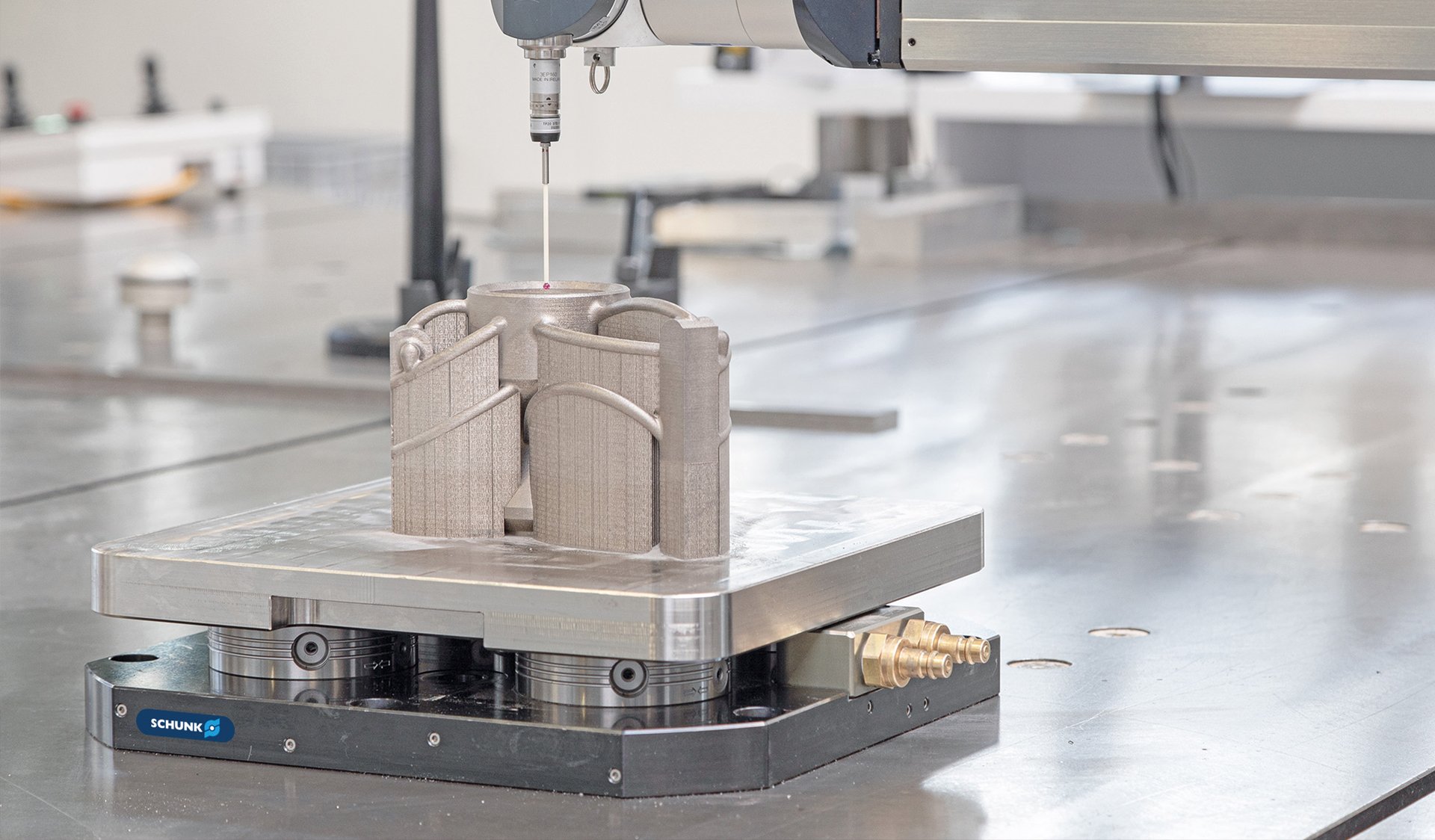
Titelthema
Spannt zuverlässig unter widrigen Bedingungen
Mit Begeisterung setzt Neher, der Hersteller von PKD-Sonderwerkzeugen, das Spannsystem VERO-S NSE_HT mini 88-20 von Schunk in der additiven Fertigung von Metallwerkzeugen ein. Denn es bietet absolute Zuverlässigkeit, hohe Flexibilität und kurze Rüstzeiten. Das vollständig abgedichtete Spannmodul verträgt Hitze, Staub und Tauchbäder. Es eignet sich deshalb für besonders anspruchsvolle Anwendungen – auch im Pulverbett-3D-Druck (SLM). Dank des speziellen Dichtkonzepts bleibt die Funktionalität des Moduls vollkommen sichergestellt.
An vielen Stellen der Produktion bei Neher sind Schunk-Module verbaut. Für die Fertigung kundenspezifischer Sonderwerkzeuge für die Automotive-Branche – etwa Getriebe- und Lenkungsgehäuse, Motorblöcke und Zylinderköpfe – hat das Unternehmen in Ostrach-Einhart (Landkreis Sigmaringen) diverse Werkzeughalter, Spannbacken, Drehfutter und Schraubstöcke im Einsatz.
Sowohl für die Werkzeugspannung als auch die Werkstückspannung benötigt Neher als Top-Performer zuverlässige Produktionskomponenten, um die hohen Kundenanforderungen zu erfüllen. „Wir brauchen in jedem Fall Top-Qualität“, sagt Tobias Niess, Entwickler bei Neher. Erst recht, wenn es um die besonders anspruchsvolle Teileproduktion geht, etwa die additive Fertigung hochspezifischer Werkzeuge aus Metall.
Dann rückt das Nullpunktspannsystem VERO-S NSE-HT mini 88-20 in den Fokus. Mit ihm und seiner bemerkenswerten Funktionalität ist den Entwicklern bei Schunk ein Coup für die moderne Produktion gelungen.
Dem Spannsystem für den Einsatz in Hochtemperaturanwendungen mit dem Typenmerkmal „HT“ – High Temperature bis 200 Gradn Celsius – können feinste Stäube, abrasive Materialien und sogar dauerhafte Tauchbäder nichts anhaben. Es besteht Herausforderungen, die weit entfernt davon sind, was Spannsysteme in herkömmlichen, konventionellen Zerspanprozessen aushalten müssen. „Wir können und wollen uns dieses Nullpunktspannsystem für unsere Produktionsabläufe gar nicht mehr wegdenken“, betont Niess.
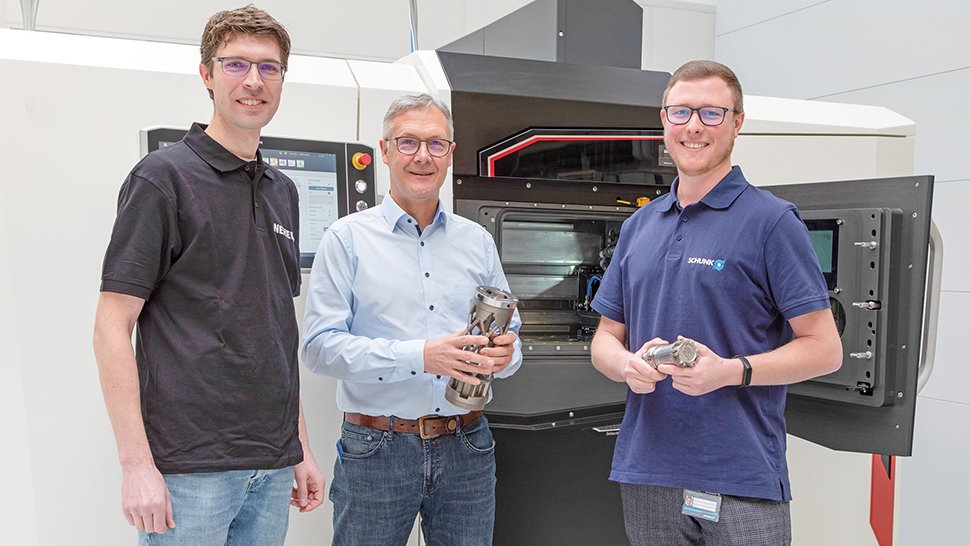
Tobias Niess, Entwickler bei Neher in Ostrach, mit Rolf-Peter Göser, Technische Beratung und Verkauf Spanntechnik bei Schunk, sowie Benjamin Hirz, Entwicklung Spanntechnik bei Schunk im Fachaustausch vor dem 3D-Metalldrucker (von links). Fotos: Schunk
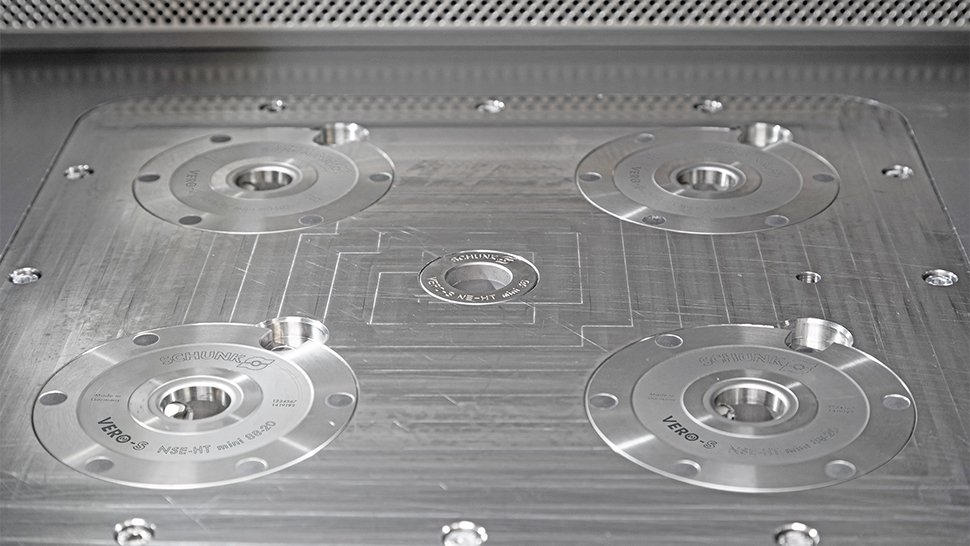
Einbausituation des Nullpunktspannsystems im 3D-Metalldrucker.
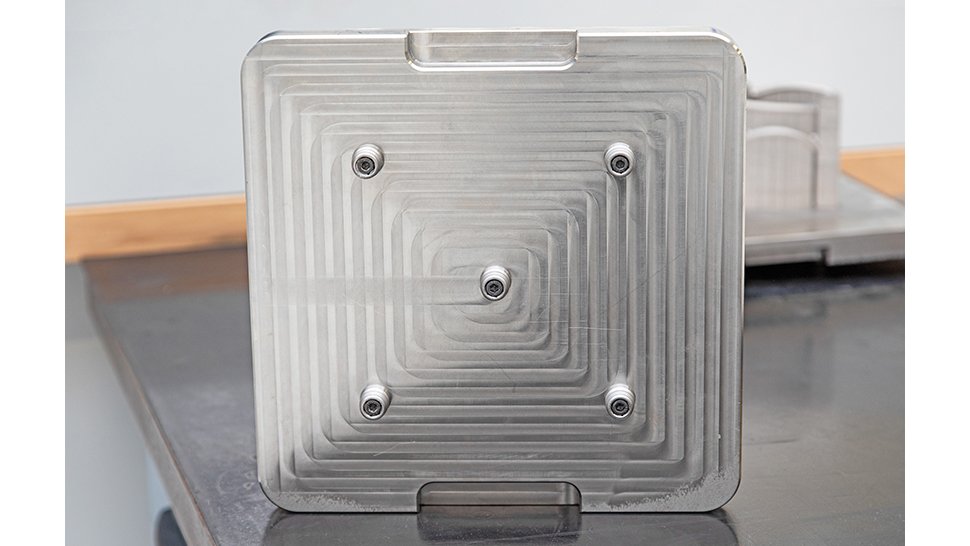
Die Bauplatte ist die Basis für das Produkt aus dem Laserschmelzprozess.
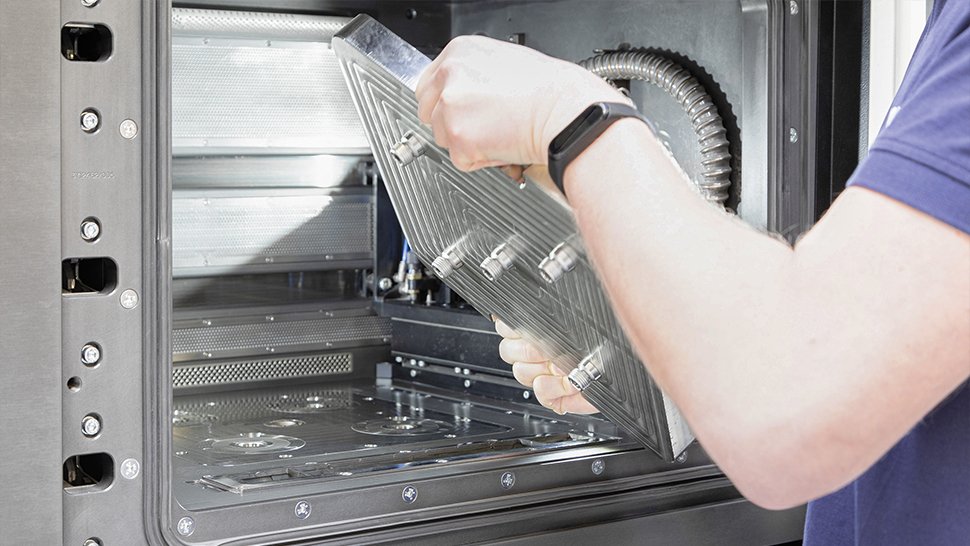
Einbringen der Bauplatte auf das Nullpunktspannsystem auf dem Maschinentisch – vier Nullpunktspannmodule, in der Mitte der thermische Nullpunkt.
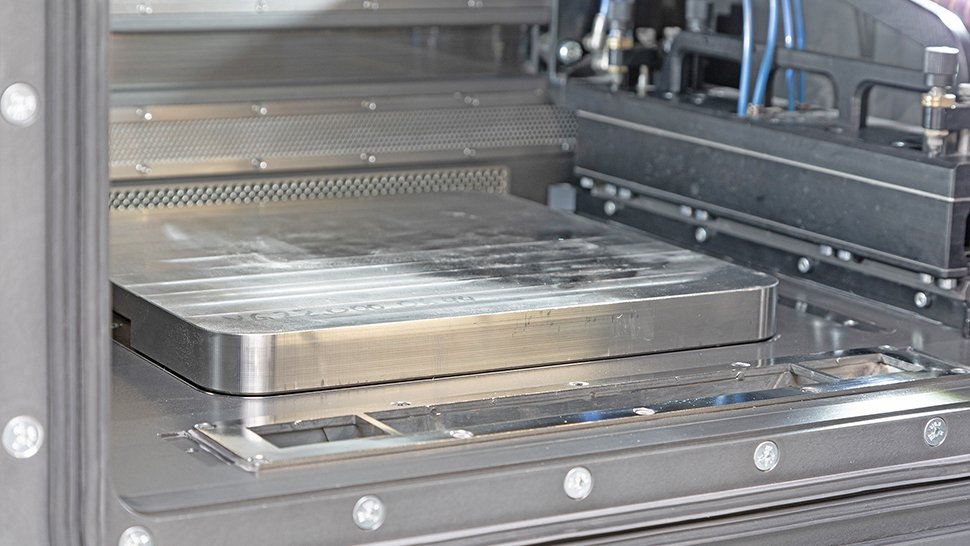
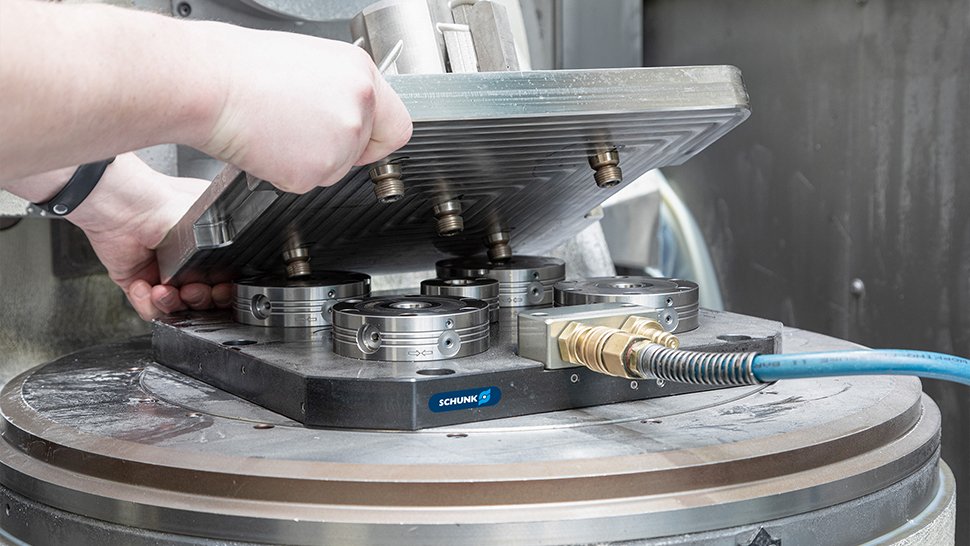
Vorbereitung der weiteren Werkstückbearbeitung auf der Fräsmaschine – auf einer Spannstation mit VERO-S NSE mini 90-25 Nullpunktspannmodulen.
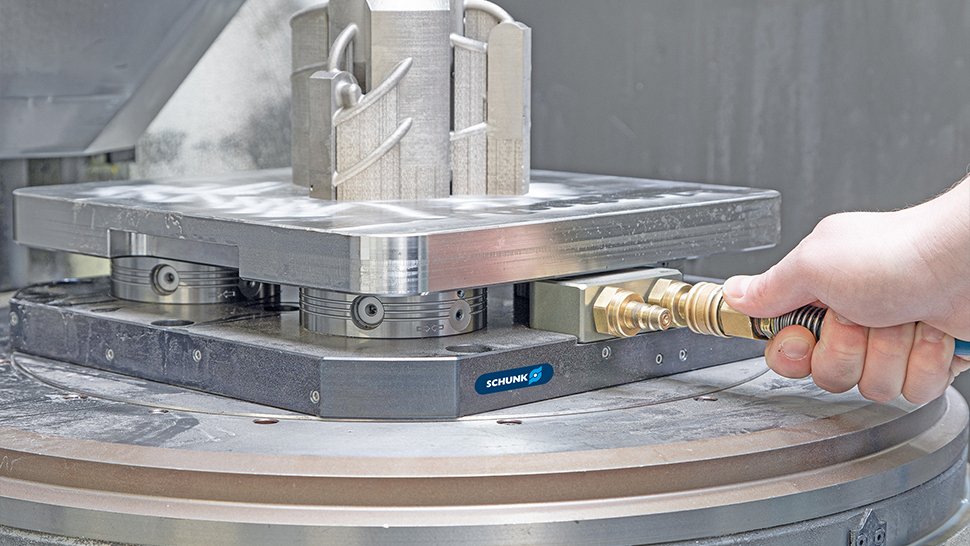
Durch einen Druckluftimpuls am Turbo-Anschluss wird die Einzugskraft nochmals erhöht.
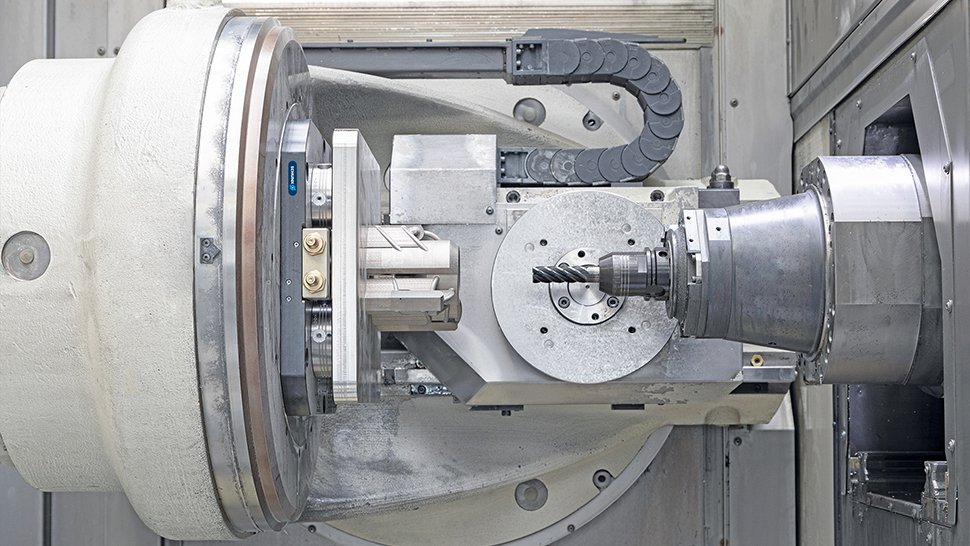
Bauteilbearbeitung in einem Grob-Fräszentrum mit mehreren Schunk-Modulen: der Werkzeughalter TENDO E compact sowie das auf einer Spannstation mit Nullpunktspannmodulen gespannte Werkstück.
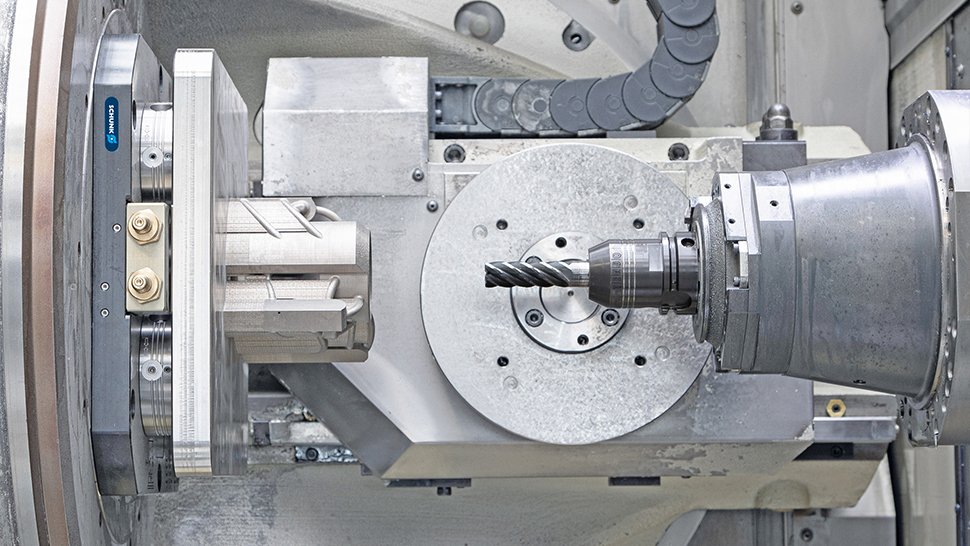
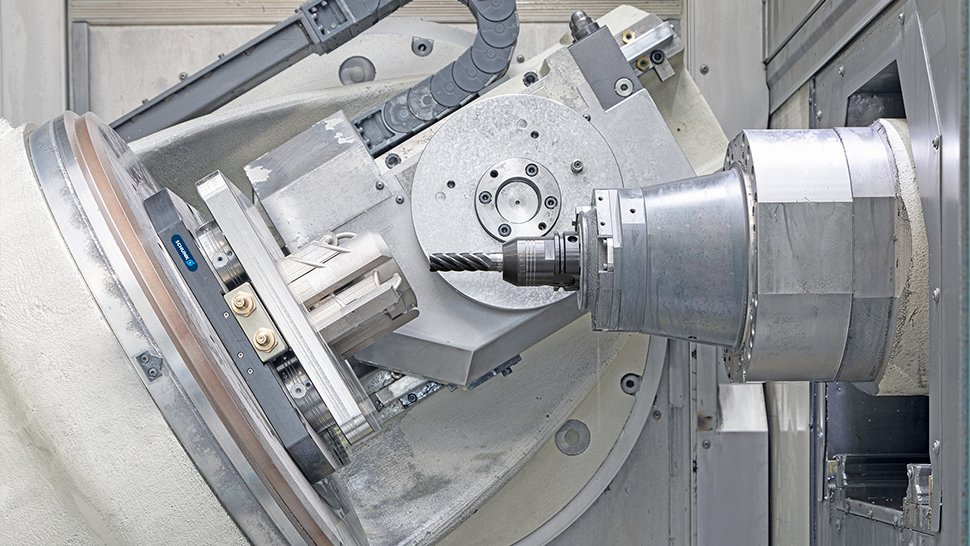
Basis für die Präzision
Der Entwickler betreut mit seinem Team den 3D-Metalldruck im Unternehmen. Neher fertigt Sonderwerkzeuge, Spezialbauteile und Prototypen für den modernen Automobilbau. Hierfür hat das Unternehmen die moderne Lasertec 30 Dual SLM von DMG Mori für die generative Fertigung durch selektives Laserschmelzen (SLM) angeschafft.
Mit diesem 3D-Drucker in Dual-Laser-Variante lassen sich in 300 mal 300 mal 350 Millimetern (x/y/z) Bauvolumen hochkomplexe Bauteile mit differenzierter Funktionsintegration generativ im bis zu 200 Grad Celsius heißen Pulverbett herstellen. Zum Einsatz kommen Serienwerkstoffe – hochfester Werkzeugstahl, nichtrostender Stahl und Alu-Legierungen.
Auch der so genannte Hybrid-Druck, das Aufschmelzen von Werkstücken auf vorgefertigten Bauteilen, wird bei Neher realisiert. Dabei werden geometrisch simple Werkstückanteile konventionell gefertigt, anschließend werden die komplexen Geometrien auf den Hybridrohling additiv aufgedruckt.
Hierzu werden die Spannbolzen des Nullpunktspannsystems direkt am Hybridrohling montiert. Diese Vorgehensweise nutzt die Vorteile beider Verfahren und senkt die Fertigungskosten deutlich. Die Laufzeit des 3D-Druckers verkürzt sich, sodass er schneller zum nächsten Auftrag übergehen kann. So wird die Produktionseffizienz spürbar angehoben.
Voraussetzung für die präzise und effiziente Herstellung solcher Werkstücke mit meist feinsten Gitter- und Wabenstrukturen, komplexen und dünnwandigen Geometrien sowie konturnahen Kühlkanälen ist die absolut präzise Einspannung der Substratplatte, auf der sich das Produkt im Maschinenraum additiv aufbaut. Hier besticht das Spannsystem, das Schunk eigens für Anwendungen im 3D-Metalldruck konzipiert und ausgelegt hat.
Hitzebeständig und resistent
„Dieses Spannmodul ist eine Besonderheit“, sagt Benjamin Hirz, Entwickler bei Schunk. „Während herkömmliche Nullpunktspannsysteme bis 60 Grad Celsius eingesetzt werden können, hält dieses Spannsystem den hohen Temperaturen des Stahlpulver-Schmelzprozesses stand“, erläutert Hirz.
Neben den beiden Lasern als thermische Quellen in der Lasertec 30 Dual SLM geschieht ein weiterer Wärmeeintrag im Bauraum durch die aktive Beheizung des Maschinentischs auf maximal 200 Grad Celsius. Dadurch wird der Temperaturgradient geringstmöglich gehalten.
„Durch dieses Vorgehen halten wir bei Neher die thermische Dehnung sowohl des Werkstücks als auch im Spannsystem niedrig“, erläutert Niess weiter. „So bleibt der Referenzpunkt konstant an derselben Stelle, so dass der Laserschmelzprozess präzise ablaufen und das Metallwerkstück exakt aufgebaut werden kann“, so Niess weiter. „Ohne das VERO-S NSE-HT mini 88-20 könnten wir den thermisch anspruchsvollen Herstellungsprozess nicht realisieren, denn es garantiert uns maschinentischseitig immer zuverlässig die fixe Position“, bekräftigt Niess.
Bei Neher kommen vier Module des Spannsystems sowie im Zentrum die Nullpunkteinheit VERO-S NE-HT mini 36 zum Einsatz. Die Nullpunkteinheit definiert über einen zentrischen Spannbolzen den thermischen Nullpunkt bei großen Substratplatten. Die Spannung selbst erfolgt simultan über die restlichen vier Spannbolzen. Ein integriertes Federpaket sichert die Spannung dauerhaft und selbsthemmend – Luft wird nur zum Öffnen benötigt.
Zuverlässiges Dichtkonzept
Das Nullpunktspannmodul ist thermisch höchst beanspruchbar. Die zweite große Herausforderung für das Nullpunktspannsystem: Es ist permanent dem hochabrasiven Material ausgesetzt. Doch dank des Dichtkonzepts widersteht es den feinsten Metallstäuben, die auch in allerkleinste Spalten dringen.
„Wir bei Schunk haben das System intensiv auf Herz und Nieren geprüft, auch unter realitätsfernen Worst-Case-Bedingungen“, bekräftigt Hirz. Mit konstruktiven Kniffen und speziellen Dichtmaterialien gelang dem Schunk-Entwicklerteam eine clevere Dichtlösung. „Unser Dichtkonzept ist so zuverlässig, dass das Spannsystem sogar für Tauchbäder geeignet ist“, erläutert Hirz.
Dieses Konzept bietet Anwendern größtmögliche Flexibilität, weil ein und dasselbe System sowohl hohe Temperaturen als auch Staub und abrasive Materialien aushält, im Reinigungstauchbecken einsetzbar ist, aber auch im Kunststoffdruckguss oder aber Schweißanwendungen.
„Bei all diesen Umgebungsbedingungen bleibt eine permanent hohe Kraft auf dem Spannschieber erhalten, was die absolute Prozesssicherheit gewährleistet“, bestätigt der Entwickler. „Selbst wenn feines Metallpulver in die Schnittstelle gelangt, blockieren die Spannschieber nicht; das Modul spannt zuverlässig.“
Mit einem Modul durch alle Prozessschritte
Die komplette Abdichtung verhindert das Eindringen von Metallpulver, Spänen, Staub oder auch Kühlschmiermitteln. Das Spannsystem läuft bei Neher seit drei Jahren auf dem 3D-Metalldrucker. „Absolut zuverlässig und problemlos und zu 100 Prozent präzise“, betont Niess. Trotz der langen Bearbeitungszeiten in der 3D-Metallfertigung – bei den Werkstücken, die Neher fertigt, dauern die Bauprozesse jeweils rund sieben bis zehn Stunden – gibt Schunk die Lebensdauer eines derart eingesetzten Nullpunktspannsystems mit circa zehn Jahren an.
Der Maschinenhersteller DMG verbaut das System auf Wunsch mittlerweile von Haus aus als vollintegrierte Lösung; so wird erreicht, dass das Nullpunktspannsystem vollversenkt und absolut plan im Maschinentisch liegt. Dies hat zum einen den Vorteil, dass der Bauraum in der Höhe voll genutzt wird und die Maschinenfunktionalität optimal zum Einsatz kommt. Zum anderen resultiert aus der vollintegrierten Konstruktion ein optimaler Wärmeübertrag des vorgeheizten Maschinentischs auf die Substratplatte und somit auf das sich aufbauende Werkstück.
Die Substratplatte mit Werkstück durchläuft weitere Bearbeitungsstationen – Entpulvern, Zerspanen, Messen. All diese nachgelagerten Fertigungsschritte sind mit der gleichen Schnittstelle durchführbar. So geht das Bauteil auf dem schnell gerüsteten Nullpunktspannsystem vom 3D-Drucker zum Fräsportal, in dem Neher das Hydrodehnspannfutter TENDO E compact von Schunk einsetzt.
Schließlich folgt die Qualitätssicherung, wiederum auf einer VERO-S mini Schnittstelle mittels VERO-S NSE mini 90-25 Nullpunktspannmodulen, auf dem Messtisch der Koordinatenmessmaschine Zeiss Carmet. Dort wird geprüft und verifiziert, ob sich alle Bohrungen, Kanten und Flansche innerhalb der Toleranz befinden und das Bauteil einwandfrei den Fertigungsprozess verlassen kann.
Kontakt
Benjamin Hirz
Entwicklung Spanntechnik
H.-D. SCHUNK GmbH & Co. Spanntechnik KG
Mengen
Tel. +49 7572 7614 1019
E-Mail senden
Kathrin Müller
Dipl.-Betriebswirtin (BA)
Digital & Media Corporate Marketing
Mengen
Tel. +49-7133-103-2327
E-Mail senden